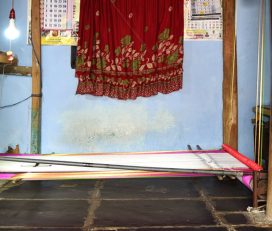
Saree weaving ~ Amar...
The place is renowned for its exquisite pure silk sarees adorned with intricate zari work. Skilled artisans here are masters of weaving elaborate jaala patterns...
Amarchinta, Telangana, India...
Silk is one of the most elegant textiles in the world, celebrated for its unmatched grandeur, natural sheen, and vibrant color affinity. With its high absorbency, lightweight softness, and durability, silk is rightly called the “queen of textiles.” In Indian culture, silk holds a sacred place, woven deeply into the fabric of life and tradition. For special occasions like weddings, festivals, auspicious pujas, or gatherings, silk remains a preferred choice for both men and women.
Historically, Pochampally was renowned for its Telia Rumal, a square piece of fabric traditionally made in black and red, used in everyday activities. The cluster also produced simple, everyday cotton sarees called “cheera” and men’s white dhotis called “pancha,” both featuring a modest border.
Pochampally sarees, in particular, are cherished in three main categories. The first category is wedding sarees, typically in bright colors with intricate zari and ikat work. Some weavers incorporate advanced techniques like double ikat and jacquard in this category. The second category is silk sarees with simpler ikat patterns, preferred for gatherings or office events. The third category is cotton sarees, which are commonly worn by women for office wear or casual gatherings and are popular even outside the state.
Beyond sarees, Pochampally is still known for its Telia Rumal. Artisans also produce bedcovers, dupattas, suit pieces, and fabric in both silk and cotton. Today, many designers and boutique brands source Pochampally fabric for stitched garments, adding a unique aesthetic and often commanding a premium. Nevertheless, sarees remain the most sought-after product from Pochampally due to their long shelf life, timeless appeal, and versatility across generations, making them a lasting investment.
The significance of Pochampally weaving lies in the joy it brings to countless saree lovers. People travel from Hyderabad and nearby towns to buy sarees here. The entire town is bustling with saree-related activities, Weavers are busy in weaving, auto drivers transport visitors to various shops, and tea sellers serve biscut and cofee to visitors. Surrounding Pochampally are many small villages where people earn their livelihood either directly or indirectly through weaving. Due to the involvement of numerous villages and people, this region is one of India’s prominent weaving clusters. With its strong cultural identity, Pochampally was one of the first traditional Indian crafts to receive the status of Geographical Indication (GI tag). It is the largest handloom tie-and-dye cluster, with over 2,000-3000 looms and approximately 7,000 artisans. Due to its large skilled population, Pochampally holds a significant place in ikat weaving.
Pochampally is also celebrated for the quality of its silk and vibrant colors. The town has a considerable number of skilled artisans adept at preparing traditional and geometric patterns in the ikat style of dyeing, which requires precision to achieve clear, defined patterns. The weaving process involves around 16 steps, including tying and dyeing sections of bundled yarn to predetermined intricate color patterns before weaving. While it may sound straightforward, visualizing a design on threads and then weaving it into a saree is extraordinary work, especially as this process is done on fine, delicate silk.
The Padmasales are one of the major weaving communities, and their name itself reflects their profession. The word “Padmasale” is derived from two words: Padma, meaning lotus, and Shale, meaning weaver. The Padmasales claim descent from the sages Bhrigu Rishi and Markandeya Rishi. According to legend, Markandeya’s son, Bhavana Rishi, had 101 sons who took up weaving. The first cloth they created was woven from lotus fibers, which led to their name, Padmasales.
The Padmasales trace their Sanskrit origins through various myths and ancient texts such as the Kulapurana and the Markandeya Purana. Their legendary origins are described in the Baramahal Records: “In ancient times, the other weaver sects would annually offer a piece of cloth to the rishi or saint, Markandeyulu. One year, they failed to present their offering on time, angering the rishi. In response, he performed a yagya (Havan) and, through the power of mantras, created a man from the fire of the sacrifice. He named this man Padma Saliwarlu and instructed him to weave cloth for his use. When the man presented the cloth to the rishi, he asked, ‘Oh, Swami, who shall I worship, and how may I attain moksha (salvation)?’ The rishi replied, ‘Worship me, and you shall attain moksha.’”
The office of headman, known as Setti or Gaudu, is hereditary within the community. The headman is assisted by an Ummidi Setti or Ganumukhi, who serves as the caste messenger and is exempt from various subscriptions for temple festivals and other communal obligations.
In one of the oldest written texts, the Vedas clearly mention weavers, referred to as “Vasovaya,” and occupations related to weaving. Archaeological evidence for clothing primarily comes from iconography found in Harappan figurines. These depictions show that men typically wore a long cloth wrapped around their waist, resembling a closely draped dhoti, along with a turban. Women are shown wearing skirt-like garments. Different patterns on the fabrics, often resembling block prints, are also visible in these depictions.
When it comes to Ikat, the primary visual evidence for the production of resist-dyed textiles in ancient India is found in the cave paintings at Ajanta in western India and some Jain manuscripts. Murals from the 6th to 7th centuries portray women wearing fabrics that appear to be patterned using resist-dyeing techniques. Gujarat and Odisha are closely connected to ikat weaving. The double ikat patola from Gujarat has been renowned since the era of the Solankis or Chalukyas, who ruled parts of present-day Gujarat and Rajasthan in northwestern India from the 9th to 13th centuries.
In the South Asian region, Indian influence on textiles may date back as far as the middle of the first millennium, coinciding with the Srivijaya thalassocracy in Southeast Asia (7th–12th century C.E.). Based in Palembang, Sumatra, the Srivijaya court expanded through a network of political, familial, and religious alliances, covering parts of present-day western Indonesia, Malaysia, and southern Thailand.The use of the term sutera or sutra—“silk” in Bahasa Indonesia and Sanskrit, respectively—suggests a long-standing relationship between the introduction of this fiber and its use in Indonesian courts.
It is challenging to determine precisely when weaving began in Pochampally. To understand its origins, we must consider the skills, communities, and settlements involved. While Pochampally flourished as a weaving center in the past 50-60 years, this does not mean that weaving activities were absent before. Being close to Hyderabad, Pochampally produced cotton textiles known as ‘sooseelu’ during the Nawab period. However, the town gained prominence for its tie-and-dye rumals, later known as ‘teliya rumals,’ ‘golkondalu,’ ‘jananilu,’ ‘mardanilu,’ and other names. The ikat silk weaving technique in Pochampally is relatively recent compared to Gujarat and Odisha; records indicate that ikat was introduced from Chirala. Some say that weavers migrated to Pochampally, while others claim they traveled to learn the technique. For many years, they primarily produced single ikat patterns on cotton.
Pochampally, now popularly known as Bhoodan Pochampally, was central to the Bhoodan (Land Donation) movement, a land reform campaign initiated in 1951 by Gandhian Vinoba Bhave. This movement encouraged wealthy landowners to voluntarily donate portions of their land to the landless. Influenced by Gram Swarajya and Sarvodaya philosophies, Bhave’s efforts led to social reform discussions in the 1950s. During this time, Andhra Pradesh’s handloom sector began benefiting from the cooperative movement, and a Handloom Cooperative Society was established in Koyallagudem, 20 kilometers from Pochampally. In 1955, Pochampally weavers formed their own independent society.
Elders in the community recall that the weaving cluster transformed around 1970 when local weavers sent young artisans to Bangalore to learn silk weaving techniques. Subsequently, workshops with Patola artisans introduced new skills that shifted much of Pochampally’s production to silk ikat. Patola’s influence is evident in Pochampally’s motifs, featuring floral, animal, and bird designs, while traditional cotton ikat designs were more geometric.
The primary weaving community here is the “Padmasale” caste. Historical records from the pre-independence era describe Padmasales as a Telugu-speaking caste of weavers scattered across the Madras Presidency. Most Padmasales practiced their hereditary trade, though few owned looms; they often worked for wealthier loom owners. They mainly produced coarser cotton cloth, lacking the resources to compete in fine cotton weaving. This suggests that Pochampally’s early weaving activities focused on cotton textiles.
The length of a Pochampally saree is typically 6.2 meters, with a width of 48 inches. The border design depends on the jacquard pattern, while the silk quality ranges from 28-32 denier, depending on the grade, with 80 to 110 picks per inch. The clarity of the design depends on the threads, and not a single loose thread can be left, as every thread plays a crucial role in creating the unique patterns. The entire process requires immense concentration, especially during warping and weaving, which cannot be replicated on power looms.
In Pochampally, aside from the traditional Telia Rumal geometric patterns, newer designs are a mix of various patterns, motifs, and layouts. It is often challenging to identify which motifs are indigenous and which are inspired by designs from other sarees. For instance, many bird and animal motifs draw inspiration from Patola sarees, while geometric patterns are rooted in local Ikat traditions. Broadly, Pochampally saree designs can be categorized into two main types:
Pure Silk Sarees & Dupattas: In this category, the entire saree is crafted from pure silk and divided into the border, body, and pallu. Artisans showcase their skill and creativity by experimenting with a variety of layouts and motif sizes.
Pure Silk with Zari Sarees & Dupattas: In this category, a zari border is incorporated into the saree. The size of the border depends on the design and the use of jacquard or dobby techniques. These sarees are more expensive and are often preferred for weddings and festive occasions.
Artisans explore a wide range of geometric patterns, including zig-zags, squares, diamonds, dots, stripes, birds, flowers, and checks. For lower-range sarees, simple motifs with two colors are popular, a white motif on a bright-colored saree or a bright-colored motif on a light saree. However, for multicolored weft Ikat motifs, chevron borders, or abstract motifs in grid patterns, the craftsmanship reaches an exceptional level.
Due to the fineness of the silk, these designs are often perfectly reversible, appearing identical on both sides. This feature makes them especially suitable for dupattas, scarves, and stoles, which tend to fold, ensuring they maintain their aesthetic appeal from either side.
As Pochampally sarees grew in popularity, they soon faced the issue of imitation by powerlooms and mills. These machine-made sarees are misrepresented during sales; they are neither real silk nor authentic ikat, as the ikat patterns are simply printed onto the fabric. Such products lack the quality and durability of handloom-produced sarees.
The demand for genuine handloom silk sarees has declined, with price competition and wage cuts becoming prevalent. Artisans point out that a mill-made saree from Surat now costs only one-fifth of a handloom saree, and price remains a major factor for many buyers. They also raise concerns about the decline in exhibitions, as rapid urbanization makes it harder for people to access these events in large cities. Additionally, online shopping has shifted consumer behavior, impacting sales of authentic handloom products.
When we buy a product, we rarely think about how many hands contributed to its creation—from cultivating the silk to the final ironing. The process of making a Pochampally saree is incredibly complex and involves many people. If we were to list them all, more than 50 individuals might have contributed to producing just one saree. The process is also fascinating because, until the very end, it is difficult to visualize the final aesthetic of the product. Developing such a keen visual sense often requires years of training, sometimes starting from childhood.
Yarn: In the typical and popular Pochampally saree, artisans use mulberry silk of different counts, such as 40s, 60s, and 80s, mostly sourced from Bangalore. Some artisans also source silk and cotton yarn from nearby towns like Secunderabad, Vijayawada, Adoni, and Chirala.
Zari: The most commonly used zari is golden in color and is procured from wholesale markets in Surat.
Dye: Wet dye is used for coloring the silk yarn.
Rubber: Artisans source old bicycle rubber tubes to tie the yarn during the dyeing process.
Wood/Gas: Wood or gas is used to boil water with dye during the dyeing process.
Gum: Rice water and coconut oil are used during the warping process.
Handloom (Maggam): Different types of looms can be spotted here, including pit looms, frame looms, and looms with jacquards. These are used to weave the final fabric.
Pirn (Pikas): A small tube used for winding yarn, which is then placed inside the shuttle.
Shuttle (Nada): The shuttle moves between the warp yarns, carrying the weft yarn during the weaving process.
Charkha (Ratnam): The charkha is used for winding yarn onto the spindle. The spindle is placed inside the shuttle and used for weaving.
Jacquard/Dobby: These attachments are used to create intricate patterns on the border or pallu of the fabric.
Reed (Aatasu): A part of the loom through which the warp yarn passes, helping maintain uniform spacing.
Bobbin: Locally referred to as Gurkal.
Metal Utensils: Various-sized metal utensils are used for dyeing the yarn. Dyers boil dye in these utensils to color the yarn.
Coming soon
The process of making a Pochampally saree is very complex and involves many people, categorized into four main roles:
1. The designer who visualizes and creates the design on paper.
2. The artisan who ties the threads according to the design.
3. The dyer who colors the yarn.
4. The weaver who weaves the final saree.
Apart from these four key roles, many other skills are required, such as warping, setting up the warp on the loom, and preparing the weft during weaving.
Step 1: Sourcing and Degumming
The process begins with sourcing silk from the market. The first step is degumming, where the silk gum is removed from the silk. This step enhances the sheen, color, texture, and overall quality of the silk.
Step 2: Hank to Bobbin Transfer and Stretching
Next, the silk yarn is transferred from a hank (a large loop of yarn) to a bobbin (a small spindle used in textile manufacturing). Following this, the yarn is stretched out on a metal frame and tightened using clips. Different types of frames may be used for this purpose. Once the weft yarn is securely stretched, it is marked with the desired design and prepared for dyeing.
Step 3 – Detailed designs are first marked out on a graph sheet, pixel by pixel. Skilled artisans transfer the design onto the yarn using a pen in a process called chitiki poyadam. Even after this step, it is difficult to visualize the final design; only lines can be seen at this stage. This process requires precision as artisans also plan the sequence of colors during tying. In most cases, old bicycle tubes are used to tie the yarn securely. Graphs and paper drawings are used primarily for intricate or newly developed designs.
Step 4 – After tying, the next step is dyeing. The lightest color is applied to the yarn first on the tie-and-dye frame. The dye penetrates the fibers of the weft, and the color is set by heating it along with the necessary chemicals. After the first round of dyeing, the yarn is left to dry before repeating the process for additional colors. It is crucial to control the temperature and timing of the dyeing process to ensure even and consistent application. The typical dyeing sequence is as follows: red is applied first, followed by yellow or orange, and then green or blue.
Step 5 – To achieve the specific design, this process may need to be repeated multiple times. During each repetition, special care is taken to prevent colors from overlapping or bleeding. Once all the colors have been applied, the warp or weft threads are untied, revealing the finished design on the yarn.
Step 6 – Warping is typically done outdoors and by hand, using a comb to separate the yarns. This step is crucial for ensuring the even and consistent application of dye across the entire length of the warp. To make the threads more durable, the yarn is dipped in a solution of water, rice starch, and coconut oil. The warp is then stretched to its full length in a long corridor. Nowadays, advanced warping machines can also be seen in Pochampally, making the process more efficient.
Step 7 – The next step involves transferring the yarn onto the loom. This is done by passing the yarn through a reed, a comb-like device that separates and spaces the warp threads in the loom. The yarn is then tied to the leftover threads in the reed using a process called knotting.
Step 8 – The weaving is done on a traditional pit loom with two shafts. During weaving, each weft must be carefully positioned to ensure a clear and accurate pattern. Completing a warp typically takes four to five days. However, many societies and master weavers now use frame looms instead of pit looms. Modern weaving environments often have better facilities, including improved lighting, tools, and cleaner workspaces.
Coming soon
Pochampally was once a small village, like many others in India, and tracing its exact history is challenging. The town gained prominence during the Bhoodan movement initiated by Acharya Vinoba Bhave. Bhave observed the disintegration of India’s economy, the dire state of agriculture, and the appalling poverty of landless laborers. In 1950-51, over 50% of agricultural labor households were landless, a figure that rose to 57% by 1956-57. Recognizing that agrarian legislation, particularly land distribution and ceiling laws, had failed, he launched the Bhoodan (land donation) movement.
When Vinoba Bhave visited Pochampally, a large village with about 700 families, two-thirds of whom were landless, he was warmly welcomed by the villagers. By early afternoon, villagers gathered around him, requesting 80 acres of land (40 wet and 40 dry) to be distributed among 40 families. This marked an important moment in the village's history.
Over the past 50-60 years, Pochampally has flourished. Initially, it was a small weaving town near Hyderabad. During the Nizam’s period, Pochampally textiles, woven in cotton, were known as sooseelu. However, the village became famous for its tie-and-dye rumals (scarves). In the late 1950s, when Kamaladevi Chattopadhyaya and others visited the area, they recognized the potential of creating tie-and-dye silk sarees for the market. The All India Handloom Board selected two Pochampally weavers to train in silk weaving techniques at different silk clusters. This initiative proved to be a turning point, transforming the region’s weaving industry, which has since never looked back.
Today, Pochampally has earned a place on UNESCO's tentative list of World Heritage Sites under the category of "iconic saree weaving clusters of India." Weaving activities are carried out not only in Pochampally but also in nearby villages such as Sripuram, Chuigottala, Koyalgudam, Chowtuppal, Galteppala, and others. These villages form a vibrant hub of traditional weaving, preserving and promoting the legacy of Pochampally Ikat textiles.
Pochampally Mandal is a vibrant region located within the Bhongir Division of Telangana, India. Positioned at 17°20′46″N 78°48′44″E, this area spans 28.42 square kilometers (10.97 square miles) and is celebrated as the heart of the renowned Pochampally Ikat weaving tradition. Situated at an elevation of 1,184 meters (3,885 feet) above sea level, Pochampally enjoys a unique geographical setting that has supported its cultural and economic development over the years.
Hillocks: The town is surrounded by rolling hills, creating a scenic backdrop.
Ponds: Numerous ponds dot the landscape, attracting a variety of birdlife.
Green Fields: Lush green fields add to the charm of the region.
Birdwatching Paradise: Pochampally's diverse ecosystem attracts a variety of bird species, making it a haven for birdwatchers. The ponds and wetlands provide ideal habitats for migratory and resident birds.
Coming Soon
Road Connectivity: Pochampally is well-connected by roads to nearby towns and cities, facilitating trade and tourism.
Water Supply and Sanitation: The village has made strides in improving water supply and sanitation facilities to support its population.
Electricity: There is access to electricity, which is essential for both residential needs and the operation of weaving machines.
Tourism Facilities: With increasing interest in handicrafts, infrastructure to support tourism, such as guesthouses and information centers, is being developed.
Education and Training Centers: Institutions focused on preserving and teaching the art of Ikat weaving are present, contributing to skill development and employment.
Overall, the architecture and infrastructure of Pochampally reflect its cultural heritage and the importance of the textile industry to its economy and identity.
Traditional Homes: The houses in Pochampally often feature a blend of local materials and traditional designs, including tiled roofs and mud walls. Many homes have intricate murals and patterns that reflect the local culture.
Weaving Sheds: The infrastructure includes numerous weaving sheds where artisans create the famous Ikat textiles. These spaces are designed for functionality, allowing for the use of traditional looms.
Community Halls: There are community centers that serve as gathering places for festivals and local events, reflecting the social structure of the village.
Sri Ramalayam
Overview:
Sri Ramalayam is a prominent temple in Pochampally dedicated to Lord Rama, a significant deity in Hinduism. The temple is known for its spiritual ambiance and architectural beauty.
Architectural Features:
Design: The temple showcases traditional South Indian temple architecture, characterized by intricate carvings and sculptures depicting various deities and mythological scenes.
Gopuram: The entrance tower (gopuram) is adorned with colorful sculptures, typical of Dravidian architecture.
Cultural Significance:
Festivals: The temple is a focal point for various festivals, including Rama Navami, where devotees gather to celebrate with prayers, music, and dance.
Community Hub: It serves as a gathering place for the local community, fostering spiritual and social connections.
The temple
Sri Lakshmi Narasimha Swamy Temple
Overview:
Dedicated to Lord Lakshmi Narasimha, an incarnation of Vishnu, this temple is another important religious site in Pochampally.
Architectural Features:
Sculptural Details: The temple is known for its exquisite sculptures and carvings that depict scenes from Hindu mythology, particularly those related to Lord Vishnu and his avatars.
Sanctum Sanctorum: The inner sanctum houses the idol of Lakshmi Narasimha, attracting many devotees who come to seek blessings.
Cultural Significance:
Pilgrimage Site: The temple attracts pilgrims from nearby regions, especially during auspicious days and festivals.
Rituals and Pujas: Regular rituals and special pujas are conducted, drawing locals and visitors alike, reinforcing the temple's role in the spiritual life of the community.
Conclusion: Both Sri Ramalayam and Sri Lakshmi Narasimha Swamy Temple are integral to Pochampally's cultural and spiritual landscape. They not only serve as places of worship but also as centers of community life, preserving and promoting the rich traditions of the region. Visitors to these temples can experience the architectural beauty and the vibrant cultural practices that define Pochampally.
Coming Soon
The people of Pochampally, a village in Telangana, India, are known for their vibrant culture, rich traditions, and strong community ties. Here are some key aspects of the people of Pochampally:
Demographics
Community: The population primarily consists of artisans, particularly weavers who specialize in the famous Pochampally Ikat textiles.
Occupation: Many residents are involved in handloom weaving, agriculture, and related crafts, contributing to the local economy.
Cultural Practices
Traditions: The community maintains strong cultural traditions, including festivals, rituals, and art forms that reflect their heritage.
Festivals: Important festivals include Sankranti, Dasara, and Ugadi, celebrated with traditional music, dance, and community gatherings.
Clothing
Traditional Attire:
Women: Often wear sarees made from Ikat fabric, adorned with traditional jewelry.
Men: Typically wear dhotis and kurtas, with some opting for modern clothing in urban settings.
Lifestyle
Community Life: The villagers have a close-knit community, often participating in communal activities and supporting each other in their crafts and livelihoods.
Education and Skill Development: There are initiatives focused on educating the younger generation about weaving and preserving traditional crafts.
Modern Influences
While deeply rooted in tradition, the people of Pochampally also embrace modern influences, balancing their rich heritage with contemporary lifestyles. This blend is evident in their attire, practices, and interactions with the outside world.
The people of Pochampally exemplify a unique combination of tradition, craftsmanship, and community spirit, making them an integral part of the region's cultural landscape.
Apart from its renowned weaving, Pochampally is famous for several other aspects:
Cultural Tourism: The village attracts tourists interested in traditional crafts and rural life. Visitors often explore the weaving process and engage with local artisans.
Heritage Sites: Nearby temples and historical sites, such as ancient structures and monuments, draw visitors.
Scenic Landscapes: Pochampally is surrounded by lush fields and scenic landscapes, making it a picturesque destination for nature lovers and photographers.
Paddy Cultivation: The region is known for its agricultural practices, particularly rice cultivation, which is a staple food in the area.
Organic Farming: Some farmers practice organic farming, contributing to sustainable agriculture and attracting health-conscious consumers.
Local Cuisine: Pochampally offers a variety of traditional dishes, including rice-based meals, lentils, and local vegetables, often flavored with regional spices.
Fairs and Festivals: The village hosts various fairs and cultural events that celebrate local traditions, music, and dance, fostering community spirit and attracting visitors.
Other Crafts: In addition to weaving, local artisans may engage in other handicrafts, including pottery, basket weaving, and woodwork, showcasing the region's artistic diversity.
List of craftsmen.