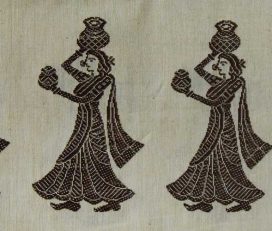
Gollabhama Saree Wea...
The Siddipet Gollabhama Saree is not just a piece of fabric; it is a living tradition, worn, celebrated, and reinterpreted through generations.
Siddipet, Telangana, India...
Bagh is the name of a block printing technique unique to a small village called Bagh in Madhya Pradesh. The craft as well as the village derive their names from the River ‘Baghini’ that flows through the village and serves as a spine for the craft. Bagh printing is an array of dynamic floral and geometrical prints made using finely cut wooden blocks and vegetable dyes.
Bagh Print is a traditional block printing technique with natural colours, unique to a small village called Bagh in Dhar district, Madhya Pradesh, India.
Bagh print was originally practised across the regions in the Indus Valley. The name 'Bagh' is generated because of the ‘Khatris’ (a textile community) who migrated from Sindh to bagh. Ismail Suleman Khatri is considered to be a pioneer of The Khatris of Bagh.
In places like ‘Kukshi’, ‘Dharampuri’ and ‘Thikri’ by a group of people known as ‘Chhipas’ or ‘Bhavsars’. The ‘Khatris’ a textile community from Sindh.
Ismail Suleman Khatri is considered to be a pioneer of the Bagh print of The Khatris of Bagh.
Bagh’ prints are characterized by multiple rows of tiny geometric patterns mostly done in red and black color. Today, the red color is obtained by using alizarin and fermenting iron filings in jaggery to make black.
Bagh print has a cultural and religious importance in the tribal communities of Dhar. The traditional Bagh prints with their characteristic red, black, white colours and religious motifs are used by the ‘Adivasis’ (tribes) for important festivals and special events like marriages. In their marriages the groom’s family gives the bride’s family a dowry consisting of 60 kg Jaggery, 4 quintal Grains, Garments made of Bagh prints like the ‘Lugda’ (head draping garment), ‘Ghaghra’ (long skirt), along with silver jewelry like necklaces, armlets and bracelets.
Bagh was also used by the local tribes in their religious ceremonies. This led to the inclusion of religious animal motif like cows and elephants in their prints.
Headed by their founding father and guide – Ismail Khatri, the printers innovated and developed the craft to gain popularity and versatility. ‘Bagh’ printed fabric which was traditionally worn by women in the form of ‘Lehngas’ and ‘Ghagras’ (forms of skirts) with time included ‘Sarees’, ‘Salwars'(pants), ‘Dupattas’ (unstitched fabric to be worn as a drape over your clothes), scarves and even t-shirts being stitched today. However, as compared to tradition men’s wear, where Bagh was printed over turbans, ‘Lungis’ (drape to cover waist below), there are almost no options for contemporary men apart from scarves and kerchiefs. The fabric was also a common feature of a traditional household, where it was used as bed-covers and cradle lining due to its light and cooling touch. Today, its uses have also blended into products like curtains, lampshades, screens, cushion covers and wall pieces.
Bagh prints, earlier known as ‘Thappa Chapai’ or ‘Alizarine Print’ are created using natural dyes, which are eco-friendly and non- hazardous. The wooden blocks used for printing consist of 200 to 300 year old blocks based on traditional motifs, inspired by 1500-year-old paintings found in the caves of the region. Another characteristic feature of the Bagh textiles is their extremely soft texture, which is achieved through repeated washes in the Baghini River. The high content of lime and iron in river water acts as cleansing and fastening agent. This prevents the loss of colour even after successive washes, especially in the red and grey tones. In fact, it is this specific chemical composition of river water that makes the vibrance of bagh prints so unique.
In summers when the river dries up, craftsmen go to the Narmada River bed and wash their textiles.
There are specific block makers for this craft, who have honed their skills in Bagh designs through years of practice. They are unique to the craft and preserve the designs. The three-dimensional effect that they create in the prints is yet to be replicated by any machine printing process. These fabrics have traveled far and wide with their traditional as well as new innovative designs and are much in demand in the contemporary Indian and international markets. As a pioneering craft from the state, Bagh has also featured in the Madhya Pradesh state tableau as part of the Indian Republic day procession in 2011.
There are various stories about how the term ‘Bagh’ originated. This craft was practiced by the early tribes. It is believed to have taken its name from ‘Bagh Gupha’, the Buddhist caves that were first discovered in 1818 AD. With the extinction of Buddhism in central India by the 10th century A.D. these caves seem to have been wiped off from human memory. As dense forests grew around them, tigers also known as ‘Bagh’ in Hindi often inhabited the caves. This association of tigers with the caves gave them their present name. The village situated at a distance of about 8 km and the river flowing nearby the cave came to be known as ‘Bagh’ village and ‘Baghini’ River respectively. Many are of the opinion that it was the river and the village, which lent its name to the caves and subsequently to the craft.
Another story suggests that the Khatris of Bagh and Kutch share common lineage, descending from the lands of Sindh. While a few settled in Dhamadka and later in Ajrakhpur and continued doing Ajrakh printing, a few moved further towards the central part of the Deccan to settle in Bagh, Madhya Pradesh. The resemblances in the crafts, in terms of the process followed and the materials used also prove the same.
Block printing in India is an ancient craft, dating as far back as 3000 BC. It can be traced back to the Indus Valley Civilization and some historians are of the opinion, that India may have been the original home of textile printing. Archaeological evidences collected from ‘Mohenjedaro’ establish that the complex technology of mordant dyeing had been known in the subcontinent from the second millennium BC. Block printing was practiced in places like ‘Kukshi’, ‘Dharampuri’ and ‘Thikri’ by a group of people known as ‘Chhipas’ or ‘Bhavsars’.
The ‘Khatris’ a textile community from Sindh migrated to Gautampura and later on to Manavar. From Manavar a part of the community moved to Bagh, a nearby village in search of good quality water for their craft and also to avoid octroi taxes. The remaining Khatri clan settled towards the Kutch regions of Gujarat.
In 1960 AD, the Khatris of Bagh of whom Ismail Suleman Khatri is considered to be a pioneer, settled on the riverbanks of Baghini when it was discovered that the high copper content in these waters increases the depth of color. This was the turning point in the history of Bagh. Young Ismail was inquisitive by nature; he compared the crafts of Gujarat and Madhya Pradesh and realized that people in the central India had a liking for brighter colors. With the right resources available, he decided to include bright vibrant colors in Bagh, compared to the erstwhile traditional colors of black and red. This increased the beauty of the craft with many colored floral prints being used now. The versatility and beauty of the fabric soon became well known and this threw the market wide open.
Apart from what is known to be modern Bagh, Ismail Suleman Khatri has also been instrumental in developing the traditional ‘adivasi’ prints to include tribal motifs of religious significance. These motifs made primarily in black and red often include animals like elephants and cows.
Mr. Khatri for his significant contributions to the development of the craft has received several accolades on national and international level. In 1977-78 and in 1984 he was honored with the Indian National Award. A passionate craftsman and a charitable man, Mr Khatri has furthered the craft by providing self-sponsored training and livelihood to at least 2500 ‘Harijans’ and ‘Adivasi’ living under the poverty line. Many of these trained artisans practicing the craft have gone to establish their own businesses and several have won important prizes nationally and internationally.
The Bagh prints of Madhya Pradesh have small abstract floral designs that are more intricate as compared to the ones found in Rajasthan. Even more intricate are the ‘Saudagari’ prints of ‘Pethapur’, from which the block making art is believed to have originated.
‘Bagh’ prints are characterized by multiple rows of tiny geometric patterns mostly done in red and black color. Today, the red color is obtained by using alizarin and fermenting iron fillings in jaggery makes black.
The traditional motifs used are ‘Nandana’ mango motif, ‘Tendu’ plant motif, ‘Mung Ki Phali’ motif, ‘Khirali Keri’ motif, ‘Leheria’ motif, ‘Jowaria’ motif and the ‘Phool Buta’ motif. The fabric borders usually printed in Bagh and the stone carvings of the Bagh Caves share a common design inspired by the climbing creeper plant known in Hindi as ‘Bel’. This craft gives great flexibility for developing innumerable surface designs through permutations and combinations of borders, ‘Buti’(motif) and ‘Jaal’ (floral net) blocks.
Nowadays, the natives wear industrially produced fabric for regular wear and buy Bagh prints only for major festivals or ceremonies. With increasing appreciation for hand block printed fabrics in global market, Bagh artisans have moved on to printing fabric for contemporary market, bringing more colors and patterns into their prints.
A generation before, the printers were catering to the demands of local market, with the increasing demand for Bagh printed fabrics in urban areas; the printers are finding it difficult to maintain the quality of the prints. Also, when in summers the village river dries-up, the artisans have to move to far off lands to wash the fabrics after dyeing, this is a big problem as the river water is essential to bring out brighter colors on the fabrics.
The teak wood blocks are made smooth with the help of woodworking tools. The craftsmen cut out pieces according to the required block size and are careful to cut away from any knots in the wood. The smoothened surface is painted white with lime paste and then the design is traced onto it.
The raw materials involved are base fabrics of cotton or silk, natural dyes and wooden blocks.
Fabrics for printing:
Cotton: Cotton is readily available from the nearby markets of Indore. The cotton normally used is from ‘Century Mills’ – (for bedcovers, table cloth, etc.) with different counts like 60/60 and 40/40, depicting the thickness of the yarn used.
Silk by cotton: Silk-by-cotton fabric is purchased from the towns of ‘Maheshwar’ and ‘Chanderi’. From ‘Maheshwar’, loom made plain silk-by-cotton saris and from ‘Chanderi’, silk cloth or dress pieces are procured. ‘Cambric’ cloth is purchased from Mumbai to make dress materials. ‘Mulmul’ fabric comes from ‘Bhivandi’ town and is priced depending on the quality of the material.
Silk: Silk cloth materials like ‘georgette’, ‘crepe’ and ‘chiffon’ are procured from Indore and Mumbai. ‘Tussar’ silk is procured from the towns of ‘Raigarh’ and ‘Bhopal’, at the price rates varying from Rs.110 to 300 per meter.
Jute: ‘Dhaka Jute’ is purchased from Delhi at the price rate of Rs. 30-40 per meter fabric.
Goat Droppings: This is used in a solution along with castor oil and generates heat when trampled on with feet. It helps in making the fiber more absorbent.
Fitkari or Alum: This is mixed together with tamarind seeds and boiled to create a paste. This paste is used during the process of red color printing.
Tamarind Seeds: These are used in the above-mentioned process during the printing of red color.
Alizarin: This is used in the process of printing red colour.
Dhavdi Flowers: The extract of these flowers is used as dye and mixed along with Alizarin.
Harda: This is used to give the fabric an off white tone.
Wood: Wood is used as fuel in the furnace.
Cotton cloth padding: Layers of cotton fabric cut to the size of the wooden trey that contains dyes are stacked together and soaked in the dyes. Blocks are directly pressed on to this cotton stack before printing. It helps prevent dripping of the liquid color.
Wooden blocks: The craftsmen only use teak wood, locally known as ‘Sagwan’, sourced from Valsad, a town near Gujarat-Maharashtra border for making Bagh printing Blocks. Teak provides the perfect base for carving intricate motifs as it is a dense and strong wood. It doesn’t absorb water or distort in shape even after years of usage. The craftsmen use a hand-drill arrangement that involves a bow called ‘Kamthi’ and a driller ‘Saarardi’ to drill out larger portions of the design voids from the block. For finer carving and finishes they use a variety of chisels of varying shapes and sizes. These tools are also handmade by them according to their requirements. The blocks that have a raised wooden cut out are used in printing the design motif (image 1). The other kind of blocks that have a softer wood stuffing are used as negative printing blocks (for the negative spaces of the print), for the larger areas (image 2).
Dyeing trays and ladles: Trays made of wood or plastic are used to fill the dyes (image 3). Various ladles are used for mixing the dyes. A thin bamboo ‘Trellis’ is fixed inside the tray containing the liquid dye mixture. This structure holds the coarse piece of cotton cloth. The blocks are pressed onto this cotton cloth padding that has been soaked in the dye rather than dipping them directly in the solution. This enables the dye to spread more evenly onto the block and prevents dripping and bleeding of colors on the main fabric.
Printing Tables: These are raised wooden surfaces and are roughly about 5ft by 3 ft. in dimension (image 5). Wooden stands or bricks are used to uniformly raise this platform by 9 inches above the ground and the printer sits on the ground to commence the printing process. The tables are chosen according to the width of the fabric. The craftsman print from left to right and when the width of the fabric is more than that of the table, they move it vertically upward to make a continuous print.
Large Containers: These are used to mix and store various solutions and dyes, to be used later (image 4).
Water Tank: Large cemented water tanks have been created to store different types of water solutions required for processing the fabric before and after the printing process. These are used for fabric soaking and washing purposes.
Bhatti or Furnace: The furnace is made of mud and is used to boil fabric in various solutions. It is fueled by dry wood.
In Bhil weddings, the groom’s side brings Bagh printed ‘Lugda’ (drape), ‘Pulke'(bangles), ‘Gud’ (Jaggery) and grains as a gift for the bride. The bride wears the same ‘Lugda’ during the main ceremony.
Carving the Block
The teak wood blocks are made smooth with the help of woodworking tools. The craftsmen cut out pieces according to the required block size and are careful to cut away from any knots in the wood. The smoothened surface is painted white with lime paste and then the design is traced onto it. This increases its contrast and visibility. The craftsmen use hand-drill arrangement that involve a bow or ‘Kamthi’ and a driller or ‘Saarardi’. They drill out large portions from the block; and for finer shapes, they use a variety of chisels in different shapes and sizes. The craftsmen make their own work tools as per their requirement. Once prepared, the blocks are immersed in oil for a few days to protect them against warping and insect attacks. This is important since the block is going to be in constant touch with water-based dyes, which make them more vulnerable to decay. Wooden blocks range from as small as an inch to as large as sixteen inches in size(image 1). While a basic block (3″ to 4″ across) takes a day or two to be made today, an intricate one may take almost a week’s work.
Preparation of the Fabric
Raw material processing is carried out in copper tubs. The fabric is washed to get rid of the impurities and left to dry in the sun. Once dry, it is dipped in a solution made of castor oil and goat droppings, which react with each other to generate heat and this makes the fiber absorbent. The cloth is dipped in this solution repeatedly and trampled on by foot to produce froth and then left to dry(image 2). After this, it is soaked in a starch solution of ‘Tarohar’ and ‘Harada’ powder and sun dried again. This also gives the fabric its yellow tone. It is necessary to dry it in the shade to prevent the desired yellow color from turning green due to the sun.
Printing
A paste is made by mixing the dye with ‘Dhavda’ (a kind of flower) gum. There are two types of pastes: one is a red in color and the other is black. For the printing of red color, alum is boiled in a solution along with tamarind seeds to create a paste. For black, Iron rust is boiled till it becomes a thick paste and this is used to print black. After preparing the pastes, it is filtered and poured into a wooden tray. This dye is applied to the wooden blocks by pressing them onto this tray(image 6).
Meanwhile, the yellowish cloth obtained from the earlier process is evenly stretched across the table. A black boundary is drawn with plain stamps around the cloth. The cloth now becomes a canvas for the craftsman who skillfully prints and matched the intricate designs. He starts printing in rectangles, beginning from the outer portion of the cloth and moving inwards until it is covered. He avoids overlapping of the prints by putting an old cloth or paper where the printing has already been done. It is left to dry and washed once more.
Dyeing
For the ‘Bagh’ printed cloth to have its characteristic contrast and finishing, it must pass through another dyeing process. ‘Alizarin’ mixed with ‘Dhavadi’ flower extracts are boiled together in a big copper container concealed in a cement structure. The printed cloth is then left to boil in it for five to six hours. The printed dye containing alum reacts with Alizarin to produce red (image 5). At the same time, ‘Dhavadi’ flowers work like a bleaching agent on portions printed with ‘Harda’, creating white areas.
Finishing
After this process, through which the designs turn red, black and white, the cloth is left to sun dry in shade.
Washing
The printed dry fabrics are finally taken to Baghini River for subsequent washes(image 7,8). The iron content of the river and the running water helps in bringing out finer colors and also softens the fabric (For all the previous stages, the artisans use the water stored in in-house tanks).
As the fabric needs to be washed in water several times, firstly to remove the starch and then after the printing has been done, water wastage is involved. Measures should be taken to reuse the water for other purposes. Other wastage includes the biodegradable remains, after natural color extraction.
This region was once ruled by Valkha dynasty, as mentioned in ancient inscriptions. The modern name is probably derived from Valkha.
During 4th-5th Century, the Valkha region was merged in Avanti (Ujjain) region. There are not many evidences indicating the existence of this kingdom, except through the copperplate charters issued by Valkha authorities themselves. We cannot claim whether the area was entirely arid or sandy or covered with dense forests during this time. The inscriptions of those times talk about cultivated lands and farming, contrary to present day condition when not much agriculture is possible owing to the nature of terrain.
The Baghini River acts as a lifeline for the people of Bagh region. The river runs 35 kms south-west and culminates into Narmada. The place could also be named after the river.
The rock-cut caves at Bagh are located in the Vindhya hills in
Madhya Pradesh and are approximately 8 km far from Bagh village, at the bank of a seasonal stream called Baghani. Excavated from the local reddish-pink sandstone are at least ten caves in various stages of completion. Five of the caves appear to have functioned as residences, while others are rectangular pillared assembly halls.
However another interesting local story tells that these caves went into oblivion for quite a time, and many tigers were believed to have taken refuge here. Local people named the caves as Bagh caves, Bagh means tiger in Hindi. Some local folktales also suggest that the place got its name from the tigers which used to take refuge in these ancient Buddhist caves.
Several historians visited these Buddhist caves of Bagh during nineteenth century. In 1850, Dr. Impey visited the region and read a paper about these ancient caves in 1854, which was published in 1856 at Bombay branch of Royal Asiatic Society. With the discovery of the copperplate in cave-2, these caves were dated about 6th-7th century AD. The copper plate grant (as mentioned on the copper plate), refers to the registration of a grant of eight villages situated in the Dasilakapallipathaka for the maintenance and repair of a 'Buddhist Vihara' by Maharaja Subandhu. The Vihara is named as 'Kalyana' or 'The Abode of Art'.
The 'Khatri' community settled in the region almost 500 years ago, they relocated from Sindh in search for better livelihoods. The community first stopped at 'Manawar' and then divided to move towards other areas citing the avenues for economic advancement. When they arrived at Bagh, the Mahajan community persuaded them to settle down in the region, there was also 'Baghini river' which was a much needed resource for their textile craft.
Bagh is located in the Dhar district of Madhya Pradesh. It is located about 90kms away from Dhar city. It is around 150 km from Indore, the commercial capital of the state and is connected to Vadodara through roads. The nearest railway station is situated in Dahode city. It is at an average elevation of 240 metres above sea level. The ancient 'Bagheshwari Devi' temple is also situated here. It is famous for both the ancient Bagh Caves, which are said to be more than half a million years old as well as for Bagh printing.
Bagh is a hilly terrain with thick forest cover and has a considerable tribal population inhabiting it. The village is sparsely populated with the craftsmen families seen constantly at work. The tribal people are trained artisans and they work for the 'Khatris'. They are involved in various steps of the craft.
The nearest railway station to reach Bagh city is situated in Dahode. The local mode of transport is four-wheelers or tempos. A bustling bazaar is where the villagers go for their daily shopping requirements. The population in Bagh has grown over past few years and now it has a few government as well as private English medium schools. A health centre has been opened for medical needs. Various organisations like 'Madhya Pradesh Handicrafts Dept.' have their offices here. Along with cement and brick houses, there are large square plots, tanks and open areas where washing and dyeing is done.
The dwellings and work areas are made of brick and cement. Mostly people have moved on to sturdier constructions from the mud and thatch houses of old times.
Bagh has rich diversity in its population with Bhil, Bhillala, Brahmin, Gauli, Khatri, Mewali, Pinjari, Mansuri, Pathan and Shah Communities. Bhils are the natives, who have been residing in the region since centuries and amount to a very large part of the total population. Bhils are small, dark, broad-nosed, well built and energetic people. Major Hendley once documented the body features of Bhil people; he measured the height of 128 men, the average of which was 5 feet and 6.4 inches. As quoted "The Bhil is an excellent woodsman, can walk the roughest paths and climb the steepest crags without slipping or feeling distressed. He is often called in old Sanskrit works Venaputra, 'child of the forest,' or PÄl Indra, lord of the pass.Bhils obtain their livelihood from agricultural activities, they are agro pastoral people. They also migrate within the region as agricultural and construction labourers.
The Bagh village is flanked by many historical sites. There is an old fort atop a distant hill that is visible from the village. The 'Mahakaleshwar' temple ruins, famous for its stone blocks and elaborate carvings are located along the riverbank. The exact origins of these sites are not even known to the locals.
List of craftsmen.
Team Gaatha
Interview ~ Shri Ismail Khatri
Interview ~ Shri Bilal Khatri