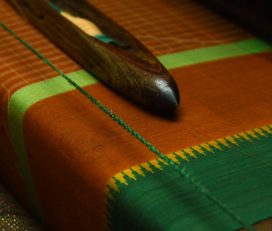
Saree Weaving ~ Nara...
Narayanpet sarees, handwoven in the small, vibrant town of Narayanpet in Telangana, are not confined to ceremonial grandeur or museum-worthy curation.
Narayanpet, Telangana, India...
Rogan painting, locally called Rogani Kam, is an intricate and skillful painting done on inexpensive textiles using a thick paste of castor oil and color. The technique with which it is done has lent a unique identity to this seemingly basic craft. The artwork becomes more beautiful with time and compliments the fabric texture. The elements utilized in Rogan art are earthy, hence they are environmentally friendly. The process itself is so beautiful that a viewer is captivated of instinctive yet calculated moves of craftsmen in imparting color to the fabric.
Rogan painting, locally called Rogani Kam, is an intricate and skillful painting done on inexpensive textiles using a thick paste of castor oil and color.
The biggest problem that the art continues to face is lack of awareness about it, which results in the finished product resembling a printed or embroidered piece of fabric.
Rogan painting was traditionally a seasonal craft, utilized to ornament various traditional attire components like Ghaghra, Lehenga, Odhani, Dupatta, Dharajo, Chabla and the household fabrics such as bed sheets, quilts, pillow covers and small pieces of fabrics used to cover dishes, these fabrics were main constituents of dowry fabrics.
It is believed to have come to India from the Afridis, who were from Syria.The craft was mostly patronized by the Ahirs in Kutch.
The unique feature of this craft is that once the outline of the design is painted over the fabric, it can be folded or pressed against another fabric or the fold of the same fabric to get the second impression of the same design.
Rogan painting was traditionally a seasonal craft, utilized to ornament various traditional attire components like Ghaghra, Lehenga, Odhani, Dupatta, Dharajo, Chabla and the household fabrics such as bed sheets, quilts, pillow covers and small pieces of fabrics used to cover dishes, these fabrics were main constituents of dowry fabrics. Rogan painted fabrics were also mandatory during various rituals including rite of passage. Overtime, these fabrics have been put to commercial uses and products like bedcovers, Sarees, scarves and even wall hangings.
The Rogan painting craft stems from agriculture, which is a major occupation of the village. Castor being the major cultivation draws the natural connection to the craft as the main ingredient of the colors that are manually prepared. The raw materials for the craft are easily available and pose less hassle.A unique feature of this craft is that once the outline of the design is painted over the fabric, it can be folded or pressed against another fabric or the fold of the same fabric to get the second impression of the same design. Along with replicating designs easily, this also ensures that the paint sticks well to the surface.
Rogan art is yet another example of union of civilizations in beaming history of India. The craft of Rogan painted fabrics dates back to many centuries. It is believed to have come to India from the Afridis, who were from Syria. They travelled around the North-Western regions, namely Persia, Afghanistan and Pakistan and the craft was previously concentrated there. It was mainly practiced by the Muslim descendents of the Afridis, it was known as Afridi Lac cloth or Peshawari Lac cloth. Rogan did not find much recognition as an art form until much later, as castor oil, the primary raw material for the craft was associated with hides and leather and it was also used by the lower castes. The process of extraction too proved to be very tedious. The process slowly spread to the other areas and settled along with the settling down of nomadic tribes. The craft was mostly patronized by the Ahirs in Kutch. It was necessary for their women to wear the Rogan painted Ghaghra during the time of marriage. The patterns and motifs largely resemble their embroidery patterns. Presently this craft is only practiced by one family in Nirona.
The motifs and patterns used in Rogan paintings contain both traditional and contemporary designs. The general features are curvilinear patterns repeated geometrically. The linear forms and symmetry is created by the double impression done by folding and peeling cloth, which leaves a mirror image. Phool (flower), Trikhani (three dots), Vesur (wavy border motif) and Jhad (trees) are the oldest found motifs. Animals, trees, humans and objects like bangles also make artistic appearances in the designs. The contemporary motifs include circular/ concentric patterns, motifs forming architectural elements like the Jalis/screens and the tree-of-life motifs.
Most times the fabric consists of thick and multi-layered borders which are filled with intricate and repeated motifs. This leads up to a large geometric central motif. The wall hangings done in Rogan style also feature instances from daily life of villagers, resplendent with trees, cattle and birds.
Boiling the castor oil is a risky process and has to be done with utmost care to avoid fire accidents. The odor and fumes emitted are harmful to the workers. Two or three of the natural colors used in the painting are poisonous if consumed and requires extreme caution by the person who handles them.
With the onset of screen printing, the demand for Rogan painting has lessened. This has led to a great decline in its practice, so much so that only one family presently carries about the craft.
Armed with great expertise and concentration, the craftsmen draw out intricately beautiful patterns with the thick paste of castor oil and color to adorn the fabric. The elements utilized in Rogan art are earthy, hence they are environmentally friendly. The process itself is so beautiful that a viewer is captivated of instinctive yet calculated moves of craftsmen in imparting color to the fabric.
– Castor oil: Oil extracted from castor seeds, when it is heated over ‘Chullah’ (stove) for over 12 hours and then quenched with cold water to produce a residue called Rogan, it is then mixed with natural pigments to get desired colors. This oil is locally available and called as ‘Endo Tel’ or ‘Haran ka Tel’.
– Fabric: Fabric to be printed is brought from local market; this fabric is then cut according to the size of the artwork, for example bed spreads, apparels, pillow covers etc have different sizes. It all depends on the design decided by the craftsman.
– Natural color: Bought in small packets sold by Bohra merchants from Ahmedabad. They cost around 180-400 Rupees per kilogram. It is available in seven colors namely yellow, green, white, orange, blue, pink and black.
– Khadiya Mitti: Traditional name for a white chalk powder used in the preparation of mixture.
– Dandi: A wooden stick used to stir castor oil in the container while it is being boiled.
– Handio: Earlier clay pots were used to boil castor oil, but those have been replaced by aluminum containers.
– Suya: Local name for the metallic rod used to mix color and castor oil.
– Dhakni: It is a traditional name for the cover plate for the container; the containers with color, castor oil and the mixture are all covered with a cover plate. Several ingredient in the Rogan paint are considered poisonous, hence they are stored with utmost care.
– Parat: A common utensil in Indian kitchen, it is made up of metal and has a very wide mouth; it is used for several intermediate preparation of raw materials.
– Chullah: It is a traditional furnace where oil is heated. Structure of Chullah is coated with a paste of clay and bio-waste of the ruminants. The fuel for heat generation, such as wood and dried cow dung is fed from the front and the container with oil is kept on the top of the Chullah.
– Kharal: A grinding stone used to grind the color and prepare the color powder.
– Kanno: container to store the colored paste in water.
– Kalam: A metallic rod is used to hold the oil-color paste while painting on the fabric. These rods have a significant role to play, as the finesse of the patterns depends upon the thickness of the rod.
When this art was being practiced in Nirona 300 years back, many communities embraced it owing to its vibrancy and exclusivity, the fabric took days or even months to finish, hence the villager used to order it before time for a particular occasion. Mostly Rogan painted fabrics constituted the bridal fabrics which were sent with the dowry. In some communities, the dowry was considered incomplete if it did not include Rogan artworks. On other occasions such as major festivals and rites of passage, the Rogan painted fabrics were essential.
Armed with great expertise and concentration, the craftsmen draw out intricately beautiful patterns with the thick paste of castor oil and color to adorn the fabric. The elements utilized in Rogan art are earthy, hence they are environmentally friendly. The process itself is so beautiful that a viewer is captivated of instinctive yet calculated moves of craftsmen in imparting color to the fabric.
Making the paste
The making of the Rogan paste takes place in the outskirts of the Nirona village where there are no residences, since there are high risks of inflammation. The castor oil is boiled in the Handio in the furnace. The temperature has to be controlled as an increase in the heat can result in flames inside the container. White particles are formed over the oil surface, which leads to a yellowish color in time. The oil is taken off the furnace and covered using the Dhakni once it catches flame. When the Dhakni is removed after sometime, the oil attains its pure state which it gets rid of the impurities in the form of fumes. The process of covering and uncovering the Handio is carried out a few more times till a thick brownish gelatinous paste is acquired. The hot oil is then cooled in cold water, which results in Rogan formation in oil, this residue is very essential in the making of color paste. This process usually takes 3-4 days.
Mixing the colors
Natural colors are used for this craft. The color powder is mixed with water over the grinding stone and rubbed into uniform consistency using the round stone. The castor oil is added after this and mixed well over 15-20 minutes. The white chalk powder is added to remove the sticky paste from the stone and it is transferred to small containers filled with water. This ensures that the paste does not harden and remains moist.
Painting on fabric
The craftsman firstly pins the fabric, along with a back-cloth, to his trouser. When he stretches his legs, the fabric too spreads out. The outline colors are done first. The mixture is placed on the palm and mixed. This paste is worked into a pliable paste with Kalam. It is made sure that the paste reeling out of the Kalam is of uniform thickness to be applied on fabric.
Without any pre-drawn sketches, stencils or traces, the craftsman directly starts to apply the paste to a traditional design. The Kalam is worked with one hand, while the index finger of the other guides the flow of the paste from beneath the fabric. The fabric is folded and pressed against this outline design to get a copy of the same. The impressions of the outline designs are only replicated whereas the colors are filled in individually. After the white outlines, the motif is filled in with pastes of other colors.
Drying
Once the designs are done, the fabric is dried in the sun for 4-5 hours. This ensures that the paint is fixed onto the surface of the fabric. The leftover colors from the Kalam are rolled back and stored with water in small containers.
Hardly any waste results from Rogan painting. The process involves expertise and skill; it is more associated with the quality of work, rather than quantity. A fabric piece can take months to finish.
According to popular belief, the water of the 'Sindh River' covered the entire stretch of the Rann of Kutch, the deepest portion being a part of the Nirona port. The village was named after this port.
The present "Rann of Kutch"came to existence after a devastating earthquake which made the river bed rise up. The port of Nirona was a major trade link for the Pakistani traders who traded rice, tobacco and fabric (Ajrakh, zari etc) from Sindh.
Nirona is a village in the 'Nakhatrana taluka' in the Kutch district of the state of Gujarat. The nearest cities are 'Bhuj', 'Anjar' and 'Gandhidham'. The village is around 38 kms from Bhuj and spans an area of 31751.38 hectares. The'Bhurud River' flows on the western side of 'Nirona' and to its south lies the 'Chitrapit' and 'Dounger' hills. A pond named 'Barahsar' lies to its east and the northern side houses a graveyard. It has regular bus connectivity from Bhuj. The major conveyance within Nirona, are buses, jeeps and 'Chakdas' (three wheeler carts).
Nirona has harsh summers but do not face a scarcity of water like the rest of Kutch due to the Bhurud River. The temperatures peak to 46 deg celsius during the summers. The winters too are an extreme with the temperatures dropping to 2 deg celsius. Nirona receives rainfall from the south-western monsoon winds mainly in the month of June to September. Maximum rainfall happens during the months of July and August. The main crops are Bajra, vegetables, rice, groundnut, castor, babul and pulses.
The village has a dam constructed over the 'Bhurud River' by the name of 'Rudranimatani'. The dam aids in irrigation and cultivation as well as water supply throughout the year for the villagers. Nirona has a small marketplace at the entrance marked by a memorial stone. This market hosts small items of daily use and has sweetmeat or snack shops. There is a school and a hospital for the basic needs. Due to the proximity with Bhuj and other cities, the necessary items and services are sourced from the surrounding cities while Nirona remains a quaint village.
The architecture of Nirona retains its rural flavour though it has evolved from the traditional construction to brick and concrete. Small narrow streets meander between the shops and houses. The shops and houses have brick walls covered by sloping roofs with clay tiles. The houses are spaced in a barren expanse with sparse vegetation. Asbestos sheets are used to roof the sheds and barns. Wooden windows have slowly given way to iron grills. The houses of the craftsmen serve as their workplaces too with workshops and furnaces forming the activity areas.
Nirona houses both the Hindu and Muslim communities who live together in perfect harmony. They celebrate festivals like 'Janmashtami', Diwali, Muharram and Eid. A symbol of the peace co-habitation of the two communities is 'Phool' peer, who was a Sufi saint who was originally a Hindu but was a disciple of a Muslim master. The festival honouring him is celebrated in the month of 'Magh' for two days.
Marriage is an important event in their lives as it signifies continuing tradition. The dowry system is still prevalent in some areas. Girls start fabricating embroidered items for their dowries at a very young age under the guidance of the older women in the house.
Nirona' has a population of around seven thousand people. It houses different communities like the 'Ahirs', Muslims, 'Harijans' and 'Bhanusali Rajputs' who follow a patriarchal system. Agriculture and handicrafts are their main occupation.
'Nirona' is famous for its crafts of metal bells, lacquer ladles and Rogan art.
List of craftsmen.
Team Gaatha