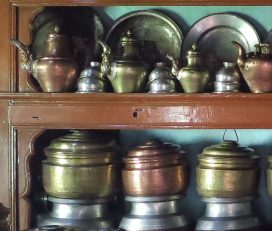
Copper Craft ~ Chili...
Copper and brass have played a significant role in fulfilling these needs. Even today, in most traditional Ladakhi kitchens such utensils are commonly seen
Chiling Sumda...
Dabu, derived from ‘Dabanna’, means ‘to press’ and is a mud-resist block-printing craft practiced in the alluring village of Akola in Rajasthan. Local women from the Jat, Gujjar and Gadariya tribes adorn the fabric thus printed. What sets this craft apart is the usage of the traditional exclusive Akola motifs in an array of bright red and Indigo, printed using carved wooden blocks.
Akola is a mud-resist block-printing craft cluster in the Udaipur district of Rajasthan.
The colors of the sky – blue of the day, indigo of the night, red of the sunsets are associated with Akola print.
Dabu, derived from ‘Dabanna’, means ‘to press’ and is a mud-resist block-printing craft. Dabu prints remain the primeval printing method.
Earlier, printing with a mud paste helped resist the required designs and patterns, but this slowly shifted to the use of tar in a quest for obtaining more refined designs.
Yes, the artisans use natural colors, like bright shades of red and indigo.
Before the advent of industrial textiles, printers were an exclusive community who were highly valued as they catered to the needs of the royal families initially before printing for other communities as well. The dabu or mud-resist printing of Akola traditionally adorned two specific types of fabrics- Phetia and Nandna, worn by the women of Jat, Gujjar and Gadariya communities.
‘Phetiya’, the flowing Ghagras (traditional long skirts) of women were usually in combination with a Bandhej Lugda, a long fabric draped over the head. Phetiya, made with just a single line of stitching, was crafted by joining the extreme ends of a 8-12 meter fabric, though the length varied according to the body type and social stature of the individuals. The traditional ‘Lal Titri’ Akola print adorned this piece of cloth in bright shades of red and indigo.
Like the essence of earth, the Akola Dabu prints remain the primeval printing method. Like the patterns, these fabrics are deeply embedded in the cultural identities of various Rajasthani communities. Block makers intricately carve out beautiful blocks in the local area, and the native craftsmen known as Chippas specialize in printing. The forms in which these fabrics are worn are changing with time, yet the soul of the craft is carried forward, unhampered, by the motifs and hues.
Today around 200 men and women together practice this craft in this quaint village where the Beduch river provides water and washing grounds on it mighty banks. Various motifs like Kahma, Lal Titri, Dholika and Kantedar were a priced possession amongst women of the Jat and Gujjar communities. Their traditional long ghagras known as ‘Phetiya’ were enveloped by the exclusive Akola prints.
In the Akola village, it has been a legend, that the colors of the sky – blue of the day, indigo of the night, red of the sunsets – are replicated in the regional attire, owing to their belief in the gods of nature and the worship of what gives them life. They narrate their relationship with the craft as ‘the lock carvers sculpt the blocks, the earth lends mud and the river bestows water and that is their possession of a traditional attire, which brings them closer to nature and the worldly orders’.
The origins of the ancient craft of hand block printing can be traced back to the Indus Valley civilization. Some historians claim its roots to 3rd century B.C China from where it is supposed to have travelled to India in the 18th century with Gujarat and Rajasthan becoming the most prolific producers of printed textiles in India.
The Hindu caste of cotton printers and dyes known as Chippas were the prominent printing community in Rajasthan. The word is derived from ‘chhapna’-meaning ‘to print’, because the Chhipas printed coloured patterns on cotton cloths with wooden stamps. They worked in harmony with other related communities of Neelgars (indigo dyers), Rangrez (dyers) and dhobis(washermen).
The Chippa communities migrated to areas close to rivers that provided water for washing and mud for resist printing. Replenished generously by nature, it is said that they were employed in India during 8th century AD. The oldest specimen found of Dabu printed fabric in Central Asia indicates this. Dabu printing style was widely practiced in villages of Tarapur, Bhilwara, Pahuna and Akola. Dabu printed cloth was widely adorned by the local women on a daily basis. The village is a self-sufficient system for Dabu printing. Block carvers sculpt the blocks, the earth lends mud and the river bestows water.
The craft is supposed to still exist in its beautiful form in the quaint village of Akola in Rajasthan, where the 7th generation of craftsmen still keeps intact the soul of the tradition.
The word Dabu comes from the ‘dabaana’ , meaning ‘to press’, is a craft of beautiful crafted motifs on fabric created for the local women. The patterns are traditional, handed on intact, over generations. The motifs are picked from nature and objects around them and then crafted onto wooden blocks by skilled carvers and block makers. All the women of the Jat and Gujjar tribe wore the Akola print fabric, as it was most comfortable during their daily activities. The craft in Akola had a beautiful plethora of 14 traditional block designs that exclusively printed the fabric pieces.
These designs slowly faded away with time and at present 4 main motifs are known- Kahma, Lal Titri, Dholika and Kantedar.
The Lal Titri motif prominently known as the Akola print beautifully covered the Phetiya’s, the long flowing skirts of women in remarkable shades of alizarin and indigo. The Phetiya was spread with an overall print in the ground and a zigzag line like border.
With time there has been use of new blocks and patterns for the contemporary market. New product range has been derived according to the market needs.
Wide ranges of yardages are printed for developing different range of products in accordance with the changing demands. The patterns and motifs are engineered for products like dupattas, stoles, saris giving details of borders, pallu and main body. Earlier, printing with a mud paste helped resist the required designs and patterns, but this slowly shifted to the use of tar in a quest for obtaining more refined designs, which was difficult with the use of mud, which mostly cracked and changed the look.
The mud resist Dabu printing technique is a very lengthy and labor-intensive process which at the same time does not provide enough livelihood to the artisans and their families. This has discouraged the present generations to see much scope in this age old family tradition and look for other means of livelihood.
The tar used for resist is continuously heated and the fumes developed, prove hazardous for the printers. The ash, which is sprinkled on the cloth fumes in the workspace, is to a certain degree another pertaining hazard to the printer and others working around because it causes suffocation from external particles in an almost closed space. New designs and patterns are used these days to satisfy the market requirements in cities and neighboring towns. There has also been a considerable fall in demand from the local people for the traditional patterns and motifs.
Resist dyeing has been an age old craft that has been explored to print fabrics in beautiful forms. Akola has given a new dimension to this technique with resisting the cloth using blocks dipped in tar. The fabric is dyed in indigo and the tar is washed off, resulting in bright rich textile pieces.
Fabric: Cotton fabric mostly of the count 20X20 is sourced from Kishangarh.
Pigments: The pigments and dye stuff are procured from Udaipur.
Tar (for Dabu): A mixture of tar, oil and Rogan is printed with blocks on the fabric and resists the flow of colour in the area during dyeing.
Ash: Ash(rakh) is spread onto the tar printed areas of the cloth, to help the drying process
Naphthol: Alizarin was traditionally used in the process but is now replaced with Naphthol.
Gaund: The printed fabric is layered with a gum solution to enable the easy removal of tar during washing.
Printing Tables: Small wooden tables are used for placing the fabric and block printing. Its size is around 150cm x 60 cm.
Dyeing Trays- Trays made of wood or plastic are used to fill the dye
Blocks- Wooden blocks with required patterns are used to print on the fabric
Boilers- Huge ‘Kadhai’ like vessels with boiling water to help in the process of removal of tar from the fabrics. These big boilers were set up in Akola with support from the Government.
Resist dyeing has been an age old craft that has been explored to print fabrics in beautiful forms. Akola has given a new dimension to this technique with resisting the cloth using blocks dipped in tar. The fabric is dyed in indigo and the tar is washed off, resulting in bright rich textile pieces.
-The fabric is first printed with Naphthol, in areas where the design is required in red colour. Naphthol dyes are insoluble dyes, which are used by applying a Napthol to the fiber and then combining it with a diazotized base or salt at a low temperature which produces an insoluble dye molecule within the fiber giving the required colour.
-The fabric is left to dry in the sun.
-The fabric is dipped in a red salt, which reacts with the naphthol to give a bright red shade to the printed areas.
-A printed fabric is now dipped in a gum (gaund) solution that later helps in the removal of tar which acts as a resist in the process.
– A mixture of tar, oil and rogan is now is applied to the carved wooden blocks which is then printed on the cloth in the areas that have to be resisted. Earlier a mud paste was used for this purpose.
– Ash is then sprinkled on the fabric as it helps in quick drying of the printed fabric along with avoiding the sticking of the cloth together.
-The process of indigo dyeing is now carried out to dye the fabric. It is a cold dyeing process where the cloth is dipped in a solution of Indigo dye. When dipped, the cloth turns to a rich green color which turns to a deep indigo shade once its exposed to dry air and it undergoes rapid oxidation. The process is repeated again to obtain the required shade.
-The printed and dyed fabric is put in boiling water to remove the tar which comes off the fabric, floats in water and can be reused.
This process is used to develop the traditional Akola print in red and indigo colors. In case of indigo dyed dabu resist fabrics, the cloth is printed with blocks dipped in tar and sprinkled with ash. This acts as a resist and prevents the dye to penetrate in the certain parts of the cloth. The cloth is then dipped in a solution of indigo dye. A deep indigo shade is obtained due to a rapid oxidation process on exposure to air. The printed fabric is washed in boiling water to remove the tar, most of which is reused.
Water wastage is involved, as the fabric needs to be washed in water several times, firstly for dyeing and washing the fabric and later for removal of the resist. There need to be measures to reuse the water for other purposes. Also, with the advent of chemical dyes and other mordents, the residue water which washes back into the ground is polluting the groundwater of the region, and will be causing damage to the ecosystem in the times to come.
Hundreds of years ago, Rani Rathorji of Mewar established a village for the Chippa Community by the banks of the Beduch river. There was a temple constructed for them along with hundred houses. This formed the beginning for the settlement where they started the craft of printing on the river banks seeking inspiration from nature and everyday elements. Today around 200 people practice dabu-mud resist printing on fabric.
Akola is a village in Bhopalsagar Tehsil in Chittorgarh District of Rajasthan state in India. It belongs to Udaipur division. Located about 52 kms towards west from District headquarters Chittorgarh, 13 kms from Bhopalsagar and 339 kms from Jaipur.
Akola is surrounded by Kapasan Tehsil towards North, Mavli Tehsil towards west, Bhinder Tehsil towards South, Railmagra Tehsil towards North. Rajsamand, Nathdwara, Nimbahera and Udaipur are the nearby cities to Akola.
The village falls under a subtropical climate, and the weather is dry for a major part of the year except in the monsoons. The summer months span from April to June with temperatures peaking up to 45 degrees Celsius. The monsoons come from July to September. The winters are during the months of October, November, December and January. The maximum temperature at this time would be 25 degrees Celsius and the minimum is as low as 13 degrees Celsius with January being the coldest month.
The villages receive water supply throughout the year from the river Beduch and with use of hand pumps and tube wells. They also have good water storage facilities like wells and tanks. The nearest major railway station to Akola is Chittorgarh (COR) at a distance of 23 kilometers and the nearest airport being in Udaipur, at a distance of 35 kilometers.
The village is equipped with basic needs like a market place with small shops, medical facilities and temple. Schools are equipped to impart primary education. For higher education, they go to the schools in the nearby towns of Udaipur, Chittorgarh and Fatehnagar. It has a gram panchayat and the population of the village is around 15000.
A community center has been opened for social gatherings and events. Along with cement and brick houses, there are large boilers established with the support from the Government to assist the Chippas in washing and dyeing.
The old houses in the village are mud constructions covered with thatched roof tiles. A lot of people have moved on to 'pucca' cement constructed houses, some of them with cattle sheds. Spread with small eateries, tea stalls, provision stores the main road attracts a lot of activities. Small gullies run throughout the village and market places. There is a bridge across the River Beduch which connects Akola with other important nearby cities.
The culture of a place is a reflection of its society. Observing the culture of the Chittorgarh region, gives one a fair idea about the traditions and practices that are still followed by the locals. The festivals, the events, the attractions, all reflect the culture of Chittorgarh in one way or the other. Tourism has picked up in the last decade or so and the local people are generally quite friendly towards the tourists. Being a majorly Hindu region, all Hindu festivals are celebrated with much valor. Bright chunaris and turbans speck the area with the massive fort in black stone standing tall as guard of the region.
Falling in the Chittorgarh region, which is famous for its massive black stone fort, considered to be one of Asia's largest, Akola is a small town which has gained its popularity over the years as one of the premiere hubs of hand-printed textiles in the country with its unique techniques, usage of materials and motifs.
List of craftsmen.
Team Gaatha