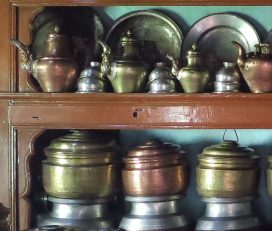
Copper Craft ~ Chili...
Copper and brass have played a significant role in fulfilling these needs. Even today, in most traditional Ladakhi kitchens such utensils are commonly seen
Chiling Sumda...
‘Bhujodi’ weaving is a craft that takes its name from ‘Bhujodi’, a small village in ‘Kutch’ where this craft is practiced. This village of weavers is famous for its exquisitely woven traditional textiles of ‘Kutchi’ shawls, traditional blankets and stoles.
'Bhujodi' weaving is a craft that takes its name from 'Bhujodi', a small village in 'Kutch' where this craft is practiced.
Traditionally, the shawls were made from wool but the craftsmen now explore other materials like silk and cotton. The craftsmen weave traditional motifs as well as contemporary modifications suggested to them by the designers. The shawls are usually adorned with several borders on the shorter length side. They are made in natural colours of wool or dyed to suit requirements.
Bhujodi weaving is done on traditional pit looms in the weavers' homes.Traditionally, the shawls were made from wool but the craftsmen now explore other materials like silk and cotton. They are made in natural colours of wool or dyed to suit requirements.
Kutchi’ shawls, traditional blankets and stoles. Though carpets and placemats are also being made lately.
Bhujodi is famous because of its ‘Kutchi’ shawls that received the ‘GI (Geographical Indication) tag’ and is recognised all over the world.
Bhujodi is a small town, located 8km southeast of Bhuj.
‘Vankars‘ or the weaver community are behind Bhujodi
In Bhujodi, weavers mainly create shawls and stoles, though carpets and placemats are also being made lately. Traditionally, these products were created to bear the harsh winters, but now cotton is also used to weave summer garments. This has ensured a flourishing yearlong market for the artisans
It takes around 10 to 12 days to weave a single shawl and around 5 to 6 shawls of the same model are woven each time. The craftsmen work by hand on patterns and intricate designs, which can take months to complete. There are many awards and accolades to their credit. Vishram Valji, a seasoned weaver in Bhujodi won the President’s award in 1974, for an elaborately patterned shawl created by him. This beautiful piece of art took him an entire year to complete. The ‘Kutchi’ shawls have also received the ‘GI (Geographical Indication) tag’.
The division of labor in Bhujodi weaving is decided by the amount of physical exertion and stamina required. Men sit at the looms, while the women do the yarn making and ready the looms. The intricate patterns are worked by hand, as they go between the threads of warp and weft. This unique technique of weaving motifs, by lifting the warp with fingers without a ‘Dobby’ or ‘Jacquard’ and the ‘Athh tako’ technique (with four peddles in the loom) is unique. The craftsmen train their children to weave from a very early age. The children learn by watching their elders at work and also by helping out.
A popular belief says, that 500 years ago the daughter of a rich ‘Rabari’ family came to Kutch after her marriage. A weaver was sent along with her as part of her dowry, so that he could weave whatever she desired. The family of this weaver grew into a large community over time and they came to be known as the craftsmen of Kutch.
Bhujodi weaving is a craft practiced by almost 200 weavers of the village. The nomadic tribes that were on the move needed warm clothing to bear the harsh winters. Traditionally, weavers would use hand spun yarn provided by the ‘Rabaris’, a nomadic community of sheep and goat herders. Among them ‘Meghwals’ and ‘Marwadas’ developed a unique style of weaving, that provided the Kutchi community with blankets, cloth and traditional dress fabric. They came to be known as the ‘Vankars‘ or the weaver community. The ‘Vankars’ slowly developed designs that suited the requirements of the ‘Rabari’ community, and so the designs became characteristic of this clan. This helped in distinguishing the work of communities separately, even though they worked interdependently as the craft grew.
Traditionally, the shawls were made from wool but the craftsmen now explore other materials like silk and cotton. The craftsmen weave traditional motifs as well as contemporary modifications suggested to them by the designers. The shawls are usually adorned with several borders on the shorter length side. They are made in natural colours of wool or dyed to suit requirements. Some of the popular colors are Indigo blue, red, green, off white, black etc. The most popular embellishing styles from Kutch are ‘Batik’ work, ‘Bandhani’ (Tie Dye) patterns, ‘Ahir’, ‘Rabari’, ‘Mutwa’, ‘ Abla’ embroideries (mirror), ‘Aari’ or ‘Mochi’ embroideries (chain stitch) and ‘Sindhi’ embroideries (Kutch work). Many designs have linear patterns interspersed with motifs running throughout the body. Sometimes even tie-and-dye technique is incorporated to add value to it.
The border sizes differ from shawl to shawl. The common sizes are 3, 9 or 18 inches. The borders of 18 inches are mostly used in shawls for males. The finishing of the shawls or stoles is done using colorful tassels, which is a characteristic feature of the Kutchi weaving.
Hiraghiryu – This is a traditional ‘Dhabda’ or shawl and is woven in two parts due to the small width of the looms. It is then pieced together using a traditional hand-stitch known as ‘khelavni’.
Jhar – This motif is said to resemble a tree.
Chaumukh – This is a four-sided motif made by lifting warp threads. This is a distinct feature of the Kutchi weaving style. It has a religious connotation and represents the Mandala.
Sachchi kor – This is a warp based design having a pointed temple-like figure with a thick base. This is done on a black and white weave.
Sathkhani – This is a pattern that requires seven steps in its making.
Dholki – This is a drum shaped motif.
Wankia –This motif resembles a crooked or ‘zig-zag’ line. The inspiration for this is said to be the pattern created by a cow as it walks on soil.
Bhujodi weaving is a craft that requires high levels of concentration and expertise. It is a physically strenuous craft that requires the craftsman to hunch over his loom for days together. This causes health concerns like sore arms, poor eyesight and stomach problems. This is a big cause of worry for the weavers.
The craft is time consuming as it takes more than a fortnight of hand weaving at a stretch, all the warp put around the drum at once. The weaver has to handpick the warp and weft from memory and any error will mean starting the entire process all over again.
‘Taana Baana’ (warp & weft) are used to create shawls and stoles in both mellow as well as eye-catching colours. These designs that are woven on traditional looms using wool or cotton yarn have intricate motifs that speak of the local culture in miniature.
Wool – The craftsmen procure it from the sheep reared by the ‘Rabari’ clan as the wool from local sheep is not of best quality. One local sheep gives only about 200-250 gm wool. Today the situation is different as weavers now use 4 types of yarns -100% Marino wool (from Ludhiana), Acrylic, local wool and silk (from Bihar).
Silk – Brought in from Bangalore.
Acrylic – Brought in from Ludhiana.
Cotton – Fine cotton which has 70 threads per sq. inch.
Loom – The traditional pit loom is used for Bhujodi weaving. A large wooden frame or ‘Thambla’ is fixed into the ground forming the main structure of the loom. The ‘Pankha’ or beater and the ‘Lathe’ called ‘Velan’ are fixed onto this. The ‘Pankha’ consists of two strips of wood into which the ‘Phani’ or ‘reed’ is set. The ‘Phani’ is made of bamboo and the number of dents formed between each bamboo stick corresponds to the number of threads in the warp. The ‘Raach’ or shafts consist of nylon threads suspended between two aluminum shaft sticks. Two of these are joined together to form a harness. The ‘Gendha’ or ‘shuttle picker’ is situated one on a long narrow tray-like wooden structure on either side of the beater. It receives and throws the fly shuttle from one side to another.
The fabric after being woven to a considerable length is wound on another square piece of wood across the pit, which is called ‘Tor’.
Killori – This is a brush used for combing the warp when it is set. The bristles are made from a plant which grows in the ‘Rann’ area. It can last for as long as 10 to 15 years.
Warp stand – This is used to support the warp when it is in the process of being set. The weavers now use metallic stands as they are more durable.
Bobbin winder – A tool used to convert bigger ‘hanks’ into smaller ones and then into ‘Bobbins’.
Treadles – These are rectangular wooden blocks mostly four in number which are connected to the harnesses. The shafts are lifted by pressing them.
‘Taana Baana’ (warp & weft) are used to create shawls and stoles in both mellow as well as eye-catching colours. These designs that are woven on traditional looms using wool or cotton yarn have intricate motifs that speak of the local culture in miniature.
Preparing the threads or Warping: The yarn is of 2 x 60’s count and is looped around the wooden pegs of a wooden frame. This way a length of 55-60cm can be easily achieved. The yarn is then stretched out and coated with starch. The warp is supported by a ‘Jaal’ or wooden stand, placed on an empty stretch of land. The threads are then rolled into bundles and new warp is joined. This process is called ‘Shantni’ and is done by smearing ash on the hands for ease of handling the yarn.
Dyeing the wool
Natual colours like black, white and brown were used in this craft. As time passed and demands increased, weavers began exploring other vibrant colours. Now vegetable dyes as well as acid dyes are used.
Weaving
The weaving is done in a traditional pit loom with a foot pedal. This simple process is known as ‘Taana Baana’. The shawls are woven in a plain weave with extra weft ornamentation. It has one ground pick and one extra weft pick for the motifs of the borders. The loom used is a ‘throw shuttle’ or a ‘fly shuttle’ pit loom.
Finishing:
The main residents were the 'Rabaris', who have been cattle herders. The originally came from Afghanistan about 4000 years ago, moving down to 'Jaisalmer' and then 'Kutch'. The 'Rabaris' were nomads and would stop wherever they would find a lot of water and space to stay. Having found a temporary place they would construct their 'Bhungas' and cattle sheds. It is said that in 'Bhuj' near the 'Hamirsar' Lake, there lived 'Bhoja' and 'Hamir Rabari'. Once the king of 'Kerakot' was hunting in the area and his hunting dogs were stopped in their tracks by a small rabbit. The king was taken aback by the bravery of the rabbit. He inferred that the land is precious, that even small animals are brave there and decided to annex the region. The king called the 'Rabaris' 'Bhoja' and 'Hamir' to ask whether they would give him the land. They agreed but asked where they would they go if they should have to leave the land. The King told them that they can reside in the vast land nearby. Thus, the land which he gave Bhoja came to be known as Bhujodi and the lake was named after Hamir. Therefore the village was established much before Bhuj. Wherever the Rabaris lived, the Vankars followed.
Bhujodi is located in the Bhuj district of Kutch in Western Gujarat. A town also by the name of Bhuj is located 8kms away from Bhujodi and is the district headquarters. The port town of Mandvi is 55 kms away from Bhujodi. The village is a 2km walk further from the Bhuj-Anjar highway and is connected by road. The state capital Ahmedabad is 398kms away.
By Air
The nearest international and domestic airport is Ahmedabad.
By Rail
The new Bhuj railway station is 1km to the north of the Bhuj town. Two daily express trains, the Bhuj Express and the Kutch Express, connect Bhuj to Ahmedabad (8hrs) and on to Mumbai (16hrs.) However, both trains pass through Ahmedabad in the middle of the night, as the schedules are designed to depart and arrive and reasonable hours from Bhuj and Mumbai, not Ahmedabad.
By Road
State transport, luxury coaches, auto rickshaws and taxis are available between all the centers in Gujarat. Bhuj is connected by the state highway upto Bhachau (85 kms) and from there upto Ahmedabad by the national highway number 8A (310 kms). Chakras are big auto rickshaws that shuttle between the town and village making frequent stops. Jeeps travel in the same manner only making lesser stops.
The region has a tropical monsoon climate with an average annual rainfall of approximately 14inches. The temperature ranges from 2 degrees Celsius in the winter to 45 degrees in the summer. The three main seasons are - summer from February to June, monsoon from July to September and winter from October to January.
The village is managed by the village 'Panchayat' (local self-government at village level). There are three main schools in the village, out of the three, one is for the 'Rabaris' and the other for 'Vankars'. There is also a CBSE (Central Board of Secondary Education) school with hostel provisions. A big pond in the village provides water for cattle bathing, washing and other such activities. Drinking water is supplied by the many bore wells in the village. Earlier a massive earthquake struck the village and was the epicenter. Many houses were severely damaged. The 'aritas India Foundation' provided much support by constructing the present day 'Pink houses' in the village.'.
The houses now are made of concrete and are much more stable. Sheds have been constructed to house the looms. The earlier traditional houses were made of mud and wood. The circular huts of the 'Rabaris' are known as the 'Bungas'. They decorate these huts with mud in traditional patterns called 'Maati ka kaam'. Mirrors are also used to decorate the walls.
The layout of the village is in a 'Jhampa' pattern. This is a settlement pattern in which a street has all the 'Vankar' houses on either sides of it, leading to a dead end on one side. In this closed set up all the families live inside forming a small colony. The Rabaris have their houses outside of the 'Jhampa'.
The Vankars and the Rabaris belong to the Hindu sect and worship Hindu Gods including 'Lord Shiva' and 'Lord Ganesha'. Before any weaving begins, special pujas are performed to worship 'Lord Ganesha'.
Marriages are held during the Hindu months of 'Vaisakh' after the harvest season is over. Marriages in the same sub-caste, is strictly prohibited. Death is also celebrated with a mourning feast called the 'Parojan'. Every family has a shrine which is of the patriarch of the family.
The festival of Diwali is enjoyed with much fervor, with lighting of oil lamps called 'Diyas' and drawing of 'Rangolis' in the front yard. Before Diwali, Vankars stop their work on looms and on the night of Diwali, 'Meriya' custom is observed. The cloth woven between two shawls is taken and is tied to a stick. This is then lit up as a torch called 'Meriya' and fixed in the fields.
The staple food of the people is 'Rotlis' made of millet and eaten along with butter milk and jaggery. 'Khichchdi' made of mashed rice and dal is also another staple dish. The food is mostly dry and easy to store.
The Hindu communities of the 'Vankars' and 'Rabaris' comprise the population of this small village. The 'Vankars' belonging to the 'Harijan' caste (scheduled caste), come under the 'Meghwal Marwars'. The 'Rabaris' are categorized into four groups according to their settlement in Kutch - 'Dhebaria', 'Kachchi', 'Pataniya' and 'Waghadia'.
Majority of the 'Vankars' stick to their family occupation, weaving. If they do not own looms, they work as paid labor for other weavers who own looms. Many of them have taken to alternative jobs like working in factories, 'Chakra' drivers and cattle rearing.
The 'Ramdevji Pir' temple is the biggest temple in the area. Ramdevyji pir belonged to a scheduled caste and was adopted by an heirless king. He strived for the betterment of the craftsmen and is worshipped even today.
List of craftsmen.
Team Gaatha
Interview Vankar syanji bhai (01/20/2011)
Interview Moorji bhai (01/20/2012)