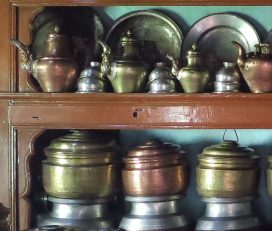
Copper Craft ~ Chili...
Copper and brass have played a significant role in fulfilling these needs. Even today, in most traditional Ladakhi kitchens such utensils are commonly seen
Chiling Sumda...
The crafts of West Bengal are renowned all over the word, mainly because of their pastoral charm. Amongst all the crafts of the state, the art of clay doll making is amongst the most popular ones. These beautiful, lively clay structures are adorned with vibrant colours. The art of doll making has thus become an integral part of West Bengal’s culture. These are real-life stylized dolls depicting various social scenarios in India. With their intricate detailing and precision that imitates the expressions and features of an actual human, these dolls are a representation of different individuals and their stories throughout the ages. The craftsmen engaged in this doll making are known to bring life to these dolls through the magic in their fingers and years of experience.
The craft of the Ghurni clay doll making is believed to be 200 – 250 years old and are predominantly practised in Krishnanagar in Ghurni district of West Bengal.
The earliest known Ghurni figure modeler was Mohan Pal (born in 1745); he and his contemporaries were brought to Krishnanagar to create religious deities. Since then the Pal or Paul community, have been the custodians of the clay craft for nearly four centuries in Krishnanagar.
Krishnanagar is famous for the craft of the Ghurni clay doll making – a tradition that is nearly 200 years old.
These beautiful glimmering clay dolls are mainly used as decoration pieces or as gifting items. Since a large variety of figurines are made- all the way from insects, to representation of folklore, to popular human figures to animated cartoons- these clay dolls fit perfectly in every setting. The colours and hues of the dolls add a pop of colour and aesthetic to any room. These clay dolls can be seen as storytellers within themselves since they represent a certain story of a certain individual and truly capture the essence of history.
These clay dolls from Krishnanagar are considered to be unique and special because of their designs, colours, techniques and the history attached to them.
The making of miniature clay dolls (2 to 6 inches in height) from Krishnanagar is purely an artisan’s skill-based work and is known for the detailing involved. A wide variety of day to day objects are made in this craft ranging from fruits, vegetables, animals, birds to gods and goddesses. The real specialities of this craft are to capture and recreate everyday life, work, mood and characters – farmers, weavers, rag pickers, basket makers, umbrella makers etc. The detailing given to each object and character through intricate artistic handwork & colouring gives these clay dolls close to reality representation, thereby contributing to the uniqueness of this craft of West Bengal. The utmost care, dedication and hard work that the craftsmen put in results in the clay dolls appearing to be extremely realistic in terms of expression and detailing which further makes this craft famous.
The clients for this craft range from national to international. At the national level – the local buyers, a tourist visiting their outlets in Krishna Nagar and other parts of West Bengal, at craft exhibitions organised in different parts of the country, we have a large display of these dolls in the Shankar’s Doll Museum in New Delhi. Moreover, Exhibitions of Krishnanagar dolls have also been held in London, Paris and Boston. The Ghurni clay models have also won medals and certificates at international exhibitions.
According to myths and traditions, clay art was originated from the Potter. Potter is the synonym of ‘Prajapati’ and is also revered as Lord Brahma, the creator, created human beings from clay. According to mythology, when Lord Shiva came to marry Sati, the need for an earthen pot was required. So Lord Shiva took two beads from his necklace and gave birth to male and female forms who are the first moulder of “Kumbha“. So the potter is also known as ‘kumara’.
This craft of clay doll making is 200 – 250 years old and are predominantly practised in a place called Krishnanagar in the Ghurni district of West Bengal. According to the doll makers, the area where this craft is located and practised is mainly in Ghurni since the proper image-makers have settled here. The purpose of this effort is to preserve and revive the traditional heritage of doll making.
Maharaja Krishna Chandra (1710–1783), a patron of arts, supported the production of clay dolls. As a pioneer who started Kali pooja, Jagadhatri pooja for the first time in Bengal, he encouraged the local artisans and brought in more potters from Dhaka & Natore districts of Bengal to the Ghurni- a neighbourhood of Krishnanagar. Hence, started the Bengali tradition of clay image-making, which is indeed a celebrated feature of the culture to this day.
Craftsmen practising the craft of Krishnanagar doll making belong to the group of the community called ‘Kumbhakaras’ constituting potters and clay modellers. In Krishnanagar over 300 people are involved in this craft including women and children. Initially started with four or five families, now it is a big community. As a community, they are not much integrated. The decline of feudal zamindari culture and loss of their patronage has adversely affected this craft.
The clay dolls of Krishnanagar generally capture the ordinary Bengali men and women at work. These dolls showcase a realistic representation of various emotions and objects through the craftsman’s skill and experience. Anybody who sees these dolls could easily interpret the scenario and feel that the craftsman wants to depict and portray. As an example, you can see basket weavers working with bamboo bark; a Brahmin priest doing puja in front of a Shiv Ling; umbrella repairmen fixing broken handles; Santhal tribal men dancing with the dhols; rural Bengali men and women carrying firewood home; an iron welder working his craft; a man making rope out of cotton; and male and female devotees with manjiras and dhols participating in kirtan.
The dolls are made with soil from the river Ganga (recently declared the National River), called “etail,” leftover once the tide recedes. The clay dolls of Krishnanagar (in Nadia district) are famed for their realistic depiction of everyday village life – fishing, farming, rag picking, basket making, cooking, cleaning and worshipping, among others – and subjects like fruits, vegetables, birds and animals. They have been a part of the legacy of the native potters for over five generations.
Exquisitely crafted, these mud dolls and figures in various sizes have delighted connoisseurs and laymen alike, with their real-life depictions of life around them. Figurines of gods and goddesses, Bengal rural scenes of thatched houses and palm trees, cobblers, priests, miniature Eskimos, birds, animals, fruits, vegetables, etc., are replicated with precision and consummate artistry. The detailing of these figures, especially in their clothes and accessories are brought about by tools to create that single or double pleat, a crease here and there, and with a few strokes, life is infused into their eyes.
The model making involved in this craft purely depends on the hand skill of the craftsman. There are different types of models – depending on the volume they can be categorized as small, medium and large.
Just like other handicrafts of India, there are several challenges associated with the clay dolls as well which prevent them from achieving the status and recognition they deserve.
In Krishnanagar, out of 100 craftsmen present today, hardly 15-20 could be counted as well flourished. A large number of craftsmen are still struggling and earn very low income in a month. This could be one of the major reasons that this craft is slowly dying out. This is mainly due to 3 reasons- first, there is high financial instability, second, the sales of these dolls keeps varying throughout the year making it difficult for these craftsmen to receive a constant income, and third, there is a lack of support and recognition.
Only 10 in every 100 craftsmen today believe they are doing well at doll making as a profession. the poor knowledge amongst the artisans about sales and marketing, the market is defiantly not as commercially viable as it can be. Besides, the craftsmen as a usual trend today find it more fulfilling to move to bigger cities like Calcutta where occasions (seasonal and otherwise) give their skill the raison d’être to persist. Nevertheless, doll making is passion personified and an admirable piece of indigenous art, which will find an increased number of takers as public awareness increases.
The process of making these beautiful Krishnanagar dolls is one that requires immense detail and accuracy. Moreover, it is an extensive process that is carried out through several stages.
The clay dolls of Krishnanagar require the following raw materials-
• Clay & Admixtures
Locally available clay from the river Jalangi and other places within Krishnanagar is used in this craft. This particular type of clay is most suitable for the kind of work the craftsman does This local clay is added with different admixtures to get different desired results such as sandy soil, rice husk/ saw dust, cotton etc.
• Metal wires
These are used for giving reinforcement to different components of the doll so that the clay does not break down.
• Colours
Colours give life to Krishnanagar dolls and makes them look more realistic. Powder colours mixed with water and glue, poster colours, different dyes and pigments are used in the colouring process. Colouring is followed by applying varnish mixed with kerosene to give the glossy finish to dolls.
• Fabric
After the clay models are made, coloured and polished, they are dressed up with miniature clothing based on the character they portray.
• Fuel
This is used for lighting the furnace.
Mostly the tools used by these craftsman are customized and as per their requirement then make and modify their tools. Most of the tools used by the craftsmen are used generations after generation.
The following tools and technology are used in the process of making the clay dolls of Krishnanagar-
• Chirage– This tool is made of bamboo and has a flat and pointed tip. It is used for intricate detailing work.
• Basua– This tool is made out of bamboo and Kanini wood with blunt tip. It is used to create folds of cloth which they simulate from clay.
• Knives – Different sized knifes are used for scrapping work.
• Brushes– Brushes of different sizes and shapes are used depending on the need. Previously foreign made brushes were used but now days they make their own brushes. Brushes are made out of horse hair/ goat hair/ hog hair. Horse hair is soft and hence used to avoid scratches. Goat hair is used in making white colour and for painting. Dog hair brushes are used for cleaning and brushing work.
The process of making these beautiful Krishnanagar dolls is one that requires immense detail and accuracy. Moreover, it is an extensive process that is carried out through several stages. These stages are as follows-
1. Model Making
This is the first step for making the clay dolls and it begins with planning out the desired model. In this step, the whole figure is divided into various components and made one by one. These individual components get added on a reinforcement structure made out of metal wire that acts like skeleton for the model. The reinforcement structure should thus be made first as per the posture required for the model. For example: if the craftsman intends to make a human figure in sitting posture, he first visualizes the entire model. He then divides the human figure into various components keeping in mind the sitting posture. Based on the posture, a skeleton for the model is made out of metal wire. The craftsman makes each of these components like the legs, body, hands etc on the metal wire skeleton structure with their detailing. The head process of the human figure is made separately and added to rest of the body part of the model or the metal skeleton would have the head being made and attached beforehand. The level of intricacy depends on the experience of the crafts man. In case, a particular model has to be made in large number then they make mould. Every time the model is made, the wire frame is sandwiched between the positive and negative of the mould and thus a large number of pieces could be made easily. Finally, when the model is made, a final touch and detailing is given to it by the craftsman using different hand tools. Fine brushes are used to clean the surface of the model and with wet brush the surface of the model is smoothened.
2. Firing
Once the model is made, it is dried under sun only to the extent that the model does not get cracks on its surface. After drying the model is fired. The total firing process depends on the experience and may vary from place to place and craftsman to craftsman. Moreover, the temperature required and the duration of firing is decided by the craftsman. The process for firing includes- drying, loading, firing, cooling, unloading, cleaning.
3. Colouring
After firing, the models go through the process of colouring which is another important part of this craft. Though the models are intricate but by the skill of selecting and applying colours is the one that makes the models look realistic and lively. Previously, in this craft powder colours were used by the craftsmen. However, in the present day, poster colours, water colours, different dyes and pigments are also used. Powder colour is mixed with water and adhesives for colouring the models. Adhesive sometimes are locally made by the craftsmen from tamarind seed. These seeds are fried and then after cooling they are soaked in water to peel off the skin of the seed. The seeds are then ground and boiled in water thereby forming a sticky viscous material having good adhesive property. At times readily available adhesives like fevicols are also used. To make the colour have a shiny appearance, cornflour is added. At last after applying the desired colour to the models, an additional coating of varnish mixed with kerosene are applied to give the clay dolls a glimmering effect. The coloured models are then kept for drying under sun or under a fan. Colours normally used in the doll making are red, blue, green, yellow and clay colour. Besides this the crafts man also use oil paints, plastic colours and metallic colours as per the requirement. For painting fruits they mix oil based colours with paraffin to get the gloss.
4. Final Product
The clay dolls after getting coloured are given clothing. After this, these dolls find their place in a showroom nearby its place of creation, where the onlookers and the customers can see them and buy them. The final product need not be a single piece of clay doll and may be a group of them and together they might represent a scene or particular emotions for example, tribal men dancing with their dolls.
Krishnanagar clay dolls are unique in their realism and the quality of their finish, as they truly represent a breakaway from the traditional form. Fruits, fish, insects, animals, birds, and of course the entire pantheon of gods and goddesses, and even the ubiquitous Donald Duck and other popular comic strip characters, faithful copies of real-life, down to the minutest detail. Realistic recreations of everyday life, work, mood and character- farmers, weavers, rag pickers, basket makers, umbrella makers – are yet other specialties of Krishnanagar dolls. Exhibitions of Krishnanagar dolls have been held in London, Paris and Boston. Ghurni clay models have won medals and certificates at international exhibitions.
Clay as a material is difficult to control at all stages and the potter has to be constantly diligent from beginning to end, in order to avoid damage or breakage.
Krishnanagar municipality was established in 1864 and is one of the oldest municipalities. It is claimed to be named after Krishna Chandra Ray (1728–1782). Previously, the city was called ‘Reui.’
West Bengal was formerly known as, ‘Vanga’ and was spread over a vast area. Ruled by several dynasties from ancient times, the actual history of this region is mainly available from the Gupta period. West Bengal, the gateway to eastern India is shrouded in history that dates back to antiquity. There are historic references to the state that are found in the Vedic annals as well as the chronicles of the Murayan, Gupta and Mughal eras and the musty archives of the Pala and Sena dynasties.
The first traces of West Bengal’s history are recorded to belong to the Vedic era when the state was inhabited by myriads of people of varying origin and ethnicity. The state was ruled by several chieftains during the epic Mahabharata period and was inhabited by the Aryans in the post-Vedic period that soon followed. West Bengal witnessed the flourishing prosperity of the Mauryan Empire as well as the efflorescence of the Gupta Golden Age. Among the various dynasties that established control over West Bengal, the Palas, Pundras acceptance..
The voluminous evidence of history cites references to the glorious Pala rule that spanned nearly 400 years. 3rd century the Mauryan and the Guptas established their rule. The Palas established their strong rule from about 800AD till the 11th century after which the Senas ruled. The economy, arts and culture of this region developed under the rule of the Hindu dynasties. In the beginning of the 13th century Bengal became a part of the Delhi Sultanate and later the Mughals. The influence of the Muslims led to conversions besides development of art and culture and cottage industries that produced items such as Muslin which were in great demand around the world. The proximity to the sea also resulted in the influence with the foreigners -- the Portuguese in the early 16th century, the Dutch in about 1632, the French influence between 1673-1676, the Danish in 1676 and British in 1690. The increased influence of the British resulted Hazar Duari ,Murshidabad ,West Bengal in conflicts with the Nawab. The diplomatic efforts with a series of conspiracies resulted in the ultimate capture of power in Bengal by the British. The battle of Plassey (1757) and the battle of Buxar (1764) sealed the fate of the Mughal rule. The British later brought forth the Dual system of administration. In 1905 the English partitioned Bengal on the basis of religion. Calcutta remained the Capital of the British Empire in India till 1911. After that the capital was shifted from Calcutta to Delhi. In 1947 when India became independent Bengal was partitioned between India and Pakistan. India’s share came to be known as West Bengal and Pakistan’s share was called East Pakistan. Later, the state of Cooch Behar, French enclave of Chandranagore and some parts of Bihar were added to West Bengal. Bengal represents the land that possess a distinct culture with its indigenous art and crafts and make it an important part of the Indian Union.
Krishnanagar is located at 23°24N 88°30E, 23.4°N 88.5°E with an average elevation of 14 metres. It is situated beside the Jalangi River and is the headquarters of Nadia district. he Tropic of Cancer passes through the outskirts of Krishnanagar and the area of the municipality is around 16 square kilometres.
The climatic conditions in the town are largely moderate and it is possible to visit the place throughout the year.
Summers are not extreme and light cotton clothing is required if you are travelling during this period. Monsoons are relatively long and most amount of annual rainfall is restricted to this phase. However it is possible to travel during this season as well. Winters are cool and pleasant and many tourists can be found here during this period. The summer season is during the months from March to May. Temperatures can be expected to rise to a high of around 34 degrees Celsius during this period. The lowest expected summer temperature is around 19 degrees Celsius. The monsoon season starts in June and extends till the end of September. The month of July receives the most amount of rainfall and August does not receive much precipitation. The post monsoon months of October and November are pleasant and some amount of rain is to be expected in October as well. The winter season starts in the months of December and ends in the month of February. The lowest winter temperature is around 11 degrees Celsius. The mercury can be expected to climb to a high of around 21 degrees Celsius.
The town is well connected by road to different parts of the state, and also has a railway junction. Main site of clay doll making craft is in Ghurni, Krishnanagar. It can be reached from Kolkata by either train (100 km) or bus (118 km) Krishnanagar City is part of Kolkata Suburban Railway on the Sealdah – Naihati – Ranaghat –Krishnanagar line. Journey time is 2½ hours and one can return the same day. Cycle rickshaws are available for travel within the city.
Krishnanagar lies on NH 34 and is connected with Nabadwip through Krishnagar Route no 8. There are private buses like Kaseshowri, Ma Laxmi, Bubu, Tarama, Camelian, Sharica, Ma Manasha, Biswarup, Nandini, Buraraj, Shartaci, Ma Durga in this route. Krishnanagar is also connected with the Karimpur as wel as Palashi para, Majdia through roadways. One could also take auto from Krishnanagar to reach Nabadwip Ghat.
A narrow gauge rail line passes through Krishnanagar but recently it was stopped by the Indian railways for conversion its conversion to broad gauge. This narrow gauge line connects two cities Santipur and Nabadwip. Krishnanagar is also a Junction on Broad Gauge line on Kolkata-Sealdah line of Eastern Railway.
In terms of healthcare facilities, there are several government hospitals as well as private run hospitals. The residents of this are receive regular water and electricity supply. Moreover, there region also has several schools and colleges, both private and public run. Other basic sanitation facilities and drainage systems are also in place.
Due to the rich historical past of Krishnanagar, one can find several architectural wonders in this town which contribute not only to the aesthetics and beauty of Krishnanagar but also to its tourism. Some of these are-
• Rajbari
It is famous for hosting the “Jhulan Mela” in the months of July and August and also for “Baro Dol” that is celebrated at a length of 12 days from Dol Purnima with great pomp and pride in the months of March and April. It also possesses a shrine for the ‘Goddess Durga’ in the midst of its courtyard.
• Roman Catholic Church
It is known for its marvellous sculptures and architectural grandeur. It holds possession of some illustrations of Jesus Christ’s life on canvas and other wooden masterpieces made by skilled artists from Italy.
The Bengali language boasts a rich literary heritage, shared with neighbouring Bangladesh. West Bengal has a long tradition in folk literature, evidenced by the Charyapada, Mangalkavya, Shreekrishna Kirtana, Thakurmar Jhuli, and stories related to Gopal Bhar. In the nineteenth and twentieth century, Bengali literature was modernized in the works of authors such as Bankim Chandra Chattopadhyay, Michael Madhusudan Dutt, Rabindranath Tagore, and Sharat Chandra Chattopadhyay.
The Baul tradition is a unique heritage of Bengali folk music, which has also been influenced by regional music traditions. Other folk music forms include Gombhira and Bhawaiya. Folk music in West Bengal is often accompanied by the ektara, a one-stringed instrument. West Bengal also has an heritage in North Indian classical music. “Rabindrasangeet”, songs composed and set into tune by Rabindranath Tagore and “Nazrul geeti” (by Kazi Nazrul Islam) are popular. Also prominent are other musical forms like Dwijendralal , Atulprasad and Rajanikanta’s songs, and “adhunik” or modern music from films and other composers.
Bengali dance forms draw from folk traditions, especially those of the tribal groups, as well as the broader Indian dance traditions. Chau dance of Purulia is a rare form of mask dance. State is known for Bengali folk music such as baul and kirtans and gajan, and modern songs including Bengali adhunik songs. From the early 1990s, there has been an emergence of new genres of music, including the emergence of what has been called Bengali Jeebonmukhi Gaan (a modern genre based on realism) by artists like Anjan Dutta, Kabir Suman, Nachiketa and folk/alternative/rock bands like Moheener Ghoraguli, Chandrabindoo, Bhoomi,Cactus and Fossils.
Rice and fish are traditional favourite foods over here, leading to a saying in Bengali, machhe bhate bangali, that translates as “fish and rice make a Bengali.” Bengal’s vast repertoire of fish-based dishes includes hilsa preparations, a favorite among Bengalis. There are numerous ways of cooking fish depending on the texture, size, fat content and the bones. Sweets occupy an important place in the diet of Bengalis and at their social ceremonies. It is an ancient custom among both Hindu and Muslim Bengalis to distribute sweets during festivities. The confectionery industry has flourished because of its close association with social and religious ceremonies. Competition and changing tastes have helped to create many new sweets. Bengalis make distinctive sweetmeats from milk products, including Rôshogolla, Chômchôm, Kalojam and several kinds of sondesh. Pitha and patishapta are specialties of winter season. Sweets like coconutnaru, til-naru, moa, payesh, etc. are prepared during the festival of Lakshmi puja. Popular street food includes Aloor Chop, Beguni, Kati roll, and phuchka. The variety of fruits and vegetables that Bengal has to offer is incredible. A host of gourds, roots and tubers, leafy greens, succulent stalks, lemons and limes, green and purple eggplants, red onions, plantain, broad beans, okra, banana tree stems and flowers, green jackfruit and red pumpkins are to be found in the markets or anaj bazaar as popularly called. Panta bhat (rice soaked overnight in water)with onion & green chili is a traditional dish consumed in rural areas. Common spices found in a Bengali kitchen are cumin, ajmoda(radhuni), bay leaf, mustard, ginger, green chillies, turmeric, etc. People of erstwhile East Bengal use a lot of ajmoda, coriander leaves, tamarind, coconut and mustard in their cooking; while those aboriginally from West Bengal use a lot of sugar, garam masala and red chilli powder. Vegetarian dishes are mostly without onion and garlic.
Durga Puja in October is the most popular festival in the West Bengal. Poila Baishakh (the Bengali New Year), Rathayatra, Dolyatraor Basanta-Utsab, Nobanno, Poush Parbon (festival of Poush), Kali Puja, SaraswatiPuja, LaxmiPuja, Christmas, Eid ul-Fitr, Eid ul-Adhaand Muhharam are other major festivals. Buddha Purnima, which marks the birth of Gautama Buddha, is one of the most important Hindu/Buddhist festivals while Christmas, called Bôŗodin (Great day) in Bengali is celebrated by the minority Christian population. Poush mela is a popular festival of Shantiniketan, taking place in winter.
The Bengali women commonly wear the shaŗi, often distinctly designed according to local cultural customs. In urban areas, many women and men wear Western attire. Among men, western dressing has greater acceptance. Men also wear traditional costumes such as the panjabi with dhuti on cultural occasions.
As of the 2011 Census, Krishnanagar city had a population of 181,182The urban agglomeration had a sex ratio of 978 females per 1,000 males. The effective literacy rate was 88.09%, of which male and female literacy was 90.84% and 85.29%, respectively.
The people of West Bengal are immersed in the rich history and tradition of their state. Everything here from the food to the clothing is an expression of the people and their uniqueness. The heart and soul of the people here is immersed in cultural plurality, vibrancy and love for their traditional values. The people here carry with themselves a certain dignity and pride for their breathtakingly beautiful culture and magnificence of their handicrafts.
The Bengali women commonly wear the shaŗi, often distinctly designed according to local cultural customs. In urban areas, many women and men wear Western attire. Among men, western dressing has greater acceptance. Men also wear traditional costumes such as the panjabi with dhuti on cultural occasions.
Since handicrafts form a significant part of the people’s lives here, one can find different communities of people working on different handicrafts. Some of these are-
• Chitrakaras / Patuas – Painters
• Kumbhakars – Potters / Clay modellers
• The Sutradharas – The Architects
• The Metal Group- the Karmakaras (Iron Smith), the Swarnakaras (Gold Smith) c)The and the kangsakara (Makers of Kngsas)
• The Minor Arts. This includes -a) The Malakars – Garland Makers b)The Sankhakaras – Makers of Shell Bangles c)The Tantubayas – Weavers
For the Krishnanagar Clay Dolls in particular, making the dolls is distributed among the family members of the craftspeople. Clay collection and other heavy works are done by the men whereas the women in the family are involved in clay grinding and sieving. Model making, moulding, firing, and colouring are all done by both men and women. The children in the family are also involved in doing all sorts of work, however, they do not specialize in doing any specific sort of work, that is, they are not involved in any intricate detailing work of the clay models. The entire family is involved in the firing which may take place at any time in the day.
Apart from the clay dolls, West Bengal is also famous for its pottery, metal casting, mat making, sholapith, muslin, jute, cane and bamboo products and katha embroidery.
List of craftsmen.
Sujay Das & Swarup
•https://www.indianetzone.com/37/clay_art_india.htm
•http://www.bharatonline.com/west-bengal/arts-and-crafts/clay-dolls.html