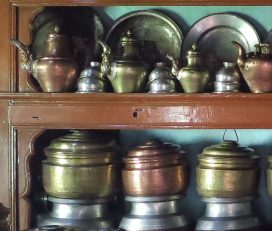
Copper Craft ~ Chili...
Copper and brass have played a significant role in fulfilling these needs. Even today, in most traditional Ladakhi kitchens such utensils are commonly seen
Chiling Sumda...
Waraseoni sarees are known for their simplistic beauty and grace, much like the town, that holds a long history of handloom sarees in it. The weavers community or the Koshtis are said to have derived their name from ‘Kosa’ (Tussar silk); and Salewar is said to be from the Sanskrit SÄlika, a weave.
The sarees earlier used to be only made of cotton woven into heavy, flannel-like fabric. The weavers have now moved to silk and silk-cotton too and weaving elegant aesthetics out of the yarns.
The woven cloth is used to make sarees, stoles, salwar suits, accessories and home furnishings. In recent times, the weavers also weave Chanderi and Maheshwari fabric to support the clusters in meeting their high demands.
The Maratha and Telugu caste dominates weavers of silk and fine cotton cloth. They belong principally to the Nagpur and west Madhya Pradesh divisions of the central provinces.
The fabric from Waraseoni is sometimes also known as Wainganga cotton because river beside Waraseoni is called Wainganga. It is the largest sub-basin of Godavari river. The area is known for its weaving in very fine counts – 80s to 120s. Amongst the merchants, the sarees are known as ‘Solah haath ki saadi’ or saree measuring 16 hands, also called Lugda.
The sericulture and weaving is highly aided by the government. The sericulture holds great importance in forestry as a supplementary activity. It helps in arresting forest destruction. Tussar culture also provides great economical value due to its minimum investment requirement and high employment potential for both tribal and rural population. Traditionally the spinning and subsidiary activities are carried out by women and the weaving is done by the men.
The Handloom Census of India, undertaken in 1987-88, places the number of handloom textile workers at 65.3 lakh persons. This makes them the single largest group of artisans in India. The handloom production is the largest economic activity second only to agriculture in India, which provides direct and indirect employment to more than 30 lakh weavers. The Handloom Act passed by the parliament in 1985 aims to shield handloom weavers against power loom and textile mill operators by reserving certain textile articles (presently eleven in number) for exclusive production by handlooms.
The caste suppose themselves to be descended from the famous Saint Markandi Rishi, who, they say, first wove cloth from the fibers of the lotus flower to clothe the nakedness of the gods. In reward for this he was married to the daughter of Surya, the sun, and received with her as dowry a giant named Bhavani and a tiger. But the giant was disobedient and so Markandi killed him, and from his bones fashioned the first weaver’s loom. The tiger remained obedient to MÄrkandi, and the Koshtis think that he still respects them as his descendants; so that if a Koshti should meet a tiger in the forest and say the name of MÄrkandi, the tiger will pass by without harming him; and they say that no Koshti has ever been killed by a tiger. On the other hand they will not kill or injure a tiger. Even at their weddings the BhÄt or genealogist brings a picture of a tiger attached to his sacred scroll, known as Padgia and the Koshtis worship the picture.
The craft of handloom weaving has survived for years due to its adaptability to meet the changing needs of the community. The Indian saree is fascinatingly more than five thousand years old. It is mentioned in the Rig Veda dating around 3000 BC. The Rig Veda is the oldest surviving piece of literature in the world. The Indus Valley civilization spun cotton since at least 3000 BCE, as indicated by the ruins of Mohenjo-daro. The saree, originally worn by both men and women, was called ‘Chira’ in Sanskrit, meaning cloth. This rectangular piece of cloth was usually 5-9 yards in length.
The East India Company imported raw cotton from India while they dumped the local Indian market with inferior machine-made cloth. This led to a great decline in the handloom industry. The Khadi weavers were first affected with the subsequent establishment of the power looms in India. Imitations of the hand-woven saris and garments were dished out, making it much cheaper and severely affecting the rural scenario. During the Second World War (1939-1945), majority of the Indians turned to hand woven saris. This was further supported by the Swadeshi Movement initiated by Gandhiji, where women turned to hand woven Khadi fabric in order to shun the English machine made fabric. The effect of the mill spun fabric continued to affect the handloom sector even post-independence. The extent was so large that the Government of India had to ban power looms producing certain textiles, one such being the sari. The Government took active interest in reviving traditional saris to prevent it from extinction and provide handloom weavers with a livelihood through the Janata Scheme. The Janata scheme involved a per saree wage to the weaver and was production centric rather than quality being a concern. The idea was to make the sari as economical and production as high as possible. More number of saris implied more wages for the weaver. This however did not last long. More recently, various state-run schemes are aiding the weavers.
The weaving in Waraseoni in the Balaghat district is known to be happening for over 250 years. Raja Raghuji Bhonsle had taken over the Balaghat region during 1900 AD and the craft flourished under his patronage. Earlier the weavers used to make thin dhotis and Lugda and used to sell it in the open markets. The weavers used to use 10s to 100s counts of cotton for weaving. From around 1920, they started weaving in only 10s and 20s. Heavy Maharashtrian influences are seen due to its proximity to the state. Initially, only cotton was woven extensively. As the demand and sale for the cotton fabrics reduced, the weavers started working on silk. From 700 looms, it has diminished to 70-80 looms, which also weave Chanderi and Maheshwari fabric. Silk weaving in Waraseoni was an initiative of the Madhya Pradesh government to aid the dwindling population of weavers. Identified after 1999, this small scale industry is operational under the Madhya Pradesh Hastshilp Vikas Nigam (MPHSVN). Most weavers have shifted to silk from cotton, as that ensures more wages for their efforts.
Design work on the bases of hand measurements –
Ekungal – one finger, Do ungal – two fingers, Teen ungal – three fingers,
Char ungal – four fingers, Paanchungal – five fingers, Ekbhitha – one hand span
‘Ekbhithakinar’, which forms a complete veil over the head.
D – Ekhaath – one arm length from elbow to fingertips.
Colours – There are a variety of body colors – deep maroon, haldi yellow, blue-black. The colors used in these sarees are named interestingly -“ Purple is Baingani (Baingan – Brinjal), Pink is Gulabi (Gulab – Rose), Red-Brown is Eent (brick), Pyaazi for lavender (Pyaaz – Onion) etc. Others are Firozi, Mehndi, Chutney, Aasmaani etc.
Border – It always has a red ground and is called Nakshikinar (flowering wine border).
Selari pattern – The saree is referred to as Selari if the body is striped.
Bhaga – If it has variegated stripes, then it is called Bhaga.
Moongia pattern – A saree with a 4’X 4’ check.
Mukhtiya pattern – Sarees with 2’ X 2’ checks, made using a two shuttle technique.
Dhoop-chaon- When the saree has two shades – a lighter and darker one.
Warp border motifs – Ruiphool, Jai phool, Karvati or double Karvati (saw-faced motifs), Shahpuri or Gom (arrow-head pattern).
There are various traditional sarees which characteristically incorporate these motifs and patterns in different ways.
Reshmijote saree – This type of saree has a cotton body of 18s to 24s counts. The borders are made of heavy two ply Malda silk from Bengal, completely hiding the cotton weft.
Baal saree – This type of saree either has a silk warp and cotton weft body with a 7’ silk Dhodhadirui phool or double flower pattern, or it had a dark blue-black cotton body with yellow Mukthiya check in silk with red silk border. Also called a Kothi (checked) sari.
Anjari or Aanjanasaree – These sarees are made of pure silk and are used mainly for marriages. They are also called the Bhanwarai saree. It had ‘Mukthiya‘ checks in red or ‘Cheechpopdi‘ check (named after a large lentil seed which it is said to resemble) in deep blue and yellow. A broad red border is a characteristic. Pure black color in the body is avoided as it is considered inauspicious.
Pitambari Aanjana – This has a yellow body and a red border. The border is adorned with the ‘Gom’ motif. It often has Zari in the end-piece and borders. This saree is traditionally worn by the women of wealthier communities like the Baniyas and the Lodhis.
Handloom weaving is under the constant threat of power looms and mill made fabric. The designs are also slowly getting redundant and are in need of new inspirations and contemporary modifications to suit the present needs. The market links are weak and the cluster has no stark brand name for their products and hence it is very difficult to place them. Chanderi and Maheshwari still remain well known but Waraseoni weaving has not caught up yet.
Most weavers are of the older generation and the craft seems to be dyeing down with them. The younger generation has moved onto faster paying jobs in the neighboring towns.
The silk threads are extracted from the cocoons and this process is called Reeling. Charka and the reeling machine are used for this purpose. The silk obtained out of the reeling process is referred to as ‘Raw Silk’. The reeled yarn is taken out to an open area and wound onto the warp beam. Specific warp yarns are raised in the process called Shedding. The weft yarns are picked and passed through the shed using a shuttle.
Silk – 22 denier mulberry silk from NSDC (National Silk Development Corporation),
80 percent pre-dyed Tussar silk yarn (produced naturally in forest areas with trees like Arjun, Saja and Sal).
Zari – from Chanderi or Surat.
Cotton – from south India.
Dyes – From Nagpur
Traditional pit loom – The loom was placed over a pit dug into the ground, so the weaver could sit on the edge of the pit which contains the pedals. The warp from the log is wound over another log. The threads are guided through metallic reeds till it reaches the ‘Hattha’ or frame which is used to beat in the weft threads. Screws on the loom beams are used to adjust the tension of the warp. One Dhurrie is normally made in a few hours.
Charkha – use to prepare bobbin.
Bobbin – from Nagpur
Reed – A reed is part of a loom and resembles a comb. It is used to push the weft yarn securely into place as it is woven, separates the threads and keeps them in their positions, keeping them untangled and guides the shuttle as it moves across the loom. It is bought from Nagpur.
Before beginning work for the day the weaver makes obeisance to his looms and implements, he may not touch them without having washed his face and hands, this is his way of paying respect to his workspace and equipments. Some superstitions also surround their practice; A woman must not approach the loom during her periodical impurity, and if anybody sneezes as work is about to be begun, they wait a little time to let the ill luck pass off. They believe that the posts to which the ends of the loom are fastened have magical powers, and if any one touches them with his leg he will get ulcers up to the knee.
Among some classes of Koshtis the killing of a cat is a very serious offence, almost equivalent to killing a cow. Even if a man touches a dead cat he has to give two feasts and be fully purified. The sanctity of the cat among Hindus is sometimes explained on the ground that it kills rats, which attract snakes into the house. But the real reason is probably that primitive people regard all domestic animals as sacred. The Koshti also reveres the dog and jackal.
Silk production : Silkworms are the larvae of the silkmoth. Tussar silk is produced from a species called Antheraeamylitta. Their wings are cut and the males and females are put in an earthen pot called Matka, to mate. They produce around 150 eggs. These are then sent for testing. The good ones are given to the farmers who, once they hatch, leave them onto the trees of Arjan or Saja. They change the tree onto which they are put, every 28 days. Three harvests are done in a year.
The cocoons on the tree are watched over all night by the farmers. The cocoons are made into garlands and stored during the monsoons. Once the mating is done, the male is separated from the female worm and can be used to for another 3-4 batches.
The silk threads are then extracted from the cocoons and this process is called Reeling. Charka and the reeling machine are used for this purpose. The silk obtained out of the reeling process is referred to as ‘Raw Silk’. It is the silk reeled by drawing together the filaments from a number of cocoons (6-12) based on the thickness required for weaving sector. In the case of Matka silk, the discarded short fibers are handspun. Coarse silk fibers are obtained after they are twisted on the base of an inverted pot.
Preparing the loom: The yarn is bought from the government organization like MPHSVN at the ITI Centre in Waraseoni. The reeled yarn is taken out to an open area and wound onto the warp beam. Care is taken to keep the threads at regular intervals so as to not get them tangled. Sticks are also inserted at regular intervals to keep the tension and also have the threads spread evenly. These warp threads are then taken through the heddles and the reed. The craftsmen dust ash onto their hands to help pick the threads better. The weft threads are then wound around the bobbins using the charkha.
Weaving: The weaving is done on a traditional pit loom. Specific warp yarns are raised in the process called Shedding. The weft yarns are picked and passed through the shed using a shuttle. The picking movement propels the shuttle by pulling the handle to let the shuttle move across to the other side. In the process of beating, the weft is pulled and tightened. Different textures of hand woven cloths are produced by varying the count of the warp and weft threads, the order in which the warp threads are lifted, and varying density or tension of the yarn. The finished cloth is taken and rolled onto the beam and steps taken to release the tension. In a day, 3 meters of silk is woven and 5-6 meters of Chanderi or cotton can be woven.
Finishing : The fabric, if dyeing is needed, is sent to the skilled dyers. Designs are made according to the requirements. In some cases, Butis or motifs are inlayed in the body or the Pallu of the saree or fabric. The women also embroider intricate and colorful patterns onto fabric. Sometimes patterns are block printed onto fabric and for this; the fabric is sent to Champa. It is then roller pressed and given back to the government organization which then markets it.
No waste
Waraseoni is a place where all the religions live together. The history has many stories of the region being ruled by the Pawar Kings. As a result, the Pawars form major part of the clan today.
Waraseoni was established around 220 years ago by Vilayat Khan of Newargaon, who wanted to establish a market in his 'Zamindari' (reign). Waraseoni was earlier a hamlet named 'Wara' and this is where the name stemmed out of. It was made the tehsil headquarter in 1931-41. It was also re-formed later by adding a few more towns to it.
Waraseoni is located 17 km from the district headquarters of Balaghat. The other nearby villages of the district are Hatta, Beni and Mehndiwada. Waraseoni is situated at 21.75° North latitude, 80.03° East longitude and 282 meters elevation above the sea level.
In the east lies Mandla district, in the west is Bhandara district, the Seoni district in the north and Rajnandgaon to the south.
By Road : Waraseoni is flanked by state highways and equipped with buses which connect it to neighboring towns as well as cities like Gondia, Jabalpur, Raipur etc. It lies 435 kms away from Bhopal, the state capital.
By Rail : It is situated on Narrow gauge line of Jabalpur-Balaghat and Broad gauge line of Balaghat-Gondia section of South-Eastern Railway.
By Air : The nearest Airport is at Nagpur, around 150 kms away.
The land has varied elevations, thus creating various natural scenic spots like the valleys and cascading streams in the Wainganga valley. The soil is suited for agriculture and is known to be very fertile due to dense forest cover. Teak, Sal, Saja, Bamboo, Neem and Mahua are commonly found trees.
Waraseoni has a moderate climate. The monsoons span mid-June to September with an average rainfall of 1310 mm (mostly in July-August). Winter spans from November to February and summers from March to June with temperatures from 10 degrees Celsius in winters to 40 degrees Celsius in summers.
The chief industries are silk production, weaving, dyeing, livestock trading, glass bangle making, brass utensils and agriculture-based industries like rice mills. Dams constructed near the Sonawani hills and the canals from the Wainganga provide water for domestic use and irrigation. There are private and government schools up till higher secondary classes. There is a polytechnic college and a civil hospital. There is a special hospital for 'Bidi' workers as they are exposed to conditions that make them prone to cancer.
Bus stand is located in heart of the city, daily around 100 buses pass through Waraseoni.
Waraseoni has all the basic facilities like Bank, ATM, hospital, collage, Good roads, Shops and hotels.
The skyline of Waraseoni is very rustic, laden with hills, thatched roofs and occasional tile factory chimneys. There are temples by the riverside. The houses are modest single storied houses which are kept spick and span, very much like the town itself. The floors are swept and cleaned with cow dung smears. The verandah is the space for work related activities. Teak wood is used for loadbearing frames, bamboo for rafters and purlins and clay tiles for the roofs. The walls are made of daub construction - mud plaster walls with lime wash, and painted white or blue.
Hindi is the primary language of the town. Ganesh Chathurthi, Diwali and Shivratri are celebrated with much aplomb. Celebrations happen with 'Melas' or fairs by the river, Polle or bullock race etc.
The principal deity of the Koshtis (weaver community) is GajÄn and or Ganpati, whom they revere on the festival of Ganesh Chathurthi or the fourth day of the month of BhÄdon (August). They clean all their weaving implements and worship them and make an image of Ganpati in cow dung, to which they make offerings of flowers, rice and turmeric. On this day, they do not work and fast till evening, when the image of Ganpati is thrown into a tank and they return home and eat delicacies. Some of them observe the 'TÄ«j' or third day of every month as a fast for Ganpati, and when the moon of the fourth day rises they eat cakes of dough roasted on cow dung fire and mixed with butter and sugar, and offer these to Ganpati.
Wheat roti and rice is a staple diet, boosted by the agriculture in the town. Their lifestyle is very organized and work oriented. Radios keep playing while they work away from 8 am to 6pm. Kabir is a popular figure in the people's beliefs. They deeply revere the Wainganga River.
The occupations include weaving, pottery, Bidi making, leatherwork, tile- manufacture and bamboo work. An interesting fact is that almost all the houses have a parrot kept as a pet.
Dhoti and Kurta is a favorite daily dress for old men, while women like Saare. Old women wear 'Nauvari saree' and cheeks are marked with a small dot and the arms adorned with a representation of the sacred 'Tulsi' or 'Basil'.
The people of Waraseoni are mostly Hindus primarily comprising of Koshtis and then Halbas, Marathas, Baniyas and Lodhis. There is a prominent Jain population also. There exists a colony of sorts called the Hyderabadi Mohalla where the Muslims used to be concentrated. The tribal population includes the Gond and Baiga tribes.
The women wear cotton sarees, draped according to the community they belong to. The men wear dhotis and kurtas, and a turban while they wander out. Youngsters have resorted to contemporary wear like the Salwar-Khameez, pants, shirts and t-shirts. A noticeably content bunch of people, they lead a very simple lifestyle. They are known to be very hospitable.
Jain temple on the banks of Bainganga, Handicrafts and small scale industry like silk weaving, sculpting and clay tiles. A very sweet dish prepared from pumpkin called the 'Buliya' is the delicacy of this place.
List of craftsmen.
Team Gaatha