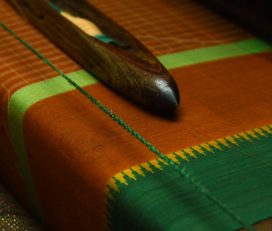
Saree Weaving ~ Nara...
Narayanpet sarees, handwoven in the small, vibrant town of Narayanpet in Telangana, are not confined to ceremonial grandeur or museum-worthy curation.
Narayanpet, Telangana, India...
Kachchh had a robust tradition of animal husbandry. The pastoral communities maintained large herds of camels and livestock like goats and sheep. The Maldharis and Rabaris (pastoral communities) shear the hair from camels, Sheep and goats. This was then given to the hand-spinners who specialized in making wool out of goat and camel hair. This wool was then used by the Kharad artisans for weaving.
Kharad, the Sindhi term for carpet, is synonymous with exquisite handwoven carpets and rugs, also known as Kharad Dhurries used to warmth on floors and for special gatherings of people and meetings. People would bring their carpets for an occasion to sit comfortably as well as show respect. The art of weaving Kharad is an age-old craft meticulously practiced by the nomadic communities of Kutch, bringing to life the vibrant colours, rich traditions, and unique way of life of this community.
The primary purpose of this craft is to cover the floor, envisioning a scenario where a nomadic community is traversing a grassland and requires a quick, clean surface – these durries play a vital role. The use of natural fibers adds strength and durability to these carpets. The Kharad artisans produced Kharad (used for spreading on the floor), Khurjani (used to keep on the back of a camel to carry heavy items), Rasa (thick cloth used to cover grains) as their basic requirements while moving from one place to another. Originally Kharad carpets were made from goat and camel hair wool.
However, in contemporary urban settings, this craft has seamlessly integrated itself; people now purchase these durries to cover their floors or even adorn their walls as impressive wall décor. Artisans are also diversifying their products to meet various market demands, creating items such as Aasan for puja, bags, and more.
Kharad, with its intricate warp and weft, embodies an ancestral technique. This method utilizes local sheep wool, woven on traditional looms, resulting in products that exude both strength and beauty. As these nomadic communities traversed in search of fodder, they crafted functional items that demanded minimal equipment yet were capable of producing intricate patterns with endless variations. Visually, the significance of this craft lies in its beautiful, unique motifs and color combinations. Over the years, artisans have masterfully transferred the camel belt braiding technique onto the loom.
The period between 2500 BC-2000 BC witnessed the urban phase of the Harappa culture, with Harappan trade reaching its zenith during this time. Various archaeological evidences and documents from Mesopotamia shed light on the flourishing Harappan trade with the west. Ports like Lothal, Mundra, and Khamnat were crucial hubs of exchange, housing warehouses where finished craft goods were gathered, stored, and transported.
In addition to sea routes, land routes served as reliable mediums for transporting goods. Merchants loaded heavy items onto the “Khurjani” and traversed diverse terrains. Due to its robust nature, “Khurjani” found popularity in Sindh, where locals, owning camels, readily purchased these items. In the past, Kharad artisans shared a close relationship with camels, crafting not only products like “Khurjani” but also beautiful camel belts using braiding techniques, serving as useful tools to secure goods on camels.
Even after thousands of years, this cottage industry in India continues to thrive. A significant number of skilled individuals explore their creative freedom, earning a livelihood in their local villages. UNESCO defines creative industries as sectors involved in the production, promotion, distribution, and commercialization of goods, services, and activities related to culture, art, or heritage. Traditional crafts, including Kharad weaving, play a crucial role in these creative industries, connecting with traditional livelihoods and practices. These crafts not only promote creativity and culture but also contribute to livelihood generation. Worldwide, shepherding remains a traditional livelihood, with sheep wool and its crafts being major products of this activity, serving as essential raw materials for making clothing and fabrics for utilitarian purposes.
In the ancient chronicles, a tale unfolds of the revered sage Dhoramnath, who embarked on a profound meditation atop the majestic Dhinodar mountain in Kachchh, balancing the cosmos on his head for an arduous 12 years. The divine deities, moved by his dedication, bestowed upon him a unique gift – the power to scorch and transform everything within his gaze when he opened his eyes post-meditation. Aware of the potential havoc, Dhoramnath, before unveiling his vision, instructed his loyal disciple to position his head in a direction that would inflict minimal harm upon living beings. Following the sage’s guidance, the disciple turned Dhoramnath’s head northward, facing the shallow sea and the Rann (salt desert). As Dhoramnath opened his eyes, a blaze erupted, consuming the shallow sea and the Rann, unveiling a fertile land where lush grasses sprouted. The news of this newfound grassland, named Banni, spread far and wide, beckoning pastoralists from distant lands like Baluch and Haleb in Afghanistan. They sought the abundant grassland, christening it Banni, derived from the Kachchhi word “Bannai,” meaning ‘that which was created.’ Thus, the saying “rann se banni hui” resonates through time, signifying the creation of Banni from the salt desert’s embrace.
The exact history of a nomadic lifestyle is difficult to trace. The large Harappan settlement at Dholavira (4000 to 4500 years ago) provided an ample opportunity to look for several potential sites around it that might have provided feeding support to this settlement on the island. These could be in the form of the food economy, raw material resources for construction, and, in turn, their utility in developing industries. For generations, Kachchh has been home to people from various regions, such as Sindh, Rajasthan, Afghanistan, Baluchistan, and Iran, who have brought their unique skills in art, craft, and music. These elements have become deeply embedded in the region’s culture, playing a major role in forming Kachchh’s rich culture today. They have also helped create an economy for various communities along the region of Kachchh, with handicrafts being one significant source of income for many artisan families.
Kachchh, located in the western Indian state of Gujarat, is extremely dry and ecologically distinct from the rest of India due to extensive grassland and salt desert ecosystems that cover most of its area. It has a long history of nomadic and settled pastoralism and other livelihoods based on its unique ecological features. Traditionally, these livelihoods were also associated with religious and caste identities, although this is becoming less distinct, especially where urban and industrial economies have developed. Vankars, part of the Marwada (and in very small numbers, the Maheshwari and Gurjar) subgroups of the Meghwal community that originally came from neighboring Rajasthan, are spread over much of the district. Traditionally, they have been involved in weaving and other occupations, including farming and leatherwork.
Since humans and animals began coexisting, fur, hair, wool, and skins have been adapted and used for shelter and clothing. Gradually, different crafts developed as technology advanced. In early times, the Bhil community from the Thar Desert area used to weave in this style, but this stopped long ago due to climatic conditions, leading to many communities migrating from the Thar Desert to different locations. Kharad weavers are also a part of them. They came to Kachchh from Marwad in Rajasthan about 600 years ago, hence their name Marwada, which accords a sustained sense of identity and community. They were traditional farmers and breeders of cattle, sheep, goats, and camels, coming to Kuran village situated between the Great Rann and the Black Hills in northern Kachchh because the water was sweet, and the land was green. Nestled between the White Rann and the Black Hills of Kachchh, Kuran is the last village before India’s border with Pakistan, 40 km to the north. It is in the heart of camel country and was, at one time, a main center of Kharad weaving—a technique that traditionally uses camel wool and goat hair to create carpets of strength and beauty.
The use of indigenous wool gave birth to a resilient ecosystem in Kachchh because of its versatility. This ecosystem engaged artisans such as the spinners, weavers, dyers, felt makers, and embroiderers, along with the herders, to create a cohesive value chain that was in sync with their local ecology and environment. Mobile pastoral herders and systems have significantly influenced the ethos of craft practices in Kachchh, and artisans adapted materials and evolved their practices to suit their needs. Each community also utilized custom-made handicrafts as an identity, and its products and clothing served as a means of communicating non-verbally. At the heart of this system lay community interrelationships—threads of interdependence that tied communities and economies together.
The distinctive look of the Kharad weaves caught the eyes of royal families and received their patronage, flourishing for some time. However, it is now a dying art with local linkages and communities no longer engaging with the craft. The few that still practice the craft had to reinvent it to ensure its sustenance. One major step they took in this direction was to use dyed woollen yarns. Traditionally, Kharad weaves are usually black, brown, white, or rich ochre, but now artisans dye their wool with vegetable dye to give the finished products vibrancy and create more appeal. In the Kutch 2001 earthquake, their lives changed, and a few weeks after the massive earthquake that destroyed their home, they settled at Kukma village with the help of the government and local NGOs. Today, Kharad artisans depend on external markets both for buying the wool and selling their produce. The Kharad artisans buy wool from Rajasthan. Due to the nearby location from Bhuj, many tourists also visit their workshop, and with time, they are gradually gaining visibility. But still, artisans are not able to reach the right market segment that can appreciate the work involved and are willing to pay a premium.
The beauty of Kharad weaving lies in the exquisite natural, earthy-colored yarn and intricate patterns. The designs used in Kharad are deeply rooted in the traditions of the local community and can be observed in wall mud work, embroidery, or even in camel belts. Initially characterized by geometric patterns, carpet weaving later embraced narrative designs inspired by the desert environment, depicting village scenarios, earthquake memories, farming scenes, Kutch grasslands, rituals, animals, and more, showcasing the craft’s adaptability. These scenarios serve as a means to narrate the stories woven into each work, making the craft of special importance to the communities as it is intricately interwoven with their ancestry and way of life.
Traditionally crafted on a simple loom constructed from local materials, Kharad weaving employs a flat weave that utilizes a tapestry-like technique to create patterns worked from the back. The process is intricate and typically involves two artisans with expertise in handling the loom. Gujarat carpet weavers artistically produce knotted pile carpets without using any mechanical contrivances.
Artisans are exploring a variety of layouts, such as carpets filled with repetitive patterns, borders at the ends of the carpet, plans at the center, strips featuring different motifs, four-side borders, and figures on the main body. Both ends of the carpet are knotted in the tassel format, adding a charming touch to the carpet or rug.
Regrettably, Kachchh, situated in an active earthquake region, has endured numerous natural disasters throughout its history. The seismic event of 2001 stands out as a particularly devastating episode, resulting in significant loss of life, resources, and the destruction of many artisan workshops, tools, equipment, and local markets. The aftermath of the earthquake, coupled with shifts in market dynamics and cultural changes, has posed considerable challenges to the future of Kachchh’s traditional crafts.
Various factors contribute to these challenges. The disruption caused by the earthquake severed local linkages, leading to a decline in the demand for Kharad products within the community. Additionally, the partition resulted in artisans losing access to the once highly lucrative Sindh market. The intricate value chain involving Maldharis supplying wool to spinners, the hand-spinning of camel and goat hair into wool, and Kharad artisans utilizing this wool for production has disintegrated. Today, the hand-spinning of camel and goat hair into wool has become extinct in Kachchh.
Despite these setbacks, Kharad artisans believe that educating customers about the meticulous Kharad process, where only 3-5 pieces can be crafted in a month, and emphasizing the longevity of the carpets, especially those made from hand-spun wool lasting over 100 years, could help expand the market. They hope that such awareness will attract more artisans back to the craft, revitalizing the traditional art form and ensuring its sustainability for future generations.
Kharad weaving is a great example of a community-based craft, where herding communities like Jats and Rabari collect wool from domestic animals. They, either within their own community or with the assistance of another community, spin the yarn. Subsequently, skilled weavers from the Wegha or Vankar community weave the Kharad. These skilled artisans employ a basic horizontal loom with two pegged rods, offering portability and ease of setup in diverse locations. Kharad rugs, woven with meticulous effort, showcase bold geometric patterns inspired by the desert environment and reflect a rich cultural heritage.
The natural resources required for Kharad Craft mainly include three types of wool: camel, goat, and sheep. In the early days, the local community was responsible for supplying the materials. Over time, things have changed, and camel wool has become harder to source as camels are no longer as widely used for transport. Jat communities maintain large herds in areas with more fodder, and some Rabari communities still migrate annually with their camels as carriers for all their household possessions. Nowadays, artisans also source wool from the Barmer region of Rajasthan.
Another crucial material is dye. In the early days, dye was 100% naturally extracted from plants and trees, such as indigo plants for indigo (Indigo), pomegranate rinds for yellow, Babool bark for brown, and lac for red. Though some artisans still use natural dyes, they are mostly replaced by chemical dyes over time. An interesting fact about the colours is that there is a good demand for wool in natural colours, and they look beautiful in similar tones.
Cotton yarn is also sourced from the market. Nowadays, people also prefer cotton rugs as they are an economical option compared to woollen rugs.
The most ancient of weaving techniques requires the simplest of tools. The simplicity of the loom also makes it relatively portable and easy to erect and dismantle. This kind of loom is in use by many nomadic communities across Asia (and probably other parts of the world too).
Nomadic Self-Made Pit Loom: It’s a basic horizontal loom with two rods pegged securely to the ground on opposite sides and can be set up anywhere. The distance between two rods is determined by the size of the rug to be woven. A strong, taut warp is created on the frame, then the weaving can begin.
Mirror: Placed under the loom, a mirror is used by weavers to check the designs as they are being woven. This technique, weaving patterns from the back, requires visual verification for accuracy.
Hatho/Panja (Beating Implement): A wooden tool used for packing the weft tightly into place. This ensures a solid and even weave, contributing to the durability of the Kharad rug.
Shed Stick: A tool used in the weaving process to create a shed, which is an opening between the warp threads through which the weft is inserted.
Scissors: To cut edges and extra yarn.
As the artisan explains, weaving techniques and aesthetics came with them from Rajasthan. They had many techniques to make essential items, such as udder bags for camels, knotted tiffin bags, and camel straps with split-ply work. Sacks for carrying grain were tightly woven with goat hair as both warp and weft. They applied their knowledge to making Kharad rugs. Even today, each rug is created entirely from sheep’s wool, traditionally camel wool, and goat hair (originally hand-spun).
Kharad technically uses a tapestry-like technique to create patterns from the back. Weavers keep a mirror under the loom to check the designs as they are being woven. Fine detailing is not possible due to the coarse yarn used for weaving, and so the designs contain a bold geometric quality.
Because of the kind of effort and dexterity that go behind hand-weaving a Kharad rug, only 3-5 pieces can be woven by a weaver in a month. The technique is quite complex as it requires weaving using two sticks working as a loom.
Step 1 – Camel Wool Shearing: The initial stage involves carefully shearing wool from camels, a crucial step in acquiring the raw material for weaving.
Step 2 – Goat Wool Shearing: Similar to camel wool, the shearing of goat wool is conducted, adding another dimension to the variety of fibers used in Kharad carpet making.
Step 3 – Preparation of Yarn: The harvested wool undergoes a meticulous preparation process to convert it into yarn, ensuring it is ready for the looming and weaving stages.
Step 4 – Dyeing: Weavers use leaves, roots, bark, flowers, and fruits from their surroundings to dye the yarns used for weaving. The reds and browns are found to be most fascinating.
Step 5 – Warping – the warp is bound on the two beams of the loom. The warp has two layers, which pass through a reed (made of cotton threads) that guides the threads and maintains the distance between warp threads. In one warp, 140 to 200 threads have been stretched (depending on the size of the rugs).
Step 6 – Weaving: For weaving, alternate threads are lifted by hand to create a shed, through which the woolen weft is inserted and interlaced with the warp to create different patterns. The weft is packed tightly using a wooden beating implement called a hatho. Once the warp threads are tightly beaten between the warp, the weaver exchanges the upper and lower layers of the warp.
Step 7 – Finishing: After completion of the weaving, they take off the product from the loom and knot the loose ends of the rugs.
Trimming Waste: During the finishing stages of carpet weaving, excess yarn or fibers may need to be trimmed to achieve the desired shape and size. This trimming process generates waste materials.
Yarn Waste: Imperfections, knots, or irregularities in the yarn may lead to portions being cut or removed during the weaving process, resulting in yarn waste.
Dyeing Waste: In the dyeing phase, not all dye material may be absorbed by the wool fibers, leading to leftover dye solutions or residues, which need to be treated as waste.
Kukma or Kookma is a village near the Bhuj town, under kachchh taluka located at a distance of 16 kilometers from Bhuj. About the history of Kukma, it is one of the 19 villages established by Kutch Gurjar Kshatriya or Mistris. These Mistris first moved to the Saurashtra in the early 7th century and later a major group entered Kutch in the 12th century and established themselves at Dhaneti. Later from the 12th century onwards they settled between Anjar and Bhuj and founded the villages of Anjar, Sinugra, Khambhra, Nagalpar, Khedoi, Madhapar, Hajapar, Kukma, Galpadar, Reha, Vidi, Ratnal, Jambudi, Devaliya, Lovaria, Nagor, Chandiya, Meghpar and Kumbharia.
Most of the early infrastructure, temples, community halls, school, girls boarding house and old houses are built by this community during the late 19th century. However, majority of old houses with unique architect were destroyed in the earthquake of 26 January 2001.
The Kukma village has become a perfect example of coexistence with nature. The green revolution at Kukma as achieved thanks to the community initiative of the population of around 10,000. The gram panchayat too played the perfect role as catalyst to bring about the green change. The villagers have planted 60,000 trees in the last four years.
Kukma village is located in Bhuj taluka of Kachchh district in Gujarat, India. It is situated 11km away from Bhuj, which is both district & sub-district head quarter of Kukma village. As per 2009 stats, Kukma village is also a gram panchayat. The total geographical area of village is 1829.26 hectares.
A small village with a population of 7216 was moving towards a larger environmental crisis, given that it was already gripped by the district’s water problem. Compared to other parts of Kutch, Kukma village had groundwater tables at an acceptable depth, around 200 feet, a few years ago. As the neighbouring villagers indulged in rampant groundwater extraction, Kukma’s depth went at 600 feet. Thus, using groundwater for plants was a strict no. The idea adopted was Miyawaki method of growing trees and use recycled wastewater for its growth. The village today has a flourishing forest comprising 7,500 trees. Mandvi-based Vivekanand Research and Training Institute agreed to finance the RO plant, which was purchased and installed at Rs 7,50,000 in 2017. Every day, 10,000 litres of wastewater is purified in their RO plant to water thousands of plants.
The Miyawaki forest method was invented by and named after Japanese botanist Akira Miyawaki. Under this approach, dozens of native species are planted in the same area, close to each other, which ensures that the plants receive sunlight only from the top, and grow upwards rather than sideways. It is a multi-layered process, wherein different species of shrub layer (6 feet), sub-tree layer (6-12 feet), tree layer (20-40 feet) and canopy layer (above 40 feet) are planted next to each other. Plants grow ten times faster.” The sarpanch of the village ensured that different types of trees including fruit-bearing, root to flower-giving were planted. The forest has neem, karanj (Millettia pinnata), almond, gulmohar, pomegranate, custard apple, and jamfal (guava), among many others.
Kukma serves as a significant railway station, specifically a Flag Station, located approximately 10 km from Bhuj along the Gandhidham - Bhuj broad gauge route under Western Railways. The daily operation of essential railway services, such as the Kutch Express and New Bhuj Express (Sayaji Exp.), further establishes Kukma's importance as a transportation hub in the region. Additionally, the accessibility of National Highways NH41 and NH341 ensures convenient road connectivity to and from Kukma, facilitating seamless transportation for both passengers and goods in the area.
Kuldevi Temples of many clans of these Kutch Gurjar Kshatriya community are also there in this village. To mention, Kuldevi temple of Parmar clan of Momai mataji, Kuldevi temple of Chauhan clan of Brahmani Mata, Kuldevi temple of Rathod clan of Chaval Mataji have their temple in village.
Also Nivruti Ashram and Garibdash ji Bhojanalaya are located in Kukma. Also there is Thakore Mandir in main square and Mahadev temple both built originally by KGK (Kutch Gurjar Kshatriya) Community Also Tank clan and Gohil clan have kuldevi temples in the village.
As per the 2011 Census details, Kukma is characterized by the following demographic and socio-economic attributes:
Local Language: The predominant language spoken in Kukma is Gujarati, reflecting the linguistic and cultural identity of the local community.
Total Population: The village of Kukma has a total population of 7216 residents.
Number of Houses: Kukma consists of 1636 households, indicating the residential infrastructure within the village.
Female Population: Approximately 48.3% of the total population in Kukma is female, contributing to the overall gender composition of the village.
Literacy Rate: The village exhibits a literacy rate of 68.1%, indicating the percentage of the population with the ability to read and write.
Female Literacy Rate: The female literacy rate in Kukma is recorded at 30.0%, reflecting the percentage of females in the village who possess literacy skills.
Explore the Kukma Lake: Start your visit by taking a leisurely stroll around the picturesque Kukma Lake. Enjoy the serene atmosphere and take in the beautiful views of the surrounding landscape.
Visit the Kukma Fort: Discover the historical significance of Kukma by exploring the Kukma Fort. This ancient fort offers a glimpse into the region's past and provides a great opportunity for photography enthusiasts.
Experience the Local Cuisine: Indulge in the flavors of Kukma by trying out the local cuisine. Visit the bustling street food stalls and restaurants to savour traditional dishes like Kachori, Bajra Roti, and Ghevar.
List of craftsmen.
Team Gaatha
Interview – Tejsi Bhai & His Son
https://khamir.org/crafts/kharad-weaving
https://kalpavriksh.org/wp-content/uploads/2020/01/Kutch-Short-Report-final-2019.pdf
https://www.academia.edu/63948102/The_Sheep_Wool_Craft_Value_Chain_in_Kachchh_Understanding_it_through_the_Viewpoint_of_Different_Actors_in_the_Chainhttps://aif.org/delving-into-the-incredible-wool-crafts-from-kachchh/
https://www.directcreate.com/profile/1041/samt-tejsi
https://timesofindia.indiatimes.com/city/rajkot/kutchs-kukma-village-shows-the-way-to-live-in-perfect-harmony-with-nature/articleshow/83289679.cms
https://reshamdor.in/art-in-craft/https://www.thebetterindia.com/252756/akira-miyawaki-forest-kukma-kutch-gujarat-panchayat-sarpanch-village-kankuben-water-crisis-drought-environment-green-cover-india-gop94/