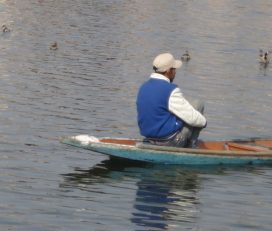
Shikara (Boat)~ Kash...
Also called the ‘camel of Dal Lake’ due to its importance, the multi-functional shikaras are a lifeline for the people of Kashmir.
Srinagar...
Locally known as ‘Bharai kaam’, Dhokra is the art of sculpting brass using the ancient technique of lost – wax casting. Practiced in West Bengal, Orissa and Madhya Pradesh, this metal craft finds different forms of expressions in its pure folk motifs and figures within the different tribes.
The bell metal casting technique is used to make a variety of objects ranging from household items to accessories. It is used to craft figures of elephants, horses, cattle and peacocks, utensils and jewelry. The popular objects made using Dhokra are:
Phorla (wrist ornament), Bisto (wrist ornament worn by females of Gond tribe), Kakana (bangles), Mudda (for males – worn in marriage), Hasli (necklace), Mudda (toe ring), Kapdonda (used to light cigarettes) and Morchimni (a peacock shaped lamp).
In Dhokra or lost-wax casting, wax strings are coiled to create beautiful patterns. The natural beeswax retains its malleability even after cooling down, making it an excellent choice to create coiled shapes and miniature patterns. Spiral, cross – hatched or smoothed into a flat surface, the texture of these wax threads will determine the final appearance of the metal product.
The cattle – bell is believed to be one of the oldest objects made using this technique. It is worshiped as god by some of the Gonds as the sweet sound of the bell is symbolic of cattle rearing which signifies prosperity.
The ‘Dhokra Shilpis’ (dhokra craftsmen) often work with brass (copper + zinc) or bronze (copper + tin). If the tin content is high, the alloy is called bell metal. Unlike the craft of earthen pottery, where traditionally the wheel turning is reserved for men, there are no restrictions in Dhokra work and can be practiced by either men or women. Children learn the craft through imitation and instruction.
Metal Casting is one of the most widely used sculpting techniques and has been prevalent since ancient times. The method, in which a mould is created by carving a hollow in stone has strong hints of a primitive era, when modern methods had not been invented.
The famous ‘dancing girl’ of Harappa, dating back 5000 years, is the earliest known specimen of lost – wax casting. This technique is believed to have originated in the ‘Indus Valley Civilization’ around 3500 BC. Two copper figures made with the Dhokra technique were excavated from Lothal an ancient Harappan site in Gujarat.
Wax – cast artifacts made in Indo – Greek style and a figurine of young Harpocrates (the god of silence) from 1st century BC, were excavated from the site of ‘Taxila’. The iconic bronze statue of Lord ‘Nataraja‘ (8 – 15th century A.D.) and the 3,000 year old bronze figure of ‘Mother Goddess’ discovered at ‘Adichanallur’, Tamil Nadu, were both created using the lost wax process.
Dhokra has been extensively used in creating temple idols, oil lamps, utensils, jewelry, and large weapons. In the modern day, it finds its place in religious ceremonies and traditions. In many communities as a religious custom, daughters are gifted with intricately crafted ‘Diyas’ (lamps) as part of the wedding ritual.
From 750 B.C to 1100 B.C the craft flourished in different regions of India namely Rajasthan, Gujarat, Raipur, Sarnath, Andhra Pradesh, and Tamil Nadu. During the period between 1500 B.C and 1850 B.C, the craft retained its dominance in south India. The craft is still passionately followed by the tribal folk of Madhya Pradesh, Chhattisgarh in central India, Orissa, Bihar in west India and Tamil Nadu (Swamimalai), Kerala (Munnar) in south India. Some of the regions in Madhya Pradesh and Chattisgarh have historic connections with the craft. A number of tribal artisans have traditionally been involved in practicing the craft. Tribes namely the ‘Malar’ from ‘Sarguja’, ‘Jhara’ from ‘Raigadh’, ‘Ghadwa’ from ‘Bastar’, ‘Swarnakar’ from ‘Tikamgarh’ and ‘Bharewa’ from ‘Betul’ have all been instrumental in preserving the craft and keeping its beauty intact. The basic method of casting done in ‘Sarguja’, ‘Tikamgarh’, ‘Bastar’ and ‘Betul’ is almost similar with slight differences occurring due to the difference in available raw materials as well as the difference in environment.
When the central state of Madhya Pradesh divided into the current states of Chhattisgarh and Madhya Pradesh, the vast majority of land inhabited by the Dhokra craftsmen went over to Chhatisgarh. It was then that ‘Madhya Pradesh Hastshilp Vikas Nigam’ started a Dhokra facility in Betul, to continue the craft in the state. Today, many craftsmen learn and practice this tribal art form at the facility, to create traditional objects as well as commercial artifacts for the larger market.
The designs used in Dhokra craft are a mix of realistic forms and figures and abstract aesthetic expressions of spirituality of the local people. Tribal myths, magic and designs inspired by nature are given form through this art.
Surface ornamentation is an important aspect of these cast metal products and the craftsmen still use old motifs which have become more refined with time. Most of these motifs are circular or linear in shape and the ornamentation is done on the wax structure. The various motifs made using the wax threads are ‘Chakri’ (spirals), ropes, waves and zigzags. While the motifs are few, the craftsmen use different combinations of motifs to derive a wide variety of new patterns that add richness to the designs.
One of the biggest challenges of the craft is the rising price of raw material. With the raw material being steeply priced, the craftsmen try to counter it by mixing cheaper alternatives and that adversely affects the quality of the finished product.
Also, various natural impurities like hay, dust particles etc. get mixed with the wax creating pinhole scars and uneven surfaces after the metal casting is finished.
In the dhokra technique metal casting moulds are custom made by hand for each product. A base form is created using mud and cow dung mixture and over this, beeswax threads are coiled to create the desired shape of the final product.
Brass- This is mainly used to cast different objects and artifacts.
Burnt clay- This is taken from previously broken moulds or burnt and broken by the craftsmen. If there are no tools available for breaking, the craftsman lays the mould on the road in front of their houses to be broken by passing vehicles.
Cow dung- This is mixed with mud to form a mixture used as the base as well as outer coating when making the mould.
Water- This is mixed in desired quantities to the mud- cow dung mixture to form a smooth paste. It is also used to test the effectiveness of the custom made drainage structure created in the mould.
Vegetable oil- This is used as a lubricant to grease the interior of the extruder as well as wooden board when rolling out wax sheets.
Beeswax- This is made into strips and coiled to create various patterns in the mould which shapes the final design. The material retains its malleability even it has cooled down after being heated.
Saras- This is a kind of resin gum that is mixed with beeswax to create wax threads and strips.
Coal- This is used as fuel in the kiln.
Furnace – This is used to bake the mould and also to melt brass.
Coal-pick – This is used to add coal in the furnace fire.
Iron file – This is used to polish and finish the final casted metal product.
Pincers or tongs – Used to handle the mold when pouring in the molten metal.
Lachhna – iron strips, used for different purposes like heating the wax, sticking with hot wax, etc.
Kati – small iron chisel used to cut wax strips and designs.
Hatha – This is a wooden tool, used to make wax strips and thick wax sticks.
Patha – This is a wooden board used for working the wax materials.
Pichkari – Multi-holed syringe like tool used to create wax threads. ‘Sikkey’ or coins are small metal coins with holes of different diameters inside the Pichkari, which help in drawing out threads of required thicknesses.
Kachni – wooden stick used for sticking and shaping small wax rings.
Kavelu – Terracotta tile piece used for smoothing and shaping the core.
Hammer – This is used to break open mold.
Axe – This is used to break open the baked mold to reveal the final product.
In the dhokra technique metal casting moulds are custom made by hand for each product. A base form is created using mud and cow dung mixture and over this, beeswax threads are coiled to create the desired shape of the final product.
Creating the core
In designs which are either large or have a hollow space within, the core is made with sand. In the last stages of the production, sand is removed leaving a hollow core behind thereby, greatly reducing the amount of brass required to build the complete design.
Usually the core is made with a mixture of fresh and burnt clay. In this process the black burnt clay is first sieved in a moderately large vessel that has been covered with an old, gauzy cotton cloth. The dust is poured over the cloth and rubbed with hands to help it pass through. Burnt clay is used here because it doesn’t shrink after drying and is easily removed from the finished product due to its weak binding strength. At this stage a small quantity of cow dung is added to the burnt clay and mixed together creating the core mixture.
The stability of the core at high temperatures is determined by the proportion and composition of these materials. The core mixture is shaped by hand to a desired form and left to dry naturally. If done properly cracks should not develop after drying. At this stage the core is rough and a little larger than the desired form. It is buffed using a terracotta tile to achieve a final shape removing any excess materials. The terracotta pieces are dipped in marl to add strength and achieve a smooth finish. The designs are left to dry in the sun for a few hours.
Preparation of wax
To prepare the wax an appropriate amount of beeswax and resin are mixed to together in a calculated ratio. During the winter months less amount of resin is used as it hardens the mixture quickly.
The mixture is filtered through a fresh piece of cotton cloth and the process involves two persons, as one holds the cloth the other pours the mixture. The wax needs to be stirred continuously through the cloth for an easy and quick flow. The filtered pure wax is collected in a container filled with cold water which is kept underneath the cloth. The collected wax is stored for hardening. After half an hour the hardened wax is taken out of water, broken into 4-5 pieces and kept in sun light for 4-5 hours. This softens the wax and is kneaded with hands for approximately half hour making it malleable enough to be drawn into wires.
Working the wax dough
The wax is worked by two methods, rolling into flat sheets to be stored away or by drawing into long wires using an extruder. Flat sheets are also made with ‘Hata’ on the wooden platform. Before making sheets small quantity of oil is applied on the platform and the wax lump is placed on it. Sheets are made by beating the wax lump with the hata.
In the latter, wax threads of different diameters are created by changing the extruder plate. Sheets are used to create flat surfaces while the threads are used to make coiled lines. A coin shaped part is fitted in the nozzle of the extruder or ‘Pichkari’ and changed according to the diameter required. Some amount of vegetable oil is applied inside the nozzle and a small lump of wax is inserted in it. Wax threads are drawn by pressing the wax lump with the piston.
Attaching the core pins
When the wax melts away, it generates a gap between the core and the mould. The core pins are provided to prevent the core from moving inside the mould when the wax melts away and the brass has not yet been poured into the cavity. These pins are iron nails pushed into the core which fixes themselves to the moulds. The use of core pins result in a uniform wall thickness of brass and prevents irregularities such as holes.
Making the mould
After a pattern is made using wax, a wax runner is fixed to it form a point. This assembly is dipped into soil slurry. The slurry is able to seep into the minutest details of the design due to its intricate consistency.This improves the surface quality of the product. After the slurry dries, this is again covered with a coarse mixture of cow dung, soil and hay to make the final mould.
Preparing the brass
Brass pieces are usually scraps obtained easily in the local markets. The calculation of how much brass needs to be used in the product is determined as 6 times the amount of wax used. A hemispherical clay pot holds the scrap with some salt added to it as flux. The pot is covered with a flat clay disc with holes. The mould is stuck on top of this using clay at the joint.
Furnace
The furnace is a pit dug into the ground having an intermediate grid. The chamber below the grid has an air passage which opens at the ground level after running a little distance away from the furnace. Cow dung cakes, used as fuel, are placed above the grid. The opening for air is attached to a blower. A layer of coal is added on top of this. The firing of furnace takes place mostly in the day, to avoid the heat of the daytime.
When the brass has melted the mould is picked up using tongs and shaken to check if the metal has come to the molten state. The wax melts away, leaving a cavity for the metal to be filled with. The mould is then inverted to enable the molten metal to flow into the mould from the clay pot.
Breaking the mould
Once the metal settles in, the mould is cooled for a while in air and then immersed in water. It is then cracked open and filed to reveal the exquisite product. When the mould is broken, the metal changes its colour due to oxidation so it becomes important to polish it properly to regain the original colour and shine of the metal.
Wax, Ash, Backed clay mold
The earliest evidences of Betul's history are date as far back as 700 AD. However, ancient sculpture and buildings found in the nearby villages suggest that it must have gone through the similar stages of development as the other civilizations. The statues and sculptures found near Betul by archeological survey of India illustrate the use of metal casted jewelry in ancient times in his area.
It is believed to be initially a part of 'Magadh' dynasty, which was later taken over by 'Vidarbha' dynasty as written in 'Malvikagnam' by Kalidas. It later became a part of several different regimes like the 'Kherlas', 'Malwas', 'Gonds', Mughals, Marathas and the British.
Raja Jetpal is said to be the last Rajput emperor of Kherla. In some places Kherla is mentioned as one of the four old Gond rajya (the tribal territories). Some historians believe that he was a tribal king, Kherla reined in 14th and 15th centuries. Here is a big lack of knowledge about the origin of the rulers of Kherla, making the early history of Betul District almost completely mysterious. For many years the historians thought that the dynasty who ruled Kherla was just another Rajput family, like many others who were ruling over petty states throughout Central and Western India. But it is recognized today that the Raj Gonds must have had some important role in the birth of this little but important Kingdom. Most of the Indian scholars today state that the Kherla kingdom's dynasty was a Raj Gond dynasty or at least of mixed origin, of Rajput and Raj Gond. The first mention of a king ruling in Kherla was contained in a religious work called as the Vivek Sindhu, which is said to be the oldest document in Marathi language. According to the book Jaitpal was the last member of a Rajput dynasty ruling in Kherla. This is the only reference to the Kherla dynasty and it is nearly impossible to determine who the kings were; but it seems likely that they were the ancestors of Narsingh Rai, who was the founder at Kherla in the next century.
After the death of Mukund Raj there was probably a change in the dynasty of the kingdom. In 1398, Narsingh Rai was induced by the Mohammedan kings of Malwa and Khandesh to commence hostilities against the Bahmani kings of Gulbarga whose territories included Berar.
He became officially an Amir of the Sultan. Firoz Shah becoming reconciled to Narsingh Rai gave him a dress of honor, richly embroidered with gold and receiving one of his daughters into his harem with a present of forty-five elephants, a considerable sum of money and other valuables, he directed the siege of Kherla to be discontinued. The state of Kherla lived in peace for more than two decades, but, after that period, a new invasion came from the west, from Hoshang Shah, the ruler of Malwa in about 1420 AD, invading the territory of the small Gond kingdom.
Hoshang soon defeated Narsingh Rai. The kingdom of Malwa, to which the Kherla kingdom was soon merged, asserted its independence against the Tughlak dynasty of Delhi during the feeble rule of Muhammad Tughlak. Their capital was at Mandir on the crest of the Vindhya Range. The Malwa dynasty lasted only for over a century and in 1531 AD, its territories were annexed to the Mohammedan kingdom of Gujarat. In 1497 AD, Muhammad Shah Bhamani sent Nizamul Mulk laid siege to Kherla and finally occupied the fort. He was however subsequently slain by two Rajputs belonging to the Malwa army.
In 1560 AD, Akbar occupied Malwa but whether Kherla was incorporated in the Mughal Empire immediately or at some subsequent date is not known. However, it was included to the Subah (country subdivision) of Berar, which was founded about 1596 AD, or very shortly after the conquest of Berar. Kherla was the headquarters of a Sarkar or district subordinate to the Subah or province of Ellichpur and the Kherla Sarkar included 35 Parganas embracing the centre and the south of Betul district and some tracts of Chhindwara and Wardha regions. After that time, the fort of Kherla continued to be in the middle of wars and was captured and lost many times by the Malwa rulers. The most famous Gond king of Deogarh, Bukth Buland, is said to have taken control over the fort in the 17th century. After that date the destiny of Kherla was not separated from that of the Gond kingdom of Deogarh (1590 - 1789).
The Gond kings fought many wars and battles with the powerful Muslim kingdoms of southern India and survived for a century. It then was taken over by the British in 1817 A.D.
Betul is situated about 175 km away from Bhopal, the capital of Madhya Pradesh and is located at 21.88 N Latitude and 77.98 E longitudes. It is about 6562 feet above the sea level.
The airports nearest to Betul are situated in Bhopal and Indore. Betul is connected by National Highway to Bhopal. Betul railway station is located between Bhopal and Nagpur station. Betul is easily accessible by buses and trains from Bhopal. Tigaria, a small village about 10 km from Betul can only be accessed through bicycles or private vehicles.
Betul is essentially a highland area, divided naturally into three distinct land portions, differing in their aspects such as the character of soil and geological formation.
The northern part of the district forms an irregular plain made of sandstone. It is a well -wooded region but has a very sparse population and little cultivated land.
In the extreme north, hills arise out of the great plains of Narmada valley. The central region possesses a rich soil, well watered by the 'Machna' River and 'Sapna'dam. This region is almost entirely cultivated and comprises of several villages.
To the south lie a rolling plateau of basaltic formation with the sacred town of Multai, and the springs of the Tapti River at its highest point. It extends over the entire southern face of the district, and finally merges into the wild and broken line of the Ghats that lead down to the plains. This region consists of a succession of stony ridges of trapped rock, enclosing valleys of fertile soil, to which cultivation is for the most part confined.
Betul district is rich in forests and biodiversity and the main timber species of Betul Forest is Teak. Many miscellaneous types of trees such as 'Haldu', 'Saja', 'Dhaoda' are also found in abundance. Many medicinal plants are also found in the forest areas of Betul. Large amounts of commercially important minor forest produce such as Tendu leaves, Chironji, Harra, Amla are also collected from the forests of Betul. Asia's biggest wood depot is in Betul.
The major rivers flowing in the district are Ganjal River (tributary of River Tapti), Rivers Morand and Tawa (tributaries of River Narmada). The Tapti River originates from 'Multai' in the 'Betul' district. Multai's Sanskrit name 'Multapi' means 'Origin of Tapi' or 'Tapti River'
The climate of Betul is characterized mainly by a dry and hot summer with rainfall during the southwest monsoon season. The winter season lasts from December to February, followed by the summer season from March to about first week of June. The period from mid June to September is the south - west monsoon season.
May is the hottest month of the year with average temperatures of 39.36°C, while the minimum temperature of 10.3 °C is experienced in December. The average annual mean maximum and minimum temperatures are 30.7°C and 17.9°C respectively.
The south-west monsoon starts from middle of June and lasts till end of September. The months of October and mid-November constitute post monsoon or retreating monsoon season. The average annual rainfall of Betul district is 1192.6 mm and about 86.6% of annual rainfall is received during the monsoon season. Only 13.4% of annual rainfall takes place between October and May.
The lowest level of humidity is experienced in the month of April. It fluctuates between 31% to 91% at different times, and different seasons. The wind velocity is higher during monsoon as compared to pre and post monsoon. The wind velocity is higher in June, ranging about 8.5 Km/hr and is lowest in November ranging about 3.8 km/hr.
The drainage of the district is diverted in all directions from the Satpura plateau. The northern and central parts of the district drain into River Narmada, in the north through Tawa, Machna, Morand and the Bhange.
In the district, there are five types of soils namely 'kali', 'Morand', 'Matbarra', 'Bardi', 'Sihar' and 'Retard' soils. The southern, central and eastern parts of the district are covered with black cotton soil. Betul is mainly a region of 'Kharif' crop. Besides cereals, sugarcane and spices are also produced here. Groundnut, cotton and jaggery are locally produced and exported. Resin, gum, bamboo, teak and tendu leaves are main forest products of this district.
Farming and metal casting are the chief occupations of the people of Betul besides some secondary occupations. The tribal economy is mainly based on the weekly 'Haats' and 'Baazars' held in nearby villages. Generally, these people are from the lower economic strata of the society but their status is rapidly rising due to the growing market. It is one of the 24 districts in Madhya Pradesh currently receiving funds from the Backward Regions Grant Fund Programme (BRGF).
The houses are mostly covered with cow dung and roofs are made with terracotta tiles. One of the rooms of the house, usually the front room (which has the same width as the whole house) has the furnace. In some houses, the furnace is located outside.
The craftsmen have small three roomed ‘Kachha’ huts, which have a low ceiling entrance. The walls of the huts are coated with clay and cow dung while the roofs are made of bamboo structures and terracotta tiles. The living environment is pollution free and pleasant owing to the farms that surround the houses.
The craftsman cleans and maintains the work areas before and after working.
Monuments and relics of historical relevance such as ‘Khedla’, which was the seat of the ‘Gond’ Dynasty in the 13th century, are to be found all over the district. At ‘Asirghad’ and ‘Bhawarghad’ in ‘Multai’ tehsil, caves have been found that were once the hiding place of the ‘Pindaris’. Situated at ‘Bhainsdehi’, there is an ancient Shiva temple built of carved stones that now lies in ruin.
An influence of Bundelkhandi language and culture can be seen in the northern part of the district, while overtones of Marathi language and Maharashtran culture can be seen in the southern belt of the district.
Betul is a tribal district of Madhya Pradesh wherein 'Gond' and 'Korku' are the main tribes residing in this area. Apart from them, the 'Bhilala', 'Pardhan' and 'Bharewa' tribes are also the inhabitants, though the 'Bharewa' tribe is not much in number.
From 1911 AD to 1921 AD about 16000 people from different parts of the country, mainly 'Hoshangabad' and 'Amravati' (Maharashtra) migrated to Betul district. The migration gradually influenced the dialect and the lifestyles of the region.
Hindi, Marathi, Gondi and Korku are the main languages spoken in this district and people worship both Hindu and tribal gods. The rest of the district is predominantly tribal, populated by the 'Gonds' and 'Korkus', who worship Bada Mahadev and perform sacrificial rituals. Despite being educated, regional superstitions are prevalent. They also use natural herbs for healthcare.
One of the prominent institutions of the region is the Bhatkhande Sangeet College, a music college where groups of research students work with various music directors. There is also an archeological museum that has been working for more than fifteen years. It constitutes a small collection of statues and sculptures; recently the District Administration has displayed information on the points of historical interest.
All over the District are scattered Monuments and relics of historical interests such as Khedla, which was the seat of the Gond Dynasty way back in the 13th century. There are other smaller ports at Asirghad and Bhawarghad in Multai Tehisil. Some caves have also been seen, which are supposed to be the hiding place of the 'Pindaries'.
At 'Bhainsdehi', there is an Old Shiva Temple built of carved stones. The roof had collapsed long ago; presently there are some beautifully carved pillars.
7 Km from Amla there are twin villages of 'Kazili' and 'Kanigiya', which contain old Temples of Hindus and Jains built in stone. They appear to be places of considerable religious importance. Excavations carried out here can result in the discovery of numerous objects of Archeological value.
At Muktagiri, there are some Jain Temples built on a hill as the name suggests the place had been sacred to the Jains, who came here to pass their last days. The District is famous for the apprising of the tribal against the British rule. Banjaridal, a village in Betul Tahisil is well known for the martyr Vishnu Singh Gond. The District greatly participated in the growth of freedom movement, no fewer than 50 volunteers took part in the Conference of congress at Nagpur.
The district is rich in tribal population. The tribal population of the district as per 2001 census is 5,49,907. One of these tribes, 'Bharewa' is instrumental in the practice of lost-wax casting craft. The meaning of 'Barrera' is 'one who fills', taken from the Hindi word for the act of filling, 'Bharna'. So, the people who create brass artifacts by filling molten metal in moulds are called 'Bharewa' and the caste is known as 'Bharewa' too. In some areas, 'Bharewa' are also called 'Bharias', but they do not belong to the 'Bharia' caste, which is distinctively different from 'Bharewa' caste.
Bharewas live in Phongaria, Chunahajuri, Barkhad, Kalamesara, Tigariya and Chitakamat villages of Betul district and follow a simple way of life. They generally live in nuclear families with the eldest male member being the head of the family and the chief decision maker. The whole family works as a unit wherein the women are also involved in the metal casting. Men wear mostly white cotton clothes and older men wear 'Dhoti' (a traditional draped garment worn as trousers by men) and 'Kurta' (men's traditional long shirt) or 'Ganji' (inner vest). The attire is completed by wearing a turban or a cloth tied around the head (a traditional headgear for men). This is considered to be a sign of respectful identity.
Banjaridal, a village in Betul tehsil, is famous for martyr Vishnu Singh Gond who rebelled against the British. Monuments and relics of historical places such as Khedla stand testimony to the 13th century Gond dynasty. The twin villages of 'Karzili' and 'Kanigiya' have ancient Hindu and Jain stone temples which are have considerable religious importance.
Shri Rukmani Balaji Temple is situated in Betul Bazaar, in the Betul District of Madhya Pradesh. The main building of 'Shri Rukmani Balaji' Temple conforms to the architecture used in South Indian temples and many reputed architects from South India were involved in the project. Individual sections of the temple resemble smaller temples, enshrining idols of Lord Ganesh, Radha-Krishna, Goddess Durga and Lord Shiva. There are three smaller temples dedicated to Lord Hanuman, Navagraha, and Saint Shirdi Sai Baba outside the main block. There is an artificial pond named Gangakund, stretching from outside gate to the main building, which contains a total of 10 fountains. Another major attraction is a python shaped structure which is a tunnel leading to all the shrines in the complex.
Kukru is a scenic village situated on the Maharashtra-Madhya Pradesh border, with a total population of 400. It is in the valley of Satpura hills and located about 75 km from the district headquarters 'Badnur', and is at a height of 3500 feet above sea level. The village is growing to be a popular tourist destination owing to its green natural surroundings.
List of craftsmen.
Team Gaatha
http://www.craftrevival.org/Monograph/003397.htm
http://www.ssmrae.com
https://docs.google.com
Interview: shri Sukhram waghmare, betul (07/05/2013)