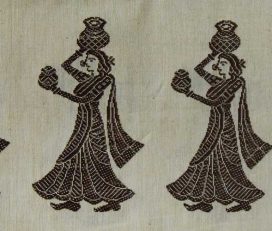
Gollabhama Saree Wea...
The Siddipet Gollabhama Saree is not just a piece of fabric; it is a living tradition, worn, celebrated, and reinterpreted through generations.
Siddipet, Telangana, India...
The second you step foot in the workspace of the Chennimalai weavers, you get a rush of an insight that makes you realize how the life of people here revolves around threads and different handloom items. The aura of the workspace creates a buzzing visual of an endless sea of colourful threads. It is these threads that provide the weavers with happiness and sadness and act as a source of their smiles and joyful tears. They appear like the silhouettes of mountains that are held by wooden frames. It is believed that nature is translated and resided in these threads Every single thing you see here- from the sun’s rays to the smiles of the weavers, from the dust in the air to the frames of looms- everything is held by an aesthetic combination of threads.
Jacquard weaving is used for home décor items that feature multiple colourful patterns with florals, leaves and geometric patterns inspired by temple architecture. The designs used are very old fashioned and heavy and the thread used is very thick. These bedsheets made from this weave are popular among local population.
Home furnishing constitutes an important product diversification among the handicraft categories. Chennimalai is a famous cluster in Tamil Nadu that produces bright artefacts for home décor.
Sandalwood assumes cultural significance among the weavers in Chennimalai. It is often smeared to the looms of the weavers since in Tamil Nadu, because it is believed to known to bring abundance, wealth and prosperity.
Chentex is the handloom co-operative set up in Chennimalai, Tamil Nadu that sought to bring fair wages and employment to the weavers of the place. It was set by the co-operative movement leader MP Nachimuthu.
The fame of the handlooms from Chennimalai travelled far and wide – so much so that Ikea the Swedish furniture brand had sourced fabrics from Chennimalai for their home décor pieces titled Indira and Linda.
The Five P is a venture started by father daughter duo C Devarajan and D Shree Bharathi in 2013 who sought to revive the handloom town of Chennimalai. The venture hopes to “inspire a movement of sustainable production and consumption of clothing and textiles by showing that conscious manufacturing and consumption is the way to a livable future”.
Chennimalai produces a series of home décor items that can be used to decorate every item in a household. The products produced here can be categorized into two– first, simple weaving. This is used for making several bedsheets with vibrant colours and checked patterns. Second, jacquard weaving. This weaving is used for home décor items that feature a plethora of kaleidoscopic patterns with florals, leaves and geometric patterns inspired by temple architecture.
All the products of Chennimalai can be seen as falling under the ‘bed and bath category.’ This includes bedsheets, blankets, pillow covers, napkins, table mats, towels, handbags and every other possible home décor item that can come to one’s mind. Due to the large size of the looms available here, the weavers can stitch king and queen-sized bedsheets through the handloom.
The weavers of Chennimalai produce and create utility-based products. There are many skilled stitching units in the city. The woven fabrics society weavers are developing many ready to use products like table mats, table covers, bags, quilts, curtains, cushion covers etc.
The products of Chennimalai are so beautiful and of such magnificent quality that they find their usage not only in the South Indian households of India but also in other parts of India and worldwide.
Chennimalai is a fast-growing cluster with a young population of weavers who are eagerly taking up the weaving profession and incorporating contemporary patterns into their home décor items. Chennimalai has also gained significance over the years since a large number of exports of home décor items such as bed sheets, towels, blankets, napkins and other bed and bath items are sold all over the country and even abroad.
Co-optex has a major role to play in the work of the weavers and the selling of the products. This society not only aims at sales increase for the weavers of the Chennimalai cluster but also at the improvement of their working conditions and equipment.
Due to the rapid transport and network system created here and the incoming talent of weavers, the Chennimalai cluster is gaining significant acclaim and praise from all over. Moreover, since a lot of individuals in this region purchase handloom items, the weavers always have an idea of how to improve their work and capture the eyes and heart of their consumer market.
The craftsmen of Chennimalai are skilled to such a large extent that they go beyond the woven fabrics and develop many products like bags, quilts, cushion covers, curtains, and towels. International buyers also give them new exposure for international orders they receive designs from the buyers and execute it skillfully. These designs also help in developing new aesthetics and the possibility to explore new designs. Society weavers are using many types of weaving structures with a 4-5 colour combination in bright and light colours.
The handloom was devised about 2,000 years ago and was brought to England by the Romans. The process consisted of interfacing one set of threads of yarn (warp) with another (the weft). The warp threads are stretched lengthwise in the weaving loom. The weft and the cross threads are woven into the warp to make the cloth weaving remained unchanged for hundreds of years until John Kay devised the flying shuttle which enabled a weaver to knock the shuttle across the loom and back again using one hand only. The speed of weaving was doubled and a single weaver could make cloths of any width, whereas previously two men had sat together at a loom to make broadcloth. By 1800, it was estimated that there were 250,000 handlooms in Britain.
After the British captured India, they took up and nourished handloom industries for their purposes at the end of the 18th Century the monopoly came to an end. Since the 19th Century, with the advent of the industrial revolution, the English people gave up all. They started medical production in their land. During this period of foreigners, the weavers of Tamils learned all techniques and they prevailed the way for the production of furnishing factors according to the new style of demand.
Weavers of Chennimalai used to weave sarees and lungis for trading and their welfare. As the country started growing after independence and people started building their lifestyles in different ways, the weavers began making bedsheets and various home decor pieces.
M. P. Nachimuthu was a Padma Shri award winner in 1983 for his social work in the handloom field. He was responsible for introducing home decor manufacturing at Chennimalai. He was the founder of Chentex Hand Looms in Chennimalai.
Nanchimuthu, the President of Co-optex, 1953-69 devoted his entire life to the development and growth of the handloom industry in Tamil Nadu.
Today Chennimalai is one of the pioneers of the home decor industry. There are almost 33 societies that the weavers have built. Weavers never differentiate between their home and their working space, they keep their belongings around them while working so they don’t feel like they are away from home, creating a heart-warming homely aura.
It is not just the government that has taken steps to preserve their traditions of weaving by providing looms to the families. They also build relations and make connections with weavers as their own family. They take steps to create a friendly environment, take care of their welfare and preserving their skills.
Among the many designs traditionally woven in the Chennimalai cluster, the two coloured checks, jacquard motifs in three colours, and a finer fabric in a single colour are the highlights.
The craftsmen of Chennimalai are skilled to such a large extent that they go beyond the woven fabrics and develop many products like bags, quilts, cushion covers, curtains, and towels. International buyers also give them new exposure for international orders they receive designs from the buyers and execute them skillfully. These designs also help in developing new aesthetics and the possibility to explore new designs. Society weavers are using many types of weaving structures with a 4-5 colour combination in bright and light colours.
There are mainly 3 types of weaves found in this cluster, these are-
Plain Weave – The weavers make simple weaves with plain colours, lines, and bold checks. Bright and light colours are combined to make a certain eye-catching combination, based on demands in the product like bed sheets, curtains, raw material for bags or quilts etc.
Terry Plain weave– This weave has an additional set of loops woven through the surface of the fabric. These loops are then left uncut to form piles on the surface of the fabric, which is gives Terry a distinctive looped surface texture on both sides.
Jacquard Weave – Jacquard designs in two or three colours are also woven. These have bold floral designs in repeating patterns. The thread used is very thick so the patterns do not look thin-lined. These bedsheets made from this weave are popular among local Tamil people.
Artisans are skilled and societies are open to new designs and innovation.
This cluster mainly faces two challenges-
First, the government spending is mainly directed towards the agricultural sector and other prominent sectors due to which the handloom industry is often ignored. In particular, the handloom industry of Tamil Nadu faces a problem with a lack of financial facilities. Various commercial banks have failed to provide the cooperative societies with resources and this has directly failed the cooperative movement in Tamil Nadu. At the same time, there has been an unexpected sprout in the power looms which has led to a scarcity of yarn. Therefore, the main challenge is the lack of yarns. This points out the need for the government to supply yarn to the handloom industry.
Second, there has also been a sharp increase in the cost of production of these textiles due to which there has been a challenge in the process of selling. This is further worsened by the problem faced by this industry in the marketing of its products and the pressures of globalization. It has been suggested that the government must take more initiatives to modernize the power loom sector to make it more competitive domestically and internationally. Thereby, highlighting the need to improve the infrastructure in the industry.
However, several positive outcomes and suggestions have also been highlighted in the case of these weavers to move ahead and further increase their sales.
Small changes in the work environment have made major improvements. For example, a big roof utilizes the solar heat of the region to generate enough electricity that powers light and fans, and the Roof Ventilator Wind Turbine (exhaust) creates a pleasant working environment. Therefore, in the field of work environment, Chennimalai can set a great example for other handloom clusters.
There is a need for energetic and young weavers to participate in the weaving process. Weavers have to pass their skills to the following generation. Good daily wages and a good working environment can attract young people. Each society should train one person in design intervention according to the market.
A sample loom can also be installed for colour or weave explorations. Jacquard designs are very old fashioned and heavy, smaller motifs, geometric patterns and a play of shades in the same colour can be a new design direction for the weavers that can attract a large number of consumers. Giving traditional motifs a modern twist in terms of layout and placement, for example, plain bedsheets with motifs on the border can bring a new outlook to the designs. Different counts of yarn with weaving techniques, for example, Twill with colour weave and the shadow weave can be explored more.
New product categories like laptop sleeves, iPad covers, bags and table runners can be explored. A brainstorming on product range is much needed.
The process consisted of interfacing one set of threads of yarn (warp) with another (the weft). The warp threads are stretched lengthwise in the weaving loom. The weft and the cross threads are woven into the warp to make the cloth weaving remained unchanged for hundreds of years until John Kay devised the flying shuttle which enabled a weaver to knock the shuttle across the loom and back again using one hand only. The speed of weaving was doubled and a single weaver could make cloths of any width, whereas previously two men had sat together at a loom to make broadcloth.
Yarn Type: Cotton 2/17, 2/30, 2/40, 10s yarn for warp and weft society weavers are working with CO-OPTEX getting yarn from NHDC. There are many private Spinning societies in Tamil Nadu such as; Krishnagiri Cooperative Spinning mill, Ramanathapuram Cooperative Spinning mill, Kanyakumari Cooperative Spinning mill etc.
Dye: After getting yarns from NHDC or mills, they are dyed locally. The dyeing unit uses wet dye, pc active dye and Naphthol dyes. This process takes about 7-15 days and colour accuracy is 90%.
Loom Type: Frame loom 2 to 8 paddle, 120-240 hooks Jacquard, products are home decor. Product loom size is big, On normal jacquard loom 90-inch width fabric can be woven and for a normal loom, 110-inch width fabric can be woven. For finer count weave, artisans also use pit loom at home.
Chandan or sandalwood has a prime significance in this weaving process. Owing to its auspicious properties, Chandan is smeared onto the looms of the weavers since in Tamil Nadu, Chandan is known to bring abundance, wealth and prosperity. Therefore, all looms of these weavers feature marks of Chandan and sometimes even photographs of deities or popular political leaders. The weavers seek the blessings of these individuals, touch the Chandan and only then begin their weaving process. These rituals attach an element of sacredness to the entire weaving process.
First of all, it has to be decided how many heddles and treadles need to be used to make a particular design or weave. The number of different warp and weft interlacements in the weave will decide the number of treadles and heddles required. In the handloom weaving, the weaver has to do drafting, denting, as well as tying up the treadles with the heddles according to the design required.
Drafting or drawing in after getting the warp beam the weaver has to pass the warp through the heddles (heald eye) according to the weave planned. This is called drafting or drawing in.
Denting– It is the process of passing the drawing in ends through the reed for beating purposes. There can be two ends per dent or three ends per dent as per the requirement. More clearly the number of ends per dent depends upon the number of threads required and the warp count. In the case of selvedge, the denting order may be different compared to the main body of the fabric.
Tie up – Once the weaver finishes the drawing in and denting, the next process he/she has to do is to tie the healds with the treadles. The loom parameters like correct warp tension, the proper opening of shed, reed movement etc, is to be checked to ensure whether the loom is compatible with weaving or not. If not the weaver has to make adjustments in the above as required and should take precautions, to minimize or avoid the yarn breakages. It is the weaver’s responsibility to check the shed opening by false picking and reed movement by false beating.
Pirn Winding– A simple machine is used for pirn winding in handloom. There is a wheel and a metallic shaft, which are connected with the help of rope for transferring motion. The hank is mounted on the wheel and the pirn is mounted on the shaft. The yarn from the hank is transferred onto the pirn by rotating the wheel.
Therefore, the entire process can be summarized as once all the threads are coloured and measured out to the right length and order, the next step is winding the warp onto the loom. Winding is transferring yarn from one type of package to another bobbin or Pirn. A spinning wheel (charka) is used by the handloom weavers to transfer yarn. First, they wind weft yarn onto a pirn and then the pin is inserted into the shuttle. The shuttle will carry the weft yarn across the loom, in the space created between threads that are raised and threads that are not.
The cluster employs both men and women, young men work on jacquard looms while women on a simple loom. Many weavers collect designs, warp and weft yarns from society and then work from home. On average, a single weaver weaves 4-meter jacquard & 8-meter plane fabric per day. Society groups also act together to meet the common needs and aspirations of their weavers, sharing ownership and making decisions democratically. At the Diwali festival, societies distribute the profits to their members based on the transactions with the Cooperative society. With the help of government schemes, the society also takes care of society members by providing housing loans, Insurance etc.
The majority of the time, chemical dyes are used to add colour to the sarees. This is done since the chemical dyes ensure that the saree has bright and vibrant colours that are preferred by the customers. As a result, natural dyes are no longer given preference. Due to this, after the dyeing process, whatever portion of the dyed water is left has to be thrown away. This contributes to the significant amount of wastage and pollution. Since cotton is widely used for the production of various home décor items, it is important to look at the wastage in the process of making these items and using them wisely.
During the recycling process, the cotton waste is first sorted by type and colour and then processed through stripping machines that break the yarns and fabric into smaller pieces before pulling them apart into the fibre. The mix is carded several times in order to clean and mix the fibers before they are spun into new yarns. The resulting staple fibre is shorter than the original fiber length, meaning, it is more difficult to spin. Recycled cotton is, therefore, often blended with virgin cotton fibers to improve the yarn strengths. Commonly, not more than 30% recycled cotton content is used in the finished yarn or fabric. Since waste cotton is often already dyed, re-dyeing may not be necessary. Cotton is an extremely resource intense crop in terms of water, pesticides and insecticides. This means that using recycled cotton can lead to significant savings of natural resources and reduce pollution from agriculture. In fact, recycling one tonne of cotton can save 765 cubic metres of water. This ensures that the wastage is curbed and environment-friendly methods are adopted.
The name, ‘Chennimalai’ comes from famous Devasthanam on the hill. This hill has Lord Murga Temple and rare medicinal herbs in its lush green forests. Chennimalai falls under the Erode district of Tamil Nadu. Thus, to understand the history of Chennimalai through the ages, we can look at historically rich past of the Erode district.
In the past, the Erode district used to be a part of Coimbatore due to which its history is inextricably linked with that of Coimbatore. In the Sangam era, these two regions formed a part of a country called ‘Kongu Nadu.’ Initially, this area was occupied by tribal groups The most prominent among them being the ‘Kosars’ who reportedly had their headquarters at ‘Kosamputhur’ or early Coimbatore. These tribes were then overpowered by the Rashtrakutas. After which, the region fell into the hands of the Cholas who ruled over this region between the 10th to 12th century.
Post-decline of the Chola regime, Kongu Nadu came to be occupied by the Chalukyas and later by the Pandyas and Hoysalas. Due to internal dissension in the Pandian Kingdom, the Muslim rulers from Delhi interfered and the area then fell into the hands of the Madurai Sultanate. Soon after it was taken over by the Vijaya Nagar rulers after overthrowing the Madurai Sultanate in the 14th century.
For a few years, the area remained under Vijaya Nagar rule and later under the independent control of Madurai Nayakas till the 17th century. The rule of Muthu Veerappa Nayak and that of Tirumalai Nayak were marked by internal strife and intermittent wars which ruined the kingdom. As a result of this, the Kongu Nadu region (present Erode District) fell into the hands of the Mysore rulers from whom Hyder Ali took over. The resulting fall of Tipu Sultan of Mysore in 1799 led to the the Kongu region falling into the hands of the East India Company under the Maharaja of Mysore. The Polygar chieftain Dheeran Chinnamalai was one of the governors of the region, who played a major part in the early struggle for Indian Independence in the Polygar Wars against the British East India Company. From then, till 1947, the area remained under British control who initiated systematic revenue administration in the area.
Therefore, through historical and archaeological evidence we can conclude that several dynasties and regimes ruled over the Erode region which has created a sense of plurality and diversity in this region. This is further visible through its people, culture and architecture.
Chennimalai is located at 11.17°N 77.62°E and has an average elevation of 320 meters. The district forms the meeting point of the Western Ghats and the Eastern Ghats separated by the Bhavani River. It comprises of a long undulating plain, sloping gently towards the Kaveri River in the south-east. Three major tributaries of the river Kaveri, Bhavani, Noyyal and Amaravati, run across the long stretch of mountains in the north. The Bhavanisagar Dam and Kodiveri Dam provide storage facilities and numerous canals along with these rivers and provide proper facilities for irrigation in the district. Noyyal river was the main water source of this town, however, this river has become polluted due to the Tirupur dyeing wastes.
The Erode district is characterized scanty rainfall and a dry climate. Generally, the first two months of the year are pleasant, but from March-May the climate becomes extremely hot. The cool, moist wind that passes through the Palghat Gap in the Western Ghats has a moderating effect on the climate of neighboring Coimbatore district, but the air loses its coolness and becomes dry by the time it reaches Erode. The temperature reverses its rising trend during the pre-monsoon period, that is, June and August. By September, the monsoon rains begin to fall. The northeast monsoon sets in vigorously during October–November. By December, the rains end, returning the climate to its dry and cold state. The soil in this region is predominantly of red sandy to red gravelly variety. Chennimalai is surrounded with a significant amount of flora, fauna, and greenery. When one visits the area, several large trees of coconut, mango and banana can be found amongst several other flower varities. This greenery appeals to the eye and makes people feel one with the nature.
The town of Chennimalai town is growing at a fast rate. By merging Chennimalai town panchayat with Ottaparai and Mugasipidariyur town panchayats, the town is expected to be upgraded into a municipality.
This town is well connect through road, rail and air which further facilitates transport, communication and development. Chennimalai has a bus stand located at the southern end of the town..Kanuvai is a narrow pass in the Chennimalai hill which is traversed by SH 96 and offers a scenic drive for the travel. The Ingur Railway Station is the closest to Chennimalai at a distance of about 6.8 kilometers and the Coimbatore International Airport located at a distance of 63 kilometers is the nearest airport.
There are several schools and colleges, both private and government that operate in the Chennimalai district, as well as clinics and hospitals. Moreover, the sanitation and sewage systems are also well in place and order. This ensures that the individuals are supplied with the basic amenities and services.
The architecture of Chennimalai is typical to that found in other South Indian districts and regions. In the earlier days, the houses in these areas were usually made with tiled sloping roofs and in the present day, one can find bigger houses with balconies and straight roofs. However, even in the modern day, the houses are constructed in a simple manner.
The temples of Chennimalai are an integral part of the culture and lives of the people there. In fact, several designs on the home décor items made here are inspired by the temple architecture.
The Chennimalai Murugan temple is of great significance in this region. It is located at the top of a hill, about 600 meters above sea level on the banks of river Noyal. This hill provides several medicinal herbs and is home to various animals such as deer, peacocks, rabbits, snakes and monkeys. Other temples such as the Valli Teyvannai Temple and the Pinnaku Siddhar Temple also have relevance in here.
Hinduism is the dominant religion of this district, other major religious groups are Muslims, Christians and Jains. Since ancient times people of this region have been known as Konga or Kongu, meaning inhabitants of the Kongu country. It has, in recent times of census, been given a division of a large number of classes, mostly Tamil, which include Ambattan, Kaikōlan, Kammālan, Kūravan, Kusavan, Malayan, Oddē, Pallan, Paraiyan, Shānān, Uppara, and Vellāla.
Kodumanal is a village located in the Erode district in the southern Indian state of Tamil Nadu. It was once a flourishing ancient trade city known as Kodumanam, as inscribed in Pathitrupathu of Sangam Literature. The place is an important archaeological site. The literature says that the people here were highly skilled craftsmen, who specialized in making beads, textile and high-quality iron. During the Iron age, quite a number of intact terracotta spindle with whorls pierced at the centre by means of an iron rod have been found. To strengthen the proposition that Kongu Nādu witnessed a thriving weaving industry, a remarkably well-preserved piece of woven cloth was recovered from the site at Kodumanal.
Tamil is the widely spoken language, the standard dialect being Central Tamil dialect. Kannada, Hindi and English are other languages spoken here. Lord Murugan and Shiva are the most widely worshipped deities. Pongal, Diwali and Mariamman are festivals celebrated with great pomp and show. Every year, during the Tamil month of Panguni, a grand festival is celebrated in Erode City. The festival starts on the first Tuesday of Panguni simultaneously at Periya Mariamman, Chinna Mariamman and Vaikkal Mariamman Temples.
Traditionally, Veshti (white fabric with simple line border) was the most common bottom-wear for men in Tamil Nadu. It is wrapped around the legs, tied at the waist and is the traditional dress worn by men in marriages too. This rectangular shaped cloth is generally made with cotton for daily usage and with silk for special occasions. It is mostly worn with a shirt or Angavastram on top. A Lungi (similar to sarong) is a traditional garment. It is either tucked in, over the waist, up to knee-length or is allowed to lie over and reach up to the ankle. It is usually tucked in when the person is working, in fields or workshops, and left open usually as a mark of respect, in holy places or when the person is around dignitaries. While most of the native crowd can still be seen in traditional wear, the younger generations and the office going men have also taken up t-shirts with the Lungi, although denims and pants are quite popular. The one thing that is common for every man is ‘vibhuti’ on their forehead in various formations.
Women, on the other hand, generally wear a draped form of fabric 6 to 8 yards in length. This is first tied around the waist with pleats gathered in front and then brought over the right shoulder, which is then brought in front along the waist. Most of the women wear synthetic fabric saree with bright colours and bold patterns. The women can also be seen wearing gajras in the hair and bangles in their hands.
As of 2011 census, Chennimalai urban agglomeration has a population more than 30,000. Males constitute 51% of the population and females 49%. Chennimalai has an average literacy rate of 75%, higher than the national average of 59.5%.
The people of Chennimalai are engaged in primarily the agrarian sector and handloom weaving. Though the soil is not the best, utilization of new methods of cultivation and improved strains of seeds together have helped the agriculturists in the district to maximize their output. Paddy accounts for 86,939 hectares, followed by Cholam which is sown in more than 11240 hectares.
Other important sources of income in the district are plantain, silk, cotton, turmeric, coconut, tobacco and sugarcane from agriculture and allied industries. Gobichettipalayam is well known for its white silk, cotton, plantain and coconut production. The district is rich in its natural cattle wealth and concerted efforts of the Animal Husbandry Department have further augmented the cattle wealth in the District. Burger breeds, though smaller in size, are well built & sturdy and are very popular. The cotton textile industry in Coimbatore and handloom industry in Erode district has encouraged the growth of various ancillary industries to meet the needs of the textile mills. Chennimalai, Erode, Gobichettipalayam and more, are important centres where cotton ginning is carried out on a large scale in the region. There are also important dyeing works in Erode, Chennimalai and Bhavani. A number of factories engaged in cotton fabric printing are also functioning in Erode. Rice milling is yet another industry which has been able to hold its own. Erode, Bhavani and Perundurai are the centres where a number of rice mills are flourishing. These mills engage in lucrative trade on the west coast.
Apart from its home décor products, Chennimalai is also famous for its agrarian sector production and temple culture.
List of craftsmen.
Team Gaatha