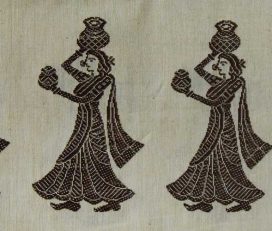
Gollabhama Saree Wea...
The Siddipet Gollabhama Saree is not just a piece of fabric; it is a living tradition, worn, celebrated, and reinterpreted through generations.
Siddipet, Telangana, India...
Weaving at Kuthampully dates back to 500 years ago, when Devanga Chettiar community of weavers came to Kuthampully from Tamil Nadu at the request of the King of Kochi to weave the clothes for the royal family. This community settled on the land with the Bharathapuzha river to the north and the Gayathripuzha river to the west. In course of time, the weaving cluster of Kuthampully flourished by producing different products like sarees (6m long cloth) for women, mundu (2m long cloth) for men and sett mundu (two piece saree) for women.
The Kuthampully sarees, sett mundu and dhotis are instantly recognized by their distinct drapes and borders. It has a cream-colored main portion of the body decorated with usually golden zari and sometimes with coloured borders.
Another significant aspect of this weaving is that no bleaching or dyeing is involved throughout the process of making except for the dyed yarn used in the weft for the border or cross-border.
Kuthampully cluster of handloom weaving is known for their fine quality. Initially during the origin of weaving at Kuthampully, the weaving was mainly done for only the royal members of the Cochin kingdom. The women of this royal family used to dress up by wearing their hand-woven products specially: Neriyathu, Kasavu Mundu (dhoti)and Kasavu Sarees. Men used to wear a plain white fine muslin cloth Mundu (dhoti) with a golden zari border.
Today, Kuthampully cluster still makes these traditional dhotis and sarees for men and women, for which the weaving of this town was earlier famous for. However, the designs have evolved and changed but the usage of these garments still remains the same.
For Men– The Kuthampully Mundu is still famous in this area. An unstitched garment of fine muslin cloth is woven by the weavers. The mundu is usually identified by its plain body and kasavu (embroidery work done from silver wires coated with gold) border. The main portion of the dhoti is left cream off-white in colour. While all the borders are in plain gold zari.
For Women– Kuthampully classic off-white cream colour saree and set mundu is famous. Set Mundu is considered as the traditional garment and as the oldest remnant of saree for women of Kerala. The Sett Mundu or called as ‘Mundum Neriyathum’, is a combination of Mundu for covering the lower part of the body while Neriyathum is to wrap around the upper portion of the body. It basically acts like a dupatta over the blouse. The set mundu consists of two pieces of cloth: the Dhoti or Mundu and Neriyathum or also called Kavani. This garment is either sold alone or as a part of a set, including both dhoti and Neriyathu.
Initially, it is said that the younger girls used to wear green hand-woven blouses, while the married middle-aged mothers used to wear red blouses. Thus, the colour of the blouse would determine the age and the marital status of the women.
At present, an extensive series of cotton set saree, embroidery saree, hand-painted cotton and tissue saree, sett mundu, men’s dhoti and veshti with different colours recently adorns the product line.
The Kuthampully sarees, sett mundu and dhotis are instantly recognized by their distinct drapes and borders. It has a cream-colored main portion of the body decorated with usually golden zari and sometimes with coloured borders.
Another significant aspect of this weaving is that no bleaching or dyeing is involved throughout the process of making except for the dyed yarn used in the weft for the border or cross-border. The sarees of Kuthampully are the most visible style outside the state. These sarees are typically woven using a half-fine zari, which generally keeps down on the cost of the final product and adds to its popularity. It is a unique experience that the entire weaver community of Kuthampully works towards a specific purpose with such perseverance and diligence.
Long ago, there’s a tale about how this caste began. When Brahma crafted Manu, he assigned him the task of weaving clothes for both gods and humans. Manu diligently wove for years, eventually ascending to heaven through his righteous and virtuous life. However, after he left, gods and humans were left without weavings, resorting to wearing leafy garments.
This situation troubled them, and they prayed to Brahma for help. Brahma took them to Siva, who swiftly created a radiant being named Devalan. The brilliance of Devalan startled everyone, causing them to scatter, except Parvati, who remained by Siva’s side. Siva explained that Devalan was designed to weave clothing for gods and humans, thus covering their bodies. The descendants of these beings came to be known as Devangas. The Devāngas trace their lineage back to Devalan, asserting that they are Devanga Brāhmans.
the Baramahal Records says, the fascinating story of the Devangas’ origin unfolds. When Brahma, the creator, fashioned the living and non-living, crafting gods, demons, and humans, there arose a predicament: they lacked any covering for their bodies. This concern reached Narada, the wise being, who brought it to the attention of Parameshwara, the mighty Lord residing atop Kailasa Parvata, the mountain of paradise.
Parameshwara recognized the importance of addressing this issue and, from his very form, brought forth a male figure named Deva angam, meaning the body of God. Curious about his purpose, Deva angam inquired. Parameshwara directed him to seek Sri Maha Vishnu, the revered god, who dwelled by the sea of milk. Vishnu instructed Deva angam to weave cloth, thus aiding the inhabitants of the universe. He offered fibres from a lotus flower that blossomed from his navel and taught him the art of crafting cloth.
Deva angam wove a piece of cloth and presented it to Vishnu. After receiving it, Vishnu commanded him to travel and utilize tree fibres to clothe both gods and humans in the Vishnu loka. Deva angam formed a group of ten thousand weavers, gathering fibres from forests and skillfully fashioning them into garments.
One day, while collecting tree fibres in the earthly Bhuloka, Deva angam’s group encountered aggressive giants known as Rākshasas. Fueled by anger, he unleashed his long, coiled hair and struck it on the ground. In that instant, a powerful goddess named Chudeshwari emerged, armed with eight weapons. She defeated the Rakshasas, earning her the title of goddess of the hair. Grateful for her protection, Deva angam chose her as his guardian deity.
There is a myth associated with the Kuthampully weaving craft form. It is believed that the culture of the weaver community of Kuthampully i.e Devanga Chettiar, closely resembles Tamil culture. They are devotees of goddess Chamundeswari, whose main temple is located 13 km away from Mysore city on Chamundi Hill. In Kuthampully village, these devotees have built two temples for the goddess.
The Devanga Chettiar community believe that their craftsmanship is a direct result of Chamundeshwari’s benevolence. It is said that this community never makes use of modern equipment. The speciality of Kuthampully weaving is its fine cotton and pure gold kasavu. They believe that, if this is made with the help of modern equipment or handlooms, it will destroy their quality of craftsmanship, and it might anger Goddess Chamundeshwari.
The town of Kuthampully located about 50km northeast of Thrissur district is a traditional cotton weaving village. The history of weaving at Kuthampully dates back to 500 years ago, when Devanga Chettiar community of weavers came to Kuthampully from Tamil Nadu at the request of the King of Kochi to weave the clothes for the royal family. This community settled on the land with the Bharathapuzha river to the north and the Gayathripuzha river to the west. In course of time, the weaving cluster of Kuthampully flourished by producing different products like sarees (6m long cloth) for women, mundu (2m long cloth) for men and sett mundu (two-piece saree) for women.
Through the skill and crafts of Devanga Chettiar community, these weavers brought new life to the state of Kerala’s traditional wear- the sett mundu also called as ‘veshti’ and settu saree (golden zari border). In course of time, Kuthampully became one of the prominent centres for the production of handloom sarees and veshtis in Kerala state.
In 1972, Kuthampully Handloom Industrial Co-operative society was established with 102 members. The society is established with an aim that the ancient methods that were earlier followed back then still need to be continued irrespective of the changing world and current trends. This society is managed by a seven-member elected body. It provides decent income to the weavers and also helps them to centralize their efforts by promoting and selling the Kuthampully products. The raw materials to make these products are supplied to the weavers by the society and wages are given based on the production. The famous Kasavu double dhoti, sett mundu, veshti are the popular products of clothing that are produced in this society. Recently, few modern weaving techniques have also been introduced to meet the current contemporary market demands.
At present there are 160 weavers working under the society. Apart from this society, there are other privately owned units in the village which constitute nearly less than 1000 weavers. In 2011 September, Kutampully sarees and sett mundu got exclusive Intellectual property Rights through Geographical Indication Act. GI tag is given by the Government of India to preserve the traditional knowledge of the region or a community which are specialized in a certain craft form. The Kuthampully products use a Government of India handloom hallmark that ensures their products are genuine and is the original handloom of Kuthampully.
Earlier during the rule of the kingdom of Cochin, where weaving of Kuthampully started and was later introduced in the market, it was woven without motifs and only with plain gold kasavu, zari borders. Traditional weaving of Kuthampully was woven as a mundu (dhoti) for men and sett mundu sarees for women. The mundu basically have a gold zari border at the end. While the sett mundu is a classic off-white cream colour stretch of cloth with gold kasavu in the pallu and the main body of the saree. These garments are generally woven from natural cotton yarn. Recently, few new experiments have been done with the patterns like weaving the same designs using coloured yarn for the weft and some popular imprints inspired from nature like peacock, elephants and flowers; imprints inspired from religious culture of Kerala- Lord Krishna motif; and also designs inspired from culture most famous one is design of Kathakali face. These types of imprints made garments are specially sold during traditional festivals like Onam.
During the 1990s, the use of ‘hal-fine zari’ at the border was quite famous. These traditional designs were made in ivory colour with golden borders. People today still make demands of these traditional designs which has now become a mark of divinity and prestige for Keralites, especially among the Hindus. At present, different types of varieties are introduced in the borders like the ‘tissue kasavu’ (woven alternately with the cotton yarn and the zari border). This type of border is considered generally stiff. The typical length of Kuthampully woven saree is 6.25m with a blouse piece. While 5.5m in length without a blouse piece.
Kuthampully weavers known for their creation of classic off-white garment with gold kasavu border now are facing a challenge to continue this craft-form. An aging workforce shifts in demand and power looms and low income are forcing the weavers to change their traditional occupation. Keeping the recent scenarios in mind, the pandemic, floods and the disapproval of the younger generation towards continuing their family handloom craft has caused the weaver community a severe crisis. Another issue is that the tourist who is not able to distinguish between the handwoven and power-loomed handloom gets easily manipulated. There is an increase in use of power-loom made handlooms recently in Kuthampully. Due to this, the weavers who used to make a chunk of profit during festivals by selling traditional and authentic hand-woven garments are now unable to do so. Hene, the majority of the weavers currently have a low income.
In the last 15 years, almost 150 weavers have quit weaving and have taken up different professions to earn their livelihood.
Various preparatory processes and tools are used in this type of weaving. These various pre-loom methods have been mentioned below.
Raw materials required are:
Cotton Yarns: 80s and 100s fine cotton yarn used to make Kasaragod’s saree
Zari: Currently, weavers utilize artificial zari threads in various shades including gold, silver, and copper. In contrast, in earlier times, authentic zari was employed, crafted by winding metal foil onto cotton threads.
Rice water (Kanji vellam): A liquid in which cotton yarns are wound up on the pins
Chalk Powder: Used to apply on the table for pasting the next set of fabric for printing
Sticker Gum: Used to stick the fabric firmly during the printing process
The type and quality of traditional products used is connected with the type of tools and techniques used for weaving and also with the pre-loom activities. The handloom industry of Kuthampully has the reputation as the weaving facility for manufacturing fine cotton combed yarn by 80s and 100s fine cotton yarn using a specific loom. The border of the saree and dhoti is often woven in extra weft zari designs by using either a dobby or jacquard loom. Also, the pallu of the saree is also woven with jacquard loom. For the preparation of warp thread, ‘street sizing’ technique is used. The street-sizing technique helps the warp threads to become almost round and uniform in shape so that the fabric has a very clear surface without any protruding fibres on it.
Wooden Handloom: The weavers employ both wooden frame looms and pit looms, each equipped with two paddles.
Jacquard or Dabby: To create intricate patterns and designs on fabric. This is done by controlling each individual thread using a series of punched cards or, in more modern versions, electronic controls. The Jacquard loom revolutionized the textile industry by allowing for complex and detailed patterns that were previously challenging to achieve.
Charkha: Weavers use a charkha to load the bobbin. During the weaving process, the bobbin is placed within the shuttle for the weft.
Small Bobbins: Used to wind the zari for warping
Scissors: Used to cut the extra fabric
Measuring Tape: Used to measure the length and width of the fabric
Piece of Fabric: Used to stick on the two edges on the printing table
Sandpaper: Used to rub the corners of the fly for better weaving
Safety Pins: Used to hold the printed fabric for drying
The process of making the special Kuthampully saree of either white or cream with a traditional kasavu (golden threads), involves the constant efforts and hardships of the weaver during all the steps of making it. Initially, paavu or starched cotton thread would come from spinning mills in bundles, in which each bundle is sufficient for weaving maximum six sarees. Usually, the elders in the family would separate and straighten out the threads and then they twist them into rolls that could be fed into the loom. Since these threads were about 44m long in length, the rolling and straightening was done standing on the street and it required at least seven pairs of hands. Meanwhile, the women and children of their community would help in spinning the yarn and twine the bundles of kasavu into smaller rolls using a charkha. It would usually take an entire day to complete this process.
At present, cotton yarns for making Kuthampully sarees are brought from the Salem regions of Tamil Nadu, while zari threads are brought from Surat. The cotton yarn in the roll form is then wound to a small pirn for the weft purpose and immersed in the kanji liquid for the purpose of stiffness. While rolling on the beam and knotting to the previous yarns, the fingers are first dipped into the melted wax to avoid the slipperiness of the fingers while rolling. The yarn is then extended and the beam is positioned on the loom for the process of weaving. While the threads of zari are wound up to small pirns for the design and weft purpose. The zari threads are usually kept dunked in water, to preserve its quality, shine and texture while rice water or kanji is used for the normal cotton yarns. These zari threads from the bobbins are passed through the eyelets and are then rolled on to the warping beams. It is said that, when the zari threads are passed through the eyelets these eyelets moved from one end to the other end of the warping frame, thereby winding about as said in the local language- ‘ Three Mona’, meaning (one set of the top and the bottom threads of the warp). These zari threads are then knotted to the earlier threads. They are then extended and applied with wax from one side to the other for the purpose of stiffness. After the zari threads and cotton yarns are inserted and tightened to the required length, the weaving process then starts with the controlled mechanisms of the jacquard loom for the insertion of the patterns.
It is important to note here that, although the weaving process is done on the handlooms, those sarees woven on the power looms from the Erode and Salem regions are brought to Kuthampully town for finishing work of the printing. This method is then followed by the screen printing where the films of the designs are sent from Tirupur and the screens are set here. As per the need, these screens are cleaned properly with the wet cloth and then the colour paste made is spread evenly to imprint the design on the fabric which is placed firmly to table with the chalk powder and the sticker gum. According to the weavers, in most of the cases the fabric observed is rough and hence, these fabrics are sent through the calendering process in order to obtain a smooth finish. It is then folded, pressed and packed now ready to be sold.
To sum up, these are steps, the weavers of Kuthampully follow for weaving:
1. The cotton yarn is brought from Salem while zari threads are brought from the Surat regions of India.
2. These cotton yarns are wound to pins with the help of Charkha equipment and are then immersed in the Kanji liquid for stiffness.
3. Cotton yarns are then spread on the beam, knotted with earlier cotton yarns and are then fixed on the loom.
4. Zari threads are then wound to pirns with help of Charkha equipment for the weft process.
5. Zari bobbins are then fed to the zari warping beam which has the eyelets moving from one end to the other end by the process of winding in the required length.
6. These zari threads are then knotted firmly to the earlier threads by applying the wax throughout the length for the better grip.
7. Right after the zari threads and cotton yarns are positioned on the loom, the weaving process then starts with the controlled mechanism of the jacquard for the insertion of the patterns.
8. As per the requirements, the woven fabric is then taken up for the embroidery and printing work.
9. This fabric is evenly spread on the table with the help of sticker gum and chalk powder.
10. According to the desired color and prints, the printing paste is made and it is spread through the screens to the saree pieces.
11. This fabric is then passed through a series of rollers for a smooth finishing touch which is usually referred here at Kuthampully, as ‘calendering process’.
12. The fabric is folded properly and is now ready to be sold.
The history of Thrissur district dates back to the 9th century. The period between 9th to 12th centuries is considered the history of Kulasekharas of Mahodayapuram. While the history after the 12th century is considered as history of the rise and growth of Perumpadappu Swarupam. The period between 14th and 15th centuries, constituted a period of severe aggressive wars during which the Samorins of Calicut acquired a major part of the present Thrissur district. Portuguese dominated this district in subsequent centuries. However, Portuguese power in Kerala, was on the verge of collapse in the beginning of 17th century. During this period, various other European powers like Dutch and English appeared and challenged the Portuguese. It is believed that, in this period, the discussions with Perumpadappu Swarupam helped the Dutch in getting a footing on the Kerala coast. At this point Kerala was conscious of the impending doom of the Portuguese, they thus looked upon the Dutch as the rising power and extended a hearty welcome to them. The consequential want of solidarity opened the floodgates of aggression, and between this period Tipu Sultan and Hyder Ali were figured prominently.
Raja Ravi Varma also known as Saktan Tampuran ascended the throne of Cochin in 1790. He is considered as the architect in developing the Thrissur district. With the accession of Raja Ravi Varma, the modern period in the history of Cochin began. In this period, all the administrative authority in the state was assigned to him and by the then sovereign on the initiative of Travancore Raja and the Dutch governor. Saktan Tampuran, as the name suggests the king was a strong ruler and his reign was characterized by firm administration. The king of Cochin was responsible for the destruction of the power of the feudal chieftains and increase of royal power in this area. Apart from this royal power, another major force entered in the public life of Thrissur and its suburbs was the Namboodithiri community. A major part of Thrissur Taluk was for long under the domination of Yogiatirippads, the ecclesiastical heads of the Vadakkunnathan and Perumanam Devaswoms. Under the Yogiatirippads, the Namboodithiri families of Thrissur were playing an active part against the ruler of Cochin in his wars against the Zamorin of Calicut. However, in 1761, after the expulsion of the zamorin from Thrissur action was taken against these families by the Raja of Cochin. The rule of Yogiatirippads ended and the management of Thrissur was taken over by the government. The Namboothiri were also reduced to impotence. Hence, the anti feudal measures of Raja Ravi Varma coupled with the several administrative reforms formed by him marked the end of the medieval period of Cochin. Soon, in the early 1805 period, the wave of nationalism and political consciousness which had swept throughout the country had its repercussions in Thrissur as well. It is considered that, in 1919, a committee of the Indian National Congress was functioning in Thrissur. It is said that, in the 1921 Civil Disobedience Movement, several people from Thrissur took an active part. Thrissur is honored for having been in the fore-front in this country-wide movement.
Kuthampally town in Thrissur district, became the centre for weaving in the 18th century, when the rulers of Cochin Kingdom brought weavers from Karnataka to weave garments specially for them i.e royal members. Since then these weavers have settled and continued to practice the traditional craft of weaving.
Thrissur City formerly known as ‘Trichur’, is a central state situated in southwestern India. Thrissur is located 12miles inland from Arabian Sea coast on an extension lagoon system. A commercial and cultural centre, this city is considered to be the oldest city on the west coast of India. The name ‘Thrissur’ means small sacred place. It is built around a hillock topped by the Vadakkumnathan Temple, dedicated to Lord Shiva. This city is home to some of the oldest churches and mosques in the country. Apart from rich culture and history, the city has few industries too like cotton weaving, rice, oilseed milling, sawmilling and soap manufacturing. It is not only a retail hub of the state of Kerala but is also a home to some of the largest textile and jewellery businesses in the region. The area surrounding Thrissur city, lies majorly on the coastal plain except in the southeast, where it overlaps the hills of the Western Ghats. Another important occupation in this region is agriculture mainly of rice and coconut, as these two are main crops of Thrissur.
Thrissur, established in 1949 is the cultural capital of Kerala state. Malayalam is the main language spoken in this region. However, apart from Malayalam, due to high literacy rate, people of this state are also aware and can speak Hindi and English languages too.
The town of Kuthampully is endowed with a distinct air of spirituality reverberating through the quaint temples and shrines strewn its landscapes. The old and traditional neighbourhoods and stretches of greenery lining its narrow paths, give this town an aesthetic as well as rich feel.
Thrissur is a fast developing district. The well established public health sectors, educational sectors, and transport system are some of the tertiary sectors that enable to boost the infrastructure of this district. The district is well connected to local roadways and national highways. The railhead connects to other major cities of South India. Before the development of roadways and railways, people of this district traveled through the inland waterways that traverse through the canals of the region. The development of infrastructure in Thrissur district has led to the reduction in the cost of production of the industries in this region. The headquarters of all renowned banks like Catholic Syrian Bank, Dhanlaxmi Bank and South Indian Bank are located in this district.
Due to the well-developed tertiary sector of Thrissur district, it aids in the development of their economy.
By creating a beautiful combination of different cultures and traditions, the town of Thrissur charms its way into every traveller’s heart. This small town has left its important mark on the historical aspect of Thrissur. This town is known for its unique features and it has been fortunate enough to witness many eventful historical moments and to keep pace with the socio-cultural sphere. A devout town, the majority of houses in this region is built in typical Kerala style of architecture with tilted roof and white washed walls. Due to various ancient and historic structures situated in this town, it gives an aesthetic appeal to this town.
Thrissur district is considered as the cultural capital of Kerala state. This district enjoys a thriving cultural tradition that dates back to centuries. Thrissur is known for its rich history in literature, cuisines and festivals. The largest festival of Kerala called ‘Thrissur Pooram’ is celebrated every year in the month of mid-April to mid-may. The district hosts a large gathering of people and elephants as they form a major part in many of Thrissur's festivals. Another festival, ‘Aanayoottu’ (feeding of elephants) is held in this district at Vadakkunnathan temple annually, and is considered as the district’s largest elephant feeding ceremony. Some other important festivals celebrated here are Onam, Christmas, Diwali, Easter, Eid and Vishu. Apart from the festivals, Thrissur is also known for its rich literature work. The government of Kerala has set up various institutions like Kerala Lalita Academy, Kerala Sahitya Academy, College of Fine Arts to promote the literature, arts and music of Kerala. When India got independence, Thrissur district was declared as the literary capital of Kerala, as it turned to be the foundation of novelist, orators, scholars and poets.
According to the census of 2011, the district of Thrissur has a population of 315,957. Males constitute around 48.2% while females constitute around 51.8& of the total population. The total number of households in this district is 66,827, where the average family size is 4.27 members. The literacy rate of Thrissur is 95.5% in which male literacy rate is 97% while female literacy rate is 94.6%.
Hindu community dominate this region as it constitutes 58.42% The other communities that live in Thrissur district is Christian and Muslim communities that constitute around 24.27% and 17.07% respectively
Thrissur which is also known as Trichur is a historical city and the headquarters of the Thrissur district in Kerala state. It was once a capital of the kingdom of Cochin, and was a point of contact for the Greeks, Persians, Arabs, Romans, Dutch and English. Apart from being a historical and culturally rich city, it is also a major academic hub and is home to various educational institutions like Kerala Agricultural University, St. Thomas College, Kerala Kalamandalam and Kerala Varma College. Thrissur is also considered as an important religious place. Asia’s tallest church- Our Lady of Dolours Syro-Malabar Catholic Basilica is located in this district. It is considered as the masterpiece of architecture and the indigenous paintings. The first church in India, ‘St. Thomas Syro-Malabar Church’ is also situated in this region. Kuthampully is also famous for being a location for the shoot of the malayalam movie, ‘Shringaravelan’.
List of craftsmen.
Team Gaatha
1. Ajith C., “Power looms may anger the goddess: The Story of unique weaver’s village in Kerala”, Scroll.in, (January 29, 2017).
‘Powerlooms may anger the goddess’: The story of a unique weaver’s village in Kerala (scroll.in)
2.Anonymous, “ Handloom Weavers of Kuthampully”, WelcomeKeralaonline.com website, (July 1, 2015).
Handloom Weavers of Kuthampully | Welcome Kerala Magazine (welcomekeralaonline.com)
3. Anonymous, “Experience Ancestral Tradition at Kuthampully”, Annamalai Homestays Online website, (December 3, 2020).
Experience Ancestral Tradition at Kuthampully (anamalahomestays.com)
4. Anonymous, “Kuthampully Sarees”, Vikaspedia online website.
Kuthampully Saree — Vikaspedia
5. Anonymous, “Kuthampully Village in Thrissur”, Keralatourism.com website.
https://www.keralatourism.org/destination/kuthampully-handloom-village/584
6. Sunny S., “A Stroll through the weavers village of Kuthampully in Thrissur district”, Onamorama, (March 24, 2021).
A stroll through the weavers’ village of Kuthampully in Thrissur district | Onmanorama Travel
7. Padmadas R., “Kuthampully Weavers: Off-white to darkness?”, Pari, (June 19, 2019).
Kuthampully weavers: off-white to darkness? (ruralindiaonline.org)
8. John H., “How Kerala’s Kuthampully Weavers Battle Competition and Dept to Keep the Art Alive”, The Newsminute, (December 30, 2020).
How Kerala’s Kuthampully weavers battle competition and debt to keep the art alive (thenewsminute.com)
9. Baral B., Divyadarshan C.S., Amulya S., “Saree Weaving-Thrissur, Kerala”, D’scource website.
D’source Credits | D’Source Digital Online Learning Environment for Design: Courses, Resources, Case Studies, Galleries, Videos (dsource.in)
10. Vattolipurakkal P., “Kuthampully Handloom Workers”, (2013).
https://www.academia.edu/9487812/Kuthampully_Handloom_Workers