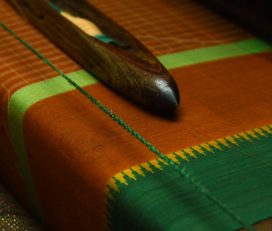
Saree Weaving ~ Nara...
Narayanpet sarees, handwoven in the small, vibrant town of Narayanpet in Telangana, are not confined to ceremonial grandeur or museum-worthy curation.
Narayanpet, Telangana, India...
Nandna is a mud resist block-printing craft of Madhya Pradesh and is one of the very few crafts being practiced in its original form. The fabric thus printed is then worn by the women from the local Bhil tribes as their traditional attire. But what sets Nandna prints apart from the other printed fabrics is its intact rustic look and ancient motifs, equally revered by the contemporaries. The craftsmen use naturally derived dyes on chaste cotton fabric and age old block designs inspired from the nature.
The distinct feature of Nandana prints is its intact rustic look and ancient motifs, equally revered by the contemporaries.
The fabric of Nandna is believed to have united the two religious communities for more than two centuries.
The technique of ‘Dabu’ (mud) printing is only practiced in ‘Umedpura’ and the craft is so well honed that the prints are in demand by the ‘Bagh’ printers as well, despite the fame the ‘Bagh print’ gets. It is the use of ‘Datta block’ for mud-resist printing in Nandna fabric that sets them apart.
Dabu is more sustainable compared to batic as they use organic colours and vegetable pastes which are eco-friendly.
Traditionally, ‘Nandna’ print fabric was only used by the women of ‘Bhil’ tribes. Their traditional attire would consist of Nandna printed skirts that doubled as a dhoti when working in the fields. An extended length of cord fabric is attached to the front of the skirt, which when pulled back and tucked into the back of the waist, divides the skirt into a loose pulled back type of trouser known as ‘Dhoti’. Having become quite popular, ‘Nandna’ textiles and techniques are now incorporated into other garments, bedspreads, table cloth, other furnishings and upholstery.
The natural dyeing of cloth depends on three key factors: type of fabric, dye-bath and mordant. About five to fifteen colours or shades can be derived from a single type of plant. Wanting to adopt a more eco-friendly procedure, craftsmen have started using more natural dyes instead of synthetic ones. Nandna was earlier indigenous to Umedhpura in Madhya Pradesh, as the rich mineral content of River ‘Gambhiri’ enhanced the colours of the fabric. The production of Nandna is said to be equally divided amongst both Hindu and Muslim communities, the ‘Chippas’ and the ‘Nilgars’ (printers and dyers). The fabric of Nandna is believed to have united the two religious communities for more than two centuries. The technique of ‘Dabu’ (mud) printing is only practiced in ‘Umedpura’ and the craft is so well honed that the prints are in demand by the ‘Bagh’ printers as well, despite the fame the ‘Bagh print’ gets. It is the use of ‘Datta block’ for mud-resist printing in Nandna fabric that sets them apart.
Indigo, a natural dye that is mainly used in the craft is considered highly and revered amongst the craftsmen community. They believe that a cow which drinks the solution becomes stronger and that if they eat with Indigo-stained hands, there won’t be any problems with the food or digestion. They say that Indigo has the power to turn anything natural. Wearing Indigo dyed fabric is thereby considered auspicious.
The various motifs like ‘Champa’, ‘Jalam Buta’ and ‘Amba’ were prized possessions among the women of the Bhil tribe. The presence of particular motifs determined their importance in the tribe and amongst other women. These motifs were also considered to be auspicious as they were worn during important occasions like weddings and childbirth. The fabric is also believed to be best for rough use and would last more than a year with frequent washes and no extra care.
No work related to printing is looked down upon or attributed to a certain class of people. The division of labor is only associated with the amount of work and the size of the family. Therefore, an increasing number of family members does not pose a problem but provides extra hands for work. The craftsmen have no fixed working hours and usually work for a minimum of 16 hours a day.
Block printing in India is an ancient craft, dating as far back as 3000 BC. It can be traced back to the Indus Valley Civilization and some historians are of the view that India may have been the original home of textile printing. Archaeological evidence from Mohenjedaro establishes that the complex technology of mordant dyeing had been known in the subcontinent from at least the second millennium BC.
India has been renowned for its printed and dyed cotton cloth since the 12th century. The country was one of the largest exporters of textiles from the 16th century till the beginning of the 19th century. In the textiles exported, ‘chintz’ was most sought after, though it was also produced in Europe. This was the name given to any cotton or linen fabric with floral patterns and fast colours. The brilliance of the colors in Indian chintz made it more appealing to the European buyers in the 17th century, than the very same fabric produced in their homeland.
Chinese chronicles report the arrival of printed cloth in China from India in 140 BC. In Europe, samples have been found in the 16th century grave of St. Caesarius of Aries. Very few pieces of fabric have survived the wearing of time and season, especially the monsoons. Practically all the material evidence before the 16th century seems to have been washed out. Indian fabrics were found at Fostat, in the outskirts of Cairo. They were excavated during the later part of the 19th century. A Frenchman named R. Fisher made the first concentrated study of the fabrics earlier than the 17th century – distinguishing them into block printed and the resist dyed. These were exported in bulk and were for the mass market than a luxury one. The block printed pieces were believed to belong to the 15th century.
The manner of printing helped distinguish between the fine and the commonplace chintz. The fine one was usually painted. Mordants and resists were applied in freehand using a brush or pen, whereas the commonplace chintz was printed. The gum-thickened mordants were applied using printing wooden blocks. In the paintings, outlines were impressed by blocks or blocks were used for transferring the resist material such as mud, wax, clay or starch.
Block printing was practiced in places like ‘Kukshi’, ‘Dharampuri’ and ‘Thikri’ by a group of people called ‘Chhipas’ or ‘Bhavsars’. A few Muslim dyers called ‘Rangrez’, practiced color printing in the town of ‘Dhar’. They catered to the clothing of the ‘Adivasi’ tribes. The patterns were mostly raw and coarse cotton was used.
The printers and dyers, in their quest for ideal conditions to hone their craft, also settled in the villages of Tarapur and Umedpura of Madhya Pradesh. The craft is believed to have existed for over three hundred years here, and grown to attain characteristic forms which make it exclusive to the region.
The traditional motifs of the Nandna prints are not necessarily influenced by the flora and fauna in that locality. The erstwhile nomadic life of the Chippa community has brought in influences from all over Uttar Pradesh, Madhya Pradesh, Rajasthan, Gujarat and Punjab. The blocks were also sourced mostly from Pethapur, where designs were eclectic. Therefore, the traditional motifs are inspired from nature and have no cultural influence on them.
‘Champakali’ (Frangipani) is worn by the unmarried women of the tribe. It also symbolizes fertility in some regions. Nandna fabric was worn by all the women of the Bhil tribe as it was most comfortable during their daily physical activities like farming. This is also a reason for the prevalence of dark colours like blue, and green as backgrounds. The skirts with ‘Amba’ (Mango) print are worn during marriages and also a few months following childbirth. It is traditionally gifted to the sister by the brother on ‘Raksha-bandhan’, ‘Diwali’ and ‘Teej’.
Champakali : Inspired from the Champa (Frangipani) flower, this motif has the stem bent to one side and the leaves on either side of the stem, ending in a flower.
Mirchi : As the name goes, the motif is inspired from the Chilli. The form is slightly bent towards the right side with respect to its background. The stem is mostly printed in Ochre and the chili in red and white.
Jalam Buta : This motif is of a fruit-bearing tree. The upright stem flourishes into leaves and branches with flowers on both sides. The stem is printed in Ochre and the foliage in red and white.
Amba : One of the most used motifs; the ‘Amba’ (Mango) has a stem which is bent in opposite directions at both the ends – to the right on top and to the left on the bottom. The stem has branches on both sides. It represents the mango tree and is mostly printed on a background color of blue.
Dola Maru : This is a combination of the ‘Champakali’ and the ‘Aekal’ motif. The name is rooted in the famous love story of the Rajasthani prince ‘Dola’ and the princess ‘Maru’ of the Poogal kingdom in Rajasthan.
The process of making ‘Nandna’ is very time-consuming. It takes around a month to complete one lot of fabric; roughly 800 meters. Skilled workers with years of experience are required to carry about the processes.
Many traditional methods of Nandna printing have been forgotten because of their labor intensive nature. The designs and patterns have been varied and retained according to the market demands, which are not that particular about the manner of printing anymore. There has been a stark decline in the volume of production over the years. Training is now being given for the less time consuming method of printing to cope with the fluctuations in demand without having steep effects on the craftsmen.
With the growing environmental consciousness, the craftsmen are seeking eco-friendly alternatives for various processes like dyeing and disposal of dyes. Preliminary steps like neutralizing the dye baths by adding acid or alkaline before draining are being carried out.
Due to the opening of factories in Jawad, many craftsmen have moved on for more income and less or fixed working hours.
Wooden blocks carved with traditional motifs are used to imprint the fabric in beautiful patterns. The resist dyeing technique is used and the craftsmen also specialize in mud-resist printing. The ‘Gadh’ and ‘Rekh’ blocks form the motif in different colours, while the ‘Datta’ blocks paste the mud onto the parts which don’t have to remain neutral on dyeing.
Fabric : Cotton cloth in its natural grey state and silk are used in this process. The different types of fabrics sourced for block printing are:
Fabric (plain weave with 4 ends in a dent and 2 weft threads picked together):
– Ded Mulmuls (warp and weft counts 100, 30s and 80s)
– Lattha or mill made grey cloth
– Handloom fabrics
– Dosuti sutti fabric (4 ends in a dent and a single weft thread pick, plain woven)
– Maheshwari sarees
– Chanderi sarees
Mordant: Mordents are metallic or mineral salts that enhance or change the color of the dye, when added to the fabric.
Dyes: Natural dyes such as ‘Geru’ as well as synthetic dyes are used.
Wax : Originally, wax that was prepared and boiled overnight was used. The blocks were dipped in wax and pressed onto the areas of the fabric, where the white color of the cloth needed to be retained.
Mud (for Dabu): Used for drying the resist printed areas.
Wood shaving: Traditionally, wood shavings were spread onto the wax printed areas of the cloth, to help the drying process, but they have been replaced with mud.
Harda: Used to bring an off white tint to the white cloth.
Dhawdi flowers: These flowers are used as dye and mixed along with Alizarin.
Alizarin: This is used in the above mentioned process of printing.
Green pomegranate rinds: These are used in the above mentioned process during the printing.
Mej – ‘Mej’ is a long wooden table on which the fabric is placed and block printing is done. Its height is such that it allows the printer to print in a standing position.
Phathiya -This is a small rectangular table of about 1.75m by 1.35 m. Thick layers of coarse jute are spread over the ‘Phathiya’ as base, to absorb any leakage of color while printing. The ‘phathiya’ used for printing the resist paste.
Gadi – ‘Gadi’ is a trolley rack with two shelves made of wood. This movable rack is used for placing the blocks for printing and the printing pastes.
Saj – This is the tray which holds the printing paste. This wooden trough is 30 cm long, 25 cm wide and 7 cm deep. The bottom of the trough has an asbestos sheet.
Katli – Katli is a bamboo or metal mesh which is placed inside the Saj. It serves as a sort of inkpad when the blocks are dipped into the tray.
Tamda – These are copper vessels used for alizarin dyeing. There are two types Tamda depending on the capacity – one which can be used to dye 200 mts of cloth and the other a 100 meters.
Tarseia – This is a huge shallow copper vessel used for cold dyeing. For example, the ‘Naspal’ or ‘Harda’ treatment is done after Alizarin dyeing.
Handi – Vessels used for storing the resist paste. These are shallow, broad-mouthed earthen vessels of different sizes.
Paundi – This is a cement tub used for bleaching and washing purposes.
Measuring tape – For measuring the lengths of raw fabric to be cut.
Brush – Used for cleaning the printing block and ridding it of dried flakes of printing paste.
Dastana – These are gloves used by the dyer to protect his hands from repeated stains.
Blocks – Wooden blocks with required patterns are brought in from Pethapur, Gujarat which has been a source of blocks for many years.
Wooden blocks carved with traditional motifs are used to imprint the fabric in beautiful patterns. The resist dyeing technique is used and the craftsmen also specialize in mud-resist printing. The ‘Gadh’ and ‘Rekh’ blocks form the motif in different colours, while the ‘Datta’ blocks paste the mud onto the parts which don’t have to remain neutral on dyeing.
Preparing the cloth
The fabric is first cut into different lengths as per the requirements of the product being made such as garments and bed sheets. Taking into account the amount of shrinkage the cloth will go through various processes, the craftsmen cut the fabric accordingly. After this the cloth is soaked in water for 16-20 hours. During this step, the yarn swells up and the impurities and starch is removed. After this, the cloth is beaten on stone platforms and strained to remove the excess water.
Mordant application
Mordant are metallic or mineral salts which enhance or change the color of the dye when added to the fabric. When the fabric is immersed in ‘Harda’ solution the fabric changes to a cream yellow color. The harda acts as a mordant for the alum paste and increases the pliability of the fabric, thereby allowing a uniform absorption of printing paste. The fabrics are dried in the sun.
Outlining the fabric or Torna
‘Geru’ or ochre is used on the cloth to make outlines of the design that has to be printed. Two people are involved in the process. Geru color is used to draw guidelines that can be washed away after printing.
Printing or Chhapna
The cloth is spread out on the ‘Mej’ or table. The printing blocks are dipped in the alum paste and their impressions are printed on the fabric. The fabric is then dried in the sun. This step takes one day to complete.
Washing and drying
The process of washing fabric is called ‘Bichalna’ or ‘Pachalna’. In this process the fabric is washed and dried several times.
Alizarin dyeing
The fabric is boiled in ‘Alizarin’ and ‘Dhawdi ka phool’. The ‘Dhawdi’ flower keeps the red color of alizarin from spreading onto the printed alum. After it is boiled, the fabric is taken out and dried, without washing. Once the fabric dries, it is dipped into a solution of gum and water. This enhances the fastness of the color.
Resist printing
Traditionally wax that was prepared and boiled overnight was used. The blocks were dipped in wax and pressed onto the areas of the fabric, where the white color of the cloth needed to be retained. Wood shavings were spread onto the wax printed areas of the cloth. This process is now considered to be laborious and has been replaced with mud-resist paste or ‘Dabu’ which is a better method, as mud takes time to dry. In this technique, mud printed areas are sprinkled with a fine dust made up of thin roots and soil used in growing wheat seedlings. This also increases the adhesive strength of Dabu.
Indigo dyeing
This is a cold dyeing process where the cloth is dipped in a solution of indigo dye. This process takes two minutes for each fabric. When dipped, the cloth turns to a rich green color. When this is exposed to dry air, rapid oxidation takes place and the green color turns to a deep blue shade. The process is repeated till the required shade is achieved.
Resist paste removal
For the fabrics on which mud-resist paste is used, washing continuously with running water removes all the mud. Whereas, wax can be removed only if the fabric is immersed in boiling water, till the wax melts and leaves the fabric. The melted wax, floating in water is reused.
Printing
Sand is spread over the base cloth on the ‘Mej’ or ‘Phatiya’. The Nandana fabric piece is placed over it and the printing is done on the red colored regions with gum and lime paste. Sand is spread over the gum to speed up the drying process.
Nasphal process
Green pomegranate rinds are crushed and boiled to create a solution called ‘Nasphal’. This solution is dabbed over the cloth to change the color of Indigo to a darker shade of green. The fabric is then boiled and left to dry in the sun.
The rock cut caves and temples near Tarapur suggest that the region was inhabited since 2000 BC. The son of Ved Vyasa, 'Suka' had also made a temple of Shiva near Tarapur near the spring of perennial water. The town was established by the settlement of tribal communities living in the vicinity.
The river Gambhiri runs through this region. It has an average elevation of 210 meters above sea level. The closest city to these villages is Neemuch. It involves a bus journey of 7 to 8 kms to reach a town called Jawad, and then a 3 km travel in a bus or auto to reach Neemuch. Small vans operate twice daily to connect Tarapur or Umedpura to the nearby towns and villages.
The villages fall under a sub tropical climate, and the weather is dry almost throughout the year. The summer months span from April to June with temperatures peaking up to 45 degrees Celsius. The monsoons come from July to September, with very sparse rainfall of around 1500 mm. The winters are during the months of October, November, December and January. The maximum temperature at this time would be 25 degrees Celsius and the minimum is as low as 2 degrees Celsius.
The major crops grown in 'Tarapur' and 'Umedpura' are brinjal, cauliflower, tomato and mustard.
The villages receive water supply throughout the year from the river Gambhiri. The villages have a good drainage system and water storage facilities like the wells and tanks.
The banks of the river rich in alluvial deposits provide fertile soil for farming and workspaces for the textile craftsmen. The villages are equipped with basic needs like schools, banks, a market place, medical facilities, training centres, temples and mosques.
Schools equipped to impart education till the 10th standard is present in these villages. For higher education, they go to the schools in the nearby town of Jawad. Small gullies run throughout the dwellings and market places, while a broader road connect the twin villages.
The village gets electricity only for 12 hours a day.
The houses in the village consist of huts, mud dwellings as well as brick/cement houses - both one storied and two storied. The more affluent people live in the two storied houses. There are small gullies connecting all the dwellings. Some houses have cattle sheds. Dotted with small scale provision stores, eateries that serve indigenous snacks and tea, the main road of the village is quite a hub of activities.
The villages have a very strong work culture and an innate contentment. Almost everyone seems to have a house for themselves and put their earnings into bettering their living condition as well as the village. They follow simple living, which is reflected in their food and clothing too. The textile craftsmen now not only depend on the local market but also national and global, thereby boosting the economy.
The joint family system is prevalent. Children start helping out in the family occupation after the age of 12.
The Hindus in the villages are mostly devotees of the Hinglaj Mata, shrines for whom are found in many places. The areas are flecked with many mosques too, showing communal harmony.
There are two annual fairs organized in the villages. One is in the 'Haryali Amavashya' of the Srawan (June - July) month and the other during Baisakh Purnima (April).
The birth anniversary of Saint Namdev (Kartik Sudi Ekadashi), Basant Panchami and the full moon day of every month are holidays for craftsmen. The festivals celebrated with much pomp and gaiety are: Diwali, Holi, Dashera, Sitalashtami, Eid, Tij and Gangour. During the festivals, all the family members wear new clothes and the women are decked in jewelry.
The people in the villages mostly comprise of the Chippas or the Nilgars - printers and dyers. In earlier times, the occupation of the people consisted only of textile crafts - Nandna prints and Bandhani making. Now they have taken up other occupations such as broom making, stitching, grinding mills, factory work, trading etc. Farming and cattle herding is another prominent source of income for the people of Tarapur and Umedpura.
The attire varies among the Hindu and the Muslim communities. The Hindu women wear sarees, the younger ones now wearing Salwar - Kameez or Kurtas. The Muslim women wear long Kurtas with a Churidar and an Odhani covering their head. Jewelry is common amongst the women, the most observed ones being silver kadha (bangles), 'Bali' (earrings) and 'Jhumar' (anklets). The men of both religions wear Dhoti - Kurta or shirts; the Hindu men are seen with a turban called a 'Saapha'. The Saapha is mostly made of Bandhani printed fabric bought from the local markets.
Nandna prints - Block prints with natural dyes bringing out the traditional dainty motifs are a popular attraction of Tarapur and Umedpura.
Bandhani - The textile craft of tie - dye or Bandhani has been practiced in these villages for many years. They have developed a characteristic style, setting them apart from Bandhanis practiced elsewhere.
Sukhanandhji Ashram - This is a popular Shiva temple near the villages. It is situated around 20 kms away from Neemuch, in an ancient rock cave. It boasts of a perennial water spring. The temple is so named because it was believed to be discovered by Suka, the son of the great sage Veda Vyasa.
List of craftsmen.
Team Gaatha
Interview: Master Craftsmen Shri Pursottam Jharia
Interview: Shri Pavan Jharia
Interview Craftsmen community