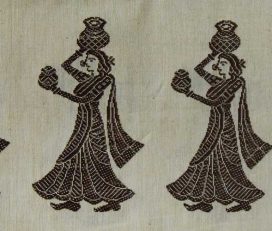
Gollabhama Saree Wea...
The Siddipet Gollabhama Saree is not just a piece of fabric; it is a living tradition, worn, celebrated, and reinterpreted through generations.
Siddipet, Telangana, India...
These handwoven cotton bedspreads and other weaves are products of a self sustained community initiative of the people of Mandsaur, Madhya Pradesh. Formerly only catering to government run establishments, the craft has now stepped out to the open markets through emporiums and exhibitions.
All the requirements of government run institutions or organizations in the state as well as the country are served by this craft cluster. The following products are woven here:
– Bedspreads, sheets and other fabric requirements for hospitals.
– Curtains.
– Binding cloth strips for files in government offices.
– Bedspreads for the railways.
– Towels.
– Fabric for blazers.
The initial designs appeared in checks and lines and in colors which were mellow. These days the designs have also evolved to suit contemporary tastes and brighter colors and variations are also used.
The work happens in commissions where the artisans can purchase the raw materials from government outlets, weave according to specifications given to them and then return with the final finished product. This arrangement aids the craftsmen immensely in not having to worry about procuring raw material of good quality, reliable supply source and the price fluctuations. The craftsmen are able to completely concentrate on the finish and quality of the product. Most of the craftsmen are women working from the looms in their homes. The men help in the subsidiary activities.
In the year of 1946 AD, like in many parts of India, unemployment was rampant in Mandsaur. So, the local community influenced by Mahatma Gandhi’s Khadi movement proposed setting up of hand looms in the cluster, thereby providing employment to the local masses. The cluster ever since has been thriving on weaving cotton for various government uses.
Khilchipura was a small weaving cluster, during India’s independence; Khadi was introduced in 1920 as a political weapon and as the best instrument for giving concrete expression to the Swadeshi Spirit to boycott foreign goods. Khadi rendered an opportunity to every man, woman and child to cultivate self discipline and self sacrifice as a part of the non cooperation movement.
“I have only one message to give and that concerns khadi. Place khadi in my hands and I shall place Swaraj in yours. The uplift of the Antyajas (the untouchables) is also covered by khadi and even Hindu- Muslim unity will live through it. It is also a great instrument of peace. This does not mean that I do not favor boycott of Councils and law-courts, but in order that people may not have a grievance against those who go to them, I desire that the people should carry on work concerning khadi even with the help of lawyers and members of legislatures. Keep the Moderates highly pleased; cultivate love and friendship for them. Once they become fearless, that very moment they will become one with us. The same holds good also for Englishmen.”
(Gandhi ji In an interview to Indulal Yagnik, which was published in Navajivan on 19-3-1922; 23:86-87)
Inspired from Gandhi’s Swadeshi ideologies, this mutually beneficial tie-up of the government and the craftsmen took shape. In 1946 the village set up a cooperative and has been weaving table and bed linen, towels, fabric for blazers and other clothes. Most of the craftsmen are women, who weave from the looms in their homes.
“A woman is adorable, not for the jewelry she wears, but for the purity of her heart. I therefore urge you, if you believe that khadi will solve all the distress of India, to a certain extent, to part with the money that you have brought and your jewelry also, if you can give it to the cause. If you will go a step further, I would ask you also to spare some time to turn the spinning- wheel. It is a fine occupation for women in their leisure hours and it would be much better for you to pass your time in this useful occupation than idle talk. Now, you will give what you can to the volunteers who will go in your midst.”
(Gandhi ji’s Speech at women’s meeting in Trichinopoly on 20-9-1927; 35:11.)
The Madhya Pradesh Hastshilp or the Hathkargha Vikas Nigam Ltd has been working tirelessly over the years to provide craftsmen of the state with the tools to continue practicing with profit and dignity. The Nigam has established several Craft Development Centers and Common Facility Centers across Madhya Pradesh. It has initiated meticulous surveys and documentation of the various handicrafts being practiced in the state. To keep in tune with the changing times and modern tastes, the Nigam also provides skill-trainings, product designing and diversification programmes. It has also been actively supporting the artisans of the state through participation in various national and international exhibitions. Now, about 600 craftsmen work in this organization, often involving designers to help the artisans incorporate changing trends into their designs. The Corporation provides them with the raw material and also buys the manufactured products from them. The hand-woven articles are becoming increasingly popular as mill made products are now losing business to these villagers. In 1999-2000 the village sold goods worth Rs20 – 30 lakh. Khilchipura is becoming famous as the ‘village of charkhas’, when hand spinning on charkhas is almost extinct or has now become obsolete in other parts of the country.
With the intervention of involving designers and the craftsmen’s explorations, the designs have become more minimal and contemporary, with geometric patterns and a color scheme spanning bright and pastel colors. But the older patterns are still in demand, which are mostly checks and lines in a body of muddy colors.
The hand woven textiles are facing the same challenges which were being faced in 1940’s, during Khadi revolution. The emergence of mechanized mills has pushed the handloom industry in oblivion. The cost of fabric produced industrially is far cheaper and it thus creates an unjust competition for hand-woven textiles. There is a need to generate awareness among people about the age-old craft of hand spinning and weaving, not just for the skill to live but also because there are still many people dependent on it for their livelihood.
The dyed cotton yarn is woven using the traditional fly shuttle loom, mostly in the weavers’ homes. The varieties of products are woven as per requirement and innovation.
The raw materials sourced from National Handloom Development Corporation are as follows:
– Cotton yarn – 2/40s, 2/20s, 20s counts.
– Chemical dyes – from Ujjain.
– Polyester yarn – PV 26s 8NM count.
– Fly-shuttle traditional loom: The whole loom rests on a frame of four vertical posts. In this loom, the sleigh carries a race board and two shuttle boxes, one on either side. The weft yarn is wound onto a bobbin, which is put in a shuttle. This is placed in one of the shuttle boxes on either side.
– Taana Machine
– Charkha or the spinning wheel
– Shuttles
– Shuttle Box
– Gittas or small reels around which threads are wound.
– Fly Shuttle Loom
The dyed cotton yarn is woven using the traditional fly shuttle loom, mostly in the weavers’ homes. The varieties of products are woven as per requirement and innovation.
Design :The organizations usually provide the designs to these weavers, if something different from the traditional work is expected out of them. The master weaver refers to the required design, to prepare the warp and the ‘Raach’ (the vertical comb-like wires through which the warp yarn passes).
Dyeing : Color selection for dyeing the unbleached cotton threads depends on the colors present in the design. The dyeing process is usually given out to specialists called ‘Rangrez’. Two basic types of dyes are commonly used for durries: Direct dyes and Vat dyes. Direct dyes are cheaper and are not colorfast. Mostly direct dyes are used for making fly shuttle durries. As they bleed on washing, retail houses recommend dry cleaning for these durries. For dyeing, the yarn is stocked in the form of loose bundles knotted at the center. These are put in a tank (usually a rectangular container of size 5 x 4 x 4 ft) that contains boiling water, to which the desired color of dye is added. The yarn is kept dipped for about 10 minutes and then taken out and dried. This process is repeated again to give the yarn lot a uniform color.
Yarn Opening for Weft
The dyed cotton threads come to the weaver in the form of bundles. This form of yarn needs to be stretched and reeled to make it free from tangles. This is done on the Charkha. The loose bundle of yarn is put over the larger wheel of the charkha and the other end of the thread is tied to a small reel called Gitta, which effectively works as the smaller wheel of the Charkha. The Gitta is then wheeled, so the yarn is pulled from the larger wheel to the Gitta. This form of the yarn is tighter, uniform and tangle free.
Warping : The master weaver now prepares the ‘Rula’ (log) with the warp, to be used by the weaver to make the Durries. For this purpose he uses a Taana or warping machine. A Taana machine is a much larger version of the Charkha principle. The thread rolls or Gittas are put on the vertical frame of the warping machine. This is a movable frame that resembles an abacus. The ends of the thread are taken from the rolls, passed through another, smaller, grid like frame, with vertical metal wires that guides the thread and are wound on the big wooden cylinder of the machine. This process starts from one end of the big octagonal cylinder and goes on till the entire cylinder is covered with yarn.
The craftsman uses a special visual measurement scale that consists of a spring with a small weight hung over it. The small weight slides over the spring, covering one coil of the spring with every revolution that the wooden cylinder takes. Normally, the entire length of the spring scale can take 50 revolutions of the wooden cylinder. Once the desired length of yarn is wound around the cylinder, the log upon which the Taana is to be wound is fitted into the blocks between the cylinder and the frame. Then the craftsman puts a heavy weight across the cylinder. This is tied to the end of a rubber tube at one end of the wooden cylinder. The tube rests over the circumference of the wheel. This is done so that when the thread is pulled over the Rula log, it comes over the Rula in a very tight fashion. The tightly wound yarn on this log is then provided to the weaver, who uses it for the warp on the loom frame.
Weaving: As mentioned, fly shuttle durries are commonly woven on the pit loom. The weaver sits at ground level and his legs rest inside a pit that contains the pedals. For weaving, the warp from the Rula (log) is bound on the two beams of the loom. It loops over another log called Kharag. The warp is then guided in two layers by a flat vertical metallic reed till it reaches the Hattha (the moveable frame used to beat the weft, which also carries the fly shuttle reel). The reed is a comb-like structure of metal wires. It maintains the distance between the individual warp threads. The design of the reed (Raach) frame varies with each design and is made by an outside specialist. Making the correct Raach is very important to get the weave as desired. For plain durries, the loom has two frames, but the number of frames can go up to a maximum of four depending on the complexity of the design.
The weaver uses the beater (Hattha) to push back the loose thread that tails the shuttle into the system of weft threads. As the weaving progresses, he adjusts the tension of the warp using the tightening screws on the two loom beams.
The only waste generated by this craft is left out cut yarn.
Mandsaur was earlier called Marhsaur. The name was derived from names of two places 'Marh' and 'Saur', which might have been merged to form this town. It was also said to be called Dashapura, when it was ruled by the Dasharnas during the Mahabharata period. Bandhuvarma was one of the rulers of this dynasty, who appears in an inscription at Mandsaur. It is said that the silk workers of Mandsaur had constructed a Sun temple here, it was repaired by Bandhuvarma in Samvat 493 (436 CE).
The Risthal stone slab inscription discovered in 1983 has brought to light the Aulikara dynasty, which succeeded the Dashapura dynasty. Two monolithic pillars were erected in a small village called Sondani (4 km from Mandsaur) by a king called Yashodharman of this dynasty in 528 AD. These described his exploits and achievements. The Indian Archaeology Department records that these were excavated from the original site in Sondani.
Before Independence in 1947, Mandsaur was a part of the princely state of Gwalior. It lent its name to the treaty made with the Holkar Maharaja of Indore, which helped put an end to the Third Anglo-Maratha War and the Pindari War in 1818. Later as it neared the 20th century, it became a thriving centre for the Malwa opium trade.
Mandsaur District forms the northern projection of Madhya Pradesh from its western Division, the Ujjain Commissioner's Division. It lies between the parallels of latitude 230 45' 50" North and 250 2' 55" North, and between the meridians of longitude 740 42' 30" East and 750 50' 20" East.
The District is bound by two Districts namely Neemuch in the North-West and Ratlam District of Madhya Pradesh in the South. The District is an average sized district of Madhya Pradesh. It extends for about 142 km. from North to South and 124 km. from East to West. The total area is 5521 sq. km.
The climate of this district is generally dry except under South-West Monsoons. Year may be divided into four seasons. The cold season is from December to February. This is followed by the hot season from March to the middle of June. Thereafter the South West monsoon season starts and continues till about the middle of September. In District there is a rapid increase in temperatures after February. May is generally the hottest month with the mean daily maximum temperature at 39.80 C and the mean daily minimum at 25.40 C. Days are intensely hot in summer and hot dust-laden winds which below during this season add to the discomfort. On individual days in the summer session and in June before the onset of the monsoon the day temperatures often go up above 450 C. January is the coldest month with the mean daily maximum temperature of 35.00 C and mean daily minimum of 9.30 C.
The average annual rainfall in the District is 786.6 mm. The rainfall in the Districts in the region around Sitamau - Mandsaur - Malhargarh in general increases in the northern part of the District from the West towards the East.
Mandsaur is a developed town with thriving industries of slate pencil, flour and opium. It is equipped with all the basic facilities like schools and colleges (both govt. and private), medical facilities, electricity etc. Mandsaur district falls under the Ganga basin and Chambal River sub-basins. The river is situated in a broad, flat, shallow valley with low gradient because the Chambal has reached the base level of erosion. Vertical erosion has reached and lateral erosion is taking place. Other tributaries of Chambal River are Retam, Shivna and Chhoti Kali Sindh. Mandsaur district has limited irrigation facilities. Only 28.64% of net sown area is irrigated and rest of the area is rain-fed. Surface water irrigation in the district is only 8.0 % of the net sown area. Groundwater is the main source of water in the district.
The architecture of Mandsaur is that of any bustling town. It has caught up to its brick and concrete counterparts in both dwellings and commercial buildings. It is steeped in archaeological eminence. The homes of the craftsmen are built around their crafts. The humble brick and tile dwellings have their work spaces right at the entrance.
Malvi is the language mostly spoken in Mandsaur. It is a mix of Rajasthani and Hindi. The place is rich in archaeological and cultural history. Nevertheless, Mandsaur is popularly known for its temple of Lord Pashupatinath, located on the bank of River Shivna. Its idol has a parallel only in Nepal.
Most of the people in Mandsaur are Hindus. There are, however, sizeable minorities of Muslims, Jains, Christians and Buddhists. There is also a small Sikh population. Hindi language is the main language. Dialects of the language, such as Bundelkhandi, Malwi and Chhattisgarhi are found to be spoken too. Agriculture is the main occupation. The others include trading and crafts. Many people from the tribal background are nowadays found to be working as workers in factories, as shopkeepers or as street hawkers.
Majority of the male community wears dhotis along with Bandi (a kind of jacket) and a turban. Most of their clothes are very colorful. The women wear Lehenga (long skirt) and Choli (blouse) with an Odhni or Lugra (cloth wrapped around their head and waists). They also wear saris.
Mandsaur is famous for the Pashupatinath temple with its eight-faced Shivling. Hoards of devotees flock to the temple for the 'Mela' or fair held in this temple. The water in the Shivna River swells every monsoon and touches the bottom of the Shivling. This is termed 'Jalaabhishek' (Offerings of water) and is celebrated with great reverence. The Nalcha Mata temple, 3kms from Pashupatinath temple, is another site of religious importance.
A famous historical spot here is the Mandsaur fort. It was built during the Dashapur dynasty and is also called the Dashpur fort.
Mandsaur is famous for its Opium production. The slate pencil industry is a prospering business here. Culinarily, Mandsaur is famous for its distinctive Dal Baafla(a dish comprising of lentils and wheat) and Kachori (fried hollow flour patties with lentil stuffing).
List of craftsmen.
Team Gaatha