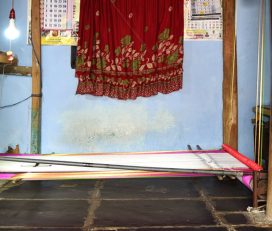
Saree weaving ~ Amar...
The place is renowned for its exquisite pure silk sarees adorned with intricate zari work. Skilled artisans here are masters of weaving elaborate jaala patterns...
Amarchinta, Telangana, India...
The Khatri community has been closely associated with the production of Ajrakh print. However, the Maldhari pastoral community is traditionally associated with wearing the print.
Ajrakh is said to have drawn its name from the Sanskrit word ‘A-jharat‘, meaning ‘that which does not fade’. ‘Azrak‘, the Arabic word for blue could have also played a role in Ajrakh’s etymology.
The prominent theme behind ajrakh is the sky as its theme and is represented by the colour blue, evening by the colour red and night by black. The white star-like motifs represent stars.
The famous traditional designs associated with the print is Champakali, Raiya, Kharek, Nipad, Grinari. However, as always, craftsmen offer their own subtle deviations from these to depict Amlaliya, Jalebiya and the famous Kakkar pattern. ‘Saudagiri patterns’ in Ajrakh are the most highly documented genre. These are done with smaller grids. They consist of more organic motifs within a symmetrical lattice. Riyal patterns are designs in Ajrakh, which are built around circular motifs and block prints as well.
Ajrakh is a craft that is said to exist in harmony with nature, this is due to natural processes and ingredients involved in the making. Although the making is a water-intensive process, at every step, water is reused until it's saturated with dye and then is released to water the fields in a parched land. Thus, usage is a circular process that conserves natural resources. Besides, Ajrakh is also among the crafts that are made in specific seasons. All of this contributes to this being a part of what is known as sustainable clothing.
The partition of the country had an important effect on separating craft clusters. Initially, based out of Dhamadka village in Bhuj, following the earthquake the community also shifted Ajrakhpur, 12kms away from Bhuj.
Following Islamic principles neither humans nor animal figures appear in ajrakh prints.
The fabric is traditionally worn by both; the members of the royal court and the pastoral Maldhari community (6). Vibrantly printed cotton fabric is comfortable for their work, nomadic lives, and the temperatures they encounter. It is both a delight to the eye and the skin.
The men use it as cummerbunds, colorful lungis (6) (garment to be draped around the waist, covering the lower body), wrap it around their heads like turbans, or toss (4) it across their shoulders as scarves. The women drape this fabric as dupattas (5) (a long scarf), chaddar (head covering or veil), and as shawls. Ajrakh printed skirts are also commonly seen in women. The semi-nomadic Maldharis also use the fabric as ‘bindles‘ (6), in which they bundle up a few belongings while traveling.
The vibrant colors (1) make it very endearing to use it as linings in cradles for kids. The fabric is used both in daily necessities as well as on special occasions. These differences are decided by the quality of the fabric. Patterns, color, and quality of cloth are used as markers for importance and hierarchy.
Its historical importance and intricacy of the design lend its great importance and therefore the fabric is also used as honorary gifts. The general uses also spill over to bed covers and hammocks.
The beauty of the fabric does not fade even if it gets old. The fabric is even used in patchwork quilts when it ages.
What makes Ajrakh a treasured possession is the fact that its qualities do not just stop at the beautifully detailed patterns (3). The elaborate and painstaking process boasts of ingredients that are all natural and environment friendly (2-4). The fabrics go through many stages of resist dyeing for the different colours. They are washed in flowing river water, the quality of which also influences the hues. These processes lend depth to the design, enabling the dyes to ooze into the warp and weft of the fabric. Thus making the fabric blush with deep hues and great tensile strength. With a fabric that has been treated to subtle down its texture and increase its durability, it can be used and reused till it becomes threadbare.
Ajrakh prints are worn across all strata of society and status, with the same patterns and principles but different qualities of fabric. Predominant use of indigo and red in dyes lends it the ability to keep the wearer warm in winters and cool in summers.
Ajrakh is said to have drawn it’s name from the sanskrit word ‘A-jharat‘, meaning ‘that which does not fade’. ‘Azrak‘, the Arabic word for blue could have also played a role in Ajrakh’s etymology.
There is a well-known anecdote about Ajrakh. There was once an opulent King of Sindh. Like the other royal luxuries he enjoyed, he insisted about sleeping on a new bed sheet every day. One morning when the servant was about to change the sheets, the King commanded him not to take away the beautiful blue block printed sheet. “Aaj ke din rakh” (Keep it for the day), said the smitten King. It is believed that this enamored line of the King is what gave this magnificent fabric its name. It must have been a beautiful sleep for the King, to feel like he was sprawled on the changing sky, amongst twinkling stars, when he slept on Ajrakh.
There are also stories related to the craftsmen and their techniques. Like the story of how “Khatri”, used to determine the quality of the red color he wanted in the dye by tasting it. Just like how the ingredients of a well-cooked dish are tested, he would taste a bit of the dye and make his decisions based on the amount of alum he could taste. The reason behind this was that, for natural dyes great care has to be taken in getting the proportions right and this can only be instinctively determined by the craftsmen. Development of a great sense of judgment was also to a great extent an outcome of unavailability of measuring devices. It is their sixth sense and well-trained eye that replaces the most accurate of the devices to reduces risks.
The craft of Ajrakh was born in Sindh and is believed to have been in existence from as far back as 3000 BC. The fabrics unearthed at sites like Fustat (4) in Egypt are believed to be this Indian fabric (1). The Gujarati port of Bharuch appears in the records of the Greek geographer Strabo (63 BC- AD 20) as ‘Barygaza’ from where a variety of Indian textiles were exported to the west. The craft was mastered by the civilizations, which flourished around the Indus River in Sindh area. The river provided both a site for washing cloth and the water needed to grow Indigo. The bust of a King Priest, excavated at a site in Mohenjedaro, shows him draped in this fabric (1), which depicts the earliest use of Ajrakh. It had a trefoil pattern printed on the garment believed to be the ‘Kakkar‘ or cloud pattern in Ajrakh printing. Similar geometry of the trefoil is evident in the present Ajrakh patterns.
Panini, the sankrit grammarian of 6th century BC, has also written about fabrics resembling Ajrakh. He has described names of clothes known by the colours in which they are dyed. ‘Nila’ – cloth dyed in Indigo, ‘Lohitaka’ was a cloth dyed red, ‘Laksha’ was Madar-dyed cloth and ‘Kalaka’ was the black cloth.
These facts establish the antiquity of the craft form. They testify that, the complex technology of mordant dyeing has been mastered in the subcontinent for centuries.
Legend says that Ajrakh printers were descendants of Rama’s sons Lava and Kusha. They came to Kutch from Sindh around 400 years ago. Rao Bharmalji (5), the ruler of Kutch (1586-1631), invited the craftsmen to Kutch to meet the growing needs of the people and the royal court. This also helped in developing overseas trade of textiles. The king gifted them land and they were free to choose where they wanted to build their homes. They were also exempted from taxes. They chose the banks of River Saran since it was a good source of saline water and alum which are advantageous in dyeing. They knew that a good supply of running water is necessary for different stages of washing and dyeing cloth.
The Khatris soon converted to Islam in the 1660s and settled in Dhamadka during the rule of Rao Bharmalji. He had established a mutually beneficial relationship with the Mughal ruler Jehangir, which lent a peaceful environment in Kutch and enabled the craft and its trade to flourish. This calm and stability allowed the Khatris to establish trading relations with the communities who became their local customers, the Maldharis and Rabaris.
The craft survived in full bloom till it wilted during industrial revolution, after independence in 1947AD. Synthetic chemicals and fabrics like polyester eclipsed Ajrakh. The traditional crafts dwindled drastically till steps were taken to revive it in the 1960s by key figures like Kamaladevi Chattopadhyay. Nevertheless, it was not until the 1970s that the State Craft Organization emerged to save the crafts that were in jeopardy. The Gujarat State Handicraft Developent Corporate and its retail wing Gurjari were established in the early 1970s. The aim was to uphold the craft and create a sustainable market. At around the same time, the National Institute of Design was established in Ahmedabad. Designers were recruited from NID to work with the Handricraft Development Corporation staff and the craftsmen from rural areas of Gujarat. Thus the crafts slowly grew into full bloom with more and more people being aware and the markets expanded from domestic customers to overseas too.
The partition of India had earlier separated the craft clusters. The shift to Dhamadka was soon affected when there were severe earthquakes. These earthquakes changed the quality of the river water by shift in the tectonic plates and rendered it unfit for the craft. The craftsmen then shifted to Ajrakhpur, 12kms away from Bhuj (3)and are now diligently creating this beautiful fabric from there.
Ajrakh is believed to have the sky as its theme. The sky is represented by the colour blue, evening by the colour red and night by black. The white star-like motifs represent stars.
Ajrakh designs appear similar to kaleidoscopic patterns. The cloth used is usually about 3-5 meters long. It is patterned with intense jewel-like colors. The symmetrical block prints transfer their patterns onto fabric mainly in deep crimson and indigo. These patterns are peppered with imprinted, sparkling white motifs. Following Islamic design principles, they do not depict human or animal figures.
This is a craft in which geometry steps in to render a divinely metaphoric quality to the design. It helps the smaller patterns transcend into a harmonious whole. A central Jaal (web-like design) is created within a grid by repeating the block print patterns. This grid becomes the base framework for the printer to expand or constrict the design. Border patterns, both horizontal and vertical, frame this central design. These separate one pattern from another. The longer laterals are printed with double margin borders.
Champakali, Raiya, Kharek, Nipad, Grinari etc are the famous traditional designs. Skilled craftsmen subtly deviate from these to variations such as Amlaliya, Jalebiya and the famous Kakkar pattern. ‘Saudagiri patterns’ in Ajrakh are the most highly documented genre. These are done with smaller grids. They consist of more organic motifs within a symmetrical lattice. Riyal patterns are designs in Ajrakh, which are built around circular motifs. Ajrakh prints also embrace new block patterns these days. They are customized designs handed in by stores or designers.
When the Ajrakh printing is applied to only one side of the cloth it is called Ekpuri. A double sided print would be called Bipuri. Very few block printers still posses the skill to produce a natural dyed Bipuri Ajrakh, which is a delight to the eye.
The massive 2001 earthquake in Gujarat caused immense damage not only to life and property, but also to the environment. The iron content of the river Saran had increased, rendering it unfit for Ajrakh printing. Only a few craftsmen decided to stay behind in Dhamadka while the rest moved to a new place. This place was closer to Bhuj and the water was more suitable. They built a village there and it came to be known as Ajrakhpur. The craftsmen understand the value of water for the craft, and have built a water-harvesting plant in the village in collaboration with the government; thereby setting an example for others to follow.
Due to the fast growing industries and their lucrative job opportunities, the traditional craftsmen and their descendants are slowly shifting to alternative employment. Most of the craftsmen are not able to make a living out of just the handicraft. Jaya Jaitley puts the plight of the craftsmen in her book ‘ViÅ›vakarmÄ’s Children: Stories of India’s Craftspeople’ (published in 2001) in this manner –
‘Yet despite their long history and plethora of plans and schemes evolved for them by various governments since India’s independence, there may be no more than a few thousand crafts people who are comfortably placed both socially and economically. The rest eke out their livelihoods at bare subsistence level'(sic).
Ajrakh is one of the very few crafts whose visiblity has considerably increased and has reached even outside India. Catering to foreign clients, the change in design sensibilities and awareness also creates changes in workflow. There is a demand for innovations in traditional designs and more solid colours. For example, traditional Ajrakh designs are intricate and do not need large expanses of solid colours. Thus when the cloth is dyed to attain one colour over a larger area, it tends to become blotchy. Nevertheless, the craftsmen soon came up with spraying mechanisms to overcome this. There are other difficulties when catering to the foreign market. The craftsmen find it hard to keep up to the demands and make the clients understand that the production cannot happen throughout the year. The craft cannot be carried out in the rainy season since the dyes are affected by the humidity. Since most of the work happens outdoors, these are pivotal in determining its quality. Therefore, understanding of the craft season and being sensitive to the process are very important aspects while spreading awareness.
Ajrakh is an intensely time consuming craft that uses the technique of resist printing to bring some of the most exuberant patterns of Islamic origin to life. It involves upto sixteen steps of manual processing and only uses natural and eco-friendly raw materials.
Blocks (1) ~ They are made from teak wood. Carving happens during rainy season, as humid air is not good for printing and dyeing work. The blocks that are meant to create fine dotted patterns are made with brass pins on the wooden surface, as the metal is strong and non reactive to the dyes. It takes 2 days to make a block if the design is simple. Finer and more intricate designs take 12-15 days. The blocks are made in Pethapur, near Gandhinagar.
From the seasoned wood, a block is cut to the required size and sanded on a stone to get a leveled plane surface, which is then checked against the edge of a steel ruler. The surface of the block is dipped in water and then in ‘wari’ (dry, powdered clay) and rubbed against ‘rohi’ (granite). With the friction, a whitish layer is formed on the surface of the block. The patterns are drawn or printed to scale on paper. This paper is stuck onto the plane wooden surface. The craftsmen then use their expertise and various tools to carve out the patterns. This results in flawlessly accurate wooden blocks.
Fabric (3) ~Ajrakh prints are being carried out on a variety of fabrics, these fabrics come from the following places: Cotton – Erode in Tamil Nadu, Mulmul – Mumbai, Silk – Ahmedabad and Surat, Handloom cloth – Maheshwar (MP)
Printing equipment ~ The fabrics are hand printed on long tables. The wooden blocks are dipped into trays (2) containing mixed colour and then pressed onto the fabric.
The block is not dipped directly into the dye liquid. A thin layer of coarse cotton is soaked in the dye. This is then used as a pad from which the dye is transferred to the block. In this manner the dye spreads evenly on the block and does not drip.
The table has layers of jute fabric covered with cotton cloth. If the base fabric for printing is cotton, it does not need to be pinned to the table, as the texture of the fabric is coarse enough to hold on to the table with its own friction. Silk needs to be pinned on due to its slippery smoothness.
Dyes ~ Water tanks are kept in the open courtyard to store the ingredients. Wood is used to fire the stove for boiling the dye. Natural vegetable dyes like Indigo, Turmeric seed (7), Lime and rice are used to colour the fabric and are mostly acquired from Rajasthan or made in-house. Very few are obtained from outside. Alizarine is acquired from Bihar / Bengal, Madder from Rajasthan, natural indigo from Andhra Pradesh (only one person makes it now) and Logwood from Holland. Other natural products used in the process are gums, oil, clay lime, sakun seeds and molasses.
Drying ~ Dyed wet fabric is laid out on the ground to sundry. Heavy pieces of stone are used to hold it down to the ground.
The tools required for various processes in Ajrakh are traditionally handmade. The materials used to prepare these tools are mainly wood and clay and are made by the women after their household chores.
The equipments made of wood are the Blocks, Danda (stirrer), Ghod (wooden stand), printing table (2) and the Budho (wooden beater). Equipments like Indigo-maat (dyeing tank), Kundi (tank for Harda treatment) and Tari (trey) are made from clay. Nowadays, plastic barrels and discarded paint buckets are re-used. Rangchul (5) (tank for dyeing) is made of bricks and cow dung. The pot inside the Rangchul is called Charu (3) and is made of Aluminum.
This craft requires lots of running water in many stages. The craftsmen value this water, which is suitable and important for the craft. Therefore, there is a need to use it wisely and conserve it. The craftsmen at Ajrakhpur have devised their own technology as a replacement for the running river water, since they moved away from the banks of river Saran. A system of huge concrete stepped tanks (6) has been installed in the village. The tank consists of various descending levels. The fabric is washed on each level in its different stages. This enables running water as well as the water from one stage to be reused in the next.
This craft is deeply revered in Sindh and embraces every significant event in the life cycle, from birth to marriage and even death.
Ajrakh is an intensely time consuming craft that uses the technique of resist printing to bring some of the most exuberant patterns of Islamic origin to life. It involves upto sixteen steps of manual processing and only uses natural and eco-friendly raw materials.
1. Saaj no Marhalo : First, the fabric is washed in plain water and beaten to remove all the impurities. The traditional procedure for this is to soak the fabric in soda ash, castor oil and then in camel dung solution, which acts as a bleaching agent (alkaline) and makes the fabric soft. Nowadays, the fabrics are washed in plain water at the riverbanks or specially constructed water tanks. The fabric is dipped in water and then beaten with a wooden beater in order to soften it. The fabric, if required, is also steamed in water containing soda ash. Excess water is wrung out of the fabric and laid flat on the ground surface to dry in sun.
2. Kasanu/Harda treatment: The next stage consists of treating the fabric with Harda (myrobalan). The cloth at this stage is treated in the same manner as it was done traditionally. This particular treatment is given to the fabric in order to facilitate better process of printing later. This is done by soaking the fabric in Harda solution, pounding the fabric with the feet, removing from the solution, drying and beating the dried fabric to dust off extra Harda powder.
3. Rekh (outline) printing (2): Gum Arabic and lime are mixed for ‘kiryana‘ (printing of the white outlines). Blocks (also called rekh) are dipped in the solution and pressed onto the fabric to print the white outlines over it.
4. Drying of rekh printed fabric: After printing the fabric with rekh (outlines), the fabric is dried in sun and if it is to be printed on both the sides, the fabric is reversed and reprinted with the same set of blocks, matching the motifs manually and then gain left to dry.
5. Kat (black) printing: A mixture of Gum, ferrous sulphate, fuller’s earth and water are used to make the black outlines. These ingredients were traditionally used but today, the process of ‘kat’ printing is carried out using rust of scrap iron, ‘kachuka-no-loat’ (tamarind seeds powder) and ‘gud’ (jaggery) to make the paste. These ‘kat’ printed areas turn permanently black in colour on treatment with indigo.
6. Phulli/Kan printing (1): This is the process of resisting of small star like areas. ‘Kachuka-no-loat’ (tamarind seeds powder) is mixed in alum and then boiled for 1 hr to produce a thick printing paste. To this, some amount of fugitive dye, ‘kesari rang’, is added to separate this paste from the other printed resist pastes. Traditionally, ‘Geru’ was used instead of fugitive dye. The fabric is now stamped with this paste.
7. Gach/ Khor printing: The first part of this stage is called ‘Khor’ printing, where the resist is prepared with a paste of alum, gum-arabic, millet flour and red clay and is stamped on the fabric with the help of filler-block (Gadh). The later step of this stage includes the stamping of resist paste made of lime and gum-arabic. These two combined steps are called ‘Gach’ printing. On this resist printed fabric, before drying up, dry powdered ‘Bakri-ni-lindi’ (Goat excreta) is sprinkled, which prevents the smudging of design. Nowadays, wood powder is used.
8. Indigo dyeing I (7): Natural indigo, extracted from the plant leaves is used for the purpose. A ‘V’ shaped well called ‘Naand’, dug in the ground is used for dyeing. The indigo along with ‘kuwadia-na-beej’ (casatoria seeds) is added in ‘Naand’ containing water and is left for months to ferment (this brings out the iconic blue of the indigo). Then, the fabric is dyed in it for 10-15 min. These days due to very limited supplies of natural Indigo, the synthetic indigo color is widely being used. It mixed with sodium hydrosulfide and caustic soda in the ‘maat’ (clay container) containing water. The ‘maat’ is left to mature for 3-4 days. The fabric is then added to this solution and dyed for 10-15 min. and then dried in sun.
9. Vichharnu (8): The indigo dyed fabric is washed in running water and laid flat to dry in sun. Fabric is not vigorously rubbed and the ‘khor’ resist is not removed yet and hence the resultant fabric remains stiff.
10. Rang: For this step, the cloth is boiled with ‘dhaori-na-phool’ (galls of tamarisk) and ‘majith’ (madder) with sufficient amount of water in the ‘rangchul’ (metal container fixed on a stand) for 2-3 hrs. The fabric is then washed in running water (9) and dried in sun.
Steps 7 to 10 are repeated once again to get brighter and more brilliant shades of red and blue.
The process involves printing, dying, washing and re-printing twenty or more times. A lot of water gets used till the fabric reaches its final printed stage. Measures are being taken to reuse and reduce the clean water consumption. Other wastage includes the organic remains after the natural color is extracted, which is biodegradable.
Their name means 'one who fills or changes colours'.
The Khatris of Kutch, in the words of the natives, are originally "the Kshatriya Brahmins from Sindh, 'Khatri' being derived from 'Kshitriya'. The King of Kutch had once invited them to settle down in his land. They were called to practice and teach their craft, to make interesting prints and therefore attire for the royal court and the people of Kutch. During the rule of Rao Raydhanji (1666-1698), the tax laws were very strict. As Hindus they needed to hand in a lot of money and gifts to please the 'Baats', who maintained the statistics of their births, marriages and deaths. The demands for these gifts kept increasing over time. If their names were not recorded in the books of 'family and lineage', then arranging a marriage in the community was very difficult. At the same time there were Sufi saints in the village who propagated Islam as a much lenient religion. With the absence of caste hierarchy, Islam came as a relief to the suppressed cast and they soon converted. It's the ninth generation of Khatris and their children today carrying on the craft tradition from the village of Dhamadka. When the Bhuj earthquake happened in 2001, the iron content in the water went up due to shifting of the tectonic plates, making it unsuitable for Ajrak printing. So, they moved to a new village and named it Ajrakhpur.
Ajrakhpur is about 12 kms from Bhuj, located along National highway 42. It is the main centre for Ajrakh printed fabrics.
Apart from Ajrakhpur, Ajrakh printing is done all over Sindh, especially in Matiari, Hala, Bhit Shah, Moro, Sukkur, Kandyaro, Hyderabad and many cities of Upper Sindh and Lower Sindh.
The weather is dry and tends to go to the extremes during summers and winters both. The rainfall is scanty and it rains around the months of July and August. During the rainy months, the printing and dying process takes a halt owing to the humidity, which affects the outcome badly.
The village is characterized by vast stretches of drying fabric, stained vats of dye and multi-hued water found in every house compound. The population is less and mostly every man in the family practices the craft. Printers or dyers at work are the usual sights. Subsidiary activities like washing, drying, preparing dyes, food, cattle also revolve around the workshops.
Ajrakhpur is a small village created and resided by the Ajrakh craftsmen, the main occupation of the people being block printing and natural dying. The houses as well as the facilities required to carry out the craft have been constructed by the community themselves. The village has a school made by the Rajiv Gandhi Foundation. There is a mosque for daily prayers and occasional gatherings. A common concrete washing tank for the fabrics is a priced possession. They value the water, which aids them in their craft, and use it with care. For this purpose, they also have rainwater harvesting demonstration plant. The village has electricity and water supply pipelines but they still use the bore wells and water tanks. Its a self sufficient and well connected village, with its proximity to the highway and other cities to get the supplies. For a daily munch or small needs there are four general shops along with a bunch of men eager to exchange a few words. A push-cart with knick-knacks can be expected to arrive anytime.
The village as compared to the other craft settlements is new, since they shifted from Dhamadka only in 2001. The houses and buildings of Ajrakhpur do not match the antiquity of the craft owing to their new and very need based, economic construction. The structures are modern and to-the-point, made with bricks and concrete. They have colonies of small blockhouses often separated by vast empty land used for drying etc.
The inhabitants of the village are predominantly Muslims. Eid is the main festival celebrated with much aplomb. This is one of the very few times they take a break from their work and celebrate. Celebration usually means group picnics to the field where arrangements for night stay and barbeque have been already made. Swings on the branches of huge mango trees are installed and cool breeze blows across the open fields unhindered.
The craftsmen will be working away amidst blocks, stretches of fabric and dyes most of the year. On January 26th of every year, they clear the village accounts and select a new person for keeping the accounts for the next year. Though television and cable have reached Ajrakhpur, the primary recreational activity for them is catching up for chitchat. The children however spend their energies on lots of after-school cricket. Women of the village spend most of their time looking after the household matters, children and food being their primary focus.
Ajrakhpur was established by Khatri community, who migrated from Dhamadka village after the earth quake of 2001. Even now the village is majorly inhabited by them. The primary occupation of the community is fabric dyeing and printing. All the major festival of Islam is celebrated with fervor. Men from Khatri community have a well-built body and majority of them wear traditional kurta pajama. Women of the community wear salwaar suit.
Ajrakh block Printing, Natural colours
List of craftsmen.
Team Gaatha
Interview: Ismail Mo. Khatri, Ajrakhpur (03/04/2010)
Interview: Musa Khatri, Ajrakhpur (03/04/2010)
Interview: Sufiyan Khatri, Ajrakhpur (17/09/2013)
http://nopr.niscair.res.in/bitstream/123456789/578/1/IJTK 7(1) (2008) 93-97.pdf