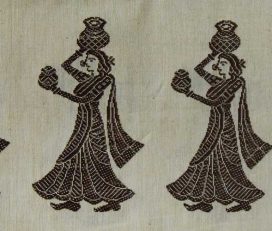
Gollabhama Saree Wea...
The Siddipet Gollabhama Saree is not just a piece of fabric; it is a living tradition, worn, celebrated, and reinterpreted through generations.
Siddipet, Telangana, India...
The Maheshwari sari is made of fine handloom cotton & silk yarn. It is uniquely bordered with a traditional design of five stripes running parallel across its length and on its Pallav (the edge which lies across the shoulder) and has a reversible quality. The sari’s origin can be traced to Rani Ahilyabai, the empress of Maheshwar who collected weavers from Surat, Bhuj, Patan and Hydrabad around 200 yrs ago and spearheaded this craft.
Maheshwari weaving was traditionally done to make saris, fabric by yardage, turbans, Dhoti (a drape worn by men around their waist), Chunri and practically to meet any fabric needs of the town. Maheshwar being a mix of weavers from Maharashtra, Rajasthan and Gujarat also became a cultural hotspot of diversities from these states. The woven fabric found varied usage in the way saris were worn differently by the women of each of these states. Keeping the weaving style similar; with striped cotton silk borders and motifs by extra weft in the border alone, the usage has expanded to a much diverse variety of garments being designed by inquisitive fashion designers from across the globe. Layering the fabric brings out the most innate qualities of the fabric like translucency and beautifully woven colorful borders in extremely exciting and innovative creations, be it through dresses or Kurtas. However, the cluster still retains its popularity as one that weaves the most exquisite and breath taking to contemporary tastes Saris.
A sari is an Indian female garment, usually associated with grace. It’s a two to nine yard long drape of fine fabric, two to four feet in breadth, wrapped around the waist. One end of the drape is usually heavily worked upon or woven and goes over the shoulder to fall free at the back and is called Pallav. Traditionally worn without one, a sari is now worn with short fitted blows covering the torso of the female body, keeping the midriff exposed and is popularly called Choli. This term for female bodice, the choli is derived from ruling clan from ancient Tamil Nadu, the Cholas. The concept of Pallav, the end piece in the sari, originated during the Pallavas period and is named after this ruling clan of Ancient India.
The onset of this sari boosted the economy of Maheshwar. Initially known for its temples and ghats dedicated to Lord Shiva, this little town transformed itself into the only place where this unique design was conjured. The expertise of craftsmen from various places, blended in the flavors of their natives. It became a beautiful concoction of cotton and silk threads and grew to be much appreciated because it was elegant and went very well with the weather. This fabric is perfect for starching into stiff pagdis and is said to be ‘ekdam khadak’ or ‘so stiff’ that it stands up without support, just as the wearers would want it to be. De-gummed silk is used in this craft, where the silk fiber is processed to remove the gum to make it soft and increase the tensile strength, it also prevents the sari or the yarn from cracking along the folds.
In ancient times, Maheshwar was known as Mahishmathi and it was ruled by King Kartavirya Arjuna (Sahastararjun). One day the King and his 500 wives went to the river for a picnic. When the wives wanted a vast play area, the King stopped the mighty river Narmada with his 1000 arms. While they were all enjoying themselves, Ravana flew by in his Pushpak Vimana (flying chariot). Downstream, when he saw the dry river bed, he thought it was an ideal place to pray to Lord Shiva. He made a ‘Shivalingam’ out of sand and began to pray.
When Sahasrajuna’s wives were done and they stepped out of the river bed, he let the waters flow. The voluminous river flowed down sweeping Ravana’s shivalingam along, messing up his prayers. Furious, Ravana tracked Sahasrajuna and challenged him. Armed to the hilt the mighty Ravana was in for a huge surprise. The mighty Sahasrarjuna with the 1000 arms pinned Ravana to the ground. Then he placed 10 lamps on his heads and one on his hand. After tying up Ravana, Sahasrarjuna dragged him home and tied him up to the cradle pole of his son. A humiliated Ravana stayed prisoner until his release was secured. Even today, the Sahasrarjun temple at Maheshwar lights 11 lamps in memory of the event.
For generations Somavaunshiya Sahasrarjun Kshatriaya (SSK) genealogy is historically maintained by the Bhats. Bhats claim that Sahasrarjun had 108 wives. Bhavasars and Shimpis were borne to the 6 wives of Sahasrarjun. Today they are in much larger number than Khatries. As expected, Parashuram arrived at the caves. He noticed many Ksatriyas were sitting calmly, wearing Janni across their shoulder. They held flower in their hands. Their mounth chanting verses of Gayatrimantra. Parashuram was puzzled. Apparently was expecting some armed resistance. Parashuram looked towards Mata to seek the answer. She explained to him that they were Khahtris and have denounced all weapons. They will no longer wish to fight. Bhats even expressed that Parashuram gathered all the offspring’s of Sahasrarjun at the caves, and taught them new trades. He taught Khatries how to weave clothes, Bavasars how to color the yarn and fabric and Shimpis how to sew the clothes. This weaving trade has been practiced in many SSK communities for generations ever since. Starting from Mandawagad,( Maheshwar in MP), down all the way to South India, to date many Khatries still weave saries. Many trade commodities related to looms and sarees. My family inherited the trade of weaving sarees and sale. They hire weavers and manufacture large scale sarees and promote them in the market place.
Queen Ahilyabai Holkar, the ruler of Malwa, made Maheshwar her capital city in 1767. This small town by the banks of the river Narmada was transformed during her rule into an active centre of trade and industry. The design of the Maheshwari sari was one of the steps taken towards this development by the Queen.
She invited many skilled weavers from various princely states like Hyderabad, Mandava and Gujarat to settle down in Maheshwar. Only a grey cotton fabric was locally produced. After these craftsmen moved in, many new aesthetics began to develop. The Queen also instructed them to take inspiration from the local architecture and the designs inscribed on the walls of her fort. This tied the fabric exclusively to Maheshwar in a distinct manner.
The craftsmen graduated from making just fabric to weaving saris, turbans and other clothing needs of the local people. Thereby slowly making the economy self-sufficient.The sari that was 5 yards in length was called – dandiya, whereas the one of 9 yards was called as sari. They used natural colours for the production of coloured textiles. Gradually, along with the simple textiles there began the production of checks and other fancy designs.
The Queen initially supported them by purchasing a lot of their products.She would then use it on herself when seen in public as well as use it to generously gift dignitaries. This way, the laurels of this craft travelled far and wide.
With the amalgamated skills of various artisans and craftsmen, under the efficient eye of the Queen, a unique aesthetic was developed. This also gave birth to a distinct traditional and cultural identity to the Maheshwar handloom operations, whose efficiency has survived until today.
The first challenge the craft faced was when the production of colours and dyes plummeted during the First World War. As an ofshoot of this, lower quality of colours were used which in turn affected the reputation of the fabric. The craftsmen slowly became lethargic. They then started moving away on the lookout for alternative professions.The population slowly diminished. This situation was resolved only around 1910 when a royal descendant, Naresh Thukojirao Holker and various subsequent organisations took measures to replenish it. The weavers were gathered once more and it was decided that the centres for dyeing and spinning will be established. After many more ups and downs created by socio-political incidents, the craft eventually flourished.
In 1921, the King Shreeman Holkarji Rao established a weaving and dyeing demonstration factory. The aim and objective of this factory was to create awareness about modern weaving techniques amongst weavers. At present this factory is a Handicraft training centre at Maheshwar. After the establishment of the training centre, various new weaving techniques were introduced in the cluster like the use of Dobby for border designing and the replacement of throw-shuttle looms with fly-shuttles. This increased the overall production in the region. These shuttles and dobbys were sourced from Nagpur and the weavers were given training in the usage of the same and many were even granted assistance for setting up pit-looms in their units. In 1978, Richard and Sally Holkar, belonging to the ex-ruler family established the
Rehwa Society, which has contributed significantly for the growth and development of the industry.
The Maheshwari saree is characterised by its elegant simplicity. Many of the patterns in the Maheshwari saris still retain their traditional form, while others have been modified over time. The borders are used as the demarcating feature. They incorporate designs inspired from the engravings on the Maheshwar fort.
The saris are classified on the basis of their borders or the patterns in them like Maheshwar bugdi kinar, zari patti, rui phool kinar (cotton flower pattern), phool kinar (flower pattern), chatai kinar (mat design), V kinar, kahar kinar, bajuband kinar ( narmada wave pattern in between silver and golden zari ) and the like.
They are also classified on the basis of texture. This determined by the amount of cotton or silk in the sari. The categories are 100 percent Cotton Sari, Warm Silk Sari, Silk Sari, Neem Silk Sari, Katan Sari, 75 percent cotton Sari, Tissue Sari, Mercerised Path Design Sari and Mercerised Checks Design Sari.
The sari has a reversible border so that it can be worn on either side. The border is made of beautiful zari work. The body of the sari is usually plain or has an array of stripes or checks. It has a unique pallav with five alternating stripes, two of plain white and three coloured ones. There are geometric patterns decorating the borders. There are no floral patterns. These patterns are usually fine abstract representations of local elements like the river and the local architecture.With fine cotton yarns in its weft and silk in the warp, this fabric is light and airy for the summers, yet has the subtle luster of silk.
Copper coated nylon has replaced the pure gold wires of zari and synthetic dyes have replaced the limited palette of natural colours. With high demands and extreme pressures on time, dyers have to get one warp of silk ready within an hour, leaving little room for revival of slow natural dyeing. There are only a handful of craftsmen who weave the original striped designs of the sari, which had a typical Marathi look, and these are popular in Maharashtra
Though recently the craft has been revolutionised by the youth of the society, almost 60 percent of the craftsmen are still lagging behind due to lack of marketing. Planning the weave of a sari is an art in itself and sometimes the craftsmen are not equipped with that. They are skilled but not everyone has the vision to study the present scenario, plan and create accordingly.
The silk yarn is dyed by the weavers in their homes. Although only acid dyes should be used for colouring silk but it has been observed that the weavers resort to cheap dyes, which leads to a large number of complaints regarding colour bleeding. To avoid this, the Weaver Service Centre at Indore has been organising workshops since past 3 years in order to create awareness on dyeing quality in the cluster. Besides, the co-operative societies and chemical merchants are supplying acid dyes in adequate quantities.
The dyers colour the yarns in rich colours after which a silk warp and cotton bobbins for the weft are prepared. Once the loom is set with the patterns for borders and motifs, the weaving starts. In the weavers’ colonies, every street is filled with the continuous clacking of wooden looms.
Maheshwari saris are handloom fabrics made of 100 per cent pure silk or in a proportion with cotton ( 50-50 or 75% silk). Silk is blended with Zari yarn to make tissue fabrics mostly worn in ceremonies.
Cotton
Cotton yarn for the weft is purchased from Coimbatore. The specifications are: No. 80 for the normal weft and No. 2/120 for the border. The normal rates are Rs.500/kg. In one kilogram there are 250 lacchis (bundles) of thread.
Silk
– 20/22 denier single Silk is used as the warp. This is purchased from China & Koriya.
– 20/22 Mulberry Silk (2 & 4 threads) is used as the warp. This is purchased from dealers in Bangalore. The rates of silk are very high, Rs.1300/kg (as on 4 September 2004). There are three bundles in 1 kg of silk.
Zari
Zari is used mainly in weaving the beautiful borders of Maheshwar saris. This is procured from Surat (Gujarat) at a rate of Rs. 1000/kg (as on 4 September 2004).
Pigments, Coconut Oil, Naphthol This is purchased from dealers in Mumbai and Indore.
Taana or Warp Machine
The warp machine is made of two basic parts. One is a big octagonal cylinder that rotates on its axis (which is very different from other warp machines in the sense that this cylinder is vertical), and the other is a vertical rack on which a number of thread rolls are placed. The rolls pass to the cylinder of the machine through hooks under a constantly moving frame that helps wind the cylinder in a criss-cross manner.
Handloom
Two types of handlooms are used in Maheshwar-”the older pit looms and the newer frame looms.
~ Pit Looms These are the type of looms originally used for Maheshwari weaving since historical times. These heavy, wooden looms are installed inside a pit, about 3 feet deep. The weaver has to sit on the wall of this pit, with his legs inside. The looms are permanently installed in these pits and have hardly moved from their place for many years.
~ Frame Looms These looms are the newer ones, with lightweight metal frames that constitute the main body. They were introduced hardly two to three years ago, and given their superior performance, have now been adopted by a large number of weavers.
The cost of a new frame loom is about Rs. 6,000, and it can be purchased from Malegaon, Maharashtra. This loom is superior to the older pit looms because they are lightweight and easily detachable. This helps when it needs to be shifted for rearrangements. Their pulley arrangement also gives a better finish for the sari borders.
Charkha
A charkha is used for making the rolls of thread. In case of warp, it is a big motorized one, which prepares big silk rolls. In case of weft, it is the smaller wooden one which prepares thin rolls called bobbins. These are put inside the shuttle to form the weft.
Dyeing Apparatus
These mainly include various types of dyes and the tubs in which the dyeing is carried out.
The craftsmen highly value their looms and consider it to be a benevolent provider. It is almost like an extended limb for them. For them, the looms are not inanimate objects but beings with life and feelings. Their intimacy to the loom is such that during the major festivals the looms are worshipped and smeared with ritual turmeric or vermillion. Even during festivals such as Raksha bandhan, ‘rakhis’ or ornamental bands are tied on the looms.
The dyers colour the yarns in rich colours after which a silk warp and cotton bobbins for the weft are prepared. Once the loom is set with the patterns for borders and motifs, the weaving starts. In the weavers’ colonies, every street is filled with the continuous clacking of wooden looms.
Maheshwari saris are handloom fabrics made of 100 per cent pure silk or in a proportion with cotton ( 50-50 or 75% silk). Silk is blended with Zari yarn to make tissue fabrics mostly worn in ceremonies.
The day starts differently for the various types of craftsmen comprising the cluster. The master weavers would first design the sari based on the raw material or the order. These master weavers are the ones who not only excel in technicality but also the thinkers who chart out the design. After this, the weaving is carried out.
At this stage, the master weavers carry out the process themselves, in cases where they have their own style or brand, or are part of any organisation (Govt. handloom training centre,M.P. State Handloom Weaver Federation etc). Alternatively, there are the worker weavers, lower in hierarchy since they do purely mechanical work. They collect the designs and instructions from the master weavers and deliver the end product to them.
The traditional designs with zari borders, motifs in them and/or striped and checked patterns are mostly used. Many designers and organisations have stepped into the craft and have come up with modifications of these traditional designs too.
Once this is done, the raw materials are procured. There are various suppliers and merchants involved in this step who bring in these raw materials from outside Maheshwar. Silk, cotton and zari come from different parts of the country. These are further processed to make it easier to work with. There are local merchants too who provide yarn and chemicals.
These threads are then dyed by specialised dye technicians for the plethora of colours. There are different kinds of dyes for dyeing silk and for cotton. When the dyed and variously hued threads are sent back to the weavers, they first free them from tangles and stretch them out. These are reeled into rolls by using a large charkha and used as the warp.
Once the warp, weft and the design is fixed in the loom, the weaving begins. Small bundles of sand are seen arrayed on the loom to help keep the yarn tense.The movement of a shuttle takes the yarn of the weft across the threads of the warp. The overhead dobby mechanism is used to design the border of the sari using the gold zari thread. Once the saree is woven, it is is released from the loom and sent of to be cut into desired lengths.
These finished products are sold by both traders and big organisations. The traders buy the end product and sell it locally or to other brands. The organisations carry the fabric to the domestic market in the metro stores or in the form of expos and exhibitions.
Mostly, there is also a merger of different crafts happening after completion. These finished saris are bought by other printers and organisations as raw material for their craft. For example, Maheshwari saris are bought by Ajrakh or Bagh printers as raw material or base fabric for block printing. This feature has also popped up with the onset of Indian brands incorporating and combining various crafts.
– The threads that are left over are used to make colourful cattle accessories called Fundha. People from the neighbouring villages come to buy these for Rs 50-100 per kg.
– The zari scraps are also reused. These are sold for Rs 200-300 per kg.They are melted to retrieve the silver and copper.
– Waste water after dyeing.
The name Maheshwar comes from Mahesh, a name for Lord Shiva. The word Maheshwar in Hindi means the abode of Lord Mahesh. Maheshwar was the capital of king Kartavirya Arjuna, who is mentioned in the Sanskrit epics Mahabharata and Ramayana. It was then known as Mahishmathi. The reason, it is said, was probably the abundant presence of mahishya or buffalos. The other assumptions for its etymology includes names of various kings and sages who once lived and worshiped here.
In the late eighteenth century, Maheshwar served as the capital of the great Maratha lady Rajmata Ahilya Devi Holkar, ruler of the state of Indore. She embellished the city with many buildings and public works, and it is home to her palace, as well as numerous temples, a fort and riverfront ghats (broad stone steps which step down to the river).
Maheshwar is situated at the banks of River Narmada, which is one of the holy rivers of India and due to which Maheshwar too became popular as a religious city.
It is located at 90 kms from Indore in the south, 13 kms from Dhamnod in the west, 5 kms from Badwaha in the east and 32 kms from Khargone in the North. The city is approximately 283 meters above sea level average (± 9 m). It's 1247 hectares (Nagar Panchayat area) is lived in by a population of 20,597 (2001 Census of India).
Maheshwar is a bustling temple town by banks of river Narmada. It attracts great devotees of Lord Shiva and the river. Now, the Maheshwari saris have also brought it in their share of visitors and admirers. The landscape goes back in time as you move into the town from the market centres. Nearing the riverside, the numerous stone steps of the ghats,forts and the splendid temples are freckled with devotees and tourists. A few take a dip in the holy river while others are engaged in rituals. The temples and magnanimous fort with their feet in the river are flocked by awestruck crowd.
Visitors come at milder temperatures or major festivals like Maha shivrathri, which exist during the months of October to March.Maheshwar has extreme climatic conditions with temperatures in summer going upto 45 deg. celsius (May) and winter dipping to 3 deg. celsius (Nov- Feb). Granite, Kailsait, Kwartjait, limestone, Breksia and Reteelapttht are the major minerals found in the district. Rabi sorghum and maize are the principal crops. Krif.Cotton and groundnut are the major commercial crops.
This temple town is a pilgrimage spot as well as tourist destination. The main city is just like any other with good hotels, hospitals and shops. Internal commute by vehicles is also not difficult because of good road network. The city changes shape as it nears the river and temple side. It splits into smaller lanes and bylanes flanked by numerous houses. The road that bifurcates at Bazaar Chawk, with one branch leading to the fort and the other to the river Narmada, forms the main axis of the town, along which are located all the important commercial activities.The rest of the town has an organic development pattern with narrow streets and large public squares.
The grand Maheshwar fort steals all the attention in the skyline. The hundreds of steps of the ghats leading upto the fort and temples, start their journey from the banks of the river. Closer to the temples, the structures seem ancient and lost in time. They are mostly massive and made of stone. These are veined by small lanes between houses of the locals. These are built of brick and concrete. There are sudden sightings of older houses amongst the modern constructions. These have pillared verandahs and elaborately carved balconies (A clear Maratha Influence).
Maheshwar also houses weaver colonies (Mominpura, Dalalpura, Maru Mohalla etc.) and cottage industries. The dwellings of the weavers are of modern construction and have simple functional plans. The handlooms are placed in the first room on entry or the living room and the private spaces far in. The looms are embedded into their routines so much so that there is no concept of a different workplace and a different space to live. There is a statue of Queen Ahilyabai at certain intersections.
There are also the organisations like the Rehwa Society (5) an NGO founded by the Holkars in 1978 to give women employment and revive the town's textiles. They have vast courtyards, lined with handlooms for the women to gather and work.
Maheshwar is a town of great historical and religious importance. Its mention in the scriptures and traces of ancient architecture stand testimony to the fact. The culture is also termed 'Nimar' as it is believed to be a mix of Aryan and non-Aryan cultures. The culture mix continued with the handloom industry which hired people from various castes and religions, including Kshatriyas, Bharuds, Muslims, Kumhars and Kahars. All these people are either from nearby areas or have migrated to Maheshwar and are now permanent residents there.
Maheshwar is full of festivals and celebrations. Maha shivrathri is a prominent festival when people flock to ardently worship Lord Shiva. Every year Swaadhyaaya Bhavan Ashram organizes Mahaa mrityunjaya Rath Yatra in the town of Maheshwar. The yatra intends to invoke blessings of Ayurved Murti Bhagwaan Sadaashiv Mahaamrityunjaya (who is regarded as the primordial and supreme doctor), and it starts from Swaadhyaaya Bhawan Ashram and culminates at the banks of the Narmada. The festivals of lord Ganesh and Navaratra are also celebrated with great enthusiasm. During Navratra, the urban squares and public places are filled with festive people dancing, singing and praying.
The continuing reverence for the Queen Ahilya Bai Holkar is visible as thousands of devotees throng to the Ahilyabada during the Ahilya festival, the palace within the fort from where she ruled and held meetings to coordinate her welfare and building works across India.Other prominent annual festivals include the Narmada festival, Kalidas festival and the sacred river festivals.Another prominent festival is Moharram. Though a muslim celebration, almost 75 percent of the Hindus join in too.
Maheshwar's religious importance and the way it interacts with its architecture and open spaces like its Ghats marks it as a must-visit on the map. It is famous for some of the oldest Shiva temples and shrines. Some of the ancient temples here are Shiv Jyotirlingam Mandleshwar, Bawangaja and Mandav. Towards 65 kms east of Maheshwar lies Onkareshwar temple, which is one of the 12 most popular Shiv Lingam temples in India. Jain influences have also been found near Maheshwar. Oon is situated in Nimad, 70kms south of Maheshwar, which is one of the important centers for Jains and excavations of the place have revealed artifacts as old as 11th century AD. The Oon is an 82 feet statue carved out of a single rock. It was built by the King Meena Ramchandra during 1166 B.C.
Maheshwar is in close proximity to some picturesque destinations. Mandu is a beautiful hill station located in the Vindhyas around 2000 ft above sea level. This city is also famous for the epic lovestory between Shamshah Bajbahadur and Queen Roopmati.
List of craftsmen.
Team Gaatha