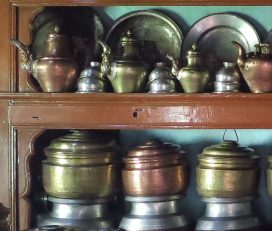
Copper Craft ~ Chili...
Copper and brass have played a significant role in fulfilling these needs. Even today, in most traditional Ladakhi kitchens such utensils are commonly seen
Chiling Sumda...
Block printing is an ancient technique of textile printing that is practiced even in modern times. Intricately carved wood blocks are used to stamp patterns onto the fabric. The method of dyeing used is ‘resist-dyeing’ where the true colors are revealed after reacting with air.
Traditionally block printed fabric was traded to the nomadic tribes at local markets. The intricacy and beauty caught on and later it was used as drapery by the royalty too. The versatility of the fabric has lent it to be used in making Sarees, Dupattas, Kurtas, Stoles, home linen and on products such as lamps.
Block print technique is known for its versatile nature, where a combination of various motifs is used to achieve a beautiful patterned fabric. Craftsmen enjoy the versatile nature of the craft as it provides them the freedom to experiment and create new designs. According to them the work with hands never ceases to stop exploration on various designs, as opposed to the screen printing done using machines. These prints have become a rarity now and a few of the old fabrics preserved by traditional craftsmen can be found in the museums today. It is only due to the passion and genuine interest shown by the craftsmen, that a highly skill based craft has survived till today.
The craft of block printing was practiced in Sindh and is believed to have existed from as far back as 3000 BC. The fabrics unearthed at sites like ‘Fustat’ in Egypt are believed to be block printed Indian fabric. The Gujarati port of ‘Bharuch’ appears in the records of Greek geographer Strabo (63 BC- AD 20) as ‘Barygaza’ from where a variety of Indian textiles were exported to the west. The craft was mastered by the civilizations which flourished around the Indus River in Sindh area. The river provided both a site for washing clothes and the water needed to grow indigo.
The bust of a ‘King Priest’ excavated at a site in Mohenjedaro shows him draped in a block print fabric that bears strong testament to its ancient lineage.
Printing and dyeing flourished in Rajasthan in the medieval ages and the influences brimmed over to Gujarat. The craftsmen in Gujarat developed an expertise in printing with wooden blocks. Printed fabric was a frequent element in royal processions with which they made tents when the battalion rested.
Soon auxiliary industries such as yarn spinning and dyeing began to be practiced in accordance to the seasons conducive to fabric printing.
Printed fabric from India was traded to Egypt, Rome, Indonesia and the Far East. ‘Surat’ was established as the main centre for export of printed cotton fabric. In Gujarat, ‘Pethapur’ flourished as the centre for making wooden blocks. Intricate traditional designs were chipped in by artisan families. The prints came to be known as ‘Saudagiri’ prints as ‘Saudagars’ or traders used to gather at fairs, markets or ‘Haats’ and sold their printed fabric to common folk as well as royalty. In Indore, the craft is still followed by the fifth generation of block printers who had come from ‘Nagore’ village of Rajasthan. They were Hindus who converted to Islam during the reign of ruler ‘Feroz Shah’ and travelled to Ujjain to serve the king, who had invited them to settle in his kingdom, due to their excellent craftsmanship. Later they spread to other regions including Indore, as their popularity grew.
The blocks incorporate designs which are traditional as well as contemporary variations. They are of different shapes and have designs carved at the bottom of the block. Teak wood is used for making them on which designs are made by skilled craftsman. The cloth is dyed into a solid color on which a latticework of patterns is stamped with the blocks dipped in dye. These patterns are formed by various motifs. The patterns are floral, free form and geometric. They are mostly inspired from local environmental elements. Intricate patterns are chipped with references from monuments, mosques, temples etc. Even old photographs are referenced for ideas. They can have large ‘Bootas’, small ‘Bootis’, trellis or ‘Jaal’ shaped designs, small borders, large borders and sometimes even geometric designs are used. Each design normally has a maximum number of three colors only and each color is derived from a separate block.
A crucial requirement for block printed fabrics is the availability of flowing water. But due to falling natural water tables and scarcity of available natural resources, many craftsmen have come to rely on man-made water tanks for flowing water. This is an expensive affair and increases the costs of production.
The natural colorants have also been replaced by chemical dyes. The onset of screen printing also poses a threat to the art of block printing since it is faster and cheaper.
With increasing difficulties in practicing the craft, the young generation of many craftsmen chooses to follow more lucrative careers, resulting in very few successors to carry on the craft tradition. In Indore, where almost 60-70 families would practice the craft before, only 2-3 families chooses to follow it now.
The beautifully symmetrical pattern of block printed fabric is created by pressing intricately carved hand held wooden blocks that have been dipped in dye. Beautiful motifs using vibrant colors are created across yards of fabric which is then treated with various stages of resist dyeing.
Wooden blocks– The wood blocks made from seasoned teak wood are sourced from the towns of ‘Pethapur’, ‘Ferozabad’ and ‘Sanganer’.
Fabric–
Dyes- Natural as well as synthetic dyes such as pigment dyes, discharge dyes, reactive dyes and vegetable dyes are used.
Khar or Starch– It is used along with castor oil to treat the fabric before being washed out.
Castor oil– Used along with starch to treat the fabric.
Harda– This is used to give the fabric an off white color.
Fitkari or Alum– It is mixed along with indigo dye to achieve a green color and mixed with black to get a chocolate brown color.
Iron– Iron is heated and put in water to obtain the black color from where it is singes. The rust is also used for color.
Glue– It is mixed with pigment binder to create a thick viscous liquid. This gives the color tray a soft base which helps to spread color evenly on the wooden block.
Newspaper– The printed fabric is rolled up inside newspaper sheets to prevent the dye from spreading onto other layers.
Coarse piece of cotton cloth– It is used inside a tray containing the dye. The cloth soaks up the dye and blocks are pressed on it instead of direct dye application. This prevents dripping of color.
Wooden blocks- Made of seasoned teak wood, the wooden blocks are the main tools of the printers. These blocks are carved in accordance to the designs given by the craftsmen in Pethapur, Ferozabad or Sanganer and are etched on the underside of the block. About two to three holes are drilled vertically and horizontally across the body of the block, which ensures free air passage and release of excess printing paste. This special feature is unique to these blocks.
Dyeing Trays- Trays made of wood or plastic are used to fill the dye and it is mixed with the help of various ladles. A thin bamboo trellis is fixed into the tray of dye mixture and this holds a coarse piece of cotton cloth. The cloth has been soaked in dye and the blocks are pressed onto it, rather than being dipped in the solution. This enables the dye to spread more evenly onto the block and not drip.
Printing tables- These are raised wooden blocks and are 5 feet by 3 feet in dimension. Bricks and smaller wooden blocks are used to uniformly raise this platform by 9 inches. Printing begins on these after they are covered with layers of plain cloth and jute for protection.
Paper Stencils– Paper stencils are used for outlining the border designs, in case of apparels like kurtas.
Metal Pins– The fabric to be printed is stretched out on a wooden table uniformly and fastened using strong metal pins.
Wooden trolley– It is used to store colors on its racks and the printer drags the trolley along as he prints.
Boilers– These are used to steam printed fabric and fasten their colors.
Bamboo trellis– A thin bamboo trellis is fixed into the tray with dye mixture to hold a coarse piece of cotton cloth.
The beautifully symmetrical pattern of block printed fabric is created by pressing intricately carved hand held wooden blocks that have been dipped in dye. Beautiful motifs using vibrant colors are created across yards of fabric which is then treated with various stages of resist dyeing.
Preparing the fabric
Before printing begins, the fabric has to be treated where the fabric is treated with ‘Khar’ (starch) and castor oil. It is then washed thoroughly to remove the factory starch. Later it is treated with ‘Harda’ to achieve an off white tint to the fabric. If the natural grey of the fabric is not desired then it is bleached to obtain a stark white color. The fabric is also sometimes dyed to get a base color at this stage and washed to remove excess dye. It is then stretched evenly over a wooden table and fastened uniformly using strong pins.
Making the dyes
Iron is heated and put in water to obtain the black color from where it is singes. The rust obtained from iron is also used for color. Alum also known as ‘Fitkari’ is mixed with Indigo to get a green color, and mixed with black to get a chocolate brown color.
Printing
The wooden blocks are used at this stage. The Color is kept in a tray on a wheeled wooden trolley with racks which the printer drags along as he works. The tray of color rests on another tray which contains a thick viscous liquid made from the pigment binder and glue. This gives the color tray a soft base which helps to spread color evenly on the wooden block. The fabric is printed by hand from left to right. Different printers/ craftsmen are involved in the stages.
One layer of blocks is pressed appropriately with adequate pressure to get the pattern. This is repeated as per requirement. In case another set of prints is needed, this is done by the other craftsman. Paper stencils are placed on the fabric for outlining the border designs, in case of apparels like ‘Kurtas’. Approximately 30 to 35 m of a single color fabric, per day is finished by one person.
Post-printing
After the block printing is done; the fabric is then dried in the sun. It is rolled in newspaper to prevent the dye from spilling on to other layers and is then steamed in boilers. The fabric is again washed in large quantities of water and finally dried. The process is finished by ironing as this makes the color become permanent.
As the fabric is washed in water mixed with starch solution, water wastage is involved. Measures should be taken to reuse the water for other purposes. The remaining dyes or colors are not wasted as they can be mixed with kerosene and re-used.
Indore became an established center of commerce by 1715 AD, when many traders settled in the villages on the river banks of 'Khan' and 'Saraswati'. This was due to Indore's prime location in the route of the Marathas of Deccan on their way to North India. These Maratha Guerilla warriors were in constant battle with the Mughal Empire. It was also located on India's oldest pilgrimage routes from 'Mahakaal' at Ujjain on river 'Shipra', to 'Omkareshwar' on the river 'Narmada' and onwards to 'Rameshwaram'.
The city derives its name from the temple of 'Indreshwar', which was constructed in 1741 AD. It grew as a center of trade under the 'Holkar' dynasty which reigned from 1733 AD to 1818 AD. The city became the capital of the 'Indore princely state' in 1818 AD, after the British forces under Sir John Malcolm, defeated the Holkars, led by Rani Krishanbai Holkar at Mahidpur. She signed the treaty of 'Mandsaur' by which the control of Indore went in the hands of the East India Company.
Indore lies on 22.2 - 23.05 degrees North Latitude and 75.25 - 76.16 degrees East Longitude. The city lies in the 'Malwa' plateau and is the largest city of Madhya Pradesh. It is centrally located in the Indian subcontinent and lies to the south of the 'Satpura' ranges at an elevation of 553 meters above sea level.
By air: 'Devi Ahilyabai Holkar Airport' connects Indore directly to Bombay, Delhi, Ahmedabad, Hyderabad, Calcutta, Jabalpur, Raipur, Jaipur, Nagpur, Pune, Bangalore and Bhopal in India. It was upgraded to the status of an international airport by the end of 2008.
By rail: The Indore railway network is part of the 'Ratlam' Division of the Western Railways. Indore is one of the several places in India with both meter gauge and broad gauge rail tracks that are operational. Regular train services connect Indore to most parts of the country.
By road: Indore is well connected to other parts of Madhya Pradesh and India through national and state highways. There are some major highways which pass through Indore and connect it to the major cities. They are: the Agra-Bombay National Highway (NH3), NH59 which connects to Ahmedabad in the West and Betul, Itarsi, Bhopal in the east by a state highway.
Local Transport: Indore has one of the ï¬nest public transport systems. In December 2005, the municipal corporation launched the Indore City Bus service, an extensive service with 24 routes servicing in most areas of the city. The other means of local public transport are the mini-buses (called 'Nagar Sevas' by the locals) and the Tempos and Auto-rickshaws.
Indore has a humid sub-tropical climate. The summers, spanning from March to June, are hot and temperatures peak up to 40 degrees Celsius on the hottest days. Winters, spanning from November to February, are chilly and dry with the temperatures dipping to 4-6 degrees Celsius on some nights. The southwest monsoons bring in moderate rains of 35' to 38' from June to September.
Indore is a thriving city, the largest in central India and plays a very prominent role in its economy. With its various large scale and small scale industries it is the commercial capital of Madhya Pradesh. Indore is also home to many prestigious educational institutions like the Devi Ahilya Vishwavidyalaya (University of Indore), The Daly College, Indian Institute of Management, Indian Institute of Technology etc. The city gets its water supply from the river Narmada and from the many surrounding lakes and bore wells.
Indore is a well developed city that finds its place in contemporary constructions. However, it hasn't lost the essence of its historical monuments and traditions. These historical structures speak of different periods of rule in Indore like the Mughals, Maratha, Holkars and the British era. Some monuments are a blend of two styles like the 'Rajwada Palace' which is a mix of Mughal and Maratha architecture. The Indore skyline is specked with these elements retained from history as well as the high rise constructions of the present times.
Indore is situated in the Malwa Plateau at the western region of Madhya Pradesh state in Central India. Malwa plateau is on the northern park of Vindhya Mountain Range which lies in western part of state, adjoining to Maharashtra state. If we go by the history of Malwa region, it remained under the influence of Maratha dynasties and rule. Holkar dynasty that ruled in Malwa region and developed this region is also originally from Maharashtra. So, it is found that Indore and its nearby towns & destinations have deep impact of Marathi culture in their dressing, social gatherings, local languages, festivals, rituals, housing styles and their food habits.
Indore has a large Jain community as well as the highest Marathi population in Madhya Pradesh. There are also sizeable minorities of Muslims, Christians and Buddhists in Indore. The official language is Hindi and the dialects spoken are 'Bundelkhandi', 'Malwi' and 'Chattisgarhi'. The other major languages spoken in Indore are Marathi, English, Rajasthani, Punjabi and Sindhi.
It is on the bank of River Khan and Saraswati, which merges at the city center. Being the biggest industrial city in the state, it is also called as the 'financial capital of Madhya Pradesh' and 'heart of Madhya Pradesh'. It is also the gateway to some of the magnificent riverside pilgrimage destinations & historical monuments. Here you will find the information on how to reach the city. Indore city is very well linked by road, train & flights with other important cities of India.
All national festivals like 'Holi', 'Gangaur', 'Teej', 'Rangpanchmi', 'Baisakhi', 'Raksha Bandhan', 'Mahavir Jayanti', 'Navratri', 'Durga Puja', 'Dussehra', 'Ganesh Utsav', 'Deepavali', 'Ramzan', 'Gudi Padwa', 'Bhaidooj', 'Eid', 'Christmas', 'Baha'i Navruz' and other others like 'Nag Panchami', 'Ahilya Utsav', are celebrated with equal enthusiasm. There are many Shiva temples in Indore; 'Maha Shivratri' is celebrated as a major festival in Indore.
Due to the good flavor, taste as well as variety of food in Indore, it is praised by food lovers all across the country. Indore is known for its popular variety of 'Namkeens' (salted savouries). The city takes a treasure trove of culinary information and today its menu caters to different kinds of taste buds. Spicy Chat Food like Pani-puri, vadas, samosas and the very delectable chola baturas are first choice of the people. Indore is well known for other dishes like Dal-Bafla, Nihari Gosht and Bafla-Gosht in Malwa Region. The city is well known for its drinks and thirst quenchers like the Shikanji, a fascinating drink which is a combination of milk and dry fruits. They are an integral part of the cuisine of Indore.
Indore is the biggest city of Malwa region. People from various ethnic backgrounds inhabit this city. Majority of population speaks Malwi and Marathi. As the city is home to India's finest colleges, students from around the country flock to this city.
The people from Malwa have a penchant for clothing themselves in colors. The traditional attire for women is Saree or Lehenga-choli and for men is the Kurta-pyjama, Dhoti and Safa. Malvi Safa is a unique type of turban which has a knot on one side of the head. The Muslim men also wear a Topi or a small hat. Most of the population has moved on to pants, trousers, shirts and t-shirts according to ease of use and contemporary influences.
Indore is famous for its 'Namkeens', a salted snack variety of 'sev', 'Dhania-Chivda', 'Papdi', 'Garadu' etc. It is also famous for the skilled craftsmen who create fascinatingly realistic products from leather, making leather toys a much sought after product.
The 'Rajwada palace' is a seven storied structure, built more than two centuries ago and that forms the main square in the heart of the city. The historic palace of the 'Holkars' was built in a mixture of Maratha, Mughal and French style. The 'Gopura-like' monumental stone and wood structure is flanked by bastions, studded with balconies and windows. It is a strong testimony of the past grandeur of the 'Holkars'. It was burnt three times in the course of history and the last time was during the 1984 riots.
The 'Lalbagh Palace' is one of the finest structures commissioned by the 'Holkars' and is situation by the banks of the River Khan. It is an opulent blend of the baroque and renaissance styles.
'Gomattgiri' is a pious place for the Jain religion devotees situated atop a hillock near Indore. A statue of 'Gomatteshwar' stands built here, 21 feet tall. It is a replica of the 'Bahubali' statue of 'Shrawanbegola'.
List of craftsmen.
Team Gaatha