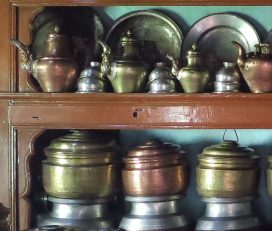
Copper Craft ~ Chili...
Copper and brass have played a significant role in fulfilling these needs. Even today, in most traditional Ladakhi kitchens such utensils are commonly seen
Chiling Sumda...
Terracotta art has left behind a diverse array of archaeological evidence in India, spanning various historical periods. This art form was utilised to create a plethora of objects, ranging from children’s toys and household decorations to religious items utilised in worship and rituals.
As water containers- One of the prime objects crafted and sold by Khavda potters are pots. Since they are made out of clay, they help keep water inside them cooler for a long time. These pots have a distinct shape- they have a round base but a flat and slating top which connects the base to the mouth. They have a smooth finish.
As kitchen utensils- Potters also make plates, bowls and other kinds of kitchen utensils. These are painted in traditional design and have a rich aesthetic.
As decorative items- In recent years, potters have also started making decorative items such as diyas, lanterns and showpieces. These decorative items have a distinct and modern design which is unlike the traditional vessels made using this poetry technique. A knife tool is used to carve holes in the items so that a lit candle or diya kept inside radiates its light evenly outside. Urns, vases and attractive showpieces are also crafted by the potters.
As bottles- Khavda pottery is used to make clay-based bottles. These are wide at the bottom and become narrower at its mouth. It has two small holes, through which a thread is passed and tied. Then, the bottle can be carried around the beck. These bottles are mostly used by farmers and shepherds in rural areas. Since pottery helps keep things cold for a long time, farmers and shepherds find these bottles especially useful.
As toys- Often, potters also make coiled toys for children who visit them. Nowadays, children prefer plastic toys over wooden ones but nonetheless, clay-based toys are shaped by hand and sold by Khavda potters.
These objects trace, reflect, and celebrate the cultural heritage of the area.
Haku Shah mentions in his book “Pottery is made from clay which is locally referred to as ‘mati’. The word ‘mati’ can also be used to refer to a man. Gujarati language has a handful of phrases and idioms which illustrate the close relationship shared by man and clay. According to one saying, if a person is born without a limb, it is said that god must have run out of clay to mould a limb in their body. Similarly, if a woman cannot beget a child, it is said that god must have run short of clay. This linguistic relationship between the two words is quite poetic and equates man to clay.”
A large bulk of terracotta objects has been yielded from these sites, indicating both religious and utilitarian use. The objects were aesthetically made, maybe used for ritualistic purposes or for children’s toys, and decorated with colours to make them attractive for buyers or household use. A large number of animals and bird figurines have been found compared to human figurines.
The most popular items include human figurines, animal figurines, pots, toys, jewellery, and more than five hundred terracotta wheels, which were most probably used as attachments to toy cart frames/chassis. Khavda pottery is unlike any other pottery form- it traces its origins to the Indus Valley civilisation. Harappan pottery is remarkably significant- pottery-making was at its peak during this era. Archeologists and researchers have found quite a few similarities between Harappan pottery and Khavda pottery. This indicates that the craft is a continuation of an age-old practice from a civilisation that is deemed to be quite ahead of its times.
In 1968, Khavda was discovered as one of the fifth largest archeological sites of the Indus velly civilisation. There are many similarities between Kutch pottery and terrractora ware of the civilization, which were traced back from rituals and customs still followed by some communities in the region. Not only does the art form’s historical importance increase its value, its various uses also enrich its significance. Khavda pottery is not merely limited to the production of pots. Artisans craft toys, decorative items and various other kitchen utensils too.
Khavda pottery is unique because all materials used in crafting it are derived from nature. From the clay that is used to mould the pot to the paints that decorate its surface, pottery is made using soils found nearby the village. In this time and age, where more people are becoming environmentally conscious, this craft can serve as a great alternative to wasteful materials such as plastic, silicon and ceramic.
The origin of pottery in the world can be traced back to the start of agriculture in the Neolithic period. The form at the time was crude and fragile. By the Mesopotamia times (around 6000-4000 BC), the potters’ wheel and kilns had been invented. This elevated the art form and made it more sustainable. It became the beginning of an era in the field of pottery. The industry peaked during the Harappan civilization.
During the Indus Valley civilisation, the art of pottery making was at its peak. According to a few sources, from Dholavira only, more than 100 potter wheels were found! Three types of pottery were produced during this period. They are glazed, plain and painted pottery. Most of the pottery produced was wheel-made and barely any pottery was made by hand. This points to the sophisticated approach to pottery that was being applied even during that day and age. Even though plain pottery was more plentiful than painted pottery, the latter bears resemblance to the present-day craft of Khavda pottery. Known as black painted ware, the red base of pottery was painted over with black to make beautiful geometric designs, shapes and patterns.
Dholavira, where one of the largest Harappan excavations took place, is only separated from Khavda by the Rann of Katch lake and is located 1 hour away. Dholavira was thought to have been occupied from 2650 BCE to 2100 BCE. Later, it was re-occupied in 1450 BCE. Artefacts excavated from Dholavira include terracotta, ornaments, animal skeletons, gold, silver, bronze utensils and pottery. The site was also a booming trade centre in Gujarat and items were exported to Sindh and Punjab from here. It is quite possible that the traditional Khavda pottery originated during the Harappan civilisation in Dholavira and quickly spread to other parts of Gujarat, like Khavda. There are many similarities between Kutch pottery and terracotta ware of the civilisation, which were traced back from rituals and customs still followed by some communities in the region. Nani Rayan in Gunthri Gadh has evidence of early history pottery from the Khavda taluka dating back to the 1st century. The two main types of pottery found there were coarse red ware and painted black on red ware, with the latter being more popular.
Black on red ware pottery consists of pots with thin walls and carefully drawn geometric designs. While the pot itself was reddish-brown in colour, the designs were drawn in black. Black on red ware has a close association with a form of pastoralism in Western Iran. It is also considered to have evolved from Rangmahal ware, which had a red background with black designs, but the designs were centred around plants and animals. The black on red ware found in Kutch was globular in shape and had geometrical designs, instead of ones depicting nature. The distinctive feature of this pottery is that it is painted. The aforementioned geometrical designs were often abstract shapes such as triangles, lines, cross hatched patterns, etc. Other types of pottery found were stamped pottery and incised ware.
Khavda potters do not limit themselves to the creation of pots only. Other items like cups, mugs, bowls, plates, diyas, bottles and toys are also made.
Before the pottery is painted on, they are coated with a layer of Geru (reddish-brown) soil. Geru soil is mixed with a bit of water and due to its bright pigmentation, it gives the pottery a natural reddish-brown colour. Then, once the colour dries, they are embellished with beautiful designs.
The designs painted on Khavda pottery are influenced by nature. The artisans take inspiration from the plants, trees, and animals around them. Beautiful patterns containing waves, flowers, leaves, birds and even fish can be seen intricately painted on the surface of the pottery. However, the silhouettes of such designs are only dotted by paint. They are unique as the paintings are dotted, so from afar, the meaning of the design is not immediately apparent. This gives it an abstract feel. Upon closer observation, one can see that the dots are carefully and meticulously arranged in repeating patterns. Paint colours used for these designs are derived from naturally occurring white and black soils. These soils too are mixed in water and then used as colour. Traditionally, the ends of thin twigs were used to paint, but these days, womenfolk use brushes to attain careful accuracy.
Similar designs have been found in ancient archeological sites of the Indus Valley civilizations, which shows the rich history of this ancient art form. Pottery ageing from that civilisation too was decorated with geometric patterns in red, black and green colours. Seldom, white and yellow colours were also used.
Khavda pots also have a distinct design. They are rounder at the bottom and then taper in slant lines towards the mouth of the pot. The outside surface of the pot is beaten evenly and its rough edges are smoothened by using a flattening tool.
The working conditions of the potters are rough. They work under extreme temperatures in the Kutch region. They also face some serious health risks due to the intense physical work and their exposure to dust, gas, and smoke from the bhatti (pottery baking kiln).
Moreover, in the contemporary scenario, the potters are suffering because people prefer steel and brass vessels, as opposed to traditional earthenware. The former are mass produced, have higher durability, lighter, and easier to access. These very qualities also make these vessels a symbol of financial superiority in rural areas. The potters themselves do not use their own items in their houses as much. This leads to a unique juxtaposition for the potters of continuing tradition and modernising.
Additionally, due to the change in climate, the quality of the clay has changed and become more saline in nature. The potters are unable to employ the techniques that have stood the test of time for many centuries, until now. It has led to many issues in production which have been difficult to resolve. It consequently has also led to the next generation of potters having a desire to break away from their family job and find employment in urban settings
The process of making Khavda pottery can be roughly divided into three stages- shaping, painting and baking.
No rituals
The process of making Khavda pottery can be roughly divided into three stages- shaping, painting and baking.
Shaping- The potters get the mud for the pottery from a particular acre (lake) nearby. This mud is called rann ki mitti. The mud is quite soft due to its proximity to the water source, which makes it easy to mold. The mitti is most often dug up during dry seasons by the potters themselves. During this time, it is sticky. Therefore, the potters leave it out in the sun for a couple of days until the lumps have dried. After they harden, they are kneaded (by hand or foot) and then crushed with a wooden stick. They are then passed through a sieve to remove small rocks and leaves. Next, it is placed on the cemented floor and the middle of the clay pile is hollowed out to pour water for mixing. Then, it is kneaded until it is smooth and sticky.
The potter’s wheel is called chak in Kutchi, Urdu, and Hindi. Two chaks are used in this form of pottery. One is the spokes wheel and the other, the stone wheel. The former is more common. Spokes wheels are lighter and easier to handle. They are used to make small, intricate objects whereas the heavier stone wheels are used by more experienced potters.
Once the clay is placed on the spinning chak, the shape of the earthenware is achieved via the throwing method. The potter molds it by applying a precise amount of pressure with wet hands. It is the oldest and simplest method and is usually employed to make items such as diyas, small cups and bowls. After the clay is shaped into pots on the wheel, the pots are placed on a long wooden bench and left to dry in the sun before they are decorated.
Some earthenware is thrown into a rough shape and then beaten. It helps make the pottery uniform and gives it strength, and it requires a tremendous amount of dexterity. Beating requires a wooden paddle called phaglo, a stone anvil called kunehra, and wood ash. The potter places the rough shape of the pot on himself while seated on the floor, sprinkles wood ash on it, and places the kunehra inside the pot for support. He then shapes the pot by pushing it down with the phaglo. The process is time consuming as the potter has to constantly rotate the pot to ensure uniform thickness. Once the pot is complete, it is placed upside down and left to dry. This method also helps to improve the thermal shock resistance of the pottery, making it an ideal method for creating cooking utensils.
Painting- The men of the community handle the making of the pots, while the women focus on decorating them with paint. The paints used by the women are all-natural and clay-based. The primary colours used in Khavda pottery painting are white, red, and black. The rock form of the clays are brought and soaked in water for a day. Next they are ground using a pestle and mortar and pushed through a sieve. The process takes 2 days, after which the power is mixed with water to create a paint. First, they coat the pots in a thin layer of geru. This gives the pot an even, red base and helps the designs stand out more. Then the artisans create patterns by using a combination of dots and stripes. The brushes used by the artisans are also made with a precise process of cutting the tip of the wood vertically and then crushing it to create bristles. The width and length of the brushes vary according to the designs and size of the pottery. Many similarities have also been observed between the designs used in Khavda and those found at excavation sites.
Baking- After the earthenware dries, they are hardened by baking. This can be done using pit firing or in brick kilns. Pit firing is widely used in the area and involves a large triangle-shaped pit dug in the ground. Potters are able to fire between 100 and 200 pots at once, however the size of pots decides how many can be fired at once. For fuel, natural substances such as cow and goat dung, twigs, leaves, and household rubbish are used. Larger pots are placed on layers of dung, with smaller earthenware spaced out between them. Then, the pit is packed with more dung and the other substances used for fuel. The kiln is covered in shards of pottery to absorb the harsh heat and then sealed with water and mud. Then the potters light the fire and begin the process of smoking, which is slow, but makes the earthenware less prone to breakages. This takes 2-3 days and the temperature in the pit can go up to 900°C. Since the pots close to the fire are at risk of melting, old or broken pots are often placed closer to the flame.
Brick kilns are also used to harden pottery. The kilns used for pottery are very different from the ones used for handicrafts because of pottery’s unique requirements. The clay used in pottery has low heat conductivity, so the kilns must be able to generate extremely high temperatures very slowly, so as to not damage the pots.
The fuel is added to the designated fireplace in the kiln, which flows into the main chamber as it heats. The chamber is made from firebrick and its shape depends on the type of fuel used in baking. The fireboxes used also vary according to the form of pottery. The excess gases from cooking then exit via the chimney.
Two types of brick kilns are used in pottery– periodic and continuous. The former has a low construction cost and has more flexible usage. The units are small, so they are generally used by artisans. However, it consumes large amounts of fuel, has uneven heating and the repeating heating and cooling of the kiln has a damaging effect on the bricks. Due to these reasons, continuous kilns were invented. Their advantages far outweigh the disadvantages, however, most artisans cannot afford continuous kilns.
Pottery making involves working with clay, which is a natural resource that is abundant and renewable. However, there can be material waste in pottery making at various stages of the process. specially during the firing stage, pottery is heated to high temperatures to harden it and make it durable. However, not all pottery survives the firing process. Pieces may crack, break or explode due to various factors such as air pockets, uneven drying, or temperature fluctuations. This can result in waste material that cannot be salvaged.
There is very little information on the history of Khavda, in particular. However, we know that Khavda lies in the Rann of Kutch and there are numerous historical records which discuss the glorious past of this region, of which Khavda is a small but integral part.
Indus Valley civilisation: The Indus Valley civilisation flourished between 3300-1450 BCE. Many archeological sites dating back to the period have been found in Gujarat, Punjab and Sindh. Of these, Dholavira, which is located in the Rann of Kutch too, is one of the most prominent ones. The site at Dholavira was excavated between 1990 and 2005. Numerous urban structures, ornaments, gold, silver, bronze vessels, terracotta figures and pottery were excavated from here. Other sites located in the Rann of Kutch which bore evidence of occupation during the Harappan civilisation are Surkotada, Desalpar Gunthi, Pabumath, Kanmer and Shikharpur.
Early history (325 BCE to 640): Kutch’s early history is marked by tribal settlement and is accounted in the historical works of Greek scholars who wrote about India. Between 320 and 142 BCE, Kutch was ruled by the Samad tribe. Greek scholars describe the land as one in which there is an abundance of water. Between 142 and 124 BCE, Kutch was ruled by Menander I who was a Greco-Bacterian king. Around 120 BCE, his kingdom was toppled by the Sakas who set up camps in various parts of North Gujarat. The Sakas were defeated by Chandragupta II. However, the rule of the Guptas was short-lived and around 56 BCE, the Sakas returned. Under the leadership of Yeukaotschin, they governed the area till the 1st century CE. The Sakas were succeeded by the Indo-Parthians.
Then between 140 and 380 CE, Kutch was governed by the Sah kings of Saurashtra. Then, the region was briefly administered by the Guptas and later, at the end of the 5th century CE, it came under the Maitrakis of Vallabhi.
8th century CE- 13th century CE: It is believed that in about 714 CE, Kutch was ruled by the Charans. The Charans are a family group native to Sindh, Balochistan, Gujarat and Rajasthan. Later, the region came to be ruled by a string of administrators. First, the king of Alor followed by the Kathis and then the Chavda dynasty. About 942 CE, the last king of the Chavda dynasty captured more than 900 villages in Kutch and declared Morgadh as its capital. The Chavda dynasty continued to govern the area for successive years until the death of its last king named Punjaji. Punjaji’s reign is dated to end in the latter half of the 13th century.
Even though the Chavdas ruled the Kutch region for a considerably long period, their reign was not without incursions. In the 10th century, the Chavda rulers’ territory was briefly captured by invading forces. Arabian pirates began to raid, loot and occupy parts of Sindh and then proceeded to Gujarat. In his records, eminent historian Al Biruni has mentioned Arabian pirates invading Kutch and Somnath. In the first quarter of the 11th century, the Chavda rule in Kutch faced another disruption. This time, the Chalukyas came to power in the region under the leadership of Jayasimha Siddharaja. His dynasty continued to rule Kutch until the end of the 13th century.
During these brief incursions, the Chavda kings possessed power over only a few villages in Kutch. They became chiefs of certain forts and paid tribute to the bigger powers. The Muslim Samma tribe from Sindh and the Vaghelas from Gujarat are examples of two such empires to whom the Chavda kings paid tribute.
Jada rule/ Jadeja rule (1365-1500): The Jadejas were a sub-clan of the Sammas of Sindh and rose to prominence in the mid-14th century. Even though the Sammas were Muslims, the Jadejas were half-Muslims and half-Hindus. The first of the Jadeja rulers was Lakha and his four grandsons divided his territory into four parts, each ruled by one of them. The successors of these four grandsons continued to rule their territories independently. In 1410, Muzaffar Shah I, the first ruler of the Gujarat Sultanate took over many territories in Gujarat. However, he failed to capture Kutch and the territory remained independent until 1472. In 1472, the tribes occupying the Kutch region were defeated by Mahumad Shah I. The Gujarat Sultanate reigned in Kutch till the 1530s and introduced Islam to Kutchis. He appointed Kutchi chiefs to govern the area on his behalf.
Kutch State (1538-1697) | Khengarji I (1548-1585) : Khengarji I was a descendant of Othaji, one of the four grandsons of Lakha. Khengarji I joined Mahumad Shah I’s royal army and became one of his closest aides. During a hunting expedition, he killed a lion who was attacking Mahumad Shah I and saved his life. Consequently, the sultan was impressed and agreed to bestow him with a hefty reward. The young boy asked the royal sultan to give him the territory of Morbi to govern and also present him with the title of Rao. The sultan gave him both and also provided him with a small army. Khengarji ruled from Morbi and in 1548, he attacked the ruler of Kutch who had killed his father. He won the battle and took over the territory. He wanted to establish his kingdom at Bhuj but the land was ravaged by dacoits. After numerous attempts, he successfully drove the bandits away and established his capital there. Khengarji I is recognised as the first official ruler of the Kutch state.
Bharmalji I: Khermalji I was succeeded by his son, Bharmalji I in 1585. During Bharmalji’s time as an emperor, the Sultanate in Gujarat was toppled by the Mughals. When the Mughals came to power, they defeated Khermalji I in two battles at Dhrol. He agreed to pay tribute to the Mughal emperor Akbar in exchange for his kingdom. In 1617, the king went to Jahangir’s court in Ahmedabad to pay tribute with 100 Kutch horses, 100 gold coins and 2000 rupees. Impressed by the grandeur of the gift presented to him, Jahangir gave him a horse of his own, two elephants and other precious items. He also agreed to free Bharmalji from the practice of giving tribute and allowed Muslim Kutchis to visit Mecca freely.
Pragmalji (1698-1715): Between these years, Kutch was ruled by Bharmalji successors without any incursions or breach of peace. The last of these rulers was Rayadhan who was succeeded by his third son, Pragmalji. To seize the throne, Pragmalji killed his elder brother, Ravaji. He placed Ravaji’s son, Kanyoji, incharge of Morbi. Morbi continued to be ruled by Kanyoji’s descendants. Pragmalji died in 1715.
Godji (1715-1718): Pragmalji was succeeded by his son, Godji. Godji’s reign was quite uneventful and he died in 1718.
Deshalji (1718-1752): Godji’s son Deshalji became king upon his death. During this time, Kutch was administered by small chiefs who paid Deshalji tributes. Deshalji had been successful in maintaining an amicable relationship with these chiefs. Kutch too, had remained free from attack due to Jahangir’s friendly overtures. However, in 1718, the then Mughal emperor Farrukhsiyar decided to overrule Jahangir’s decision. He withdrew the empire’s force from Kutch. In 1721, Nawab Kesar Khan attacked Kutch but was defeated badly. Devkarn Seth, an eminent minister who had planned the attack against Nawab Kesar Khan was given a majority of the duties.
Lakhpatji (1752-1760): Upon his father’s death, Lakhpatji took over the kingdom of Kutch. He officiated Devakrn’s son Punja as minister. Under Lakhpatji’s rule, Kutch came to be known as a prominent sea trading port. In fact, Kutch even initiated the exchange of its own currency known as Kutch Kori. This currency remained in circulation until 1948.
Godji II (1760-1778) : Lakhpatji’s son Godji II came to power after his father’s death in 1760. He refused to recognise Punja as his minister and sent him to Sindh. In Sindh, Punja became a close confidante of Raja Ghulam Shah. Being adequately familiar with the battle strategies and geography of Kutch, he convinced the king to invade it and marry Godji II’s sister. Accordingly, Ghulam Shah invaded Kutch and defeated Godji II’s army. Punja negotiated with Godji II and asked him to marry his sister to the Sindh ruler. Simultaneously, he persuaded Ghulam Shah to return to Sindh. While Godji II did not agree to the marriage of his sister to Ghulam Shah, he married off one of his chief’s daughters to Shah.
In 1775, Sarfaraz Khan who was Ghulam Shah’s son, planned to invade Kutch. He travelled through Khavda and when he reached Bhuj, he heard stories about the marvellous strength of Kutch’s army and then, decided to withdraw.
Godji II died when he was 44 and the kingdom passed into the hands of his son, Rayadhanji III when he was only 15 years old.
Rayadhanji III (1778-1786): When Rayadhanji III came to power, the kingdom of Kutch had fallen into disrepair. Battles had exhausted the royal treasury and internal strife was abound. An attempt to assassinate the king was even made. A number of chiefs who controlled territory within the state declared their independence. The royal army’s chiefs known as the jamdars overthrew Rayadhanji III and his chief, Meghji Seth came to control the state of Kutch.
Prithivirajji (1801-1813): Rayadhanji’s younger brother Prithvirajji was appointed as king. He introduced the concept of Bar Bhayat ni Jamat- a 12 person council that would debate and discuss administrative decisions related to the state. One of the council members named Fateh Muhammed was instrumental in bringing peace and order to Kutch and ensuring that Prithvirajji’s authority was obeyed to. In 1801, Fateh Muhammed retired and was appointed as chief of Bhachau. Prithivirajji’s reign was carried forward by one of his ministers, Hansraj.
Rayadhanjji III (1801-1813): After his younger brother passed away, Rayadhanjji planned to topple Hansraj and become king again. However, his plan was foiled and he was kept under control by Hansraj. The minister agreed to release him on the condition that he be satisfied with being a minister and must not attempt to become king again. Rayadhanjji III passed away in 1813.
Bharmalji II (1814-1819): Bharmalji II was Rayadhan III’s son and succeeded him to the throne after his death. Between 1815 and 1816, several British troops moved in the area and began capturing the raja’s territories. It was agreed that the Kutch state would exist only under British suzerainty.
British control over Kutch state (1819-1948)
Kutch became one of the first regions to become part of an independent India. Vijayraji’s son, Madansihnji, signed the Instrument of Ascension on 16th August 1947. Madansinhji became the ruler of the princely state and on 26th January 1948, he became the last raja of Kutch. Soon, the empire disintegrated and it became a part of the Union of India.
The village of Khavda is located in the north of Bhuj Taluka in the Kutch district of Gujarat. It is famous for its white deserted dunes and the Banni grasslands. Located at a distance of 70 kms from Bhuj, the village has a land area of 774.35 hectares. Khavda is located at 23.85°N 69.72°E. It has an average elevation of 1 metre(3 feet).
It is known for the crafts of pottery, leather, and ajrakh block printing. It is also a popular tourist destination because of flamingos that migrate to the area every winter. Kutch is a desert area, with land that is replete with salt and salt stones, instead of sand. It is infamous for its earthquakes that have an adverse effect on the land, water bodies, and its mineral resources. The earthquakes have changed the course of rivers in Kutch, because of which the land is largely barren. Due to this, the residents of Khavda taluka mainly earn their livelihood from pastoral works and making handicrafts. A port site nearby called the Nani Rayan, was a gateway to international trade. Since goods from there often crossed the Khavda taluka, some of the potters had access to the trade market. This is apparent in the Western Iranian influences seen in Khavda pottery.
Presently, agriculture is the main occupation of a majority of the population in the village. Farmers grow peas, millets and pulses.
Khavda is also located nearby the Banni grasslands reserve which is a grasslands habitat that surrounds the Rann of Kutch region. These grasslands experience arid weather but support a host of animals. Earlier, the river Indus used to flow through these grasslands and therefore, they were quite fertile. However, due to the earthquake of 1819, the Indus river changed its course and the grasslands became dry.
Khavda experiences hot weather for a majority part of the year. Average precipitation in Khavda is quite low and winters are not very cold either. January is the coldest month in the village with a maximum temperature of 26 degree celsius and a minimum temperature of 16 degree celsius. On the other hand, May is the hottest month in Khavda with temperatures soaring up to 38.9 degree celsius. In the monsoon months too, Khavda experiences considerable heat- maximum temperatures remain in the 30s.
As is characteristic of rural areas in India, Khavda experiences poor connectivity due to a lack of sound infrastructure. Bhuj, the nearest town, is approximately 70 kms away. While Khavda does have a handful of educational institutions and medical centres, most are government owned. For private higher education and specialised training, students from Khavda must travel to Bhuj. Amenities like tea shops and grocery stores are also present in the village. Private and public bus facilities can be availed by residents to travel within the village. However, Khavda does not have a railway station. One must travel to Bhuj to board a train. While commercial banks and agricultural credit societies exist in Khavda, one has to travel at least 10 kms for an ATM facility. Therefore, from the above information, it becomes amply clear that Khavda is lacking in infrastructural amenities and the government must develop accessibility to and from Khavda.
Virtually no academic information or in-depth studies are available on Khavda architecture. One thing, however, can be said about the matter. Earlier, people used to live in kaccha houses made with mud. But increasingly, due to awareness surrounding the vulnerability of the place to earthquakes, people are replacing kaccha houses with pakka houses. Pakka houses are made of bricks and cement. One feature of a typical Khavda house is that the fence wall is attached to the side wall of the house and is made out of cement.
Arts and crafts are intrinsic to the culture of Khavda. Deemed as a handicrafts town, Khavda is popular for its pottery, leatherwork, textile goods and handmade dolls. Besides this, the Rann of Kutch festival truly encapsulates the authenticity and flavour of the people, culture and heritage of Kutch, which Khavda is a part of.
Khavda village lies in the Bhuj taluka of Kutch district. Kutch has a rich historical past and cultural heritage. Most people in the region speak Kutchi or Gujarati. The Kutchi language used to have its own script but it has since gone extinct. Since rearing animals for milk was conventional one of the most prized occupations of the Kutchi people, offering milk to one another is viewed as a sign of respect. Folk music, folk art and dance lie at the core of Kutchi culture. Every year, a significant number of festivals are held in the Rann to protect, preserve and propagate Kutchi culture.
Khavda population is a mixture of different communities, mainly, the Meghwal Hindus and Muslims who migrated to Kutch from Sindh several years ago. Due to its arid weather and low connectivity, Khavda is home to only 885 families. The total population of the village is also quite low and stands at 4062. Of these, 2104 are males and 1958 are females. The sex ratio is 931 which is higher than the state’s average of 890. In Khavda, the total literacy rate is 52.45% and is considerably lesser than the state’s literacy rate of 78.03%. More than 15% of the population falls under the Scheduled Caste category and less than 2% come under the Scheduled Tribe category.
Traditionally, buffalo-rearing has been the most common occupation for the people of Khavda. Since the region is quite arid, it does not support heavy agriculture. Moreover, buffalo rearing was seen as an enticing occupation as it provided financial and nutritional security. Today, however, people are turning towards other occupations mainly, labour to sustain an income.
Primarily known for its unique and age-old Leather, Embroidery & pottery-making
List of craftsmen.
Team Gaatha
http://www.asanjokutch.com/content/geography.asp?main_cat=geography
https://www.stringsofheritage.com/khavda-pottery-from-the-indus-valley/
https://www.outlookindia.com/outlooktraveller/see/story/68888/khavda-painted-pottery-in-rann-of-kutch
http://nopr.niscair.res.in/bitstream/123456789/47078/3/IJTK%2018(2)%20325-332.pdf
https://books.google.co.in/books?hl=en&lr=&id=gdicUXyC0BwC&oi=fnd&pg=PR10&dq=origin+of+pottery+in+india&ots=ed_smI5XrP&sig=sHx3LLp2sjn4eEqsE5GrpDaiup8&redir_esc=y#v=onepage&q=brick&f=false
https://books.google.co.in/books?hl=en&lr=&id=aqrB_Nzr5QcC&oi=fnd&pg=PA4&dq=brick+making+history+and+pottery+in+india&ots=VEn8s8KuDQ&sig=5GVkyLD7ER5xAf3x_VNlMUAijeE&redir_esc=y#v=onepage&q=brick&f=false
http://www.ecobrick.in/BrickMakinginIndia.aspx
http://lib.unipune.ac.in:8080/jspui/bitstream/123456789/4630/11/11_chapter%203.pdf
https://researchonline.rca.ac.uk/1640/1/Maham%20Anjum%20MPhil%20by%20Project%20-%20Ceramics%2016%20June%202014.pdf
https://www.researchgate.net/publication/324530907_REGULATING_BIO-INVASION_IN_BANNI_GRASSLANDS_IN_KACHCHH_GUJARAT
http://www.travelresponsibly.info/publications/responsible_tourism_volume_2_issue_4.pdf
https://timesofindia.indiatimes.com/travel/destinations/arty-affair/as74510819.cms