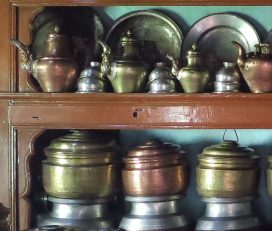
Copper Craft ~ Chili...
Copper and brass have played a significant role in fulfilling these needs. Even today, in most traditional Ladakhi kitchens such utensils are commonly seen
Chiling Sumda...
Soft wood spins on the lathe from morning to twilight, metamorphosing into beautiful objects and shapes. The art of making Lacquer ware is a thriving traditional craft, once reserved to royal patronage, it quickly found its place in crafting various items of both decorative and functional uses.
The craft produces a wide range of products due to its versatility like toys, pipes, masks, doors, bangle-stands, window frames, wooden memorials, flower vases, bedposts and cradle posts etc. Small decorative and ceremonial stools used in marriages are also made. The smaller items are made more often and are in much demand.
The craft has been functional for nearly a century. It was once practiced to entertain the likes of the Baghelkhandi kings and gained popularity amongst the masses. Soon it became a profitable profession and flourished.
Sir George Watt in his famous dictionary of 1908, ‘Commercial products of India’ has described the uses of Lac. In his observations he talks of how Lac entered into the agricultural, commercial, artistic, manufacturing, domestic and sacred feelings and enterprises of the people of India. “This craft provided substantial income to the communities living in the agricultural and forest tracts. The labor was also aptly divided as every village had its carpenter, turner and shoemaker etc. who used Lac in some form or the other. Lacquer ware is used by the rich and the poor, its versatility spans across the various sections of society. The tribal people collect Lacquer from the forest and smear it on carved bowls.-
Pure Lac used on wood gives it sheen but when mixed with color, it brings out vibrant, sleek shades. Lacquered wood is used to make a variety of objects like toys and canes to even bedsteads. Lac in India is different from that of the rest of the places because it is obtained from resin produced by insects rather than the sap of the Khus tree.
The Lacquer industry can be divided into three categories based on the scale of production:
– Independent workshop units : Family members, including children work on the craft and the whole set up is complete with a few lathe machines (hand operated or motor driven). They work in their homes or small workshops constructed nearby. They market their goods in the local Bazaar on their own or cater to bigger traders.
– Small scale enterprises : Around 4-10 lathes are set up in the artisans’ house. The master craftsmen hire other artisans who are paid on ‘piece’ basis. This setup forms the enterprise, which sells their products to the exporters. The profit margin for the artisans is less as they work through agents who are usually government agencies, which levy heavy taxes and commissions.
– Medium scale industries: Run by exporters in large cities with large profits. They employ artisans to craft products of desired quality. There is a strict focus on quality to bring about a mandatory flawlessness. These industries are open to new ideas and designs.
Lac makes its appearance in texts as ancient as the Vedas. The Lakshataru or the Lac tree is a well known feature. It appears in the story of the notorious Lac palace built by the Kauravas to execute a plot to eliminate Pandavas in an episode from the epic Mahabharata.
One of the oldest written veda has A small chapter is devoted to the Lac insect in Atharva Veda. Ayurveda stresses the importance of Lac in medical therapies. In recent history lacquer and woodwork crafts are believed to be practiced for more than 300 years. The traditional craftsmen are called ‘Vishwakarmas’, meaning creators of a universe of structures. In recorded history of India, Lac was first mentioned in ‘Ain-i-Akbari’ by Abul Fazl in 1590 AD. Lacquer ware flourished in the subcontinent due to the Mughal court and patronage.
This craft is practiced in many parts of India today, the notable places being Karnataka and Madhya Pradesh. The commonality of the craft led it to being used for most utilitarian objects, which were used for bartering and sharing with relatives or the community. Since the purpose was such, the products were of high quality, made with a precise finish in view. This has substantially led to the clean, smooth and compact look of the products. The process adds liveliness and colors to the objects as well as makes them more durable. India is one of the largest producers and principal exporter of Lac. The need for embellishment without diversion in functionality led to the wide demand of Lacquer ware. Lac is also widely used in food processing, textile, leather, cosmetics, varnish and printing industries. Being biodegradable and eco-friendly it gained further acceptance.
Hand-Lacquered objects have a distinct look to them, making them stand apart from that varnished with acrylic or oil paints. Four main colors are used in the process – yellow, green, red and silver grey. These are also mixed to make various other shades. Traditional designs along with the ones put down by various government organizations, which bring in designers to aid the craft are being used.
The influx of cheap plastic and rising prices of wood has left the craftsmen with low returns on their expertise and hard work. The craftsmen tried to incorporate the bright fluorescent colors of plastic in their Lacquer products to keep the customer interested. This led to a crucial decision of creating products which would be valued for their craftsmanship and not the amount of raw material used in them, as was the case in the earlier days. Owing to no change in the designs of the products over the years, the craft has reached a point of stagnation. Fresh inputs from young designers are required to meet the new demands and specifications of the export market.
Lac : Crimson red, plant eating, tiny insects such as Laccifer Lacca, Carteria Lacca and Tachardia Lacca colonize the branches of selected species of host trees and secrete a natural scarlet resin known as Lac. Later the different layers of resin residue on the coated branches of the host trees are scraped off as long sticks known as ‘Stick Lac’, crushed, sieved and washed several times to remove impurities till it shows up in natural red color.
The highest quality Lac is referred to as ‘Button Lac’ as it is in the button form. It is light and golden colored and can cost up to Rs 400/kg. The second is a medium brown color and sells for Rs 350/kg. The third, poorest quality Lac is dark black and sells for Rs 250/kg.
Wood : Sourced from the surrounding forests. Sagwan/Teak was used earlier but since the availability dwindled, the craftsmen shifted to locally available ‘Dudhi’ wood, which is much softer. Others are Bija, Gamir, Sarai and Kadamb.
Keware ka patta: These are leaves of Talegari or Screw pine which are used for polishing.
Natural dyes: These are used to impart color to artifacts, Sheopur Laquer ware is known for its striking colors.
Artificial colors or acrylic paints: Due to easy availability of artificial color imparting substances, craftsmen also use them at times. They can be procured from the local market easily.
Chapdi/Wax: The wax procured from Rajasthan and Balrampur is called Chapdi, this wax is utilized for better finish.
Chandrak : It is the local varnishing agent which enhances the sheen of artifacts.
Kewda oil : Locally procured oil is used for better fragrance and finish in the final product.
‘Patris’ is the local name for Lathe machines. The hand lathes consist of a stone and wood piece, which acts as the object holder and a bow string attachment for rotation. This is the traditional method, which the older craftsmen find easier to operate than the powered modern lathe machines. The power lathe has a head stock that consists of a revolving axle attached to two belt pulleys. The belt runs over a pulley mounted on a revolving shaft that is driven by an electric motor. These are useful for mass production. Matna, Barma, Aari, Naria, Thikra are local tools which are used for basic operations.
Preparing the Lac: The women make the Lac sticks while the men prepare the wood. Raw Lac is bought and put in boiling water for melting. It is usually light brown in color. After melting, it becomes sticky and elastic and is handled using long wooden sticks. When it becomes soft after cooling for a bit, it is put on the ground and is battered till it turns thick and solid. This takes around 15-20 minutes. This is then converted into usable sticks by cutting. The Lac with no extra color pigment gives natural color to the wood. If colored pieces of Lac are required, then pigments like oxides of iron, zinc and magnesium are added while the Lac is being battered.
Preparing the wood: The logs are cut and seasoned by storing them away from sunlight and heat, with good air circulation. The amount of time for which they are seasoned depends on the moisture content of the wood. After seasoning, the superfluous wood is removed and edges are chiseled out till the piece becomes cylindrical in shape.
Shaping the wood: The cylindrical pieces are then kept on the lathe machine and shaped using the various cutting tools to make desired grooves and shapes. When the desired shape is attained, the pieces are smoothened using sand paper.
Coloring & Painting:
Lacquering: The piece is turned on lathe and the Lac sticks of desired colors are held against it. The friction heats up the sticks and melts the color over the wooden piece. After this step, a final buffing is done using Kewra leaves which lend a translucency to the product. The piece is then cut and removed from the lathe and more ornamentation is done, if required.
The craftsmen rarely let anything go waste during the process; the wooden ships resulting from turning are either used as fuel or traded as fillers.
List of craftsmen.