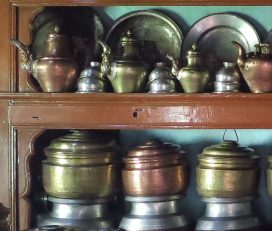
Copper Craft ~ Chili...
Copper and brass have played a significant role in fulfilling these needs. Even today, in most traditional Ladakhi kitchens such utensils are commonly seen
Chiling Sumda...
A royal marvel of the Indian textile industry is the traditional Kota Doria. The art of weaving cotton in a structured check pattern as an open weave has been passed on through the generations, the beginning of which was never recorded in written texts. The square Khat pattern gives the Kota Dori its distinct feature that differentiates it from other hand woven crafts.
Kota, a town situated in eastern Rajasthan hints at the origin or cultivation of the craft itself. The town and areas around it hosts several craft clusters that spend months delicately weaving saris known as “Masurias” derived from the possibility of weavers migrating from Mysore known by the same name. Directly translated from the Hindi word meaning “threads,” the Dori or Doria are woven with magical skill and precision, a regular visual treat.
Commonly seen on Royal heads as Pagdis, Safaas and Odhnas in the 17th century, Kota Doria then evolved into dhotis of 36 inches’ width. A significant change came when the width increased up to 46-48 inches, as a result the fabrics became suitable to drape as a beautiful Sari. What began with a simple signature check pattern took a turn with the addition of Zari (gold-or-silver-plated thread) adding a sense of luxury and royalty paying homage to the Royal family that initially adorned themselves with the Kota Doria weave.
Like many other handicrafts across the country, over a period of time Kota Doria found many applications since its origin, especially thanks to its lightweight and comfortable identifier. A wide range of fashionable garments like sarees, suits, lehengas, stoles, scarves and home furnishings are created with this weave that remain significant in today’s modern pace.
Cotton and silk act as raw material for this fabric. It is very popular for its gossamer feel, sheerness and coded texture this type of fabric is ideal for airy bright summer wear.
Furthermore, it is interesting to note that unlike other fabrics which turn brittle and get broken along the folds due to the use of silk, Kota Doria in spite of using silk it has great comfort, fall and is long lasting. People have been found to cherish their 70-year old Kota Doria saree until today. This is because of the beauty of the construction of the saree where cotton yarn is crammed together to obtain a corded feel and thus acts as a major stress receiver but the stress never gets to the silk yarn.
With their sheer look, which accentuates the natural curves of a woman’s body, and a lovely sheen, silk Kota saree have an air of subtle sophistication. With the right accessories they can be worn for either casual or semi-formal occasions.
The government has awarded a GI (geographical indication) mark to distinguish Kota Doria made on handlooms from power looms, which is visible at the corner of every hand-woven piece manufactured in Kaithoon.
The origin and name of this 200 year old fine checked fabric is shrouded in mystery and many fables surround the origin of the craft as told by the gifted weavers.
Some believe that the first Doria sarees were woven in Mysore and weavers were moved to Kota, during the late 16th century under the patronage of Rao Kishore Singh, the then-Kota Prince. Another tale recites a story of a Khatiya weaver from Kota travelling to Chandeshwari, a town in South India, to study the art of fine weaving. When he returned, the Kota durbar rewarded him handsomely for his improved craftsmanship by weaving a check pattern made up of alternate weaves of silk and cotton yarns that forms the crux of this radiant craft today.
As per another source, the tradition of this weaving has been traced back to the times of the Mughal Emperor Aurangjeb, (about 1665 A.D.), when ‘Dorias’ were woven at larges, but the tradition stayed alive only in Kaithun and its nearby villages. A textile that represents freedom and comfort ironically stayed resilient only as a source of dowry in Kaithun..
Textile experts also suggest the name refers to the finest of square checks closely resembling a Masoor lentil,disproving the notion that it originated from Mysore. Whether a staple food describing finesse gave birth to the name or skilled artisans from the South travelled North with the craft, this bright summer essential stands the test of time.
The interesting history of this exquisite craft has evolved over a period of more than 250 years. Its name as ‘Kota Masuria’ (known locally) in itself is quite enigmatic. Folklore suggests that the craft originated in Mysore and then moved to Kota where it is now based, hence the word Masuria in the name. The weavers are believed to have moved to Kota because of the patronage they received from the royal families of Rajasthan. Kota sarees were primarily patronized by the Prince of Kota and Mughal Army general, Rao Kishore Singh, who summoned the weavers from the Deccan region to Kota during the late 1600s. The art of using the open khat pattern was so intriguing that it was highly appreciated by the elite.
According to several documents ranging from State time documents to the British accounts fine cotton weaving and growing of cotton are reported, in the 13th century. Kaithun is the main weaving centre according to the records.As per the book, Sarees of India, Kota Sarees were first made when weavers were brought to Kota (Between 1707 and 1720 ) from Deccan by Maharao Bhim Singh. The weaves originated in Mysore and surprisingly one could hardly find them now at Mysore. The workers settled there and passes down the art weaving cotton in the open Khat or check structure from generation to generation. Everything is done in an age-old manner right from the setting of the patterns to graph making, dyeing of the yarn and settling of the loom. Down south it is called by name Kota Masuria. Originally made with pure cotton, nowadays synthetic as well as silk threads are also woven along with cotton threads in weaving Kota Masuria. This makes it cheaper and more durable. The traditional Kota doria is found in white colour only and one needs to get it dye in the different colour. Single colour dyeing, shaded patterns and tie-dye pattern are common with new styles coming up each day. Varieties of printed Kota doria and silk embroidered border are becoming very popular.
Since there is no precise data about the beginning of Kota Doria weaving craft, it is difficult to state in which period the craft started.
The basic design of the Kota Doria weave is simple yet intricate. A single Khat, consists of 28 yarns (14 warp and 14 weft yarns), 20 yarns are of cotton and 8 yarns are of silk. A single inch consists of 5 Khat, so there are 140 threads per inch (reed density).
Design process:
Today, both Indian and international fashion designers are incorporating a range of Kota Doria elements in their collections. These fabrics have paved their way into the ramp as well.
Bangladeshi designer Bibi Russell’s collection of ‘Kota Doria’ craft, ‘Fashion for Development’ created for the Government of Rajasthan in 2015 told the story of the time she worked with the weavers there. The bold designs were accompanied with tie and dye prints.
Traditional textiles transformed into wrap skirts, palazzos, tonal weave sarees, dhoti pants, waistcoats and kimono style covers as she gave a heritage twist to women’s wear. Her menswear line featured leheriya, kurtas, jackets, sherwani, dhoti, and cuffed trousers. The look was completed with traditional Rajasthani jewellery.
The use of Kanjivaram designs on Kota Doria fabric has increased its demand especially in South Indian states as they have proven to be a comfortable wear in the hot and humid climate down south. Apart from renowned designers, National Award-winning Master weavers of Kota Doria from Kaithoon have also showcased their sarees in fashion shows.
In recent years, Kota Doria sarees have become more design and zari intensive, giving it a luxurious edge leading to more celebrities endorsing the craft. Recently Viranica Manchupure, the Tollywood actress was seen in an elegant zari tissue Kota Doria sari woven in Paithani style. Paired with a hand embroidered floral blouse with intricate zardozi detailing.
Today if you search for ‘Kota doria’ on the internet you will find many sites selling the fabric, saree, dupatta etc. but most of those products are power loom copies. Today, a community of 5000 weavers living in Kaithoon and other small villages (near Kota City), who are mostly women, face cut-throat competition from synthetic power-loom copies, which are cheap in price as well as quality. This is unfortunate as many people who buy Kota doria now-a-days are hardly aware about the authentic handloom fabric and its unique story that lends to its cost worth every rupee. Artisans are struggling to maintain a livelihood as knock-off copies flood the market directly targeting unassuming consumers.
Remunerations are not at par with the labour involved in weaving Kota Doria sarees, resulting in vanishing art and artisans. The decline of native enterprise, the unavailability and rising cost of raw material and competition from power looms are some of the many challenges faced by the hand-woven Kota Doria.
Hence, the protection of the original Kota Doria is the need of the hour. Apart from all the above points noted. There are several issues weavers face personally everyday:
The process of weaving is supported by a number of activities like pirn winding, warping, dyeing, sizing, and so on. Experience artisans are involved in weaving process. The spinning, dyeing and weaving processes, are done by adept artisans only. To weave out these super transparent, light textured and weightless sarees, the artisans fabricate strong cotton or cotton-silk yarns.
Cotton and silk, two major raw materials are bought from traders who source it from different part of the country.
• Cotton– Cotton yarn comes in the form of hanks and 150m of mercerised cotton hanks costs Rs. 60 to Rs. 65. Cotton comes from Ahmedabad and other parts of Gujrat, it is also sourced from Coimbatoor,
• Silk– Silk costs Rs. 4000 per Kg and is sourced comes Bengaluru.
• Zari– is sourced from Surat, which costs 1500 per pack, It takes around 250gms of cotton and silk yarns each to weave a simple Kota Doria saree.
• Dye is sourced from local market.
Parts of pit loom
• Tur – it is the wooden beam at the end where weaver sits at the pit loom. Woven fabric is rolled on it as it gets completed
• Khanfati – thin wooden piece used to stretch the fabric as it gets woven.
• Hath-Rail (reed) – wooden comb, made in Banaras, used to beat the weft yarn.
• Pani – Comb-like structure inside the hath-rail, made of bamboo found in Banaras.
• Raanch – interlaced net through which warp yarn passes through.
• Hatha – Small metal bat used for extending warm yarns from the thread reel holder
• Pinjra – Thread reel holder for warping purpose
• Sua – heavy metal needles used as weight for different coloured threads for making motifs inserted through weft.
• Shuttle – thread reel holder to insert weft thread.
For Sizing process:
• Kamri – the wooden stand used for spreading cotton yarn for the sizing process
• Gholni – Wild bamboo grass broom used for mixing the starch
• Kuchi – Heavy brush used for applying the starch evenly on the cotton yarn
Design setting: the setting up of design on the jala of the loom is also a specialised activity and so is that of making the graphs for the designs. Dobby is mainly used for ground motifs and in some instances for the pallu also. On the other hand, jacquards are being used for making exquisite borders of the saris. The method of using small spindles, locally known as tillis for making the motif on the ground/pallu/ border of the sari makes the designing process quite lengthy but at the same time provides such a fine effect, which is not noticed in any other handloom sari easily.
Designing on Kota Doria Fabric during the course of weaving is an art in itself and the kind of adjustments that are needed in the motifs/pattern so as to take into account the differential picks and ends at different parts of the base fabric (owing to the Khat pattern).
To add motifs and design pattern along with weave, small spindles (tillis) for each coloured thread are inserted in the weft direction, by lifting the warp yarns, which are marked as per the design graph sheet, through hooks. The spindle of coloured thread is weighted down with heavy needles (sua) hanging from each thread. This method is used while weaving using a simple pit loom, it is time consuming and tedious at the same time, requiring a lot of skill.
The various gadgets prevalent for the extra-weft designing currently in use are Jala, dobby, and Jacquard. Design pattern are punched through holes on rectangular cardboard pieces and inserted in the Jacquard loom from left side. As the pattern changes in the saree during the weaving process the weaver pushes paddle to shift the hole-punch cards and lift the correct warp yarns. Hence, the weaver saves a lot of time while making intricate motifs on the Jacquard loom, but it requires enormous skill.
The mechanism involved the use of thousands of punch cards laced together. Each row of punched holes corresponded to a row of a textile pattern. The loom is programmed by a chain of punched cards. Each card controls single throw of the shuttle. To produce a new pattern, the operator simply replaces one set of cards for another.
Following is the process of making this punch card:
• Design draft is initially made on graph in the same way as used for a pit loom.
• Squares (smallest unit in graph) covering the motif are counted on the graph paper
• An actual single Khat is represented as a ‘Dor’ on the graph,
• Size and shape of the motif is calculated in terms ‘Dor’
• Single ‘Dor’ represents one punch hole on the jacquard punch card
• Then a single motif is calculated as number of ‘Dors’
• This calculation is done on the graph, which is handed over to the punch-hole card maker, who punches ever card manually, with a thick iron needle and hammer.
• For eg. A 6-inch-wide design border on a saree consists of 10 ‘Dors’ ie. 100 square grids on the graph and to cover the entire length of the saree no. of such units (10 Dors) required are calculated and that will give the number of such punch cards to be produced and insert in the loom in order to repeat the pattern for the entire saree length.
Work starts at 5 am in morning after breakfast and namaaz. Typical working hrs 8-12 hrs. As in the other old weaving clusters across the country, the loom never rests in Kaithoon. One or the other family member is always at work; one reason being the tedious nature of the process.
1. Design:
a. The designer is sent a digital picture of the design to be made
b. He then scales the design on a graph paper as per the requirement of the saree
c. the curves in the scaled drawing are adjusted to the grid of the graph paper, to visualise the exact placement and shape of the design. Then the final colour scheme is decided by meeting with the master weaver.
d. the drafting of design usually takes 2 days to complete, but can also take upto 6-7 days for an elaborate pattern.
Preparation and Weaving The production process of Kota Doria is quite unique and traditional. The various steps involved in the production process are:
2. Preparation of yarn: Winding
Cotton and silk act as raw material of Kota Doria. Raw materials obtained from Ahmedabad and Surat in the form of hanks. Pirn winding is a type of winding. It is a process of transferring the yarns from the hanks into spools of the shuttles used in the weft while weaving. This process is done using indigenously made ‘charkhas’.
3. Warping is the process of getting a predetermined length of warp having desired number of threads as required for the whole width of the fabric. The warping method generally being used for Kota Doria is known as Peg Warping (also known as ground/street warping), since wooden pegs are used in the process. A pinjara (thread reel holder as shown below), is filled with thread reels and as per the no. of yarns required in the warp, then each yarn is manual tied to the hatha, (kept near the feet). This is done for preparation of the next step where the hatha and the pinjara is taken outside.
These wooden pegs locally called pinjaras and are placed along the whole length of the yarn so that continuously criss-crossed set of two yarns may be obtained by the weaving process. (The criss-cross later on helps in finding out the broken yarn on the loom during the course of weaving). These wooden pegs are placed below a thick rope tied to a pair of iron pegs on each end and it is the length of the rope that determines the length of the warp being prepared. Presently this length is 40 m, keeping in mind that a time 5 saris are woven on a loom.
4. Dyeing:
Dyers dye both silk and cotton yarns. Generally, direct dyes are used owing to their easy use and good retention on silk as well as cotton. Apart from direct dyes, wet as well naphthol dyes are also used occasionally.
a. the yarn bunch is washed in a solution of detergent and water
b. direct dyes are added to boiling water on a stove in case of cotton, in case of silk direct dye is added to warm water with acetic acid.
c. Once the correct shade of dye is prepared cotton hanks are added in the dye pool and circulated in the solution with help of two metal rods
d. The cotton hank is left in the dye solution for a few minutes and the vessel is removed from stove.
e. Silk yarn is left in the dye solution for 10-15 min. and then removed
f. Lastly silk and cotton yarn are both added in a dye fixer solution and dipped 4-5 times delicately.
g. Dyed hanks are then hanged to dry all day.
5. Sizing
Sizing is done for imparting the yarn enough strength, surface glaze and stiffness so that it can withstand the beating the reed during the weaving process and also maintain the stiffness necessary for even weaving process and a proper look of the sari one the weaving is complete. Wild onion is used for preparing the starch as it is better than rice as it avoids any insects. The process of sizing is unique as practiced in Kota Doria and is important since no post – weaving finishing of the fabric is done by the weaver.
Sizing process (Charakh), is done in the city of Kota, and is practiced since more than 100 years by The Kohli community or The Kataiya. The Masaan area (Royal Cremation ground) for the process was provided by the Royal family of Kota to this community to perform their work as it required a large open area which is free of dust and other pollutants. Following is the sizing process step-by-step:
a. The cotton yarn is first spread lengthwise with help of a wooden sticks stand called (Kamri)
b. Wild onion (grown in the nearby forest area and only grows in monsoon season) which is used for the preparation of starch is first boiled and then grinded on a plate called (gholni), into a paste and mixed in water, which results in a thick white paste.
c. Before applying paste to a 2.5 kg, brush called (Kuchi), oil is applied.
d. The cotton yarn is then beaten with a stick to shed off any dirt stuck.
e. Then the starch is applied on the yarn with the help of the brush, with a back- and-forth rhythmic action, which is repeated till the starch sticks to the yarns and is completely dried up.
Cotton yarn as long as 5 sarees is provided to the workers by the weavers from Kaithun, which takes them 2-3 hrs to complete and they are paid 200 rs. For the same.
6. Preparation of the loom:
a. Drafting: the process of passing the yarn through the healed of the loom as per design to be woven
b. Denting: the reed, a comb-like structure locally known as ranch, filled with the yarns by skilled craftsmen on their own or through the men adept at this skill. The reed is made of a special variety of bamboos found only near Banaras.
c. Piecing: the addition new yarn to the left-over yarn in the reed to continue weaving.
The loom setter, prepares the loom by setting threads in warp direction manually, by checking the graph paper designs for motifs and colour placements of yarns. It can take from two hours to five hours to set up a loom, depending on the designs.
7. Weaving
Weaving of Kota Doria involves a simple pit loom that can be erected by the local carpenters of the villages and the technique of weaving is quite traditional, i.e. the throw shuttle technique wherein no gadgets are used for the to-and-fro motion of the shuttles along the width of the fabric. this provides a lot of flexibility to the weaver in controlling the design and also the beating of the reed to achieve the ‘khat’ pattern. It is the fine skill of the weavers of this region that structural pattern is created in Kota Doria fabric with just two pedals, the square check pattern, the ‘khat’. While the cramming of the yarns is mechanically achieved in the reed for the warp way, it is the only inherited skill of these weavers that helps them throw silk as well as cotton yarns double and keep the silk yarns lightly beaten to evolve the square check. The characteristic square – check patterns can be numerous with different ratios of cotton and silk yarns as necessitated by the structure required. Thus, for a 300- khat pattern, there are 14 yarns in a ‘khat’ wherein 8 are of cotton and six are of silk. Some more typical designs and motifs are made using Jacquard loom, which saves more time but requires more skill.
• Estimated 1’ – 3” of cotton and silk yarn is taken extra for setting up the loom, which is used tie ends for continuation.
• Dye baths prepared for dyeing are disposed-off after dyeing a single batch of yarn hanks.
Kota was previously known as ‘Kotah’. Even today, you can find many websites & texts using the name ‘Kotah’ instead of Kota. The city of Kota was once a part of Bundi kingdom.
Foundation of Bundi & Hadoti: The history of the city dates back to the 12th century AD when Rao Deva, a Chauhan Rajput chieftain belonging to the Hada clan conquered the territory and founded Bundi and Hadoti.
Hadoti region today consists of 4 major districts – Kota, Baran, Bundi & Jhalawar.
The Legend of Kotiya Bheel: It is believed that a powerful Bheel clan once ruled in this area during the 12th century. The ruined fort at Akelgarh along the bank of Chambal River is only a few kms from Kota. It speaks of a bygone era when the Bheel Chieftain Kotya ruled the nearby areas from this small fort. It is believed that Bheels ruled this area for many years. Some say that Kota owes its foundation to the Kotiya Bheel who more than 800 years ago laid down a small fortification at Akelgarh, it’s protective wall stretching till Retwali.
Battle Between Jait Singh and Kotiya Bheel:The 13th century had witnessed many battles between Hadas, who were ruling the Bundi Kingdom & Bheels. In one such battle, Jait Singh of Bundi defeated Kotiya Bheel and laid the foundation of Hada clan in Kota after capturing Akelgarh fort.
If historians are to be believed, Jait Singh was so impressed by the bravery of Kotiya Bheel that he named his newly conquered principality Kotah after him. The present day Garh palace is where the chieftain’s severed head was buried and it’s where he is still honoured & remembered daily.
Now, there have been disputes whether Kotah was named after Kotiya Bheel or not. Some sources say Kotah was not named after Kotiya Bhil, instead it came from the Hindi word ‘Kot’ which means fort in English.
The foundation of Kotah started with the building of a fort which presently is Kota Garh Palace and that’s how Kotah got its name, some suggest.
Princely State of Kota: It is only in the early 17th century when Kota as an independent state became a reality. The ruler of Bundi, Rao Ratan Singh gifted the smaller principality of Kotah to his favourite son, Madho Singh. Because of Madho Singh’s military service to the Mughal empire, Shah Jahan confirmed the Jagir of Kotah to Madho Singh.
Maharao Bhim Singh & Zalim Singh:Maharao Bhim Singh and Zalim Singh are two remarkable names in Kota’s history. Maharao Bhim Singh held the ‘Mansab’ of five thousand and was the first one in his community to get the title of ‘Maharao.’
Zalim Singh was a diplomat and statesman who served as a regent to the kingdom after the king’s demise which left a minor on the throne. Under his administration, Kota prospered & grew in power & size. Because of his leadership skills, Kota was the first among the Rajput states to sign a treaty of friendship with Britishers in 1817 Zalim Singh further strengthened the state’s army by bringing in new weapons, tactics and revenue system. With all of this, Kota became a cradle for Rajput power, folklore and culture.
Kota is located along the banks of the Chambal River on a high sloping table and forming a part of the Malwa Plateau, in the southern part of Rajasthan. It is the 3rd largest city of Rajasthan after Jaipur and Jodhpur. The cartographic coordinates are 25.18°N 75.83°E. It covers an area of 221.36 km2 (85.47 sq mi). It has an average elevation of 271 metres (889 ft). The district is bound on the north and north west by Sawai Madhopur, Tonk and Bundi districts. The Chambal River separates these districts from Kota district, forming the natural boundary. The comparatively rocky, barren, and elevated land in the southern part of the city descends towards a plain agricultural land in the north. The Mukundara hills run from southeast to northwest axis of the town.
The craft of weaving Kota Doria is practiced in many villages located in Kota, Bundi and Baran districts of Rajasthan. However, the oldest and the biggest concentration of weavers is in Kaithun, a village situated about 15kms from Kota. Other villages include – Siswali, Sultanpur
Though the fabric (saris) found in Rajasthan have high yarn count, Kota is famous for its fine weaves and a low yarn count, primarily due to the presence of Chambal, a perennial river, which makes the air moisture laden. The greenery present in otherwise dry state and the presence of black soil also contributes the cultivation of excellent quality cotton in the area. Kota has the distinction of being one of the three fine count cotton producing regions in North India, (other two being Chanderi and Maheshwar)
Kota has fertile land and greenery with irrigation facilities through canals. The two main canals; called as left main canal (towards Bundi) and right main canal (towards Baran) originate from the reservoir created by Kota Barrage. The tributaries of these canals make up a network in the city and surrounding areas of Rajasthan and Madhya Pradesh and supplements the irrigation of these areas.
Kaithoon is a maze of narrow and bustling streets. While walking through the town one can see colourful houses and through every window a handloom is visible. Since the town comes under Kota municipality, it is very well connected with the city, through buses and other local transport like auto-rickshaw. The town has one hospital, Weavers’ service centre, Central facility Centre and Women Weavers Association, to support the weaver community in marketing as well as funding opportunities. At the entrance of the town, a small garden is dedicated to Kota Doria Craft, with the Kota Doria GI decorated on its walls.
The maze-like streets are filled with colour houses, that have a vintage and antique appearance to them and many others have been renovated as per modern architecture. It’s interesting to note that most old homes are constructed as per the space required for a loom, especially a pit loom. There are many small and big mosques near the houses.
What started as a skilled craft, majorly employing men, during the 17th century which was cherished by the elite class, has now become a major source of income for the young women in the village and is evident in the way the loom is place near the kitchen area in the houses or in the kitchen stores. The elders of the family, often experienced weavers, say it’s a good way to keep their daughter-in-laws and daughters busy, earn an income without leaving their homes. While the job of marketing and selling still is in the hands of a few Master weavers in the village. The young men in the family have either started their own small businesses, in town or do door-to-door marketing of the sarees.
On the occasion of Holi, every year Vibhishan fair is filled by the trust in Kaithoon. Even though many things are said about the character of Vibhishana elsewhere, but in Kaithoon, Vibhishana is worshiped as a man of religion. A 7-day fair is organized on the occasion of Holi. However, due to Corona, only one day fair is being organized. Apart from being the only Vibhishan temple in Kaithoon, there is another specialty. Kaithoon is the only place in the country where the effigy of Hiranyakashyap is burnt on the second day of Holika Dahan (Dhulandi). According to Puri, after Holika Dahan, when Hiranyakashyap got angry and tried to kill the devotee, Prahlad. Then Lord Vishnu incarnated as Narasimha and killed Hiranyakashyap.
As of 2001 India census, Kaithoon had a population of 20,362. Males constitute 52% of the population and females 48%. Kaithoon has an average literacy rate of 62%, higher than the national average of 59.5%: male literacy is 73%, and female literacy is 51%. In Kaithoon, 17% of the population is under 6 years of age.
A large number of artisans belong to the Muslim Ansari, Mevati, Fakir, Mehrasi community live here. There are approximately 5000 looms in this village. Though all members participate, the weaving process is handled by the women of the house.
In most of the houses this craft has been passed onto them by their ancestors. The winding process was performed by the eldest woman in the family and the main weaving process was done by the young women, after they had completed their household work.
They work 8-12 hours a day. It takes them three days to weave a complete simple saree and fifteen days to weave an embroidered sari. It was only after the visit I actually understood the real process and deeply intricate it was. This craft of weaving needs a lot of skill and hard work, since one mistake can ruin the hard works of days.
The people of Kaithoon are extremely warm and are very hospitable, they are proud of their craft and are eager to share and spread their knowledge with the world.
Apart from Kota Doria, Kaithoon is famous for world’s first and only, 2000-year-old Vibheeshan Temple.
There is a mythological story behind the temple of Vibhishana. It is believed that at the time of the coronation of Lord Rama, Lord Shankar expressed his desire to visit the land of death. Vibhishana asked Lord Shankar and Hanuman to sit and take a tour on Kavad. On this, Lord Shankar placed a condition that wherever the plates of Kavad touch the ground, the tour will end there and they will stay there. It is said that the Kavad was (8 kos) 25 km long. Kaithoon which was earlier known as Kauthumpur. When Vibhishana reached here, the back of the Kavad was stuck on the ground. At the place where the back plate of the Kavad stood, today there is a Char Choma temple of Shivaji. The other part rests at Rangbari, located in Kota city, (4 kos) 13km away, where today Rangbari Balaji's temple is located and the Vibhishana temple is established at the same place where Vibhishan stood. The distance of Char Choma and Rangbari Balaji temple from Kaithoon's Vibhishan temple is only (4 to 4 kos) 13 km from each.
Earlier there was only one umbrella over the statue. There is a graveyard around the temple, where many boulders are scattered. Between 1881 and 1970, the then Maharaja of Kota Ummed Singh (1st) had built a canopy over the statue. After this gradually the temple building was constructed.
In the temple, only the part above the torso of the Vibhishana statue is visible in the temple. The temple committee says that the remaining part is submerged in the ground. Every year this idol sinks into the ground equal to a grain of barley. On the statue, the right hand is attached to the shoulder and the left hand is seen bent in front towards the chest.
List of craftsmen.
Documentation by Gargi Sethia for Gaatha
• Aarav. (2020, December). Kota Doria – Characteristics, Process, Popularity & Challenges. Retrieved from www.kotacityblog.com: https://kotacityblog.com/kota-doria/
• Boutique Sarees. (2021, April). Viranica Manchu Family in Label Vida. Retrieved from www.boutiquesarees.com: https://boutiquesarees.com/viranica-manchu-family-in-label-vida/
• Castelino, M. (2016). The Revival of style. Fibre2Fashion, 122-126.
• Chishti, R. K., & Sanyal, A. (1995). Sarees of India. Om Books.
• Dainik Bhaskar. (2022, March). Interesting Hidden Facts: Vibhishan Mandir Story. Retrieved from www.bhaskar.com: https://www.bhaskar.com/local/rajasthan/kota/news/burn-70-feet-high-effigy-here-is-the-only-vibhishan-temple-in-the-world-worship-is-done-on-holi-129523863.html
• Dhamija, J., & Jain, J. (1989). Hand Woven Fabrics of India. Mapin Publishers.
• Jain, R. (2003). Retrieved from www.gatha.com.
• Kota City Blog. (2020). Welcome to Kota. Retrieved from www.kotacityblog.com: https://kotacityblog.com/kota-rajasthan/
• Kota Live. (n.d.). History of Kota Doria Saree. Retrieved from www.kotalive.com: http://www.kotalive.com/kota_doria_saree_history.htm
• Mahapatra, D. N. (2016). Sarees Of India. New Delhi: Woodhead Publishing India Pvt. Ltd. .
• Ministry of Textiles, G. o. (Director). (2021, Junes). Kota Doria Weaves : Rajasthan [Motion Picture]. Retrieved from https://www.facebook.com/watch/?v=510105817082408
• Quazi, A. (2015). Kota Doria Saree: Weavers struggle, no direct market access. Kota: Hindustan Times.
• Statement of goods. (2004). The geographical indication of goods.
• Sundari Silks India. (2021, July 09). Chronicles of Kota Doria. Retrieved from www.sundarisilks.com: https://www.sundarisilks.com/blogs/article/chronicles-of-kota-doria