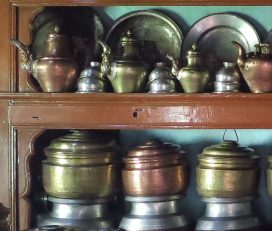
Copper Craft ~ Chili...
Copper and brass have played a significant role in fulfilling these needs. Even today, in most traditional Ladakhi kitchens such utensils are commonly seen
Chiling Sumda...
Reminiscent of the glorious lives of the Bundelas of central India that reveals the indulgences of a celebrated era, lost wax casting is a metal sculpting method in which a mould of wax is used for easy workability. Protected by a casing of clay or mud, the intricately designed hollowness it creates when melted away, is occupied by the molten metal to create fine pieces.
It is because metals are good in creating sound,or to produce good quality sound.
Lost wax casting is a metal sculpting method in which a mold of wax is used for easy workability. Lost wax casting is used to sculpt various kinds of metals spanning uses such as ornaments, idols and weaponry.
Lost wax casting is used to sculpt various kinds of metals spanning uses such as ornaments, idols and weaponry. It was traditionally used to produce canons and other war weapons as well as farming tools, cattle bells and bullock carts.
Tikamgarh is a town and district in the Indian state of Madhya Pradesh known for its Bell metal craft.
The famous lost wax casting is practiced in West Bengal, Orissa and Madhya Pradesh.
The ‘dancing girl’ of Harappa is the earliest known example of metal-wax casting. It was born in the Indus Valley Civilization. The method was also extensively used in creating temple idols, lamps, utensils, jewelry and also large weaponry. The craft has percolated into ceremonies and traditions. Many communities have a custom of gifting finely molded metal Dias (lamps) to their daughters for their weddings.
Lost wax casting is used to sculpt various kinds of metals spanning uses such as ornaments, idols and weaponry. It was traditionally used to produce canons and other war weapons as well as farming tools, cattle bells and bullock carts.
In present times, the craft is also used to make ornaments and show – pieces or intricate toys. Utilities used for worship in temples and the elaborate idols of gods and goddesses are also sculpted using lost wax casting. They also make small and elaborate oil – wick lamps with intricate traditional designs. The Government too commissions metal sculptures for various Architectural and Interiors projects.
In this craft, the raw materials partly play the role of the tools. The wax greatly aids in bringing about an intricacy in the design, which is otherwise difficult to create in basic moulds. Wax is also a very versatile material, which is easily available and can be re-used. The flexibility of this process explains itself in being able to create both small objects as well as large sculptures which are seen in several government buildings.
The designs portray the lives of the people and their surroundings. A lot can be learnt from the depictions, which also change according to the use of the object. There is a large antique appeal to the final product and it does not fail to attract connoisseurs of ancient artifacts.
A folklore from Madhya Pradesh speaks of how lost – wax casting was discovered. There were twelve brothers who to used help their father with farming. The youngest one, however, could not bring himself to be interested in farming. He used to sit under a tree when exasperated and play with wet clay. He slowly got engrossed in the interesting forms which came about. These later started developing cracks, and he applied gum to avoid these. It gave a very rugged finish to the form. To combat this, he started applying another layer of clay. When this too did not help he moved on to filling it with molten metal. It is said in this process of rectifying and polishing the form, he discovered the method of lost – wax casting.
The ‘dancing girl’ of Harappa is the earliest known example of metal-wax casting. It was born in the Indus Valley Civilization at around 3500 BC. Two copper figures were also found in Lothal in Gujarat, an ancient Harappan site. Wax casted artifacts of the Indo-Greek style, a juvenile figure of Harpocrates from 1st century BC, was excavated at Taxila. The bronze icon of Lord Nataraja (8 – 15th century A.D.) and the 3,000 year old bronze figure of Mother Goddess discovered at Adichanallur, Tamilnadu, South India; both were cast by the lost wax process. The method was extensively used in creating temple idols, lamps, utensils, jewelry and also large weaponry. The craft has percolated into ceremonies and traditions. Many communities have a custom of gifting finely molded metal Dias (lamps) to their daughters for their weddings.
This process flourished in different regions of India namely Rajasthan, Gujarat, Raipur, Sarnath, Andhra Pradesh and Tamil Nadu from 750 – 1100 AD, and remained prevalent in south India between 1500 – 1850 AD. This craft is still ardently followed in the tribal and folk regions of Madhya Pradesh and Chattisgarh in central India, Orissa and Bihar in the west and Tamil Nadu (Swamimalai) and Kerala (Munnar) in the south to create beautifully intricate objects of decoration and utility.
The metal craft in Madhya Pradesh developed and has been practiced for over three to four centuries. The blacksmiths used to make weaponry like cannons, swords, shields and spears for the royal army, as well as tools, carts and cattle bells for the farmers. Of the two main clusters, the manner it was made in Tikamgarh varied a little. Here the objects were made on moulds and wax threads were used for decoration. Whereas in the other parts, the entire object was shaped out of wound strips of wax.
Intricate details for the smallest of objects can be done in lost-wax casting. Therefore, the designs with fine patterns are made on wax. The inspirations for these patterns are derived from the elements of local architecture like the ‘jharokas’ and the ‘jaalis’, the birds and animals around them and abstract forms of surrounding fauna. These metal images, eloquent with peculiar indigenous socio – religious history, are considered auspicious. The impressions and the motifs created on the strips of wax are very simple, geometric and repetitive. The designs in the southern parts of India tend to be solid while the ones in the north are hollow. The method, however, remains the same.
Quick results and low prices for objects in demand is what is running the market. The awareness of handcrafted objects and their customized results is sparse. The cost of metal, which is the primary raw material of the craft, has also gone up. And the demand for heavy artifacts is decreasing. The buyers mainly consist of art collectors and temple authorities who buy these in the form of idols, lamps, bells etc.
The craft requires a lot of time and is labor intensive. It involves being subjected to large amounts of heat. These factors have led to the two adverse consequences. One is the number of cheaper imitations coming into the market. Since the crowd prefers the cheaper versions, most craftsmen no longer go through the original wax casting method. They instead make a permanent mould and cast similar artifacts out of the same. There are but one or two families following the entire process as it was. Many now get popular metal objects from Moradabad, and used them as moulds to create replications. Due to the heavy work involved and low returns, the younger generation are slowly stepping away from the work.
Lost – wax casting, as the name goes, involves creating the form with wax as the transient mould. After it is covered with clay or sand and heated, the wax melts away leaving the designs behind on the sand/clay layer. Molten metal is poured in to occupy this ornate void and solidify into a beautiful piece of art. Sometimes, different parts of the object are cast separately and later welded or pieced together.
Metal – Brass is used, which is an alloy of Copper and Zinc. Since pure Copper is a soft metal and is not an effective material unless strengthened as an alloy.
Beeswax and Industrial wax – This is mixed with groundnut oil and binding resin to make a mixture called ‘rar’. The initial mould is crafted from this.
Oil – is rubbed onto the working platforms to avoid sticking.
Sand and clay – to make a cast over the wax form.
Cow dung cakes, coal and firewood – to heat the entire form for the wax to melt and also to heat the metal.
Kerosene – for the small burner, which is used to heat the tips of the tools.
Metal wires – as reinforcement for the clay model in bigger models.
The tools required to execute the lost – wax technique are as following:
Dhatiya – a wooden bat used to beat the wax slabs.
Patla – A sturdy flat wooden surface, upon which the wax is worked.
Athali – wooden sculpting and molding tool.
Chisels, hammers – for making patterns and shapes with wax, breaking clay moulds and subsequently polishing the metal.
Pointed mace rolling pin – used to roll wax strips into thin threads.
Kerosene lamp – to heat the tips of the tools while working on the wax models.
Tongs and holders – To heat wax and pour molten metal.
Kiln – to melt the metal.
Press – A longitudinal metal slab with patterns in negative space marked on it. Wax strips are run through it, pressed together and they quickly rolls out as patterned strip.
Stamp tools – These are made by the craftsmen themselves for stamping on various patterns onto the mould.
Lost – wax casting, as the name goes, involves creating the form with wax as the transient mould. After it is covered with clay or sand and heated, the wax melts away leaving the designs behind on the sand/clay layer. Molten metal is poured in to occupy this ornate void and solidify into a beautiful piece of art. Sometimes, different parts of the object are cast separately and later welded or pieced together.
Mould
The Rar is heated and when it reaches a malleable state, it is used as the modeling material. In case of larger objects, a clay base is made, over which this wax mixture is coated and given the finer shapes.
The wax is melted and repeatedly heated over a period of two days and prepared. Available in the form of flat chunks, they are melted according to the amount needed. The wax is shaped into the desired form.
Sometimes, the entire form is made out of one piece and other times the limbs or other elements are made separately and fused to the main body. The ornamentation is made on wicks of rolled out wax and then added to the main form. Intricate patterns are made on wax using fine tools and stamps.
Sand and clay cast
After the mould hardens, a thin layer of local red soil is applied so that it percolates into the finest of designs. A layer of fine sand is applied so that it percolates the thinnest of patterns. Then a clay based paste is applied over this. Another thick coat of mud mixed with cow dung is then applied externally over the form. This last coat involves application of clay and sand (bajari). Here, the sand act as strengthening agent and prevents the mould from breaking open when heated. These steps of coating the mould with different mixtures takes up to 7 days.
Sometimes, in case of bigger sculptures, metal wires are used as reinforcements. So that the clay does not crack open while heating. This is then kept in sun till it dries. The mould is then heated over burning firewood and is covered with cakes of cow dung. The wax melts and flows out through the hole left open while the clay cast was made. This wax is collected in a container filled with water.
Metal cast
Molten metal or brass is then poured directly into this cavity. This non – ferrous metal casting takes over 15 – 20 minutes to complete. After the metal solidifies, the external covering is broken using hammers. The clay is wiped off and this is then again dried in the sun. Electric polishers, chisels and other tools are used to add a finer finish to the piece. Acid treatments are given to obtain antique finishes.
Traditionally, beeswax used to be the raw material for manufacture of products in which lost-wax casting method was used. But the cheaper and quicker alternative of industrial wax is presently taking over. This is resulting in more wastage than natural wax, as some of the industrial wax gets burnt away during the process.
The word Bundelkhand was not used until modern times. Throughout its history, the region was ruled by accomplished rulers. Most of the rulers were of Chandravanshi dynasty. The kingdom of Chedi can be considered as Ancient Bundekhand.
Mayakal: The third ruler of Maurya dynasty, Ashoka, built monasteries, guest houses in this region. Gurgi (Golaki Math) was the biggest monastery during his time. Southern Bundelkhand was ruled by Ashoka, which is quite evident when one stays in Ujjain and Vidisha. The preceding rulers of Maurya dynasty however did not have a strong hold on the kingdom and hence lost it to the Shudgh dynasty.
Gupta Dynasty: Kalchuri Dynasty: Chandela dynasty
During the reign of Kshatriya Khangar rulers, Tikamgarh was made capital and they ruled from 1180 A.D. to 1347 A.D. Old fort of Kundar town famously known as Garh Kundra was built during this period. Soon Bundelas took over the whole kingdom.
During the 16th century, it became a part of the kingdom of Orchcha, ruled by the Bundeli chief Rudra Pratap who was the first king of Orchcha.
During the reign of Mughal remperor Jehangir, his ally Bir Singh Deo reined in this region (1605 - 1627) and Orchha reached to prosperity. Still many architectural works of that period depict that glory, like the Jahangir Mahal and Sawan Bhadon Mahal.
During early 17th century, Raja Juhar Singh rebelled against Mughal emperor Shah Jahan, the mughal army occupied Orchha and ruled from 1635-1641. In 18th century, Orchha and Datia were the only states in Bundelkhand which were not subjugated by Marathas. In 1783, emperor Vikramjit (1776-1817), shifted the capital from Orchha to Tehri and renamed it Tikamgarh. The place was called Tehri, meaning triangle; as it comprised of three suburb clusters forming a triangle. Fort of Tikamgarh was constructed at Tehri and even the place was known by the name of Tikamgarh.
Chatrasal contributed greatly in claiming the freedom for Bundelkhand from Aurangzeb. Chatrasal took Kalin on his side. After the death of Aurangzeb, Bahadurgarh claimed the throne. Chatrasal and he got along quite well. Marathas were also gaining prominence during this time. Chatrasal was also a good poet; he used to encourage local artists. One of the regional poets Kavi Bhushan has writing these lines in the honor of the emperor:
और राव राजा एक चित्र में न ल्याऊं-
अब, साटू कौं सराहौं, के सराहौं छत्रसाल को।।
After the death of Chatrasal, Bundelkhan splitted into smaller kingdoms.
Raja Hamir Singh (r 1848-1874) attained a position of Maharaja in 1865. After his death Maharaja Pratap Singh succeeded the throne in 1874, he was a devoted emperor and did major developments of the state, he himself designed several irrigation systems. In 1901, his state area amounted to 2000 square meter, with the population of 52634. Pratap Singh's successor merged his state with Union of India on January 1, 1950. Then in 1950, the region was merged to Madhya Pradesh.
According to a legend, once Emperor Hemkaran tried slitting off his neck with a sword to sacrifice him in honor of Devi, but the goddess stopped him. Still the sword's sharp edge touched Hemkaran's neck and 5 drops of blood touched the ground. Because of this Hemkaran was known by the name of Pancham Bundela.
Tikamgarh was earlier called Tehri, meaning a triangle. This was because it comprised of three hamlets forming a rough triangle. The early history of Tikamgarh is not chronicled much, but the studies from the ruins in the city indicate the various dynasties which have ruled. Tikamgarh was part of vast empires, successively ruled by the Mauryas, the Sungas and the imperial Guptas. In the beginning of the 9th century A.D, Nanuk founded the Chandela dynasty here. Along with Khajuraho and Mahoba, Tikamgarh formed part of the extensive Chandela kingdom.
The Kshatriya Khangar rulers made Tikamgarh their capital, and ruled from 1180 A.D to 1347 A.D. They built the old fort of Kundar town, famously known as Garh Kundar. They were soon taken over by the Bundelas. During the 16th century, it became a part of the kingdom of Orchcha, ruled by the Bundeli chief Rudra Pratap who was the first king of Orchcha. In 1783, the ruler of Orchha Vikramajit (1776 to 1817) shifted his capital from Orchha to Tehri and renamed it Tikamgarh. Post independence, on 1st January 1950, the district was merged with the Indian Union. It became a part of the Vindhya Pradesh state. In 1956, it was merged to the state of Madhya Pradesh.
Tikamgarh lies to the northern part of Madhya Pradesh and the northwestern part of the Sagar district. The city lies 80 kms south of Jhansi and 40 kms north - east of Lalitpur in Uttar Pradesh. The state capital Bhopal is 320 kms away. The city lies on the Bundelkhand plateau between tributaries of Betwa and Dhasan rivers. It has an average altitude of 337 meters above sea level.
By Air : The airports closest to Tikamgarh are Gwalior (201 kms) and Khajuraho (125 kms).
By Rail : The train from Jhansi goes to Tikamgarh via Lalitpur. The Lalitpur station is 55km from Tikamgarh. Another railhead is at Mauranipur at Jhansi, connecting the Delhi - Mumbai and Delhi - Jhansi mainlines.
By Road : Tikamgarh is well connected by both state and inter - state buses. The daily bus services connect the city to the neighboring cities like Orchcha, Lalitpur, Nagpur, Indore etc.
The city is flanked by rocky terrain and specked with many small lakes. The land slopes towards the south. The land is fertile and suitable for agriculture. The main crops grown here are Jowar, Wheat, Urad, Till, Soyabean and Sugarcane.
Tikamgarh faces extreme weather conditions. The summers, from March to mid June, have temperatures soaring up to 45 degrees Celsius. The winters, from December to February are cold with the lowest temperatures reaching 2 degrees Celsius. Monsoons, from July to September come with an average rainfall of 1000 mm.
The wind direction changes seasonally in Tikamgarh. The north - westerly winds set in during the winter months and the south - western winds during monsoon. Winds blow from west to east during the summer months.
Tikamgarh is equipped with basic infrastructure. It has hospitals (both govt. and private) as well as primary health centers. There are many schools in the city which provide education up to senior secondary level and a few colleges too. The city also holds many agro - based industries and small industries like wood work units, handloom weaving, pottery, brick making, utensil making and gold, silver and Lac ornaments making.
Water supply for domestic use and irrigation is derived from the river and ground-water resources.
Tikamgarh is known for its fort, palaces and old buildings. They are, however, in ruins and steps are being taken to conserve them. The monuments and ruins are surviving evidences of the various rules Tikamgarh was under. For example, the Garh Kudar is a famous fort built by the Khangars and later seized by the Bundelas. It houses a temple and a tank. The Umri temple is a 9th century temple of the Pratihara period.
The dwellings in Tikamgarh are of both the Kachcha and Pakka type. Brick wall constructions with flat roofs or asbestos coverings are commonly seen now-a-days. These are low rise buildings. The development of newer residential areas is seen along the northern parts of the city, towards the road leading to Niwadi, along the SH-10. The housing clusters are fragmented due to the existence of chunks of agricultural land.
Tikamgarh is steeped in Bundelkhand culture. Hindi and Bundeli are the locally spoken languages of Tikamgarh. People also speak Dravidian, Devanagari and Bharia languages. Hinduism and Jainism are the prominent religions here. There is a substantial Muslim population. All the major festivals like Eid, Holi, Diwali, Mahavir Jayanti, Ramzan etc. are celebrated together. The Jain Community also celebrates the 10 days Paryushan Parv. There are a few tribal festivals also, for example Madai, Bhagoria, Dusshera and Karma. A large number of people participate in the grand Bundeli Utsav held in Chhatarpur, where the local songs and dances are featured.
Garh Kundar is the fort situated at a distance of around 22 kms from Tikamgarh, on the Niwari-Senderi road, on a hill. It was built by the Khangars and then seized by the Bundelas. The fort's administration has changed hands over the different rules, each one leaving behind certain elements.
Achroo Mata Temple is famous for its 'Kund' or well, which never dries up. During the Nav Durga festival every year, there is a fair organized here.
Baldeogarh is another fort situated on the Tikamgarh - Chhatarpur road at a distance of 26 kms from the city. The fort is situated about a beautiful tank called Gwal Sagar. It houses the temple of Vindhya Vasini Devi, which is famous for the annual seven - day fair in the month of Chaitra. The area around the fort is also known for its betel - leaf cultivation.
Tikamgarh is also famous for its lost-wax casting. Beautiful products are crafted out of this method, where the wax of the mould is melted out and replaced with bell metal.
List of craftsmen.
Team Gaatha