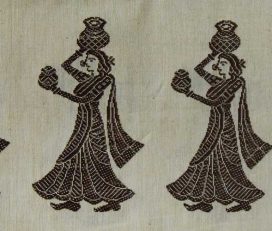
Gollabhama Saree Wea...
The Siddipet Gollabhama Saree is not just a piece of fabric; it is a living tradition, worn, celebrated, and reinterpreted through generations.
Siddipet, Telangana, India...
The prints from the villages, locally known as ‘gaam’ of India, are called as the ‘Gaamthi’ prints; vibrant colors, contrasting shades, varied patterns being their characteristic features. Originally done with natural dyes extracted from plants and other source, they are now also being done in artificial colors.
Vibrant colors, contrasting shades, varied patterns are the characteristic features of Gamthi prints.
Craftsmen believe that block printed fabrics are known for their versatile quality and their combination of motifs. According to them, working with hands is a never ending process of design exploration as opposed to screen printing. Earlier sold in local markets, these prints came to be known as ‘Saudagiri’ prints as the traders are called ‘Saudagars’. These prints have now become a rarity and only a few of the old fabrics preserved by traditional craftsmen can be found in museums today.
The blocks are of different shapes and have designs carved at the bottom surface. They can have large ‘Botas’, small ‘Botis’, ‘Trellis’ or ‘Jal’, (types of designs), small border, large border and sometimes geometric designs too. Each design normally has 2-4 colours and each color is imprinted from a separate block.
Hailing from the land of Maharajas, block-prints with their universally appealing degree of intricacy, competed their way to the weekly ‘haats’ and ‘melas’. Saudagars (the traders) from all over would come and sell their works to the landlords, Maharajas and their ladies. These very intricate and exuberant prints typically made to adorn their turbans and chunris came to be known as Saudagari prints. Although a rarity now, some Saudagari blocks, preserved by the traditional craftsmen can be seen in the museums today.
Today, These fabrics are utilized for ‘Sarees’, ‘Dupattas’, ‘Kurtas’, home decor and many other lifestyle products.
Craftsmen believe that block printed fabrics are known for their versatile quality and their combination of motifs. According to them, working with hands is a never ending process of design exploration as opposed to screen printing. Earlier sold in local markets, these prints came to be known as ‘Saudagiri’ prints as the traders are called ‘Saudagars’. These prints have now become a rarity and only a few of the old fabrics preserved by traditional craftsmen can be found in museums today.
Printing and dyeing techniques flourished in Rajasthan in the medieval ages and the influences brimmed over to Gujarat. The craftsmen in Gujarat developed an expertise in printing with wooden blocks. Printed fabric was a frequent element in royal processions with which they made tents for when the battalion rested. Until the establishment of fabric trade routes Europeans used wool, silk or leather as dress materials and cotton was not an extensively explored material. Eventually, plain cotton started being heavily imported by European ports. Absence of knowledge about colors and fabric printing also gave way to the European demand for printed fabrics. The climatic conditions in Europe didn’t allow the colors to mature as brightly as they did in India. The traditional weaver clan ‘Chaliyans’ used to weave the plain fabric and printing on fabric was done in western and northern India. These printed fabrics became popular in Europe as Calico prints, also termed as ‘Chintz’. John Ovington came to India in 1689. He summarized his observations by saying: “In some things the artists of India out-do all the ingenuity of Europe, viz., the painting of chintz or callicoes, which in Europe cannot be paralleled, either in their brightness and life of color or in their continuance upon the cloth-.The interest of Europeans in cotton printing and dyeing were clear enough and those cases of ‘borrowing’ from India were written by Frenchmen in the 70 years between 1678 and 1747, a period that coincided with initial phase of European expansion for the new textile printing industry. Between 1678 and 1680, Georges Roques wrote a 333-page manuscript containing a detailed analysis of the production of textiles in Ahmedabad, Burhanpur and Sironj. The French East India Company’s Lieutenant Antoine Georges Nicolas de Beaulieu was the author of a second manuscript, probably compiled around 1734. Finally, the third document was produced as a series of letters by Father Coeurdoux, a missionary from the Society of Jesus who lived in India between 1742 and 1747.The principal cotton textile described by Roques was the less expensive wood block printed Chintz as opposed to the more expensive painted Chintz from the same region and elsewhere in India. The less expensive wood block printed Chintz was produced at Ahmedabad, Sironji, Bhuranpur (Khandesh). Ahmedabad was one of the lowest cost production center for the textile in western. The use of one or more carved block was practiced; Ahmedabad producers used three types of block, one for outline of the design, one for the ground and third types of detail, worker first print outline then ground and then details.Ahmedabad was also famous for its intricate traditional designs that were chipped on the blocks by the artisan families. These prints came to be called ‘Saudagiri’ prints as ‘Saudagars’ or traders would gather at fairs, markets or ‘haats’ to sell their printed fabric to common folk as well as royalty.The ‘Gujarat State Handicraft Development Corporation’ and its retail wing ‘Gurjari’ were established in the early 1970s. The aim was to uphold the craft and create a sustainable market. At around the same time, the ‘National Institute of Design’ was established in Ahmedabad. Designers were recruited from NID to work with the Handicraft Development Corporation staff and the craftsmen from rural areas of Gujarat. Thus the crafts slowly grew with more and more people being aware of it and the markets expanded from domestic customers to overseas. Presently there are about 8-10 big units in the city and each employ almost 70 skilled block printers.
Craftsmen at Ahmedabad are masters of their work on different designs that are traditional as well as have contemporary variations. The blocks are of different shapes and have designs carved at the bottom surface.
The artisan goes on to print with several blocks to attain the final composition, the first block imparts the outline and the other block imparts different colors on the fabrics.
Numerous combinations achievable by the same age old blocks, with some colors and a little playfulness in hand, still stands unparalleled “Hand ka koi end nahi hai”, as quoted by the master craftsman ‘Farooq Bhai‘, it means that there is no end to the number of variations you can get by this technique.
The cloth is dyed in a solid color on which a ‘latticework’ of patterns is stamped with the blocks dipped in dye. These patterns are formed by various motifs. The patterns are floral, free form and geometric. They are mostly inspired from local elements. They can have large ‘Botas’, small ‘Botis’, ‘Trellis’ or ‘Jal’, (types of designs), small border, large border and sometimes geometric designs too. Each design normally has 2-4 colours and each color is imprinted from a separate block.
Flowing water is a crucial requirement for making block printed fabrics, so the craftsmen now have tanks for the same purpose since the natural waters sources are overridden by marshes. The natural colorants have also been replaced by chemical dyes. Also the modern screen printing technology poses a huge threat to the art of block printing, since it is faster and cheaper.
Wooden blocks, carved with intricate designs are dipped into dye and used to transfer patterns onto the fabric. The fabric is then treated in various stages of resist-dyeing to transform into the final product blossoming with vibrant colors and beautiful motifs.
Printing fabric – This is brought from ‘Bhimandi’ (Maharashtra) and ‘Thirupur’
Dyes – Pigment dyes, Discharge dyes, Reactive dyes, Vegetable dyes.
Plain cloth – This is used as a cover for the printing tables before printing cloth is laid out over it.
Muslin – This is also used a as a base covering for the printing table.
Glue – This is mixed with different colored pigments and dyes. It gives a consistent and an easy application of the dye.
Wooden blocks : Made of seasoned teak wood, the wooden blocks are the main tools of the printers. These blocks are carved in accordance to the designs given by the craftsmen of ‘Pethapur’ and are etched on the underside of the block. About two to three holes are drilled vertically and horizontally across the body of the block, which ensures free air passage and release of excess printing paste. This special feature is unique to these blocks.
Dyeing Trays : Trays made of wood or plastic are used to fill the dye and it is mixed with the help of various ladles. A thin bamboo trellis is fixed into the tray of dye mixture and this holds a coarse piece of cotton cloth. A piece of cloth is soaked in the dye and the blocks are pressed onto it, rather than being dipped in the solution directly. This enables the dye to spread more evenly onto the block and not drip.
Printing tables : These are raised wooden blocks and are 5 feet by 3 feet in dimension. Bricks and smaller wooden blocks are used to uniformly raise this platform by 9 inches. Printing begins on these after they are covered with layers of plain cloth and jute for protection.
Washing tank : In olden days, the cloths were washed in the running waters of the river. But now the artisans have erected a series of water tanks with varied heights. The top most tank has the purest water, while the lower most tank has the water containing the dye from washes. The fabric is first washed in lowermost tank, then further in higher tanks.
Drying structure : Earlier, the printers used to dry the fabrics by laying them out in open under the sun near the rivers. Due to lack of clean spaces on river banks nowadays, the artisans have a bamboo structure developed at their workshop, it spans up to the height of two storeys. It is a rectangular framework with a number of parallel runners made of bamboo or iron rods. The fabric of length up to 12 meters can be dried on these structures.
Wooden blocks, carved with intricate designs are dipped into dye and used to transfer patterns onto the fabric. The fabric is then treated in various stages of resist-dyeing to transform into the final product blossoming with vibrant colors and beautiful motifs.
Preparing the fabric : The fabric is thoroughly washed to remove factory starch. If the natural grey of the fabric is not desired then it is bleached to obtain a stark white color. The fabric is also dyed sometimes to get a base color at this stage and washed to remove excess dye. It is then stretched evenly over a wooden table and fastened using strong pins.
Printing : The wooden blocks are used at this stage. Color is kept in a tray on a wheeled wooden trolley, which the printer drags along as he works. The tray of color rests on another tray that contains a thick viscous liquid made out of mixing pigment binder and glue. This gives the color tray a soft base and helps in spreading color more evenly on the wooden block. The fabric is printed by hand from left to right. Different craftsmen are involved at this stage. One layer of blocks is pressed appropriately with adequate pressure to get the pattern. This step is repeated as per need. In case another set of prints is required, it is done by the other craftsman.
Post-printing : After the block printing is done; the fabric is dried in the sun. It is rolled in newspaper to prevent the dye from spilling on to other layers and is then steamed in boilers. The fabric is again washed in large quantities of water and finally dried. The process is finished by ironing as this makes the color become permanent.
During the process the fabric is put through frequent washes, which leads to a lot of wastage because unlike older days, the process is not carried out in flowing rivers anymore and the use of chemical dyes renders the soil and water unfit for any other usage.
Around the 11th century, archaeological evidences state the existence of Ahmedabad by the name of Ashaval. Karandev I, the Solanki ruler of Anhilwara waged a war against the then Bhil king of Ashaval and established a city called Karnavati on the banks of river Sabarmati.
Gujarat was taken over by the Vaghela dynasty in the 13th century. It was soon seized by the Delhi sultanate in the 14th century. Soon during the early 15th century Muzaffar Shah I crowned himself the sultan of Gujarat after he detached himself from the Delhi sultanate. He founded the Muzaffarid dynasty which went on to rule till the Marathas came in during 1758. Ahmedabad derived its present name from Muzaffar Shah's grandson Ahmed Shah who ruled from 1411 AD. It went through a series of occupation by the Mughals and then back to the Muzzafarids till emperor Akbar set foot in 1573.
During the Mughal reign, Ahmedabad became one of the Empire's thriving centres of trade, mainly in textiles, which were exported as far as Europe. The Mughal ruler Shahjahan spent the prime of his life in the city, sponsoring the construction of the MotiShahiMahal in Shahibaug.
The Mughals surrendered the city to the Marathas in 1758. The British East India Company took over the city in 1818 during the Third Anglo-Maratha War. A major development took place in the year 1864, when railway line was laid that connected Ahmedabad with Bombay. These developments brought Ahmedabad on the map of leading centers of trade and manufacturing.
The Independence struggle and movements had seen a strong centre in Ahmedabad with the presence of Mahatma Gandhi who established the Kochrab Ashram near Paldi in 1915 and the Sabarmati Ashram on the banks of the Sabarmati in 1917. It witnessed many protests like the Dandi salt march and the Quit India movement until India got its Independence in 1947.
During the 1960s a large number of educational and research institutions were founded in the city, making it a center of higher education, science and technology.
Ahmedabad has now flourished into a thriving city with strengthened infrastructure and economy and lived past the many trials and tribulations in the form of riots and natural calamities.
Ahmedabad lies in the state of Gujarat at an elevation of 174 ft above sea level. It is located on the banks of the Sabarmati River. The Kankaria lake and the Vastrapur lake are the two manmade lakes within the city limits. Its longitude and latitude are 720º 41' E and 230º 1' N respectively.
By Air - The Sardar Vallabhai Patel Airport is just 10 kms from downtown Ellis Bridge/Ashram Road area. It functions for both domestic and international purposes. Direct Air India and Indian Airlines flights go to the Gulf and to other destinations through intermediate stations. Domestic flights on Air India, Indian Airlines/Alliance Air, Jet Airways and Gujarat Airways will take you to Delhi Mumbai, Kolkata, Hyderabad, Bangalore, Pune, Jaipur and several other destinations within the country.
By Rail - Ahmedabad has a well maintained railway network connected to important destinations of the country. Ahmedabad railway station is the largest railway station in the state of Gujarat. Various express and super fast trains are available between Ahmedabad and important cities of the country.
By Road - Ahmedabad has a good network of roads also. National highways connect cities like Vadodara, Rajkot, Jamnagar and Mumbai. The Gujarat State Road Transport Corporation (GSRTC) runs express and luxury deluxe buses to the neighboring towns and cities. One can reach the city by taxi from nearby cities.
Ahmedabad has a hot, semi arid climate which is mostly dry throughout the year. The temperatures peak to 45 degrees Celsius in the summer months from March to June. The monsoons bring in relief from July to September with an average annual rainfall of 800 mm. The winters span from October to February bringing in mild chills with temperatures dipping to 10 degree Celsius.
Ahmedabad is a thriving city with its infrastructure matching upto many of the metropolitan cities. Ahmedabad is endowed with abundant supply of natural resources like minerals, forests and rivers. The principal mineral resource in the city includes crude oil. The river Sabarmati is the main water resource for the people of Ahmedabad. It provides drinking water to the entire city. There are two lakes present within the city's limits - Kankaria Lake and Vastrapur Lake. Kankaria Lake, in the neighborhood of Maninagar, is an artificial lake developed by the Sultan of Delhi. The city's forest cover is decreasing day by day due to rapid industrialization.
Ahmedabad city is an administrative headquarters of Ahmedabad district, administered by the Ahmedabad Municipal Corporation. The city's suburban areas are administered by the Ahmedabad Urban Development Authority (AUDA). Electricity in the city is generated and distributed by Torrent Power Limited, owned and operated by the Ahmedabad Electricity Company, which was previously a state-run corporation. Ahmedabad is one of the few cities in India, where the power sector is privatised. The Sardar Sarovar Project of dams and canals has improved the supply of potable water and electricity for the city.
The city is equipped with health facilities both private and government aided. Ahmedabad hosts many prestigious educational institutions like the Indian Institute of Management, the National Institute of Design, CEPT etc.
Ahmedabad was once a fortified city. It has now grown beyond the old gates and walls. The city is divided by the Sabarmati River into two physically distinct eastern and western regions. The eastern bank of the river houses the old city, which includes the central town of Bhadra with the Bhadra fort. This part of Ahmedabad is characterized by packed bazaars, the pol system of close clustered buildings, and numerous places of worship. The colonial period saw the expansion of the city to the western side of Sabarmati, facilitated by the construction of Ellis Bridge in 1875 and later the modern Nehru Bridge. The western part of the city houses educational institutions, modern buildings, residential areas, shopping malls, multiplexes and new business districts.
Monuments and structures of the Indo-Saracenic style can be still found in Ahmedabad. The Sidi Saiyyed Mosque is one such example. Many Havelis from this era have unique carvings and can be seen in the ancient pols of Ahmedabad. When the city stepped into the modern era it was honored with many world renowned architects like Louis Kahn, F.L.Wright, B.V Doshi and Le Corbusier who were commissioned to design many of the buildings like IIM, Calico Mills, Gandhi Ashram etc.
The Gujarati culture is a vibrant and active one. Popular celebrations and observances include Uttarayan, an annual kite-flying day on 14 January. The nine nights of Navratri are celebrated with people performing Garba which is the folk dance of Gujarat at venues across the city. The festival of lights, Deepavali, is celebrated with the lighting of lamps in every house, the decorating the floors with the 'Rangoli' and the bursting of firecrackers. Other festivals such as Holi, Ganesh Chaturthi, Gudi Padwa, Eid ul-Fitr and Christmas are celebrated with enthusiasm. The annual Rath Yatra procession on the Ashadh-sud-bij date of the Hindu calendar and the procession of Tajia during the Muslim holy month of Muharram are integral parts of the city's culture.
The people of Ahmedabad enjoy rich culinary traditions. The most popular form of their meal is a typical Gujarati thali (meal) consisting of rotli, dal, rice and Shaak (cooked vegetables, sometimes with curry), with accompaniments of pickles and roasted Papadums. Popular beverages include buttermilk and tea; sweet dishes include laddoos and mango.
The major religions followed by the people are Hinduism, Jainism and Islam. The city is also home to a substantial population of Parsis. The traditional Gujarati dresses for women consist of the lehenga choli or the ghagra choli. These are colorfully embroidered and complemented by bare-backed blouses extending to the waist. Ghagras or lehengas are gathered ankle-length skirts that are fastened at the waist. The entire outfit is completed by a veil cloth called Odhni or dupatta which is thrown across the neck or over the head. Gujarati men usually attire themselves in dhoti, long or short coat and turban cap. The urban population, however, has progressed towards contemporary forms and sports the latest in fashion.
The kite festival of Ahmedabad is sight to behold. The festival marks the days in the Hindu calendar when winter begins turning to summer, known as Makar Sankranti or Uttarayan. Kites of all shapes and sizes are flown, and the main competition is to battle nearby kite-flyers to cut their strings and bring down their kites. Since 1989, the city of Ahmedabad has hosted the International Kite Festival as part of the official celebration of Uttarayan, bringing master kite makers and flyers from all over the world to demonstrate their unique creations and wow the crowds with highly unusual kites.
Navratri celebrations are another striking feature. The place erupts into a nine-night dance festival, perhaps the longest in the world. The dance form called Garba is followed where people dance around in circles uniformly to beats in the traditional steps.
The Sabarmati Ashram in Ahmedabad is a site which is prominent in Indian history. It was the center of Mahatma Gandhi's non-violent struggle for India's independence. The ashram is located on the banks of river Sabarmati and was established in 1917.
The Adalaj stepped well is a much visited architectural attraction of Ahmedabad. Built in 1499 by Queen Rudabai, wife of the Vaghela chief, Veersinh, this five-storey stepwell was not just a cultural and utilitarian space, but also a spiritual refuge. It is believed that villagers would come every day in the morning to fill water, offer prayers to the deities carved into the walls and interact with each other in the cool shade of the 'Vav' (well). Another remarkable feature of this step well is that out of the many stepwells in Gujarat, it is the only one with three entrance stairs.
List of craftsmen.
Team Gaatha
Interview: Farooq Bhai chippa, Ahmedabad
https://docs.google.com/
http://myblog-prerna.blogspot.in/2010/01/history-of-block-printing.html