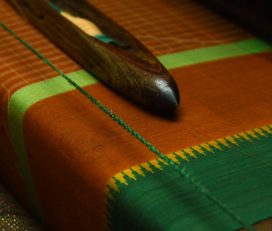
Saree Weaving ~ Nara...
Narayanpet sarees, handwoven in the small, vibrant town of Narayanpet in Telangana, are not confined to ceremonial grandeur or museum-worthy curation.
Narayanpet, Telangana, India...
Block printing is an ancient printing technique used on cloth and textiles to make beautiful patterns. The origins of hand block printing are believed to lie in China, where the technique was first used around the 3rd century when books would be written by hand and there couldn’t be many copies since writing a book was a very long, slow and strenuous process. The technique slowly grew in China as was used on textiles and paper alike, to print texts as well as beautiful patterns. However, with time, as travelers from China travelled to India and other parts of Asia, the technique was picked up artisans in these parts as well.
The artisans of Sanganer worked for three types of royal patrons: nobility and courtiers, temple devotees and everyday clients. Destined for kings and queens, royal attire required the most sophisticated printing and dyeing techniques. Remarkable depictions of flowers dance across the courtly cloth. Whereas local and temple textiles featured indigenous flora, fabrics designated for royalty often portrayed flowers from foreign lands.
During the 18th century, the famed chhipa and rangrez communities of Sanganer expanded their trade by uniting to create delicately patterned and coloured muslin material for a broad clientele. Royal patronage fueled domestic trade and eventually launched the work of the Sanganeri craftspeople into the international arena.
The oral tradition of the Sanganer chhipa community incorporates a myth to explain the source of their inherited dye and print knowledge. Their elders recite various versions of the tale but all renditions focus on the popular Sant Namdev, a nomadic mystical poet and chhipa. If a printer in Sanganer is asked of the origin of his art, Kimvadanti is narrated. In the time of the Sultana, the king of Sanganer, there lived a pious man named Namdeo. One night, in a dream, the process of vegetable dyeing was explained to Namdeo. In the morning, Namdeo called his friends and instructed them with what he had dreamt. The people were grateful to Namdeo and accepted it as a gift from God. The popularity of this parable reinforces the traditional belief that Indian crafts result from the harmony existing between religious devotion and the practice of art. For the block printing community the process of creating colours on cloth is a religious act and the ability of natural dyes to impregnate cotton with colour, evokes mystical connotations. Sant Namdev is omnipresent in the streets and alleys of modern Sanganer. Numerous shrines dedicated in his honor dot the cityscape and his image frequently appears on a popular poster that adorns the workplace of many chhipa families. At the heart of the old town in the Chhipa Basti neighborhood, Namdev Chowk square and Namdev ka Mandir temple preserve his name for posterity.
The origin of the printing craft in Sanganer prior to the establishment of Jaipur is speculative. Some Hindu block printers claim their forbearers arrived from Gujarat and historical records support this claim. The social upheavals that occurred during the wars of Mughal Emperor Aurangzeb during the mid-17th Century, flowed by incursions of raiding Marathas, may have forced Gujarati printers to flee to Sanganer. The flow of ideas between Gujarat and Rajasthan fostered aesthetic similarities marked by the clear bold lines appearing in both state’s printing styles. As Jaipur’s population grew, the commercial areas became increasingly congested and craftsmen soiled outside the confining city walls. Oral tradition suggests that the chhipa families of Jaipur began to shift their work to locations where space and running water were freely available, yet still within easy reaches of the capital. The riverbanks of Sanganer presented the ideal location with the added benefit of specialist dyers and cloth bleachers residing in the town. These artisans formed a large, supportive community with block printing at the core of their culture.
BLOCK CARVING: A critical component of block printing is block carving and it is an art form in itself. The stamp underpins the work of every chhipa. The block carving community of Sanganer is often overlooked; yet, these small businesses illustrate the shifting dynamics of Sanganer’s textile industry. Historically, block carvers worked from a repertoire of designs designated to a particular community. As the old blocks aged with repetitive use, they were mended or replaced with fresh blocks bearing the same classic motifs. Close proximity between the carvers and printers was unnecessary and at times, hundreds of miles divided these craftspeople. Until the 20th Century, local families of block carvers lived mainly in the ‘Purani Basti’ district of Jaipur’s walled city. Very few families based themselves in Sanganer. Those who did live there, tended to be carvers who mended old blocks rather than those who created new blocks. Then in the late 1970s, the number of traditional carvers and printers in Sanganer grew following an exodus of artisans from Farukkhabad. Suffering with the pressure of competing with modern printing methods, these migrant craftspeople looked to Sanganer and Jaipur to provide
Original textile products of Sanganer were roughly divided into three categories:
1.The ‘Syahi Begar‘ black and red designs on gossamer white cloth were worn as safa turbans or angochha shawls by men of the local community.
2. Buti sprigged floral motifs stamped upon softly coloured or white backgrounds graced Jaipur court society.
3. Dupattas and shawls bearing auspicious red designs on a white or yellow background adorned the pious attendees at Hindu temples.
Menswear constituted the majority of Sanganer’s printed fabric. In Rajasthan, traditional male attire consists of a simple series of garments like the ‘dhoti‘, one example of India’s famed aptitude for taking a single piece of unstitched cloth and folding it into a complex garment. Ordinarily, he wears a white kurta long shirt along with a bundi vest, worn underneath in winter or donned as outwear in the summer. Next, he winds a length of cloth around his head as a safa turban. To complete his outfit, he tosses an angochha shawl either over his shoulder or around his neck or waist.
Many chhipas in Sanganer remember the regular production of printed designs for local women. Some patterns mimicked the bandhani-tie-dyed head cloths particular to local Mali and Mina women. The bright yellow Mali chunnari or veil cloth is distinctively patterned with a single large red circular motif in the center of the rectangular cloth. On the other hand, the Mina Chaddar, a heavy cotton shawl, is covered with small flower-shaped arrangements of simple red dots on a dark-black background.
Home furnishings incorporate a wealth of folk imagery. Regimented borders of flowers, vines, animals and human figures flank the geometric jaal patterns in the center. Ranks of small soldiers accompanied by decorated cows, elephants or horses compete with vignettes depicting popular folk tales. These large textiles enable a block printer to exhibit his creative flair because each piece is a unique combination of block designs derived from the printer’s personal collection and filled with hidden clues to the client’s identity.
BLOCK CARVING: For hundreds of years the traditional blocks used by Sanganeri chhipas were recognized by their diminutive size and detailed carving, Fundanbhaya, a local block carver, describes these tiny old-fashioned printing blocks as ‘cigarette packets’ that look like children’s toys next to the modern blocks. This animated 68-year-old carver is the son of a handloom weaver and started making blocks at the age of 12. By the end of the 1980s, organized borders of ‘butah’ and ‘buti’ combinations gave way to stripes, geometrics and irregular bold repeats. To compete with screen-printing, the size of the blocks increased by three to four times from their original size. According to the 2008 census there are 52 block carving units in Sanganer today. They receive regular orders from local printing units but their numbers are shrinking in conjunction with the block printers.
Their links with Farukkhabad remain strong; carvers regularly visit family members, as well as order ‘shisham‘ rosewood from local timber merchants. Carvers’ workshops lining the lanes of Sanganer are a familiar sight. Open-fronted shops contain stacks of seasoned, sliced wood inside. They work under the front awning, squatting at small three-legged tables. Unfazed the cacophony of tapping which fills the air, each worker guides his tiny chisels across the face of a wooden block with utmost precision. Every carver retains a traditional toolkit: a personal and unique set of over thirty miniature chisels, well-worn hammers, and old-fashioned bow-drills. They don’t use power drills or saws. They may save a carpenter some time, but are of no help to the block carver. The symbolic relationship between the art of hand carving wooden blocks and the skill of printing is now ingrained in the heart of Sanganer. Old and new designs sit side by side. Even though the traditional designs compete with new ones, the old blocks are compulsory because they were made, are made and will always be made.
Over the past three decades, block printing in Sanganer has increased dramatically because of an expansion in the textile market all over the world. With changing times, craftsmen have adopted cheaper and more easily available raw materials, which include the usage of chemical dyes in abundance and the almost null use of the traditional natural dyes. Chemical dyes, which offer an abundant variety of colours picked up a rapid sale in the market and soon, majority of the printers made a shift to the same. With over 400 chemical dye dealers in Jaipur alone, the sudden shift became prevalent even in the domestic markets. This began taking a toll on the ground water of Sanganer and surrounding areas. When the printed fabrics would be washed, over and over again, the chemicals from the dyes would seep into the ground water making the water unsuitable for drinking and other purposes directly related to human beings and animals. Today, the groundwater here is so polluted that government has released orders to shut down all printing units in the Sanganer area.
Along with environmental challenges, the availability of artificial printing material and change in the trends and forecasts of the markets has resulted in the loss of identity of the Sanganeri prints. There has been a major shift in the colours used, the motifs used, the fabrics used and the purpose of the making a certain kind of print. Globalization and the mass expansion of the printing industry ahs led to a certain loss of essence of the Sanganeri prints.
Also, with the coming of screen-printing, which produces printed fabric way cheaper and faster than block printing, it has taken up the majority of the market demand for block printing.
Raw Materials: The process of block printing is widespread due to its intricate process, motifs and vibrant colors. The main raw material is the color used in the printing. Traditionally the artisans used natural colors but today it has been replaced by chemical and artificial colors.
Different types of dyes are used for silk and cotton.
Vegetable/ Natural dyes: Vegetable dyes have been used for generations for printing and dyeing. Extracted from nature, vegetables, fruits etc., they are eco-friendly and traditionally important. There are few major colors produced naturally which are known internationally too: black, red, green, yellow, indigo, pink.
Discharge Dyes: These are chemical dyes are used to print on dark background because of their quality to react with the dark base fabric. These dyes bleach out the dark color from the printed area and print the desired color on it. In this process a range of white and other light colors can be printed on a dark background.
Pigment Dyes: These colors are readily available in the market and are easy to use. Pigment colors, are mixed with kerosene and a binder to be made ready for use. The mixing has to be done carefully as the thickness of the material can give raised effects on the cloth while printing. These colors follow the direct printing technique. Colors applied are visible and do not change after washing.
Reactive Dyes: These are the chemical dyes which when mixed with second chemical produces a third color. Artisans therefore dye the cloth, to be printed, in one chemical and then print it with another chemical. These two chemicals react with each other and hence produce a different color.
Rapid fast Colors: These colors are difficult to store and has to be used the same day. In rapid fast color process the color in the design and the ground color both are printed in one go. Generally white or light background is used. There are only few colors available in this process.
Cloth: Traditionally the printing was done on white or pale background of cotton cloth. Today the craft is practiced on any material ranging from cotton, silk, organza, jute, kotadoriya, chiffon, paper etc.
Water: for washing
The main tools of the printer are wooden blocks, which are available in different shapes and size as per the design and requirement.
1.Printing Table – The tables that fabrics are printed on have varied specifications as well. Block printers often customize them but vastly it approximately measures 3 feet in height, 3 feet in width and 9 feet in length and it allows about 3-4 printers to stand and work simultaneously. But earlier, the tables would be about 1 feet high, 2 feet wide and 5 feet long because there would usually be only one printer who would be sitting on the ground and printing. The to-be-printed fabric is not placed directly on the wooden table because when the block printer hits the block to get a proper print while printing, it would damage the block and the colour would smudge. So the table is covered with layers of canvas, jute and other fabrics to provide a cushioning for easier and clearer prints.
2.Color Plates – While printing, the printer needs his colours next to him and such that he does not have to keep carrying them around, since it would break the flow of the printing process. So, block printers use a wooden tray in which they keep colour, called ‘saaj’. The tray works on a certain kind of mechanism, which would make sure that the colour just dabs onto the wooden block and the does not smudge on fabric when printed. Colour is poured into the tray and a wire mesh is kept over it, after which a piece of felt is also placed on it because felt soaks the colour nicely. Finally a fine cotton (malmal) cloth is kept on the cloth.
3.Tray Trolley – These are wooden trolleys’ accommodated with two shelves and wheels in the base for the easy movement and are locally called as ‘patiya’, 3 feet tall, suitable for working on the printing table. The upper shelve is to keep the color tray is kept while in the lower rack is required to keep blocks in.
4.Block for printing – The making of blocks is in two kinds: wooden blocks and metal blocks. Both are made in very unique ways and have very unique purposes as well.
5.Scale – Scales are used to mark the areas to be printed on fabric.
6.Chalk – Tailoring chalk is used for marking and the sharp edges of the chalk give fine lines.
7.Brushes – To maintain the life of the block, metal or nylon brushes are used to clean the wooden and metal blocks after use.
8.Tambadi (Copper vessels) – Traditionally copper vessels are used for dyeing and washing of cloths.
9.Mogari (wooden roller) – A cylindrical wooden roller on which the cloth is kept and beaten is called a mogari.
10.Kotan (Wooden mallet) – This is used to beat the cloth over mogari, to remove the starch from the fabric.
Block carving and printing has a very local dialect. The number of blocks per design depends on the number of colours that the design will have. The outline of the motif(s) is called ‘Rekh’, which in the case of Sanganeri print is the ‘Syahi’ i.e. outlining with black colour. The block for the background is called the ‘Gadh’, which in the case of Sanganeri printing, traditionally did not exist because it would mostly be printed on white cloth. The block used to fill in colour is called ‘Datta’, which in the case of Sanganeri printing is the ‘Begar’ i.e., filling the red into the motifs. In other kinds of block printing, if the number of colours is more, the number of ‘Datta’ will be more too. Sometimes, designs do not have the ‘Rekh’ or the ‘Gadh’, but that is only because of the play of negative-positive spaces, which designers have started working with. However, traditionally, a design had to have all three of these blocks.
A critical component of block printing is block carving and it is an art form in itself.
BLOCK CARVING: The making of blocks is in two kinds: wooden blocks and metal blocks. Both are made in very unique ways and have very unique purposes as well.
Wooden Block: The first requirement for block printing is carved out wooden blocks. For generations, artisans have been carving blocks out of teak or sheesham wood. The wood has to be seasoned properly for blocks to be carved out. The design is first printed out on paper and then stuck on the wooden block. Using iron/steel chisels of different shapes and sizes, the artisan then carves out the design from the wooden block. The handle of the block, also mostly made from wood is attached with nails to the opposite side of the design base for support and grip during printing. Every block has holes drilled into the wooden piece for air to pass freely and to allow the release of excess colour. The blocks can be made of any shape: square, rectangular, circular etc. The block is soaked in oil for about 10-15 days after it is made to soften out the grains of the wood. The life of these block are approximately 600-800 meter of printing.
Metal Block: For the more intricate, clearly printed designs on fabric, the use of metal blocks is prevalent. There is no smudging or mixing of colour on the fabric when metal blocks are used because of the highly narrow width of the engraved design. Evenly cut metal strips are engraved into wooden blocks. The metal strips are beaten till they are thin and then are cut into strips of even length. The design is traced on the wooden piece and the metal strips are gently hammered on it. It is checked thoroughly once the block is made, to see whether all the strips are of the same height on the wooden base. Metal blocks take a long time to be completed and are costlier than wooden blocks but are comparatively very long lasting.
The Sanganeri block-printing process involved:
1.Preparation of the cloth: The chhipa begins his task by subjecting the cloth to a rigorous scouring and bleaching procedure called teluni, to emulsify the oils on the cotton threads, acting like a modern laundry detergent. Goat or camel dung is mixed with sesame seed oil and soda ash and a little water and left overnight with the fabric soaked in it. The fabric is then dried and this process is repeated every night for about a week. This solution creates the soap, which acts like a laundry agent.
2.Pila karna: (To-do yellow): This process involves the application of harda onto the cotton cloth. Harda is a dried powder extracted from tannin-filled fruit and because of high levels of the tannic acid; it functions as a pre-mordant link between the fibers and the various other ingredients. Once this process is done, it leaves a yellowish tinge to the fabric, which is why the term ‘pila-karna’.
3.Syahi: The word, syahi means ink and this is the process where the craftsman prints the black portion of the design during the process. The syahi printing paste is prepared while the raw, grey cloth is bleaching. Scrap iron, such as old horseshoes, blackens in a fire to remove rust after which it is steeped in an earthenware vessel with a quantity of gur (jaggery). The heat of the sun causes fermentation and results in a runny iron-rich solution after eight to twelve days.
4.Begar: After the black outline is made, the craftsman makes the begar, a mordant used for red. Alum is mixed with sticky tree gum paste and a pinch of geru red ochre to bring out colour in the otherwise transparent paste. The beggar paste is then applied using a ‘Datta’ block to fill in the ‘Rekh’ and highlight the printed areas. The alum is required to mature on the fabric for a few days. So once the Begar is filled in, the printer lets the fabric dry for about a week.
5.Dhulai: Once the printing is done, the fabric has to be thoroughly washed in order to remove the tree gum, so that it does not get soaked into the fibers during the next process. Also, for this process the printers usually prefer running water so as to not smudge the printed designs.
6.Ghan ki Rangai: Water is filled into a large copper vessel called the Tamda and it is set onto the bhatti hearth. Red dye matter is added into it along with shakur ka phool insect gall or dhaura ka phool fire flame bush and a drop of either castor or sesame oil. The printed fabric is set into the copper vessel and allowed to soak for about an hour before lighting the fire underneath. The temperature is gently raised over several hours. The chhipa stirs the cloth in the vessel and adds the shakur ka phool or dhaura ka phool if the red colour begins to spread from the begar printed areas. Alizarin is mostly used as the red dyestuff from the late 20th Century, though earlier the red dyestuff came from the roots of Al, Indian mulberry tree. By heating the cloth in the red dye solution, the red dye molecules chemically attach them selves to the areas printed with alum beggar mordant. Also, the black syahi becomes strong and colour fast.
7.Dhulai: The printer washes the dyed fabric in the running river water, so that the natural water can rinse and cleanse the fabric of the extra dye from the cloth.
8.Tapai: One last procedure is required for Sanganeri block-printed textiles to brighten the white background of the fabric and to bring out the printed designs. Tapai means ‘to warm’ and this process involves spreading the fabric and sprinkling it with mineral rich water from the rivers and letting it dry in the fierce power of the Rajasthan sun, side by side. The chhipa sprinkles it with water throughout the day and repeats this process for the next eight to ten days. Though the task is very arduous, it results in a bright white background and clear richly coloured butis and butahs.
The wastage in the process of hand block printing is immense when it comes to water and chemical wastes. Usually less fabric is wasted, as the dimensions of the block are multiplied to calculate the dimensions of the fabric to be printed on. The chemicals in the water seep underground, polluting the underground water of the area, and in turn leading to a lot of water wastage.
Sanganer began as a sleepy village located on the edge of a broad riverbank in the Dhundhar region of Rajputana now known as Rajasthan. Topographically, Sanganer was located on prime, fertile land at the band of the Aman-I-shah River. Although dams upstream now restrict the water flow, older residents of Sanganer still call the former river course Saraswati Nadi. The Kachchwaha Rajput prince, Sangaji, founded Sanganer in the early 16th century and the little dwelling was thriving by the 17th century partially due to its strategic location on major trade routes. Reminders of Sanganer's architectural heritage are still visible in the older quarters. Remnants of crenellated walls with gateways surround primarily 17th century public buildings and private 'havelis' mansions located within the crumpling ramparts. In 1727, Maharaja Jai Singh moved the capital from Amber in the Aravalli foothills to his new city of Jaipur situated on the plains below. The ruler recognized the importance of relocating close to Sanganer and established trade routes. In turn, Sanganer enjoyed increased activity because of its proximity to the bustling, new city. From then on, Sanganer's fate became entwined with the fortunes of Jaipur. After 1947 when the princely states of Rajputana were integrated into Rajasthan with Jaipur as the capital, Sanganer rapidly evolved from a satellite town into an industrial suburb of this rapidly expanding city.
The geography of Jaipur is significant. It has its location in Rajasthan state of Indian continent. It is the state capital of Rajasthan encompassing total area of 200.4 km2 (77 SQ MI). Strategically, Jaipur lies approximately at 26.92° N 75.82° E. Its height rises to approximately 432 meters or 1417 feet above the mean sea level. From Jaipur, popular tourist locales of the northern India, namely Delhi, Agra, Jodhpur, Udaipur, and Jaisalmer are not far off and also are connected by rail, road, and airports. It stretches to 232 km from Agra, 350 km from Gwalior and also 405 km from Udaipur. Places in the neighborhood form the boundaries of this Jaipur city. Sikar and Alwar bind it in the northTonk; Ajmer and Sawai Madhopur constitute the southern boundaries of Jaipur. Also Nagaur, Sikar and Ajmer lie in the west, Sanganer to the south.
Jaipur has a semiarid climate under the Koppen climate classification, receiving over 650 millimeters (26 in) of rainfall annually but most rains occur in the monsoon months between June and September. Temperatures remain relatively high throughout the year, with the summer months of April to early July having average daily temperatures of around 30 °C (86 °F). During the monsoon there are frequent, heavy rains and thunderstorms, but flooding is not common. The winter months of November to February are mild and pleasant, with average temperatures ranging from 15' 18 °C (59' 64 °F) and with little or no humidity though occasional cold waves lead to temperatures near freezing.
By Air - Jaipur Airport at a distance of around 11 km from the city center, is situated in Sanganer. There are direct flights to Delhi, Mumbai, Udaipur, Jodhpur, Aurangabad, and some other cities from Jaipur.
By Rail - There are many trains that connect Jaipur and other cities in Rajasthan; Palace on Wheels is a dedicated train for tourists. Other important trains include, Shatabdi Express and Pink City Express both from Delhi.
By Road - From Delhi, there is a direct and well-maintained road to Jaipur. City is connected to most of the tourist destinations in Rajasthan as well as Agra. Jaipur is part of the Golden Travel Circuit of India that includes Delhi, Agra, and Jaipur. Most of the tours are conducted either through the buses or trains.
One of the most prominent Jain temples here is the 'Shri Digambar Jain Temple' that resembles the Dilwara Temple structure at Mount Abu. The sky-high structure, complete with an ornate inner chamber, 'shikhars' (spires), intricate designs and a Parshwanath shrine protected by 7 serpent hoods, are the highlights of this temple. In the midst of underground portion, there is located an ancient small temple guarded by the Yaksha. The sacred temple has got seven underground floors, which are kept closed due to old religious beliefs, and visitors are not allowed to see them. It is said that only a Balyati ascetic Digambara saint can enter in it and able to bring out the Idols of this underground temple for a limited period, which is declared and decided previously. The idols thus brought out for viewing (Darshan) of devotees, must be placed back with in auspicious signs. The temple came in light when Muni Sudhasagar ji, a disciple of Acharya Vidyasagar ji visited the underground floors. He brought valuable, never seen before, Jain Murti made of precious stones from the underground floors in the presence of more than five lac Jain disciples.
The Hindu community, closely followed by a substantial percentage of Muslims, Sikhs and Jains, largely populates Jaipur. Hindi and Rajasthani are the most commonly spoken languages. The Rajasthani culture is colourful and flamboyant. It is rich in heritage. Famous dances of Jaipur include Ghoomar and Chari; the Chari dancers dance gracefully on a pot with a lit 'Diya' on their head. Traditional instruments like Sarangi, Ektara, and Jhalar are also played while singing folk songs. Food or the local delicacies of Jaipur also reveal the culture of the city. Jaipur's utterly delicious mangodi, papad, khichdi, buttermilk, sohan halwa have no match. There are a few prominent festivals celebrated in Jaipur.
- Married women who pray for a long and happy marital life celebrate 'Teej', a festival dedicated to Lord Shiva and Parvati, during the monsoon months July-August.
- Gangaur fair - Idols of Issar and Gangaur, manifestations of Shiva and Parvati, are worshipped by women, particularly the unmarried women who wish for a consort of the likes of Shiva.
- Elephant festival - This is celebrated during the month of Holi. The elephants are caparisoned, their bodies painted with floral decorations by the mahouts and paraded around with great pomp.
Jaipur is a land with vibrant culture and a thousand-year-old heritage. The people of Jaipur primarily speak Hindi in the Rajasthani accent. However, there are deviations according to various regions. The people of Jaipur are called as Jaipuris in the eastern part of Rajasthan and their culture epitomizes the very essence that the state of Rajasthan stands for royalty, chivalry, legacy, history, festivals and colors. The brown-skinned desert people are quite affable and win the hearts of the tourists with their sweet smiles and warm and cordial hospitality during any hour of need. People of Jaipur have been greeting their guests with regal courtesy and genuine affection for decades. Even in the era of kings and dynasties, these common people have left behind legends of loyalty, affection and compassion. Despite being rugged in their appearance, the people of Jaipur are well built, cheerful and simple. These desert folk are hardly touched by the swiftness of modern times. The people of Jaipur prefer to wear bright colored clothes and probably compensate for the barren landscape. The women are often seen clad in dazzling colors like Red, yellow, green and orange attires with eye-catching embroidery of gold, silver zari or gota. The tribal ladies of Jaipur love to adorn themselves with loads of Silver jewelry and the men too are often seen wearing earrings. The men wear turbans or pagadis of bandhej that is made in the process of tie and dye in bright colors.
The town of Sanganer is well known for the handmade paper industry and the Jain temples. The prints manufactured at Sanganer are also extremely popular and are unique in design. Floral, bold and block prints with bright patterns on a white background are the typical USPs of this settlement. At present, there are about 10 paper industries in Sanganer and countless Jain temples. Apart from the temples, the ruins of archaic palaces and frequent excursions to Hindu temples are also the highlights of the town.
List of craftsmen.
Team Gaatha