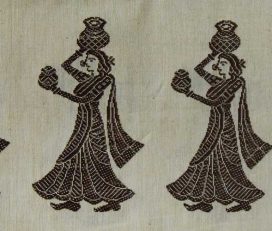
Gollabhama Saree Wea...
The Siddipet Gollabhama Saree is not just a piece of fabric; it is a living tradition, worn, celebrated, and reinterpreted through generations.
Siddipet, Telangana, India...
Music, they say, is the silence between two notes. The silence becomes even more omnipresent as it makes rare appearances between the constant sounds of metal being beaten in the ‘Thatheron ki gali’. This street in Jaipur is a home to utensil makers, locally known as the ‘thathere’ and is as old as the city itself.
The craft of the Thatheras constitutes the traditional techniques of manufacturing brass and copper utensils.
Thatheras, has a unique ethnic and historical identity with an oral tradition that underpin their skill. The very name of the community – ‘Thatheras’ is identical with the name of the element.
The crafting process is carried out by a specific group of craftspeople, known as Thatheras.
In Jaipur, this craft form flourished under the royal patronage of Sawai Jai Singh II. In 1727, Jaipur was established as a new capital by Sawai Jai Singh II (1700-1743) and artisans, craftsmen & merchants were invited to institute centres of trade in Jaipur. As a result, the ‘Thathere’ who had all along lived with the Maharajas in Amer Fort, came down to settle in Jaipur. But unlike other artisans who were beckoned for their knowledge of craft, the ‘Thathere’ artisans were summoned because they were absolutely necessary for their supply of utilitarian objects in the newly springing city.
Containers and vessels. Today the craftsmen are mostly approached for creation of Singhasans (royal seats) for idols, Chatris (umbrellas) and bells for temples.
Jaipur has been the hub of crafts and crafts people since ages. Metal vessels have been an essential household product since ancient time. These elements were necessary for storing water, food, drinking water, bathing etc. The thathera craft utensils are of both Utilitarian and ritualistic value made of copper, brass and ‘kansa’ (an alloy of copper, zinc and tin). The ancient Indian school of medicine, Ayurveda, recommends the metals used.
The Thatheras of Jandiala Guru in Punjab, India are a clearly defined community sharing a common ethnic, historical and geographical identity, which is connected with the ‘Jandiala Guru de Thathere’, or the traditional craft of making brass and copper utensils among the Thatheras.
The craft of the Thatheras constitutes the traditional techniques of manufacturing brass and copper utensils. The crafting process carried out by a specific group of craftspeople, known as Thatheras, has a unique ethnic and historical identity with an oral tradition that underpin their skill. The very name of the community – ‘Thatheras’ is identical with the name of the element. They belong to a single caste/social group called the ‘Khatris’, and follow a common hereditary occupation- that of processing metal and crafting utensils using brass, copper and kansa (an unusual alloy of copper, tin and zinc).
According to their traditions, they are Chandravanshi, Suryavanshi, Agnivanshi, Rajputs and Chandravanshi. They trace their origin from Sahastrabhu, who was killed by Parsuram. They also claim descent from the Haihay kings, a medieval Hindu dynasty.
It is believed that the bygone era had artisans who made- water vessels, ‘lotas’, large serving plates – paraat, paani ka ghada, mandir ka kalash. It is often narrated that huge silver water vessels were created for kings travelling away to foreign lands. One such vessel is housed in Jaipur’s city palace today.
It is believed that the food product stored in copper or brass metal is preserved well as compared to aluminium and steel. Copper and brass have certain kind of mineral content which is good for health. Therefore in early time people preferred utensils made out of copper or brass. Metal vessels became a ubiquitous household necessity in the primordial times as elements of storing water and other edible fluids, for kneading the flour dough and other common chores. The belief that is concurred upon even in these days of steel and aluminium is that food and beverages stored in copper and brass utensils were rendered preserved, whilst the mineral content of the utensil lent health benefits to the consumers.
The ‘thathera’ craft dates back to the Mughal Era, and later pursued by the craftsmen, who settled in Jandiala post-Partition. Thathere Walon Ka Rasta’ is located within the walled city of Jaipur. The lane is filled with the constant sound of hammering on metal. The place was an accommodation for around 300 Thathera, which today has reduced to 50-70.
In Jaipur, this craft form flourished under the royal patronage of Sawai Jai Singh II. In 1727, Jaipur was established as a new capital by Sawai Jai Singh II (1700-1743) and artisans, craftsmen & merchants were invited to institute centres of trade in Jaipur. As a result, the ‘Thathere’ who had all along lived with the Maharajas in Amer Fort, came down to settle in Jaipur. But unlike other artisans who were beckoned for their knowledge of craft, the ‘Thathere’ artisans were summoned because they were absolutely necessary for their supply of utilitarian objects in the newly springing city.
During the reign of Maharaja Ranjit Singh in Punjab, Amritsar was a flourishing trade and market centre along the Grand Trunk Road. Communities of craftsmen, carpet weavers, pashmina and woollen shawl craftsmen and metal workers from Kashmir and Rajasthan had settled down there making Amritsar their home. In 1947, before India was partitioned, a community of Muslim Thatheras used to live in Jandiala Guru. After partition, the Muslim Thatheras from India migrated to Pakistan, and a 400 strong community of Hindu Thatheras migrated to India from Kujranwala in Pakistan. This migration had brought about an exchange in culture between India and Pakistan. The establishment of the thatheras were known as ‘Bazaar Thatherian, Gali Kashmirian’.
Over a period of time the craftsmen have designed variously shaped hammers that give different impression on the metal vessel. The artisans also believe that these dents give strength to the vessel and prevent it from further damage. These hammer strokes also highlight the form and texture of the product. The most commonly used texture is called Matthaar. Apart from these artisans also do metal engraving, Chitaai etc. to enhance the product.
The desired utensil is always designed as a combination of parts, which are welded into a unanimous whole. Square or circular pieces are cut out of the flat metal sheets – Brass (70% Cu + 30% Zn) and Copper. The vessel they are intended for determines the gauge of these sheets.
Thathera work was once the biggest market of handmade brass utensils, even bigger than Moradabad and supplied to Haryana, Himachal Pradesh and Rajasthan. The craft is still flourishing with the demands of new market. The number of thathera artisans have been depleting over the years with only about 80 remaining of the 300 families who were brought to Jaipur by Sawai Man Singh II. Though the craft is flourishing in a lot of ways, the women of the households have to fetch water at least twenty times a day since the hand-pump does not satisfy the need of 70 people in the family. The various water tests performed show a much higher quantity of fluoride than essential. Their garbage is not collected and keeps getting pushed into side-lanes for a year until the ‘annual cleaning day’. Their living conditions have been deteriorating, causing the newer generations to move out and find other jobs that would provide them better living conditions. Beating and crafting the metal for centuries now, the Thathera community today is reeling under the pressure of competitive market and abandonment by the establishment.
The making of Thathera is a tedious process and does not pay well, so has been languishing over the past few decades. Most of the craftsmen sell their goods to shopkeepers in Tripolia bazaar of Jaipur and do not have direct contact with the client/ buyers. This craft has substantial potential for development. Some concerted efforts are being made within Jaipur to adapt this craft form to suit contemporary needs and respond to an evolving market.
Earlier the craftsmen were mostly approached for creation of Singhasans (royal seats) for idols, Chatris (umbrellas) and bells for temples. While light weight and low cost steel and aluminium utensils have largely replaced brass from the modern day kitchen, there still exists a group of dedicated admirers who appreciate them for their aesthetic quality and health benefits.
Thathera is the process of shaping metal, especially brass by beating it into fine sheets and molding it by hand. The community that practices it have come to be known as Thathera – a Hindu community found mainly in North India who are involved in the production of household utensils made from various kinds of metal alloys.
The main raw materials used in Thathera metal craft are outlined below:
Pattar (Metal Sheets) – Metals like copper, brass, iron etc. are used to make utensils of different shapes and sizes.
Suhaga – A powder used for welding.
Metal rod – Thin brass rods are used to join two metals while welding.
Gas – LPG gas is used for welding.
Lac – It is sometime used to fill the hollow metal and then carving is done on the metal.
Over a period of time the craftsmen have designed variously shaped hammers that render different patterns on the body of the metal vessel. As a matter of fact, the local craftsmen believe these multiple miniature dents make the sheet metal stronger and prevent further surface manipulation.
Tools used in Thathera metal craft are as follows:
Hatodi (Hammer) – Different sizes of hammers are used to shape the metal.
Wooden Mallet – Big size wooden mallets are used for initial shaping of big products.
Bangad (Metal ring) – It is a solid metal ring of iron on which the metal sheet is placed and beaten with the hammer along with simultaneously rotating it.
Thiya (solid metal stand) – Different shape and size of solid iron blocks are used for shaping the utensils. These act as a support while hammering the sheet.
Cheni (Chisel) – Different size and shapes of chisels are used to cut and shape the product.\
Metal Scissors – Small and big metal scissors are required to cut the sheet.
Files – Round, half round, flat and triangular files are used to finish the surface.
Prakaar (Compass) – Used for marking.
Aari (Saw) – For cutting the product or the metal artisans used saw.
Grinding machine – Used to clean and finish the surface of the product.
Buffing machine – Used in finishing process to enhance the smoothness of the final product and also to obtain the glossy finish.
Welding Machine – Helps in attaching two pieces of metal.
Pakad (Iron forceps) – Used to handle hot metal while welding.
Kharavar- An apparatus that keeps it in place while it is hammered and folded
Aavan- A specialised metal hammer.
Thathera is the process of shaping metal, especially brass by beating it into fine sheets and molding it by hand. The community that practices it have come to be known as Thathera – a Hindu community found mainly in North India who are involved in the production of household utensils made from various kinds of metal alloys.
The process of craft utensils is a lengthy, time taking, labour-intensive one.
1. Cutting the metal sheet:
The sheet (brass, copper or iron) is first straightened. Markings are done on the metal sheet using a scale, marker and compass, for the product to be made. The sheet is then cut either with a chisel or by metal scissor depending on whether the sheet is thick or thin, respectively. The shape can be square or circular depending on the final product.
2. Hammering to give shape:
In former days blacksmiths used a joinery technique, which involves creation of a subtle ridge, which camouflages the welding on further beating and finishing. The cut sheet is placed on the ‘Bangad’ and hammered on with wooden mallet or hammers. The wooden support of this tool is of indispensable importance as it equips the artisan with greater control for making dents, unlike a less preferred metal stem that might completely butcher the metal. The metal is beaten till it naturally bends along a concave or convex curve as required. Another important tool that assists this process is the ‘Bangad’ or a solid metal ring anchored in sand. This becomes the seat for the metal as it undergoes controlled bending. A sold iron rod bent at the tip, called ‘Megh khushiya’ further contributes to the process of handling the utensil while it is being textured. Traditionally ‘thiya’ is also used to shape the product or to make the neck of the vessels. The metal sheet is kept in continuous rotation for even treatment of the shape or the metal body. Vessels are usually made in two or more parts and then joined together by welding, like pots.
3. Joining the pieces:
Since, the products are made in different parts, they are finally joined at the end, either by heating or by gas welding. The artisans at times also join two pieces using the traditional technique of interlocking metals. These joints were converted into a design element by further heating and beating them. The pieces of metal were placed in a kiln/furnace made of mud (bhatti) and heated to high temperatures. The metal thus acquired would be more malleable and merge into one another to form a single mass as against the gas welding.
Today gas welding is used as it is less time consuming and easy. For this process both the pieces are heated till they become red hot. On the surface ‘suhaga’ is applied and a thin brass rod is melted which joins the two pieces. Melting the brass rod on the product, thus helping in joining the two pieces, fills the gaps.
4. Finishing:
The excess metal accumulated on the surface due to welding is removed by grinding machine or files once the pieces are joined and the product is ready. Then these items are washed with acid to clean the surface. The product is then buffed using buffs of different grades/numbers. These containers retain the impression of the hammer strokes that mould them, which in turn accentuate their forms and textures.
By the time, a product of koftgiri is finished, it is buffed and polished and leaves shreds of metal along with powdered metal as waste. These are usually given away to the recycling industry.
Jaipur was founded on 18 November 1727 by Maharaja Sawai Jai Singh II who was a lover of astronomy, mathematics and astrophysics. The city was named after him when he shifted the capital from Amer to Jaipur due to growing population and scarcity of water. Jaipur was a planned city and the layout was based on several traditional architectural treatises like the Vaastu Shaastra. In 1876, during the regime of Sawai Ram Singh, the whole city was painted pink to welcome Edward, Prince of Wales. Even today, these buildings remain painted in pink, giving Jaipur a distinctive appearance. In 1922, the throne was taken over by Man Singh II, during his reign buildings like secretariat, schools, and hospitals were built. After India got independence, Jaipur merged with Jodhpur, Jaisalmer and Bikaner to form the largest state of India with Jaipur as its capital.
Jaipur is located in the eastern part of Rajasthan at the co-rdinates of 26.92°N 75.82°E. It has an average elevation of 431 metres (1417 ft). The rivers Banas and Banganga pass through the district.
By air - Jaipur Airport at a distance of around 11 km from the city center is the main air gateway to Jaipur. There are direct flights to Delhi, Mumbai, Udaipur, Jodhpur, Aurangabad, and some other cities from Jaipur.
By rail - There are many trains that connect Jaipur and other cities in Rajasthan; Palace on Wheels is a dedicated train for tourists. Other important trains include, Shatabdi Express and Pink City Express both from Delhi.
By road - From Delhi, there is a direct and well-maintained road to Jaipur. City is connected to most of the tourist destinations in Rajasthan as well as Agra. Jaipur is part of the Golden Travel Circuit of India that includes Delhi, Agra, and Jaipur. Most of the tours are conducted either through the buses or trains.
Jaipur has a semi-arid hot climate with monsoon months bringing in 650mm of rain from June to September, the summer months of April to early July having average daily temperatures of around 30 °C and the winter months of November to February are chilly with average temperatures ranging from 15 to 18 °C.
Jaipur district is a centre for both traditional and modern industries. It is famous as a large exporter of gold, diamond and stone jewellery in Asia it is the only city finishing blue diamond, or tanzanite, in the world. It is a fast developing city and has every necessary infrastructure like airports, banks and educational institutes. Jaipur is a hub of educational activities from primary level to college level education. University of Rajasthan in Jaipur has completed its 60 years. Jaipur district is receiving the hydro-electric power, supplied by the Chambal Hydel System. Out of total 2,131 villages in the district, all were electrified (as on March 2000).
Jaipur was developed as India's first ever planned city by Raja Jai Singh with the help of chief architect from Bengal, Vidhyadhar Bhattacharya. Vidhyadhar Bhattacharya, following the principles of Shilpa Shastra (the science of Indian architecture), and referencing the ancient Indian knowledge on astronomy, devised the planning of the entire new capital. The town of Jaipur is built in the form of an eight-part Mandala known as the 'Pithapada'.
The city was divided into nine blocks, of which two consist the state buildings and palaces, with the remaining seven allotted to the public. Huge fortification walls were made along with seven strong gates for the purpose of security of the city. Jaipur city is remarkable among pre-modern Indian cities for the width and regularity of its streets which are laid out into six sectors separated by broad streets of 111 feet. This number is a holy number in Hinduism and hence considered lucky.
Jaipur is largely populated by the Hindu community, closely followed by a substantial percentage of Muslims, Sikhs and Jains. Hindi and Rajasthani are the most commonly spoken languages. The Rajasthani culture is colourful and flamboyant. It is rich in heritage. Famous dances of Jaipur include Ghoomar and Chari; the Chari dancers dance gracefully on a pot with a lit diya on their head. Traditional instruments like Sarangi, Ektara, and Jhalar are also played while singing folk songs. Food or the local delicacies of Jaipur also reveal the culture of the city. Jaipur's utterly delicious mangodi, papad, khichdi, buttermilk, sohan halwa have no match.
The prominent festivals celebrated are:
Teej- This festival is dedicated to Lord Shiva and Parvati; celebrated during the month of monsoon July-August by married women who pray for a long and happy marital life.
Gangaur fair- Idols of Issar and Gangaur, manifestations of Shiva and Parvati, are worshipped by women, particularly those unmarried women who wish for a consort of the likes of Shiva.
Elephant festival- This is celebrated during the month of Holi. The elephants are caparisoned, their bodies painted with floral decorations by the mahouts and paraded around with great pomp.
The lac bangles are crafted by the Manihar community who are traditional Muslim bangle makers. Many of them were rajputs who had converted to Islam. The community speaks Shaikawati dialect of Rajasthani.
The city is one of the most sought after destinations. It is famous for its architecture, vibrant handicrafts and arts.
Hawa Mahal - The palace of winds was built in 1799 A.D by Maharaja Pratap Singh. This five storied pyramid shaped structure is made up of small casements, each with tine windows and arched roofs with hanging cornices, exquisitely modeled and carved. This unusual structure is more like a screen than a palace, its top three stories are just a single room thick and at the base are two courtyards.Built at a time when ladies of the royal household observed very strict pardaa, this unusual palace, with its screened balconies provided them with an opportunity to watch processions and other activities on the streets without being observed themselves.
Jal Mahal - The lake palace was built in the middle of Man Sagar Lake near Amber. There was a natural depression in earth where the rain water of surrounded Aravali Hills was collected. No man made construction was there till 16th century. Natural beauty of lake, surrounded Aravali hills, lush green mountains, and migratory birds attracted Sawai Pratap Singh, the then-ruler of Amber. In 1799 AD, Sawai Pratap Singh decided to convert Man Sagar Lake in a pleasure spot; hence, he built Jal Mahal.
Jantar Mantar - This fascinating observatory was constructed in the year 1728 by Maharja Sawai Jai Singh II, the founder of Jaipur. He was a learned person and a great astrologer. He acquainted himself thoroughly with religion, philosophy, art, architecture, Hindu, Greek, Muslim and European schools of astronomy and astrology. He thoroughly studied Ptolemy's Syntaxis, De La Hire's Tabulae, Newton's Principia, Euclid's Clements, Mirza Ulugh Beg's Astronomical Tables, Master works of Aryabhatta, Varahmihir, Brahamgupt, and Bhaskaracharya. UNESCO inscribed Jantar Mantar Jaipur in the list of World Heritage in July 2010.
List of craftsmen.