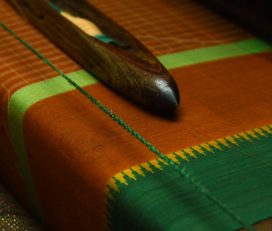
Saree Weaving ~ Nara...
Narayanpet sarees, handwoven in the small, vibrant town of Narayanpet in Telangana, are not confined to ceremonial grandeur or museum-worthy curation.
Narayanpet, Telangana, India...
Bandhani is one of the famous textile patterns in India. Bandhani of Gujarat is very famous in India. It’s a traditional textile of Gujarat. Wadhwan town in Surendranagar district has largest production of Bandhani in Gujarat. In Wadhwan around 75% of the families work in this profession. The process of making one Bhandhani is lengthy. This process is complicated and many different skilled craft’s men and women are involved.
This tie and dye craft of Wadhwan in Surendranagar is done to mostly produce lengths of fabric, which they later cut and sell according to dress sizes, unstitched clothing and saris. The locals wear bandhani on a daily basis as well as on special occassions. The bandhani of Wadhwan was so famous that other royal families of the state and country also used to buy bandhani cotton fabric from here.
75% of Wadhwan population is engaged in this business in one or the other way. Business of Bandhani was started in wadhwan by the Brahmkshtriya (Khatri) community and still most of the brahmkshtriyas are involved in this business. Now days other communities are also getting involved in this business. Main reason for this is that Wadhwan’s bandhani is famous in Gujarat and in other parts of India. Water of Wadhwan is one of the key reason for the development of this business here. Wadhwan is also the place where the Bandhani was born. Wadhwan’s soil
was also a reason for development of this business. In olden days when colours where made from the natural elements the soil of Wadhwan had the widest range of colours available at that time. Later with time, due to modernization and competition now they do not use the natural colour any more.
The history of dyeing can be dated back to pre-historic times. This art finds its mentions in the Alexander the great time texts about the beautiful printed cottons of India. As per evidences in Historical Texts, the first Bandhani saree was worn at the time of Bana Bhatt`s Harshacharita in a royal marriage. It was believed that wearing a Bandhani saree can bring good future to a bride. Ajanta walls stand for the evidences of these Bandhani sarees. The dyers have experimented with the use of different elements both natural and man made for ages. Also there are experiments with different binding/tying techniques to create patterns on cloth immersed in containters of dye.
The wide variety was evolved over the centuries because of its close links with the religious and social customs of different people. Bandhani work involves tying and dyeing of pieces of cotton or silk cloth. The main colours used in Bandhani are yellow, red, green and black. Bandhani work, after the processing is over, results into a variety of symbols including, dots, squares, waves and strips. The main colours used in Bandhani are natural. In fact all colours in bandhani are dark, Rajasthan is one of the most important centers of the tie and dye textile. Each area, each caste and each tribe has its special designs.
The main colours used in Bandhani are yellow, green, red, pink, and black. The colors commonly used signify different things like -“ red, a symbol of marriage, saffron, a color worn by yogi who has renounced the world, yellow, which stands for spring and black and maroon, used for mourning.
Bandhni material is sold folded and with the knots tied. One has to pull the folds apart for the knots to open. The payment is made according to the number of dots in the pattern. An intricate design in a sari would have approximately 75000 dots. What is essential in bandhni is the minute and skillful manipulation of the fingers for tying, extensive knowledge of color schemes and skill in dyeing materials. It takes several years for a craftsman to perfect his skill.
Basically there are two types of Bandhej:
– Bandhej for design
– Bandhej for basic colour
Bandhej for Design
This Process is mostly done by women at home. So once the distribution of design cloths is done to these women, they do the bandhej at home. Bandhej for design is a very fine small bandhej which needs time and accuracy. Once this bandhej is done it goes back to wholesaler and they send this cloth for colouring. Once the colour is done if design needs more bandhej, then it again goes to the ladies for one more bandhej and then again for colouring.
Bandhej for Basic colour
This Bandhej is done when the cloth is sent for the colour and it is done by the person who is colouring the cloth. This bandhej is done using polythene and plastic thread as shown in photo. After this bandhej it goes for the colour. After colour this polythene are used again for the bandhej for other similar bandhej. If the design demands more small and different bandhej it again goes for design bandhej. If not then after colour they left it open to sky to dry. In summer it takes around 4-5 hours to dry, in monsoon sometime it takes 2 days to dry in and in winter it takes 6-7 hours to dry.
The craftsmen face no challenges as of today but the craft in general is causing harm to the environment because the constant mixing of artifical colours with groundwater.
For making this colour they use below listed materials. This combination can colour around 40 pieces of cloth:
Colour – 350 gm
Alum – 350 gm.
Sodium- 175 gm
Powder – 50 gm
Sulphate Sodium – 50 gm
Water – until it mixture become paste
Acid – 150 gm
VAT Dyes: are mostly used in this process
Thread: of a constant thickness is used for tying
Large Utensils and mugs: to dye the fabric in
Gas Stove: To heat the dye bath
Gloves: To keep the hands clean
The process of making Bandhani includes several stages like cutting cloths, farma making, transferring design on cloths with the help of farma, bandehj, colouring, removing bandehj, drying and removing the final bandhej. If it’s two or more colour Bandhani then it needs a bandej and colouring again.
The name Bandhani comes from the word Bandhej which means tying in Gujarati. The whole piece of cloth is tied according to design and then it is coloured.
1) Cutting cloth: Wholesaler buys the cloth from the market and sends it to the person who transfers the design on the cloths. As soon as cloths arrives this person, cut the cloth according to the design. Since Bandhani is a textile pattern one can make Panjabi Dress as well as Saree from bandhani. So the cloth is cut according to the kind of the dress it will be. The cloth from the wholesaler comes in different sizes of width and length according to their requirement. The person who cuts the cloth he is the one who transfers design on the cloth. Hence after cutting he sits to transfer the design through Farma.
2) Farma: Farma is a transparent plastic sheet, on which the design is created first. This design is created Either by Professional Designer or By Wholesaler or sometimes by the craft people themselves. In this case, the craft person is the designer and he sells his design to the wholesaler. Once the design is approved they create small pin holes in the plastic sheet. With the help of these pin holes Design is transferred on the cloth.
3) Design Transfer: Once the Farma is ready they lay bundle of the cut cloth on the ground. Then they put Farma on top of it. Then with the help of the colour water and Squeeze they transfer the design on cloth. Since the size of the cloth is big, for good transfer, this process requires two people to do it. Once the Design transfer is done this person sends this transferred cloth to the wholesaler who, later Distributes to the ladies who during their free time do the “Bandhej- work.
4) Distribution for Bandhej: Once the design is transferred and delivered to the wholesaler, he distributes this cloths to the Ladies. Bandhej is mostly done by women. These women come to the wholesaler everyday to collect the new design for Bandhej and to return the ready Bandhej which then goes for colouring. When these ladies come to collect the cloth for Bandhej, along with the cloth, they are provided with thread rolls. These ladies have accounts with the wholesaler. He writes and maintains the account for them and pays them accordingly. The payment of these Bandhej is decided by ladies after looking at the design and detail of the work. Smaller the Bandhej more charge and it also varies on the amount of Bandhej needed to be done. In the next chapter I will be explain the porcess of Bandhej.
5) Bandhej: Bandhej means tieing knots in the specific pattern. This knot is tied because when this tied cloth goes to colour this knot doesn’t let that part catch colour so it stays white or whatever colour of cloth has. Bandhej is the main part of the bandhani making. Bandhej is the process which is repeated many times in the making of one Bandhani. Every bandani mostly has bandhej two times. First time when it’s distributed to Ladies for bandej and then when it goes colour. If the bandhani has two colours as base colour then the people who colour the cloth, also tie a big bandhej which is different than the small bandhej done by ladies based on design.
6) Dying: After Bandej for Colour is done it goes for colour. It is not necessary that every piece of design has Bandhej for Colour. Some might have only design Bandhej. These kind of cloth directly goes for colour. Again colours are decided by the person who has designed it. In olden days the colours used were natural colours but now a days they use artifical colours.
Once the colour is made then they dip cloths into it for around 1 -1.5 minutes per cloth. Then it goes for drying. This process is used when base colour is light and the colour which will now be added is dark. If it is other way round they have to do another process which is called ‘wet colouring’ . In that materials are same but it is done on the stove. After colour it goes for Drying or for removing Bandhej.
7) Drying: The drying is done on the terrace. Drying takes some time depending upon the weather conditions. In monsoon it takes around 1.5-2 days to dry while in summer it takes only 4-5 hours. In winter it takes around 6-7 hours for drying. After Drying if there is more bandhej required, then it goes for bandhej through wholesaler or through the colour person depending upon the deal. If there is no more requirement of any Bandhej then it directly goes to wholesaler and wholesaler sends it to retailer. In between this sometime Deknoting of bandhej happens depending upon design. Small amount of deknoting happens at retailer’s end. Wholesaler never does anything.
When the bandhej is opened, the strings it was done with become waste and are disposed. The other waste is the synthetic colour which is thrown into the ground and slowly pollutes it.
The region of and around Surendranagar was possibly under the control of other traditional dynasties ruling over several varied regions of the state of Gujarat though no significant information is available about the past history of Surendranagar.
After the mobilization of the states, the now Surendranagar district was called Jhalawad. The present district, which is called Surendranagar, was the head quarter of the British political agent. Political agents left from the Wad van camp and returned it to the ruler of Wad van in the year 1946 AD. There after it was named Surendranagar again in 1947 as per the name of the past king of Wadvan, Surendra Singh ji. Since 1948, Surendranagar has remained as the main center of the district. Surendranagar is one of the districts of the Saurashtra sub state.
Architectural research has been done on a small scale in the district and some places of pre-historical habitation are found. In the year 1957-58 some equipment of the era after the stone age are found from Sejakpur in Sayala taluka. This depicts the culture of the era after the Stone Age, which had the economy, principally, of the hunters and fishers. The equipment used by the people at the start of the mythological era is also found from this district.
The district occupies an area of 10,489 square kilometers (4,050 sq. mts). As of 2001, it has a population of 1,515,148, out of which 26 per cent live in cities. Surendranagar District of Gujarat is situated between 22°00' to 23°05' North altitude and 69°45' to 72°15' East longitudes. The district has Ten Talukas and two main industrial and commercial centers of Gujarat and Saurashtra, are at equal distance from Surendranagar.
It has an average elevation of 128 metres (420 ft). The city is located on the bank of Bhogavo River, which remains dry except the monsoon months of July to September.
Surendranagar has a semi-arid climate, with hot, dry summers from mid-March to mid-June and the wet monsoon season from mid-June to October, when the city receives 590 mm of rain on average. The months from November to February are mild, the average temperature being around 20 °C, with low humidity. One of the most important weather phenomena, which are associated with the city of Surendranagar, is 'cyclone'. The cyclones generally occur in the Arabian Sea during the months after the rainy season. The region experiences a lot of rainfall and high-speed winds during the time of the year after the monsoon season as well as the months of May and June. However, June experiences lesser amount of rainfall and winds than the post- monsoon time. Thunderstorms are another important part of the weather in the months of June and July. During summer time, the temperature ranges between 24 °C and 42 °C. In the months of winter, temperature varies between 10 °C and 22 °C but on a whole winters are pleasant.
The city of Surendranagar is well equipped with a bus stand and a railway station with the nearest airport at Rajkot, about an hour away. There are hotels with a range of varied tariffs to suit customers from different financial strata. There are shops in the market places for all kinds of necessities and the city has higher secondary schools, twenty-four hour electricity, hospitals and educational institutions. The roads are mostly permanent, though in the interiors of the city and surrounding villages, there are still temporary muddy roads. Local transport is plenty and comfortable.
Houses in the area are of a lot of kinds. Mostly, the houses are bricked and cemented with clay tile roofs. Some houses are big, up to three storeys big and painted in bright colours with a courtyard and area for vehicle parking. There are mud houses in the interiors, which are small and have thatched roofs. Some are even brick houses with clay tile roofs. In the older houses, which are mostly made of bricks and wood, the balcony railings have elaborate intricate metal work in shapes of vines and lower tessellations. The windows and doors of the older houses are big wooden ones and have carved designs as well.
A Hindu dominated area; all the Hindu festivals are celebrated with much enthusiasm and valor. They have elaborate rituals both communities oriented and religious, signifying a very vibrant culture. Navratri is celebrated with great luminosity and is awaited all year round. Houses are decorated and lit up on all major festivities with a play roll of the local music and dances. Lord Shiva and Lord Hanuman are the two Hindu deities that are largely worshipped in this region, with temples at a distance of every few meters throughout the town and its outskirts.
The people of Surendranagar are called 'Kathiawari' Gujaratis and this community have a way of life different from other Gujarati communities. Their accent and language of Gujarati differs variedly and they have differences in cuisines and culture as well. The women of this area mostly wear bandhani saris when married and salwar kameez with bandhani dupattas before marriage. The men wear kurta pajamas on special occasions and trousers, shirts and tshirts on a regular basis.
Raj-Rajeshwari Temple, on National Highway Number 8 near Limbdi, is a large area of residences, hospitals, and schools. The temple features an exhibition of yoga performed by Rishiji. This temple has temples to three major gods' Brahma, Vishnu, and Mahesh' inside. It is the only such temple in Gujarat. The temple is noted for its architecture.
The famous kund known as 'Gangavo' is located in Dedadara village. It was developed in the 11th century. 'There are many cultural institutions' Shabdalok sahitya vartul (founder: Dr.Nagjibhai Desai)
Nanalal sahitya sabha (Ramesh Acharya) Kalamandir Group (founder: Atulkumar Vyas) Club of Desert lions.
List of craftsmen.
Cluster Visit & Interview (3.Nov.2013)
http://theindiacrafthouse.blogspot.in
http://www.dsource.in/resource
http://www.indiamarks.com/bandhani-indian-tie-and-dye/