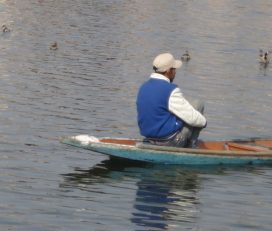
Shikara (Boat)~ Kash...
Also called the ‘camel of Dal Lake’ due to its importance, the multi-functional shikaras are a lifeline for the people of Kashmir.
Srinagar...
Panja weaving’ forms an important part of India’s glorious weaving tradition and is mostly used for making durries, (light woven rugs used as a kind of floor covering). The craft gets its name from a metallic claw-like tool called ‘Panja’ in the local dialect, used to beat and set the threads in the warp. Unlike carpets the panja dhurries are woven and not knotted, making them light and usable on both sides.
The making is what chiefly distinguishes a durrie and a carper as the former is woven flat while the latter is knotted. The durrie is also lighter, reversible, more flexible, and made using cotton most of the time, unlike carpets that have a more rigid making style and are usually made using wool with one display side.
Famous for their durability and quality, the Punja dhurrie derives its name from the claw-like metal tool called Punja used to beat and set the threads in the warp while making.
Durries have been proved to be effective in preserving heat during winter and for being cool during summer as they are made chiefly of natural cotton.
Durries are made in either vertical loom or pit loom using cotton or woolen yarn. Before the weaving takes place, the yarn is dyed in vibrant colors.
Durries/dhurries have an interesting history as traditionally there are accounts of prisoners making this craft during the Mughal rule. In the 1850s, durrie weaving became a commonly found activity in the prisons after being introduced by the Maharaja of Jaipur Sawai Ram Singh as part of the prisoner reform program. In the 1930s, Bikaner Central Jail was awarded the top prize at the All India Weaving and Printing Competition organized by the Government of United Provinces.
Being a highly versatile product, ‘Durries’ have a wide variety of uses depending on its size, pattern and material. The smallest ones ranging 12 by 12 inches are used as table mats to keep flower vases, while a moderate sized durrie of 24 by 24 inches known as ‘Aasan’ is used as yoga mats and for meditation. A large durrie of about 20 feet by 20 feet is used for large gatherings like a political or social gathering. Traditionally, Dhurries were used as floor coverings, but due to their attractive and intricate patterns they are also used as wall hangings. Due to their low cost and ease of maintenance, Durries do not get infected by pests and insects like ‘silverfish’ that often affect carpets. Having versatile nature cotton durries helps in keeping warm during winters while it has a cooling effect during summers.
In the study of crafts, durries were earlier dismissed as a poor man’s carpet and undermined in its value. But with time it soon became popular due to its abstract patterns and contemporary design appeal. Being woven these durries have an advantage of being reversible, which enhances its functionality. In comparison with carpets, they are lighter and its weaving method provides better flexibility in creating more varied designs. The craft of durrie making is mostly practiced by women of the house. The craft requires a simple set up of a ‘punja’, a ‘pit loom’ or just two horizontal bars that are used to weave by hand. This basic set up enables them to practice the craft efficiently. Durrie making uses two basic techniques; the ‘punja’ technique and the traditional ‘pit loom with the fly shuttle’. The Punja technique requires a simpler set up than the traditional pit loom. Cotton is mostly handspun by women while yarns are dyed by men.
The origins of dhurrie can be traced far back to the ritualistic floor paintings in India. In the Hindu and tribal communities, drawing patterns on walls and home floors was believed to be a powerful religious charm that would ward off evil spirits and energies form their houses. These patterns were drawn as a prayer to invoke the deities and ask for protection from negative energies. In this way the merging of religious belief systems and a love of art and decoration gave rise to an intricate art where the homes became the canvas. Even in the Hindu religious epic ‘The Ramayana’, Goddess Sita is mentioned decorating the threshold of her home with religious designs. The Ramayana mentions Sita decorating the threshold of her home with sacred designs. Even today in various parts of India, these floor decorations are made as part of different religious festivals and are known by different names such as ‘Rangoli’, ‘Mandana’ and ‘Kolam’.
In many traveler accounts of the 13th century, there are descriptions of the floor mats of India. It is mentioned that palm leaves, reeds and other dried foliage were used to make floor coverings for their qualities like water resistance, cooling capacity and easy storage (they could be rolled up and stored in corners or shelves). A painting made in the late 18th century for Lady Impey, wife of British governor of Bengal, depicts a striped Indian dhurrie covering the floor of a nursery.
The ‘Sitalpatti’ mat of Bengal, Assam and Tripura was woven on a loom with cotton warps for the finest and most flexible mats. Animal skins were also used as floor coverings and were commonly depicted in Persian as well as Indian miniature paintings. Tiger and leopard skins were symbols of high stature and power. In many records of 19th century, ‘dhurrie’ is referred to as a ‘Dari’ or ‘Satranji’ in the northern parts of India and as ‘Jamkhani’ in southern India. The earliest surviving relic of the ‘Indian dhurrie’ can now be seen in the British Museum in London where it has been permanently housed. It is a cotton rug fragment found by ‘Sir Aurel Stein’ in 1901 at the ancient ‘Niya’ site in Turkistan. Carbon dating puts it between first and third century AD.
The earliest depictions of the dhurrie, is found in the painting of Mahajanaka Jataka found in Ajanta caves. In the painting King Mahajanaka is depicted standing on a plain Indian dhurrie. In ‘Ain-i-Akbari’ of the Mughal era, there are references to the production of ‘Satranji’ or flat weaves, in the royal workshops of Lahore, Agra and Fatehpur Sikri. Many other references are present in the paintings of Mughal emperors such as ‘Shah Jahan in Darbar’ (c.1630), ‘A Night celebrating the Prophet’s Birthday, ‘Agra’ (c.1635) etc. The ‘Calico museum of textiles’ in Ahmedabad houses one of the finest examples of the Indian flatwoven rug. It was originally in the ‘Ambar’ palace in Rajasthan. It has a cotton warp and woolen weft, and is believed to have been woven in the middle of the 17th century in Lahore. In the early 19th century, during the peak of the British rule, dhurrie manufacturing flourished immensely as it entered a highly organized phase where details of crafts and industrial projects were logged. A dhurrie with a tile design was used as a backdrop in the Indian pavilion during the ‘Great Exhibition’ to promote trade at the Crystal Palace, London.
As dhurri making craft could be made in small productions, many prisons took to it as a professional and recreational activity for the inmates. In the late 1930s, the ‘Bikaner central jail’ won the ‘All India Weaving and Printing Competition’, awarded by the government of United Provinces. This broadly divided weaving into two organized sectors; private industry and prison industry. Apart from these a third but very important sector was the village industry. The private and commercial sectors were taken forward with workshops in towns and setting up of cotton mills. Slowly production was only concentrated on ‘striped dhurries’ and niche ‘prayer mats’. It must have been the pressure to buy only British mill produced products, that caused the striped dhurries to be found all over India. The monographs written in the 19th and early 20th centuries concentrated on the village industry – the locally owned productions and workshops.
The prison workshops were among the many reforms and enterprises by the maharajas. They proved to be a fierce competition for the private industries. Maharaja of Jaipur, Sawai Ram Singh II, was believed to be a pioneer in such a move – he built a new jail in Jaipur in 1856 AD, introduced reforms and the idea of employing prisoners for skill based activities.
Dhurrie weaving has grown to be one of the richest traditions in India, and a significant aspect in the life of many villagers. The tradition has been passed on through generations and holds a vast decorative vocabulary of cultural symbolism. Designs have been handed down with the intention of passing on skills as well as in the form of dowry. In Madhya Pradesh, the main centres for dhurrie production are ‘Sironj’, ‘Jhabua’, ‘Raigarh’, and ‘Jabalpur’ where women mainly practice the craft in their homes. Dhurries of these regions are famous for their strength and sturdiness as well as choice of bright color palettes.
The main patterns and motifs in dhurries are mostly geometric in design. A wide range of designs exists which contains inspirations from local architecture, flora and fauna. Stripes, geometric variations, sprawling wines, peacocks, tree of life, hunting scenes, medallion patterns etc are the most commonly seen designs in dhurries. Kiln designs are also replicated in the dhurrie weaving. Popular tales and stories are also depicted in the dhurries.
The dhurries of Madhya Pradesh conventionally have a pinkish white background with patterns in bright red color. The motifs are separated by black or bright red color lines. The skill of the craftsmen can be judged by the level of complexity in motifs like the ‘Neempatti’ motif which has 24- petal flowers surrounded by flowers and leaves. The ‘Surajmukhi’ or sunflower design is another popular motif.
Even though durries are a much sought after product, the craft profession is on the decline, with many craftsmen families moving to profitable professions. Surveys indicate that even low income groups such as laborers (agricultural or construction) are paid 150 rupees a day, which is far more than the measly 75 rupees a day that a durrie craftsman earns making it the lowest paying profession.
Owing to the poor state of this trade, many families traditionally involved in this trade prefer to get their children employed in other trades, which pay better. This has reduced the number of durrie looms in Sironj, from a large number of five hundred to about a handful of ten to twelve only. Due to lack demand many small mills in Indore and Bhopal that earlier provided durrie threads, have now shut down. The craft is now being revived by the ‘Bunkar Samiti’ but the process is slow.
Attractive and sturdy dhurries are woven on pit-looms or vertical looms using cotton or woolen yarns. Before weaving begins the yarn is dyed in vibrant colours according to the designs which are traditional as well contemporary variations.
Cotton-hand-spun or mill-spun yarns
Wool- hand-spun or mill-spun yarns of wool are used.
Waste-Waste fabric pieces from saree, fabric etc.
Taana machine– Thread is unwound from reels and wound around an octagonal drum of the Taana machine.
Loom– Hand operated pit looms or vertical looms are used to weave dhurries.
Charkha– Rolls or bundles of yarn used for ‘weft’, are made using the ‘charkha’.
Punja– It is a metallic claw-like instrument that is used in pushing the weft threads together to create a tough and stable dhurrie. Strength of the dhurrie increases with each beating.
Scissors or clippers– Excess knot and protruding fibers are cut away using scissors or clippers.
Attractive and sturdy dhurries are woven on pit-looms or vertical looms using cotton or woolen yarns. Before weaving begins the yarn is dyed in vibrant colours according to the designs which are traditional as well contemporary variations.
Designing
Weavers of this craft have achieved a level of mastery in the traditional designs and are well versed in it. Any variations in the traditional designs or addition of new designs are provided by the master weaver in the form of a sketch, and are referred to during the process of weaving.
Dyeing
According to the requirements in the design, the yarn is sent to be dyed by the specialist dyers. Both chemical as well as natural dyes are used. The yarn that is dyed using chemical dyes is more evenly coloured, whereas the yarn dyed with vegetable dyes is mostly in uneven shades. The direct dyes give vibrant colours and are mostly used for fly-shuttle dhurries, though they bleed color on normal washing. The yarn is stocked in the form of loose bundles and is knotted at the center. These are put in a tank that contains boiling water to which the dye of desired color is added. The yarn is kept submerged for about 10 minutes and then taken out and dried. This process is repeated again till a uniform shade is achieved.
Opening up the weft yarn
The yarns that come from the dyers arrive in bundles and need to be detangled and loosened before it can be used for weaving. A charkha is used for the process, where one end of the thread is tied to a small reel called ‘Gitta’, which works as a smaller wheel of the charkha. The turning of the ‘Gitta’ pulls the yarn thread from the larger wheel to the gitta forming a reel with tightly wound, uniform and tangle free yarn.
Warping
The taana machine is used for this procedure. According to the colour combination in the design, thread rolls are set on movable vertical frames. The ends of the threads are passed through grid-like frames and wound onto a big octagonal cylinder. Once the desired length of yarn is wound around the cylinder, the log upon which the taana is to be wound is fitted into the blocks between the cylinder and the frame. The weaver then uses this as the warp on the frame of the loom.
Weaving
1) Traditional pit loom
In this loom, the weaver sits at ground level with the legs inside a pit which contains the pedals. The warp from the log is wound over another log. The threads are guided through metallic reeds till it reaches the ‘Hattha’ or frame which is used to beat in the weft threads. Screws on the loom beams are used to adjust the tension of the warp. One dhurrie is normally made in a few hours.
2) Panja technique
In a vertical loom, two layers of warp are bound on two beams that pass through the reed while weaving. There is a small bench before the loom, facing the warp, on which one or two weavers sit and work. The number of weavers depends on the width of the dhurries. The design is kept in front while weaving and is used as reference. The warp is marked at regular intervals to remind the weaver about a particular motif or feature. After a row of weft is woven, the weavers beat it using the ‘Panja’ tool and comb it so that it gets compacted to the warp. Once this is done, the weaver interchanges the layers of the warp using the ‘Kamana’ (a V shaped wooden frame) and ‘Ruchch'( rods which the Kamana is attached to). This locks the weft between the two layers of warp, making the dhurrie strong and durable.
Finishing
Once the weaving is done, the ends of the dhurrie are knotted and any problems are rectified. If the dhurrie has developed differential width at fringes due to shrinkage, it is kept stretched on a frame for a day or two. In case a stone wash is needed, the dhurries are sent to be washed with water, detergent and potassium permanganate. The finished dhurrie is then sent to a clipper who clips away all the protruding threads to give it a smooth finish.
Sironj was ruled by the Nawabs of the Tonk province in Rajasthan till 1956 AD. It was a part of the Malwa region, lying beside the Bundelkhand region. Earlier known as Sironcha, it was an important peg in Jain pilgrimage, trade and military conquests since it lies in the south to north and west route from Burhanpur to Surat or Agra. For the Digambar Jains, it was the Atishaya Kshetra. In trade, it was the centre for calicos cotton(Maheshwari), kalamkari works and Muslin cloth trade. The Maheshwari traders had soon left Sironj when they took offence to the Nawabs actions. When it was ruled by the Mughals, a Mughal district in Sironj catered to the trade of water cooling pots and flat-woven mats, directly to the ports of Gujarat. It was the halting station for the army of Ghiasuddin Khan, the governor general of Gujarat and Malwa. He was commissioned by Nizam-ul-Mulk to launch an offensive against the Peshwa Baji, during 1738. Ghias-ud-din was unable to conquer the Konkan and retreated. Some members of his army are believed to have stayed back in Sironj. The city also sheltered Tantia Tope during the revolt of 1857.
The city lies at 24005' N Latitude and 77 050' E Longitude and is 300m above mean sea level. A tributary of the Betwa River runs through Sironj and has a hilly terrain. The terrain can be divided into four parts -The Valley of river Betwa proper, The Bina Valley, The Eastern Range, The Western Range and the Sindh Valley. Sironj city lies in the Malwa region characterized by Black cotton soil and drained by 2 small rivers namely, Kethan and Naren.
The city is strategically located at the intersection of two State Highways - SH 23 and SH 14. Siroj lies approx. 120 km north of the capital city Bhopal. Vidisha district is surrounded by Guna and Ashoknagar districts towards North, Sagar district to its East, Raisen to the South and Bhopal district to its West; thus offering it excellent connectivity and proximity to prime commercial nodes in Madhya Pradesh.
By Road - There are frequent buses going from Bhopal to Sironj, a journey of about 2.5 hours.
By Rail - The city does not have direct rail connectivity, the nearest Railway Station being Ganj Basoda, 45 kilometers east of Sironj.
By Air - The nearest airport in in Bhopal
Sironj has a semi-arid climate with hot summers and pleasant winters. The temperatures peak to a maximum of 45 deg celsius during the summer months of March, April and May. During the winter months from December to February the night temperatures fall to a minimum of 4 deg celsius. Humid heat sets in with occasional relief of rainfall during the monsoons spanning June to September. The city receives an annual average rainfall of 960mm.
Sironj lies in a part of the great Vidhyanchal range .The main crops cultivated in Sironj are wheat, maize and gram in winters and soyabean and lentils in rains. Scrub forests rich in flora and fauna lie in the periphery of the city. The trees native to this region are Teak, Sandal and Sagwan. These are under great threats of deforestation and grazing pressure.
Sironj is a growing city with a municipal area of 10 sq.km, divided into 21 wards. Agricultural occupation is the main contributor to Sironj's economy. Beedi making and Dhurrie making are flourishing household industries. Sironj does not have a development Authority. Bhopal development authority was established in October 1976 to plan and implement the integrated city development plan of Bhopal city, with a view to meet the needs of people in urban as well as rural areas.
There are no factories in the city. Water supply for drinking and irrigation is from the dam on the river Kethwa. The bazaar or mandi is a bustling hub where all the daily necessities are purchased. Sironj has a district hospital and other medical facilities. Higher secondary schools and colleges are located around the periphery of the city. Electricity supply in Sironj is under MPSEB (Madhya Pradesh State Electricity Board) which deals with generation.
The erstwhile architecture of Sironj is an amalgamation of various influences, depending on the changing rulers and dynasties. Today, the city is specked with many old mosques and ancient temples. The Jama Masjid in Sironj is said to be built by Aurangazeb. There are ruins of an old observatory, which is believed to have be one of the three observatories Sir George Everest organised to measure the height of Mt. Everest. This survey was later completed by Radhanath Sikdar using a Theodolite. The ruins still exist exist in a village called Bhoori Tori.
The Girdhari temple is a 11th century temple in Sironj known for its exquisite sculptures and fine carvings. Temples dedicated to deities Jatashankar and Mahamaya are said to be very old and sacred. The Mahamaya temple is the site of the grand annual fair of Sironj. It lies 5km southwest of the city, on a small hill. The inner city has narrow lanes flanked by shops and stalls. The residential areas are towards the outer regions and consist of both pakka and semi pakka construction. The houses in the outermost regions are slum houses or have mud-walls with thatched roofs.
Sironj has a religious diversity comprising of Hindus, Muslims and Jains. The village population is mostly Hindus whereas the town area has both Hindu and Muslim population in equal numbers. The Jain population in Sironj is a very small number.
The Sironj Mahotsav is a 9-day long grand annual fair. It is celebrated with much aplomb with performances by celebrities as well as with dances like Gutumbaja, Kalbeliya and Badhai. Cattle owners deck up their cows in bright and colourful attire, and parad them across the city part of 'Gopa Ashtami', a festival when cows are worshipped.The other major festivals like Diwali, Eid, Ram-navami, Ekadashi etc are also celebrated.
The traditional attire of the people of Sironj are sarees or salwars worn by the women, and the dhoti-kurta worn by the men. Shirts, t-shirts and pants also form the clothing now with contemporary influences.
Other than the Hindu, Muslim and Jain classification, the Mina tribe is also native to Sironj. They are mostly farmers and also depend on animal husbandry, labor and service for their livelihood. They mostly speak Braj and Hindi. They are non-vegetarians. Wheat and rice are their staple cereals. Soya bean and mustard oil are used in cooking. Alcoholic beverages are consumed by them regularly.
Ruins of an old three tiered market still exist in Sironj. This is a rare and famous kind of arrangement. In a single building, there were shops that were partly underground and partly on the surface (meant for customers on feet), shops that were slightly raised (for the customers on the horseback) and shops on the first floor (for the customers on elephant -back). Many of these shops survive.
The dhurries of Sironj are famous throughout history. It was a prominent part of trade to western countries. There is an entire locality in Sironj called the Dari-wala Mohalla.
List of craftsmen.