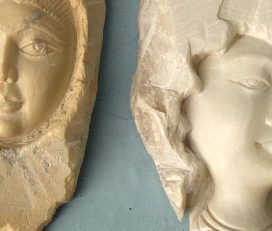
Stone Carving~ Jabal...
Stone carving in Jabalpur reflects a deep connection between material, sacred symbolism, and evolving aesthetics.
Bhedaghat, Madhya Pradesh, India...
Damascening is the art of encrusting one metal on another, which are soldered on or wedged into the metal surface to which they are applied, but in the form of wire, which by undercutting and hammering is thoroughly incorporated with the metal which it is intended to ornament. Damascening is now practiced with great success in India, Persia and Spain.
Koftgiri is the technique of encrusting one metal onto another.
Koftgiri craft is damascening the art of encrusting one metal on another, which are soldered on or wedged into the metal surface to which they are applied, but in the form of wire, which by undercutting and hammering is thoroughly incorporated with the metal which it is intended to ornament.
Koftgiri has been closely guarded through generations in the community of ‘Sigligar’.
Damascus steel was the material used to produce the famous Damascus sword blades renowned for remaining extremely hard and sharp, yet able to be bent to a 90 degree angle and spring back to its former shape without any detrimental affect to the blade’s performance, Such a quality is a highly desirable feature for both ancient and modern blades. As an added bonus, the blades also exhibited a decorative surface pattern, which apparently acted as the blades’ trademark’ of quality.
Prior to the early 20th century, heating narrow strips of iron and steel and shaping them around a mandrel, forged all shotgun barrels. This process was referred to as “laminating” or “Damascus”. These types of barrels earned a reputation for weakness and were never to be used with modern smokeless powder, or any kind of moderately powerful explosive. Because of the resemblance to Damascus steel, Belgian and British gun makers made higher-end barrels. These barrels are proof marked and supposed to be used with light pressure loads. Current gun manufacturers such as Caspian Arms make slide assemblies and small parts such as triggers and safeties for Colt M1911 pistols from powdered Swedish steel resulting in a swirling two-toned effect; these parts are often referred to as “Stainless Damascus”.
Until a hundred years or so ago, koftgiri, the technique of encrusting one metal onto another, was widely used by the Gadi-Lohars, the traditional armourers of Rajasthan, to create a range of weaponry and armour for the use of their Rajput clientele.
The technique of Koftgiri was traditionally used for ornamentation of Swords, Sword handles, Sword sheath, Shields, Knifes, Body Armor – Helmets, Horse Armor. These products were traditionally formed of Damascus steel (it was locally known as ‘Faulad’) or mild steel.
Since Koftgiri was always in relation of to this sword making technique. It can be said koftgiri originated somewhere in between the Persia and India. Historically koftgiri has never been traced for origins but the artisans say the craft has become prominent since the time of the Mughals.
At present, there are few craftsmen left who practice this craft. Some families in the regions of Udaipur, Jaipur and Chittorgarh in Rajasthan are still practicing Koftgiri and imitation of Damascus steel as their profession.
With the growth of the ammunition industry, many older weapons of warfare and other paraphernalia have become obsolete. These objects are now seen only on the occasion of Dusshehra when each family takes its collection of arms to a temple so that these may be consecrated. Although elite houses of the region still commission the occasional coat of arms and swords for ritual display at weddings, the wares of the Lahore are now mostly seen as decorative curios and are made as per the requirements of antique dealers and interior decorators.
Common legend states that European Crusaders first encountered Damascus steel in the Middle East, where Islamic soldiers were wielding fantastic Damascus steel sabres. The Crusaders then brought tales of these impressive blades back with them to Europe. Those who believe in the Crusaders’ story also often believe that swords made of Damascus steel were produced in Damascus, Syria, and that the technique was While it is conceivable that the Crusaders first became aware of Damascus steel during their wars in the Middle East, interest in its composition began centuries before the First Crusade (1095) and the technique to produce it was never ‘lost’ as such.
As an art, koftgiri has been closely guarded through generations in the community of ‘Sigligar’. For long they have served the purpose of Rajput traditions by creating forth numerous decorations on the arms. The locals also often call them ‘lohars’.
Only the family was taught the precious art of engraving gold and silver. As the artisans say, these crafts originated out of the need to please the ‘Raba’, The King or the ministers.
Origins of the craft are closely related to another craft of forging the armor’s steel, presently called as ‘Damascus-Steel’.
Damascus steel was a term used by several Western cultures from the medieval period onward to describe a type of steel used in sword making from about 300 BC to 1700 AD. These swords are characterized by distinctive patterns of banding and mottling reminiscent of flowing water. Such blades were reputed to be not only tough and resistant to shattering, but capable of being honed to a sharp and resilient edge.
The original process of damascening was lost to metal smiths, after production of the patterned swords gradually declined and eventually ceased circa 1750. Several modern theories have ventured to explain this decline, including the breakdown of trade routes to supply the needed metals, the lack of trace-impurities in the metals, the possible loss of knowledge on the crafting techniques through secrecy and lack of transmission, or a combination of all the above.
The raw material for producing the original Damascus steel is believed to be ‘wootz’ imported from India and Sri Lanka by Persia. Due to the distance of trade for this raw material, a sufficiently lengthy disruption of the trade routes could have ended the production of Damascus steel and eventually led to the loss of the technique. As well, the need for key trace-impurities of tungsten or vanadium within the materials needed for production of the steel may be absent if this material was acquired from different production regions or smelted from ores lacking these key trace elements. The technique for controlled thermal cycling after the initial forging at a specific temperature could also have been lost, thereby preventing the final damask pattern in the steel from occurring loss of the technique.
The craft of koftgiri has become more of a commercial craft rather than a usage-based craft. There are only a few families practicing it today in Udaipur and there are industries copying the craft without its best practices.
The craft is losing its valor though the families who do practice it, if revived, can carry the torch ahead.
The craft of koftgiri has become more of a commercial craft rather than a usage-based craft. There are only a few families practicing it today in Udaipur and there are industries copying the craft without its best practices.
The craft is losing its valor though the families who do practice it, if revived, can carry the torch ahead.
Mild steel, Iron Alloys, German silver, Nickel Iron
Thin wires: These wires are made of gold and silver and are wound on a paper roll
Silver & Copper: These metals are used in required quantities to control the colour of gold
Coconut Oil: Used once the product is finished to prevent corrosion on the metal and to provide sheen and glossiness
Silver foil: Started to be used recently to make the leaf motifs work faster than wires
Fule
Gas Burner– Chirni and Sarai
Gutai – A MS file that itself is buffed to a smooth finish;
Buffing Machine
Hakkik-moonstone
Hammers- basic, pointed and often customized
The Mughals and Rajput Kingdoms were based on a hierarchy of monarchs, from the king to the courtiers to the general in charge of the army. Each one held importance according to rank. This display of rank was embodied in the pompousness of their House, Horses, Jewelry, Dress, and armaments. The embellishment of gold and silver on the armaments displayed pompousness. Koftgiri provided the symbolism required to distinguish in between the hierarchy of powers.
The intricateness of the pattern and the amount of gold or silver decided the worth of the armaments’ wield.
Iron discs are bought from Karkhanas (factories) at Ajmer and Bhilwara, manually cut into the desired forms using a hataudi and a sheni and patterned with metal wires. Both women and men are involved in the process- the women prepare the polishes, finish the pieces and embroider the red velvet cases for the objects while the men do most of the heavy manual labour.
1) The Iron or the base is first heated in the kiln.
2) The hot iron slab is taken out of the furnace and taken towards the pneumatic hammer.
3) The thick iron slab is beaten into a long and comparatively thinner slab on the pneumatic hammer.
4) Using an L-shaped strip, a crease is given to the hot slab.
5) The creasing gives a fold to the hot strip.
6) The folded strip is again beaten vigorously. This binds the iron surface join to each other. The process of folding and beating with pneumatic hammer is done approximately from 4 to 5 times.
7) Previously the sheet metal was hand-engraved or ornamented with meenakari. Nowadays, however, the cut strips of metal sheet are usually embossed with dyes and embellished with plastic meenakari.
8) The sheet is then fitted onto the wooden frame of the object and glued on with a synthetic rubber-based adhesive, pressed into position and dried; the ends are nailed as further reinforcement.
9) The object is clamped in a vice and the process of embedding wire into the metal is begun-silver or gold wire is laid on the abraded metallic surface and pressed.
10) The wire is further flattened with the aid of a moonstone. Larger areas such as the tip of the dagger are executed in silver or gold leaf.
11) The strips are then taken to another artisan who gives them different shapes to make different products.
12) Circular drills or vertical/horizontal lines are made to create the required pattern.
13) Grinding is done to attain the required shape and sharpness.
By the time, a product of koftgiri is finished, it is buffed and polished and leaves shreds of metal along with powdered metal as waste. These are usually thrown away and not used again. If the shreds of metal are bigger in size, they can be molten and used again in the next product.
Maharana Udai Singh laid the foundation of Udaipur in 1557 AD, on the word of a sage, who advised him to build a city in the fertile land, protected by the Aravalli mountain ranges. Maharana Udai Singh was a successor of the 'Sisodias', who claimed to have been the descendants of the 'Sun God' (Suryavanshi). The Sisodias are believed to be the oldest ruling family in the world and also the most powerful. For the same reason, they have had many enemies and were under constant attack even from the Mughals. Hence, Maharana Udai Singh decided to shift the capital from 'Chittorgarh' to a more protected city of 'Udaipur' and it continued to be the capital of 'Mewar', till it became the princely state of British India in 1818 AD.
When India got independent in 1947 AD, the Maharaja of Udaipur granted this place to the Government of India. At that time, 'Mewar' merged into the state of Rajasthan and it came to be known as the 'City of Lakes' or 'Venice of the East' due to its luxurious lake palaces like the one which covers an entire island in the 'Pichola' lake.
Udaipur is located 403 kilometers southwest of the state capital, Jaipur, 248 km west of Kota, and 250 km northeast from Ahmedabad. The city lies at an average elevation of 590 meters.
By Air : Dabock Airport is 24 km from the city center. Daily flights connect Udaipur with Jodhpur Jaipur, Aurangabad, Mumbai and Delhi.
By Rail : Udaipur is directly linked by rail with major cities like Jaipur, Ajmer, Delhi, Chittorgarh, etc.
By Road : A wide network of bus service link Udaipur with several destinations. Some of the important destinations are Agra (630km), Ahmadabad (262 km), Jaipur (406 km), Jodhpur (275km) and Mount Abu (185km).
Local Transport : Un-metered taxis, auto-rickshaws, Tongas, regular city bus service is available for 'Dabok airport', 'Badi Lake', 'Bedala' and 'Saheliyon ki Bari'.
Udaipur has pleasant winter temperatures, with a maximum temperature of 32 degrees Celsius in the day during the months of December to February. The summers are hot, with temperatures reaching up to 45 degrees Celsius from March to June. Udaipur gets scanty rainfall in the months of July through to September, which makes the place very humid. The city blooms to a green color and the lakes are full during this season, making the city very beautiful.
Udaipur is a thriving and well-connected city with strong infrastructure, water supply, electricity supply and tourism. It is equipped with many hospitals, blood banks and educational institutions.
Udaipur still retains a quaint old world charm, with beautiful Rajput palaces and forts sitting comfortably amidst the modern constructions of brick, cement and concrete.
Narrow streets, yellow and blue colors on the walls decorated by paintings give a feeling of old Rajput time.
City Palace: Udaipur City Palace is one of the architectural marvels of Rajasthan, located peacefully on the banks of Lake Pichola. This majestic City Palace is the most visited tourist attraction of Udaipur and often distinguished as the largest palace complex in Rajasthan. City Palace boasts of the wonderful blend of Medieval, European and Chinese Architecture. The Palace has various towers, domes and arches, which add to the flavor of heritage site. City Palace has several gates that are known as 'Pols'. 'Bara Pol' (Great Gate) is the main gate to the City Palace complex that will take you to the first courtyard. On passing 'Bara Pol', you will come across a triple arched gate, which is known as 'Tripolia'.
Lake Palace: This is one of the most elegant palaces situated in the heart of the 'Pichola' Lake. The courtyards of the palace are lined with columns, pillared terraces, fountains and gardens which enhance its beauty.
Few temples in Udaipur like the 'Jagdish' temple follow the 'Nagara' style of architecture. In this style the temple is a square, with a number of graduated projections in the middle of each side, giving rise to a cruciform shape. In elevation, it resembles a tower gradually inclining inwards in a convex curve. 'Rishabhdeo' Temple is a chief pilgrimage site for followers of Jain religion. The 'Ambika Mata' Temple, also known as the 'Jagat' temple is a small shrine made in the fissure of a rock.
The primary language of Udaipur is 'Mewari' but Rajasthani, Hindi and English are also commonly spoken. Jainism is the main religion that is observed in Udaipur. Other religions include Hinduism, Islam, Sikhism and Christianity. 'Bhavai', 'Ghoomar', 'KachhiGhodi', 'Kalbeliya' and 'Terahtaali' are the well known dances of Rajasthan. 'Morchang', 'Naad', 'Tanpura', 'Sarangi' and many other instruments were traditionally played in the courts of the Mewari rulers and still finds its patrons and audiences in present times. Udaipur cuisine comprises mostly of vegetarian dishes, as Jainism and 'Vaishnavism' is widely followed. Food is usually made from lots of vegetables and lentils and is seasoned with a great variety of spices.
The 'Mewar' festival is celebrated here with much pomp and show to mark the arrival of spring in the months of March and April. At the time of the 'Mewar' Festival the idols of Lord Shiva (Isar) and Goddess Parvati (Gangaur) are dressed and carried in a traditional procession through different parts of the city.
The final destination of this procession is the 'Gangaur Ghat' at 'Pichola' Lake, where the images are immersed into the lake waters.
'Shilpgram Mela' or 'Shilpgram' Crafts Fair is celebrated in the months of November or December. It is a popular festival organized annually in the western region of Udaipur.
The 'Bhil' tribes are chief amongst the tribal population of Udaipur. A varied mix of urban population is found in the city. Udaipur is also a center for many talented artisans and craftsmen. The traditional attire of women is the 'Ghaghra-Choli' (Skirt & blouse) and for men it is the 'Angrakha' (Kurta) and 'Dhoti'. But in modern times, people wear contemporary clothes like Salwars, Trousers, t-shirts and shirts.
City palace: One of the largest palace complexes in the world, it is a beautiful mixture of Mughal and Rajput traditions. The city palace is built atop a hill beside the 'Pichola Lake' providing a panoramic view of the city.
Gulab Bagh: A vast garden of almost a hundred acres. The garden also has a museum and zoo within it. There is also a public library attached to the garden, which has large volumes and illustrated manuscripts on Indology, Archaeology, and History.
Lake Pichola and Fateh Sagar Lake: Famous man-made lakes of Udaipur. They add tranquility to the beautiful palaces and lend Udaipur the title -'City of lakes'.
Monsoon palace: Also called 'Sajjan Garh Palace' after Maharana Sajjan Singh, who commissioned its construction. It is built high atop the Aravalli ranges at an elevation of 944 meters. As the name suggests, the palace was a monsoon retreat of the Royal family.
Shilpgram Art and Craft fair: It is held annually during the month of December. Over 400 artisans and craftsmen from all over India participate in this fair. The fair takes place in a sprawling artisans' village set up by the West Zone Cultural Center. Folk dances and cultural programs are held as part of the festival. It is a vibrant showcase of the rich 'Rajasthani' culture and heritage.
List of craftsmen.