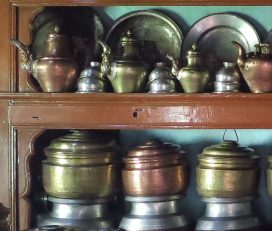
Copper Craft ~ Chili...
Copper and brass have played a significant role in fulfilling these needs. Even today, in most traditional Ladakhi kitchens such utensils are commonly seen
Chiling Sumda...
Batik printing is a form of textile art wherein a piece cloth is decorated by covering it with a coat of wax and then dyeing it. The word ‘Batik’ means ‘wax writing’ and its journey through the ages proves that it is more than just a handicraft. In the small village of Mundra, Kutch, Gujarat, the art Batik printing has been handed down through generations and is still a main source of income for the people living here. These Batik prints feature a three-dimensional look with traditionally inspired motifs representing various folk scenes and deities, nature elements such as birds, flowers, bees, leaves, and several other more complex geometrical designs. These prints give the impression of a kaleidoscopic dream as they imbibe the colours of the universe and patterns of nature.
The word Batik traces its origin to the Indonesian word ‘ambatik’. In Javanese words “Amba”, means “to write” and ” titik”, means “dot or point”, therefore the print literally means -a cloth with little dots or wax writing.
Historically, the Khatri community of Gujarat were known to be the original artisans of Batik printing.
Mundra being located on the western coast of the country, has always had an important role to play in fostering international trade relations. Currently, it houses one of the largest private ports in the country. In addition, culturally, it is the birth place of many handicrafts including the batik prints.
Batik is a technique of wax-resist dyeing applied to whole cloth, or the word is used to refer to the cloth made using this technique. Batik is made either i) canting which involved drawing dots and lines of the resist with a spouted tool or ii) by printing the resist with a copper stamp called a cap. The applied wax resists dyes and thereby letting the artisan colour selectively by soaking the cloth in one colour, removing the wax with boiling water, and repeating if multiple colours are desired.
The batik technique offers immense possibilities for artistic freedom. Due to the wax used in the Batik prints, the lines featured on the fabrics are usually thick and wide, as opposed to the fine lines seen in another art forms. The finest Batik is also reversible.
Predominantly, yes. However, a combination of beeswax and paraffin wax is used or even only paraffin wax is also used because of its easily availability and relative cheapness.
The textile art of Batik printing goes way back in time. This craft allows the artisans to freely express their creativity as the designs are drawn on the fabric. Everything from the colours to motifs make this craft significant not only in the East but also in the West. Initially, the Batik prints were used for making fabrics for the tribal communities to wear. Over the years, contemporary patterns have also been included in these Batik prints to maintain their popularity and significance.
The colourful and playful designs of the Batik prints can be seen on several countless products. Therefore, these prints are used on a variety of products to enhance their beauty and appearance.
Batik prints were an essential part of the daily ensemble of the native communities, the artisans made ‘Odhna’ (90’’ X 90’’) for women with Fulkiya print, Bairaj print, Singh Champa print and Chonia print. It was made by stitching two lengths of fabric side by side and each community had their own preference of motifs. Khatri community women wore Batik Salwars, which were hand-stitched by them. As for men, they used to wear batik printed ‘mediya rumaal’ ( kerchiefs) as turbans.
Apart from the traditional local usages, now-a-days, the cloths with Batik prints are used for stitching different apparel such as salwars, kurtas, sarees, scarves and many more. The Batik printed cotton and silk sarees are extremely popular among the masses and widely sold all around the country. The cloth from the Batik prints can be used and incorporated into any form of clothing, be it Indian or western.
Moreover, the striking beauty of Batik bedspreads, curtains, tablecloths and placemats is also indescribable. The colors are extremely vivid and the designs are so stunning that it is hard to believe they were made with wax and dye.
Until recently, batik was made for dresses and tailored garments only but modern batik is livelier and brighter in the form of murals, wall hangings, paintings, household linen and scarves. It has been introduced in many areas as a source of income generation where there is an absence of sustainable source of livelihood. The market has increased in the last decade and there is more product diversification and one can see batik on clothes, home furnishings, fabric and paintings. Embroidery, beads and mirrors are also added to the fabric to give it a more decorative look.
The starting point of the Batik’s significance can be tied to its interesting technique and cracked effects. Batik is also known to be very durable, that is, it has more color fastness than printed fabrics because through the dyeing process the fabric absorbs the color so well that it does not easily fade.
Although it is common to see the mass production of batik with machines, it is still made by hand in many parts of the world. There is a considerable market for this high-quality cloth. The batik technique first started out as a decoration for royals. Today, the striking and intricate patterns can be seen on the ramp, in the office and on formal occasions. Designers have recently started incorporating batik into everyday clothing, not only in Asian countries, but all around the world.
Batik printing is one of the most significant handicrafts of India. This form of printing is not only practiced in various different regions of the country itself but also different parts of the world. Everything from its popularity amongst the masses to its designs contribute to its significance even in the modern day.
Much of the popularity of Batik can be tied to the fact that the batik technique offers immense possibilities for artistic freedom. The designs on the Batik prints are heavily inspired by the architecture in Mundra. It is believed that there is a bi-directional relationship between the growth of a civilization and the flourishment of arts. This means that whenever a civilization grows, the arts and crafts of that region seek inspiration from the different elements of that civilization. In the case of the Batik prints of Mundra, the architecture on temples showcasing floral patterns and geometrical designs was of great inspiration for the artisans. The Mundra artisans have also been inspired by several aspects of their environment and culture. As the artisans move around the city of Mundra, they gain inspiration from everything around them and include this within their aesthetics of Batik prints.
The earlier Batik prints mainly featured 3 colours of- black, red and white. These prints also included designs with dots, such as dotted flowers or dotted geometrical patterns. One of the most significant Batik print design featured lions, flowers, fish and moon all in one print. This was heavily influenced by the culture and folk tales of Mundra. The earlier Batik prints of Mundra were also known to use only natural dyes in the early days. However, the incoming of chemical dyes allowed the artisans to explore and work with a plethora of colours due to which many artisans shifted to these. In the recent times, there is a growing demand for eco-friendly and skin-friendly colours thus, many artisans find themselves shifting back to natural dyes.
The popularity of the batik designs is so extensive that many batik patterns are used in a wide variety of fabrics. Many fabrics are called batik even though they are not made in the resist method. Most purists believe that such cloth has a batik like design but is not true batik which is confined to fabrics made through the application of the originally conceived Javanese methods of resist dyeing. Modern designers in Indonesia, Malaysia and to a lesser extent Thailand, the Philippines and elsewhere often use batik design elements and often the actual batik clothe in their clothing and accessories.
There was a time when Mundra and Bhujpur (village near Mundra) were known for their Batik prints. In India itself, Batik printing is done in several regions.- Gujarat, West Bengal, Rajasthan, Andhra Pradesh, Maharashtra and Madhya Pradesh. The Batik printing can be done anywhere but each area and region has its own specialty in designs and colors. Each of these regions utilize a different technique for the Batik printing.
The market for these Batik prints has expanded due to the continuous efforts of the artisans who have not only accommodated contemporary prints with the traditional ones, but also carried out several experimentations with colour and pushed their boundaries of practicing Batik on different cloth materials. Sales are good in metros like Mumbai, Bangalore and Delhi and other cities like Baroda and Ahmadabad. The Gujarat state emporium, Gurjari, also stocks the fabric and is a regular buyer. Either the fabric/products are sold directly at the exhibition or they are supplied to wholesalers and retailers in the market. There is year-round demand for the fabric. Export for Batik has also increased in the last decade as its been exported to areas like United Kingdom, Japan and United States.
Since Batik printing is practiced not only in different regions of India but also different regions of the world, there are countless number of myths and legends surrounding it. The mystery surrounding the origin of the technique itself makes some stories seem like myths and some like history.
The designs of the Batik prints are known to be inspired by various myths and legends of the region in which they are produced. Outside India, Indonesia is considered the cradle of batik with its many designs, which are restricted for different wearers and occasions. Indonesian batik has characters of mystic and ritualistic connection. Objects like flowers, trees and birds have a significant meaning. The Sawat in Javanese batik has its origins in Hindu mythology, as it is the decorative form of Garuda, Lord Vishnu’s bird. ‘Sidomukti’ is another Hindu influence in batik. ‘Mukti’ means happiness and prosperity in the Hindu mythology. While Indonesia, Malaysia and Thailand are known for their block printing (tjab) method to create batik on a large scale, in Sri Lanka batik is still made by hand. The art of Batik is also practiced in some African countries.
There is also a Chinese folk tale surrounding the origin of this printing. It is said that several years ago, a small girl who lived in the stone village of Anshun (which is presently a city in Guizhou Province) really enjoyed dyeing cloth in purple and blue, which were her favorite colours. One day, during the process of her dyeing, a bee sat around her cloth. As soon as she spotted the bee, she shooed it away. After dyeing, she spotted a white dot on the area where the bee had sat due to the residue of the bee’s wax. It was this discovery that led to the beginning of wax usage in dyeing.
The word Batik seems to come from an Indonesian word ‘ambatik’, in Javanese words “Amba”, meaning to write, and ” titik”, meaning dot or point, which means -a cloth with little dots or wax writing.
Originally, the art of Batik printing was known as ‘Mediya’ which is derived from the word, ‘wax.’ This was inspired by the women in the earlier days who used to adorn the ‘bindi’ which was also featured the usage of wax.
The actual origins of this beautiful printing technique remain a mystery till date. The earliest evidence of batik dates back to more than 2000 years ago in areas across Africa, Central Asia, the Middle East, South East Asia, and the Far East. The theory that the art form of batik evolved independently in each of these regions is plausible. However, historians believe it is also likely that batik spread through caravan trade routes. By the 17th century there were established trade routes between China, the Indonesian islands Java and Sumatra, Persia, which is present-day Iran, and Hindustan, which includes the North Indian Gangetic Plain and the Indus River basin in Pakistan. Batik even travelled as far as the Netherlands, Germany and Switzerland in the 19th century during the Dutch East Indies colonization. However, many historians dispute the true origins of Batik. Some attribute it to Egypt, while others believe it originated from India.
Frescoes, a type of mural painting that make use of lime plaster, discovered in Maharashtra’s Ajanta Caves include illustrations of Batik, signifying that the craft was present in India before the 7th century CE. For a period of time, the technique of Batik was almost lost due to its meticulous and time consuming repetitive three stage process. However, Batik was preserved as the métier of aristocratic women; the delicacy of batik’s hand-made designs with flower and bird motifs were considered a sign of refinement and cultivation. In earlier times, wax as well as rice starch were used as a resist for batik printing, as opposed to today’s preferred use of paraffin wax and beeswax. Traditional Indian batiks often made use of indigo, brown and white colours as a tribute to the three Hindu Gods – Vishnu, Brahma and Shiva.
Historically, the Khatri community of Gujarat were known to be the original artisans of Batik printing. Over time, other cultures and communities in Gujarat, and eventually other regions of India, began practicing the techniques to create batik. However, it is believed that this craft was begun by the Khatris of Gujarat and even today, the art of Batik printing is being passed down from one generation to the next.
Over time, the technique of Batik dispersed to other regions and cultures of India. It was Rabindranath Tagore who traveled to Java in Indonesia and was fascinated with the exquisite art of batik. He then brought back several pieces of fabric with the hope to revive the traditional technique in India. Consequently, The 20th century saw the resurgence of Batik, as it was introduced as a two year course at the Visva-Bharati University in Shantiniketan, West Bengal. In the 1980s, batik printing became a popular industry for small scale Indian female designers and entrepreneurs. In the mid- 1960s Tamil Nadu became another center for batik printing and its artisans, with the establishment of the Cholamandal Artists’ Village in Injambakkam.
Batik prints were an essential part of the daily ensemble of the native communities, the artisans made ‘Odhna’ (90’’ X 90’’) for women with Fulkiya print, Bairaj print, Singh Champa print and Chonia print. It was made by stitching two lengths of fabric side by side and each community had their own preference of motifs. Khatri community women wore Batik Salwars, which were hand-stitched by them. As for men, they used to wear batik printed ‘mediya rumaal’ ( kerchiefs) as turbans.
Experimentation with Batik in India continues till date wherein vegetable colors and natural dyes are used to reduce costs and create eco-friendly methods of production. Apart from dying on silk and cotton sarees, Batik prints are also done on leather goods, like side bags, clutches, file covers, wallets, and many more. All these products get exported at quite exorbitant prices to various parts of India and outside India.
The designs on the Batik printed cloths are the primary reason for their significance, popularity and acclaim. These designs present a perfect mix of contemporary and tradition through their motifs and colours. The designs feature a certain adaptability that allows them to be featured on several different items, all the way from clothes to linen, and find a market in the East and the West.
Batik prints present a three-dimensional effect that can attributed to the fine cracking of the wax on the fabric that allows small amounts of dye to seep into the fabric, thus giving the design a textural depth.
The traditional designs and motifs in Indian batik are often passed down from one generation to another. These motifs generally fall under two categories – geometrical patterns and free flow designs. The former commonly involves designs transferred from paper onto the fabric, while the latter allows artisans to freely express their artistic skills with elaborate motifs. Traditional non-geometrical batik motifs may represent the beauty of nature such as flowers, leaves, birds, fish, insects and animals. Other more intricate motifs depict humans, folk scenes and Gods. The use of indigo, brown and white colours is traditionally a tribute to the Hindu Gods – Vishnu, Brahma and Shiva. These three colours are amongst many that are used in Indian batik. Colours are often vivid and contrasting, capturing all the fine details of the design.
Contemporary designs in batik pay homage to its traditional designs, though they may differ in style. Contemporary batik artisans often make use of stencils to outline designs or use the ‘discharge dyeing method’ which involves using a bleaching agent while dyeing the fabric. This innovative method allows the light colours to be printed onto the darker colours. The uncustomary use of such tools and techniques in Batik printing has allowed for artisans to create products that meet the demands of modern fashion.
Therefore, Batik printing portrays an array of themes, which include- religious influences as well as abstract patterns. Since Batik printing is done in several states of India, each print represents cultural elements of the respective states in which it is made.
Much of the popularity of Batik can be tied to the fact that the batik technique offers immense possibilities for artistic freedom. The designs on the Batik prints are heavily inspired by the architecture in Mundra. It is believed that there is a bi-directional relationship between the growth of a civilization and the flourishment of arts. This means that whenever a civilization grows, the arts and crafts of that region seek inspiration from the different elements of that civilization. In the case of the Batik prints of Mundra, the architecture on temples showcasing floral patterns and geometrical designs was of great inspiration for the artisans. The Mundra artisans have also been inspired by several aspects of their environment and culture. As the artisans move around the city of Mundra, they gain inspiration from everything around them and include this within their aesthetics of Batik prints.
The earlier Batik prints mainly featured 3 colours of- black, red and white. These prints also included designs with dots, such as dotted flowers or dotted geometrical patterns. One of the most significant Batik print design featured lions, flowers, fish and moon all in one print. This was heavily influenced by the culture and folk tales of Mundra. The earlier Batik prints of Mundra were also known to use only natural dyes in the early days. However, the incoming of chemical dyes allowed the artisans to explore and work with a plethora of colours due to which many artisans shifted to these. In the recent times, there is a growing demand for eco-friendly and skin-friendly colours thus, many artisans find themselves shifting back to natural dyes.
Due to the wax used in the Batik prints, the lines featured on the fabrics are usually thick and wide, as opposed to the fine lines seen in another art forms. However, the beauty of this handicraft lies in its bold and thick patterns.
Nevertheless, both traditional and contemporary motifs and techniques of batik printing allow the artisan freedom of expression. This attributes to the uniqueness and authenticity of each and every batik print, which is ingrained with the artisan’s individual aesthetic. Today, one can say that the Batik designs have undergone significant changes in terms of styles and tastes. A modern batik design is simple yet attractive piece of art that captivates the various nuances of modern life in a mesmerizing blend of colors and patterns. However there is equal craze for traditional Batik designs that serve as reminders of our rich historic past.
The most promising feature about the Batik printing is that over the years, their demand and market has not decreased. There are improved facilities now for waxing, bleaching and washing the fabric. The adapted techniques have led to the process becoming less cumbersome and easy to learn.
Batik is a time-consuming and meticulous technique of decorating fabric by hand. Batik’s signature characteristic is the effect created by the wax cracking on the fabric. It is a feature not possible in any other form of printing. It is very important to achieve the right type of cracks or hairline details for which the cloth must be crumpled correctly. This requires a tremendous amount of practice and patience.
Just like any handicraft, the Batik prints experience their fair share of challenges. This includes the increased price of raw materials and wastage of water. However, attempts are being made to make this process more eco-friendly and sustainable.
The designs on the Mundra Batik prints are often replicated by screen and laser printers, who produce these textiles in bulk at cheaper prices, thus nearly smothering this Kutch handicraft out of existence. However, despite all problems, several Khatris continue to make efforts to ensure that the Kutch Batik continues to exist today and more Batik printers are engaged in working towards the revival of the art. To keep up with the changing times and heavy demand, these pioneer artists are incorporating modern motifs and using paraffin wax, which is sourced from China. Around 75% of the wax is re-used and Kutch batik is becoming one adaptive, sustainable art.
The earlier Batik prints mainly featured 3 colours of- black, red and white. These prints also included designs with dots, such as dotted flowers or dotted geometrical patterns. One of the most significant Batik print design featured lions, flowers, fish and moon all in one print. This was heavily influenced by the culture and folk tales of Mundra. The earlier Batik prints of Mundra were also known to use only natural dyes in the early days. However, the incoming of chemical dyes allowed the artisans to explore and work with a plethora of colours due to which many artisans shifted to these. In the recent times, there is a growing demand for eco-friendly and skin-friendly colours thus, many artisans find themselves shifting back to natural dyes.
Due to the wax used in the Batik prints, the lines featured on the fabrics are usually thick and wide, as opposed to the fine lines seen in another art forms. However, the beauty of this handicraft lies in its bold and thick patterns.
The raw materials used in the process of Batik printing have evolved continuously with the progression of time.
• Fabric/Cloth– The Batik printing is done on a piece of fabric/cloth which is then sold in the market. Traditionally, cotton and silk fabrics were used in the batik printing process, however, today, different fabrics such as poplin, cambric, voiles, chiffon and velvet are also used. Cotton and silk still continue to be the most preferable option for the artisans and the usage of synthetic materials is relatively less.
• Paraffin Wax– Wax is the key raw material used in the process of Batik printing. The designs on the fabric appear through the repeated process of application and removal of the wax on the fabric.
Traditionally, Kutch Batik prints were made by pressing a block dipped in hot piloo seed oil, on cloth. The oil paste was then taken off after dyeing to make the original print liven up on the fabric. A huge amount of tiny seeds were pressed to release a large number of even smaller seeds out of which this oil was extracted. Over the years, the artisans found this process to be painstakingly tiring and the oil was replaced with beeswax.
The introduction of wax subtly altered the style of the batik prints and this Kutch handicraft actually became more appealing. The wax created cracks that appeared as thin, spidery lines of dye running through the motif. This created a beautiful veined appearance. By the 1960s, the Kutch Batik print became a huge success.
Today, either a combination of beeswax and paraffin wax is used or only paraffin wax is used since it is cheap and easily available.
• Dyes– Naphthol, direct and vat dyes are used in the dyeing process to colour the fabric in the desired choice of the artisan.
• Firewood/Kerosene– This is used for the heating of the wax.
• Water– This is used for the washing of the fabric.
Rate of raw material: Cotton cloth for wax printing and dyeing is bought from South India, particularly Tamil Nadu. This costs between Rs. 14-25 per meter. Paraffin wax is bought from Rajkot-Gujarat and Mumbai for Rs. 44-48 per kilogram. Dyes are available in Jamnagar, Anjar, Gujarat and Mumbai. Vat dyes have more color fastness but a limited color range. These dyes are the most expensive of the lot with a price of Rs. 1550-2200 per kilogram. Naphthol dyes are used more for dark base colors like maroon and blue and cost anywhere between Rs. 230-400 per kilogram. Direct dyes are used more for over dyeing after the pattern and the other colors have been done and cost about Rs. 90-220 per kilogram.
Availability: All the raw material required for batik is easily available though it is difficult to find some of the old block designs that were used earlier for printing.
The process of Batik printing requires a few simple tools, these are-
• Wooden Printing blocks– The desired designs are traced onto vertically chopped wood to create the printing blocks. These blocks are then used for creating the designs on the fabric itself. Teak is the preferred wood since it rarely cracks or flexes. These wooden blocks have countless designs- all the way from flowers, to leaves to basic circle and complex geometrical patterns. The artists are able to explore and work with multiple permutations and combinations of designs which makes these designs unique and popular.
• Vessels– Different sized vessels are often utilized in the process of Batik printing for heating of the wax.
• Wajan– This is a container that is used for the purpose of holding the wax.
• Plastic Bucket/Bowls– These are used for mixing of the dye colours that are to be used on the fabric.
• Frame/Table– This is used for fixing of the fabric. It often contains sand so as to prevent the wax from spreading. The length and construction of the table ensure that the wax does not get deformed in any way.
• Brushes– Several sized brushes are present with the craftsmen for the purpose of drawing free- hand designs onto the fabric. These brushes can only be used for waxing.
• Bottle sponge applicator– This is used for colouring the fabric.
• Kundi– This is a large pot wherein the de-starched white cloth is stone washed.
• Lath– These are bamboos on which the fabric is hung to allow the excessive water to drain away.
• Big tanks– These are used for the purpose of washing away the wax on the fabric. The water in these tanks is usually hot in order to melt the wax away successfully.
• Karchi- This is used for heating of the wax.
The process of Batik printing takes place in 3 stages, these are- waxing, dyeing and de-waxing (removal of wax). The main steps involved in the Batik printing process are as follows-
Step 1: Cotton fabric is bleached (with bleaching powder and water) and kept overnight for whiteness. This process is done by machine or manually.
Step 2: Wax printing is done either with the hand, using a brush or with the blocks (paraffin wax is melted and kept on the stove right next to the printer). The table on which printing is done is kept cool with sand and water so that the wax does not spread and the design stays consistent throughout.
Step 3: After the initial printing, the fabric is dipped in a color fixer.
Step 4: The fabric is then dipped in naphthol dye for 10-15 minutes
Step 5: If only a single color is required then after this, the cloth can be dipped in hot water so that the wax comes off and one gets the required pattern and color.
Step 6: If any unrequired white spots are left then the fabric can be dipped once more in any direct dye. This process is called ‘topping.’
Step 7: If one wants more patterns and colors, reprinting could be done with wax and the whole process is repeated again.
Therefore, in the process of Batik printing, wax is applied to the cloth in order to resist successive dyes so that wherever the cloth is waxed, the dyes are not allowed to penetrated.
For example, if the artisan wants to produce a design of a pink flower on a yellow background then wax is first applied to the area that will become the flower. The white cloth is then entirely immersed in a yellow dye and dried. After dyeing, the wax covering the flower pattern is scraped off. Since the wax was able to resist the blue dye, the artisan is now presented with a white flower on a yellow background. Now in order to make the flower pink, the yellow background is covered with wax and dipped in a pink dye. When the wax is scraped off the second time, a pink flower can be seen on a yellow backdrop.
This process can be repeated multiple times if several colours are used. The finest Batik is reversible– the motifs are drawn, waxed and dyed first on one and then the other side of the fabric.
The white cloth is de-starched by soaking the fabric overnight. It is then stone-washed and kept it in a large pot call a ‘kundi,’ and further soaked in soda water for softening the fabric. Since soaking and washing use a great deal of water, the workshop is required to have a proper drainage system. After washing, the fabric is hanged on bamboos call lath which allow the excess water to drain away. This method avoids wringing the cloth, which may smudge the colour. Below the lath, molded iron sheets are fixed through which water drips and accumulates in a large water container. A similar washing process is also followed, with the kundi filled with soap, to later remove the wax.
For the wax-making process, wax is boiled at extremely high temperatures. To achieve this, a two-tiered structure is used. Wax is kept in a vessel above a brick furnace at ground level. Since wax has a lighter density (ghanata) than water, when boiled, it forms on the surface of the vessel, like butter from milk. The unused melted wax is moulded together for reuse. Printing is done on the sand-filled pad. The dyeing method varies according to the number of different designs on a piece, but completing a single batik cloth is a laborious process.
The fabric is first prepared by being starched. It is then stretched on a frame in order for pre-determined designs to be outlined and transferred from paper. Traditionally, the transfer of designs onto the fabric was done by hand. Many Indian batik artisans continue to make use of this traditional production method to ensure authenticity and the preservation of the ancient art form. However, modern-day commercial methods that make use of screens in design transfer are on the rise, particularly in South East Asia. The wax is then applied with precision to the design outlined on the fabric.
The characteristic effects of batik are the fine cracks that appear in the wax, which allow small amounts of the dye to seep in. It is a feature not possible in any other form of printing. It is very important to achieve the right type of cracks or hairline details for which the cloth must be crumpled correctly. This requires a lot of practice and patience.
Moreover, knowing how to use the wax is of prime importance. The ideal mixture for batik wax is 30% beeswax and 70 % paraffin wax (but these days mostly paraffin wax is used as it is easily available and less costly). It is the skillful cracking that is important. While applying, the wax should not be overheated or it will catch fire. Correct knowledge of colors is also important. Practicing on small pieces of cloth helps in the beginning.
The cloth used should be strong enough to bear the heat and wax. Cambric, poplin and voiles are used besides pure silk. Synthetic fabrics are avoided. Along with handmade batik, blocks are also used for wax printing.
The process of Batik printing does not involve much wastage.
The wooden blocks are created from the teak plant species and efforts are made by the forest authorities and several individual parties to ensure the replenishment of this tree and minimum wastage while creating the designing blocks.
Water wastage is also a problem in this process of Batik printing. Many times, the cloth has to be washed off of the chemical dyes after which it cannot be reused. Measures are being taken to reduce the water consumption.
Moreover, the usage of industrial wax (paraffin wax) makes it difficult for the artisans to re-use it without any form of wastage.
Archeological evidences reveal existence of strong trade relations between the port of Mundra and ports in Arab and Egypt along the Red sea. These goods were further transported to Europe through Mediterranean Sea. Until 1969, the port was still used by Haj pilgrims to commence their sacred journeys.
Mundra was established by Bhojarajji I of Cutch State in the 1640s.
According to a legend, a Jain merchant, Vardhaman Sheth approached Pir Hazrat Shah Murad Bukhari to pray for safety of his sinking cargo ship. Miraculously the ship was saved when Pir used his dhoti to prevent seawater from entering the ship. Vardhaman Sheth then requested Pir to rename the town to Munahara and that is how the name, ‘Mundra’ was derived.
The town was fortified in 1728 by Devakaran Seth, Dewan of Deshalji I. Old Mundra town was walled and fortified with the masonry from the ruins of the ancient town of Bhadreshwar, Colonel Holland who visited it 1840s mentions that the walled town had 1.5 miles of circumference and 1500 houses.
In 1755, Mundra was held and defended by Godji II in revolt against Rao Lakhpatji, his father. Godji imposed charges on merchants entering and exiting the town to raise funds on advise of Punja, his adviser. Lakhaptji angered by the act and sent an army to the town. Godji then fled to Morbi, strengthened his army and recaptured the town from his father. A compromise was made wherein Godji was allowed to keep the town of Mundra, however Punja was forced to retire.
In 1801, Mundra was given by Fateh Muhammad to another chief Dosal Ven. He later regained the town from him. Later it was given to Hansraj who also rose against him so he transferred Mundra to his associate, Muhammad Sota. In 1815, during the reign of Muhammad Sota, Mundra was unsuccessfully attacked by Rao Bharmalji II.
In 1818, Mundra is said to have had a population of 1200 individuals and to have yielded a revenue of Rs 30,000. In 1855, the Mundra fort was in good conditions and contained approximately 1500 houses.
In 1879, there was a considerable trade with Kathiawar, Khambhat, Surat and Bombay. The chief exports were cotton, castor seed, pulse, wool and dyed cloth and the chief imports were metals, timber, grain, dates, grocery, and piece goods. In 1872, Mundra had population of 7952.
The town was base of many mercantile communities including Kutchi, Oswal, Vanias and Bhatias from the 18th to early 20th century. However, the importance of town declined with the rise of Bombay (now Mumbai) and the construction of Rajputana railway in 1870s
After the independence of India in 1947, Cutch State acceded unto the dominion of India and was constituted an independent commissionaire- Kutch State. In 1956, Kutch State was merged with the Bombay state, which in 1960 was divided into the new linguistic states of Gujarat and Maharashtra, with Kutch becoming part of Gujarat state. Mundra now falls under Kutch district of Gujarat.
In 1994, the Mundra Port was announced at Mundra. The operation started in October 1998. In subsequent years, the port expanded rapidly resulting in rapid expansion of town and population. During the January 2001 Gujarat earthquake, Mundra was the only place in the district of Kutch which was not affected by the devastation. Following the earthquake, the tax incentives were granted for setting up new industries in this district which led to the rapid industrialization of this region. In 2014, Mundra Port surpassed Kandla in cargo handling and became the largest private port of India.
The Kutch District, at 45,691.895 square kilometers, is the largest district of India. The administrative headquarters is in Bhuj which is geographically in the center of district. Mundra is considered to be one of the main towns of Kutch district. Kutch has 969 villages. Kala Dungar or Black Hill is the highest point in Kutch at 458 meters.
Kutch is virtually an island since it is surrounded by the Arabian Sea in the west, the Gulf of Kutch in south and southeast and Rann of Kutch in north and northeast. The border with Pakistan lies along the northern edge of the Rann of Kutch, of the Sir Creek. The Kutch peninsula is an example of active fold and thrust tectonism. In Central Kutch there are four major east-west hill ranges characterized by fault propagation folds with steeply dipping northern limbs and gently dipping southern limbs.
Kutch is divided into 4 zones, namely- Wagad (including Rapar and Bhachau Taluka and Little Rann); Kanthi (Sea Coast area comprising Anjar Mundra and Mandvi Taluka); Banni Region (with Pascham which includes Bhuj, Nakhatrana and surrounding areas) and Maghpat (includes part of Nakhatrana and Lakhapat Taluka.)
The Mundra lies at 13 meters above sea level and is characterized with desert climate. During the year, there is virtually no rainfall in Mundra. The average annual temperature in Mundra is 26.4 °C and the rainfall here is around 399 mm.
The driest month is February, with 0 mm of rainfall. The greatest amount of precipitation occurs in July, with an average of 170 mm. The average water temperature during the year located in Mundra is 26.70°C.
The closest Ocean of Mundra is Gulf of Kutch with roughly 6.59 kilometres.
The infrastructure in Kutch is still developing and modernizing. A large setback in the development of this region was created due to the Earthquake of 2001.
Water and power supply is provided to the entire region, however, some areas still experience a shortage or lack of these facilities. Mundra is one of the main ports of Kutch that serves as the backbone for the trading business here.
The region is connected through road, rail and air and the quality of the roads is known to have significantly improved in the recent years.
In terms of Mundra in particular, despite being an important port area, the region is largely agricultural. The area is populated by stray cattle and the lined with small shops selling everyday items. More government attention and investment is required in this region so as to improve the sanitation facilities and allow Mundra to proudly uphold the title of being one of the unique regions producing the Batik prints.
The earlier architecture of Mundra featured houses that were made of mud and roofs lined with bricks. These houses were painted white and consisted of simple architecture. However, after the earthquake, a significant amount of architecture including the temples and buildings were destroyed. After this, the construction that came about featured architecture similar to that seen in cities. The newer houses featured different colours such as blue and green and even had balconies attached to them.
The architecture of Mundra is of great significance since many of the Batik printing artisans are inspired by the floral patterns and geometric designs seen in the Mundra temples and old architectural pieces.
The Mundra fort is one of the oldest architectural constructions that can be seen here. he walls of the old city fortifications have a religious origin, as they were dragged from the ruins of the ancient city of Bhadravati.
The culture of Kutch is as rich as its history and as dynamic as its evolution through the ages.
At the time of the 2011 Census of India, 54.91% of the population in the district spoke Gujarati, 34.92% Sindhi, 7.53% Hindi and 0.51% Telugu as their first language. The language spoken predominantly in the Kutch district is ‘Kutchi’ which is classified under Gujarati language. However, the script of the Kutchi language has become extinct and is now mainly written in the Gujarati script. Samples of Kutch script are still available in the Kutch Museum. The increased use of Gujarati language can be seen as a direct result of it being used as medium of instruction in schools.
The food of this region also forms a big part of their culture and cultural identity. The majority of the population is Hindu and Jain and thus largely vegetarian. Jains also refrain from eating kandmool food grown below the ground such as potatoes, garlic, onion, and yam. There are also a sizeable population of Muslims, who eat vegetables, chicken, mutton and occasionally camels.
In the villages, staple foods include kadi-khichdi, bajra and milk, ‘bajara na rotla; with curd and buttermilk is very common food for all the Gujarati people. They also extensively drink buttermilk during lunch. Milk is considered to be sacred food and offering it to somebody is considered a gesture of friendship and welcoming. Settlement of dispute invariably follows offering milk to each other as a concluding remark. In the Kutchi engagement ceremony, the bride's family offers milk to the groom's relatives as a symbol of accepting their relationship. Tea is the most popular drink in this region.
The people in Mundra often dress in simple clothing and rarely adorn their own Batik prints.
According to the 2011 census, Kutch District had a population of 2,092,371. Kutch has a sex ratio of 908 females for every 1000 males, and a literacy rate of 71.58%.
The people of Mundra in particular, lead simple lives since this region imbibes the true sense of being a traditional Indian town setting. The sentiments of community and togetherness are heightened due to the small population and all individuals are said to live in peace and harmony. This small town is known for having people with big hearts.
An amalgamation of people from different communities and religions can be seen here. Therefore, this small region itself upholds the idea of India’s ‘unity in diversity.’ One can find various nomadic, semi nomadic and artisan groups living in Kutch. Ahirs constitute a comparatively large group in Kutch. Hindus form majority of the population, followed by Muslims, Jains and Sikhs.
Due to the diversity in communities and religion, the people here often adorn distinct clothing. For example, the Muslim women can be seen wearing salwar kurtas, and Hindu women from different backgrounds can be seen wearing sarees and sometimes even ghagra choli. Men wear kurta and pajama, however, the younger population has even incorporated shirts and pants into their wardrobe.
Apart from the famous Batik prints of Mundra, Gujarat is also famous for its Ajrakh printing, terracotta toys, metal work, bead work applique work, weaving, painting, carving, and embroidery
List of craftsmen.
Team Gaatha