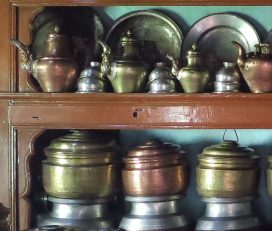
Copper Craft ~ Chili...
Copper and brass have played a significant role in fulfilling these needs. Even today, in most traditional Ladakhi kitchens such utensils are commonly seen
Chiling Sumda...
Blue pottery is widely recognized as a traditional craft of Jaipur. The name ‘blue pottery’ comes from the eye-catching blue dye that is used to color the pottery. Some of the pottery is semi-transparent and most are decorated with animal and bird motifs. The pottery is made using Egyptian paste, is glazed and low-fired.
Blue pottery is widely recognized as a traditional craft of Jaipur.
Blue pottery is different from other pottery because it is the only pottery in the world that does not use clay. The pottery has a distinct appearance as it is made out of Egyptian paste, glazed and low-fired.
When alkaline soil was mixed with copper and heated it gave a turquoise blue color, which is derived from cobalt oxide.
Leela Bordia is a social entrepreneur who is acknowledged with bringing back the Blue Pottery of Jaipur. People say there was a time when this art form had faded away from Jaipur but her attempts have helped control its decrease and grant her to evaluate with it.
Yes, though Blue pottery is widely recognized as a traditional craft of Jaipur today this traditional craft provides day jobs to many.
Blue pottery as a technique was mostly used to produce decorative items such as tiles, door knobs, pots, vases and plates. But now, the uses have evolved to include functional articles such as ashtrays, narrow mouth, beer mugs, candle stands, hukkah, coasters, various animal shapes, incense stick holders, jugs, napkin rings, pen holders, soap dishes, trays, trinket boxes, wall hangings, bathroom sets, tumblers and containers with lids etc.
Blue pottery is different from other pottery because it is the only pottery in the world that does not use clay. The ‘dough’ for the pottery is prepared by mixing quartz stone powder, powdered glass, Multani Mitti (Fuller’s Earth), borax, gum and water. Another source cites ‘Katira Gond’ powder (a gum), and ‘Saaji’ (soda bicarbonate) as ingredients. The pottery has a distinct appearance as it is made out of Egyptian paste, glazed and low-fired.
The history of the art of pottery is as old as the history of mankind. Glass was discovered in the ancient civilizations of Egypt, Syria, Iran and Indus Valley. It was further discovered that when alkaline soil was mixed with copper and heated it gave a turquoise blue color.
From Mohenjodaro and Harappan era right till the Gupta period glazed utensils, necklaces, beads and tiles were in vogue. This art greatly flourished during the Buddhist period.
The Central Asian and Middle Eastern glazing techniques came to India with the several successive Islamic invasions while the Chinese porcelain continued to be imported to the Indian courts (both pre-Mughal and Mughal). The Baburnama, commissioned in 1590 in the reign of Akbar mentions that “Babur and his friends were regularly served kebabs and pilaus from dishes and plates that are sometimes golden, sometimes green and sometimes blue and white.- The miniatures paintings of the era also depict the same.
Researches of the Archaeological Survey of India mentions the fact that the glazed tiles first appear in Delhi in the Tughlaq monuments dated between 1321 AD and 1414 AD. The designs of which are inspired from the Turkish patterns. Excavations at the Purana Qila have revealed glazed ware of the Sultanate period from 1206 to 1526. The pottery introduced to India in Delhi and Multan is believed to have come from Bokhara. Some of the earliest tile work can also be seen in Arab-ki-Sarai in Delhi near Humayun’s tomb. The other centres of glazing and painting tiles opened up at Khurja, Agra, Meerut, Rampur, Bulandshahar due to the mushrooming of glazing kilns.
When the city of Jaipur was founded in 1727 by Sawai Jai Singh I, craftsmen from all over the country were invited to come and make their home in this new city. Royal patronage, lucrative offers and the attraction of living in a beautiful city led many artisans and craftsmen to come and settle in Jaipur. By the beginning of the 19th century the city was well established as a thriving art centre. In keeping with the traditions of his forefathers, Sawai Ram Singh II (1835-1880) set up a school of art and continued to encourage artists and craftsmen. Blue Pottery took an interesting route in finding its home in Jaipur. Ram Singh II attended a kite flying session and watched as his kite masters were engaged in battle with two brothers from Achnera (near Agra). When the ruler saw that the brothers managed to bring down the royal kites almost every time, he was intrigued. He asked the brothers their secret. They told him that they were potters by profession and had coated their strings with the same blue green glass that they used for their pots. Sawai Ram Singh II was impressed so he invited the brothers to stay in Jaipur and teach this unique form of glazed pottery at his new art school. On the Verge of Extinction Blue Pottery had enormous potential and should have flourished, but over the years master potters refused to share their trade secrets with their fellow craftsmen so there was an eventual lowering of standards and a gradual dying out of the craft. Over the years the craft was kept alive by her Highness Gayatri Devi who widely promoted Blue Pottery. The craft received a much needed boost in the 1960’s as internationally renowned artist; Kripal Singh Shekhawat entered the field of Blue Pottery and raised the bar. His presence brought a new excitement to the craft as his designs began selling very well.
Most of the pottery is decorated with animal and flower motifs while some of it is semi-transparent. The color palette is restricted to blue which is derived from cobalt oxide, green derived from copper oxide and white, though other non-conventional colors, such as yellow and brown are also sometimes included.
The traditional patterns and motifs in blue pottery are of Persian origins, though craftsmen have developed contemporary patterns too along with the traditional ones. These patterns include floral, geometric designs, animals, birds as well as many deities like Goddess ‘Durga’ and Lord ‘Ganesh’. Custom made designs are also sent in by the client and can be as experimental as cockroaches walking over a pot.
One of the major difficulties for the craftsmen is the presence of the raw lead oxide used in the glaze. Though the content is reduced to harmless amounts after the process of fritting, the presence of lead makes customers skeptical about buying.
The craftsmen also need bright sunlight for the drying required in various stages of the craft. Any excess moisture will keep it from drying and lead to collapsing from its own weight during firing. This is also because of the presence of sodium sulphate which causes water retention.
The process of making blue pottery is not simple but rather tedious and time-consuming. The articles of blue pottery are handled with utmost care as the slightest mistake can create cracks or turn them black. It takes 10-12 days for a batch of blue pottery articles to be made.
Ground Quartz Stone- This is in a powdered form and is obtained from the nearest market. Since it is the main raw material, it is normally bought in tons. The cost of quartz stone is about Rs. 1200 – 1300 per ton.
Glass Powder- Green glass which is normally used in making tea glasses is taken into use. Broken pieces of glass are available with the ‘Kabaadi’ (a waste material collector) and costs around Rs. 4-5 per kilogram. The obtained glass is first treated before being used for the dough. The treatment involves thorough washing of the glass, breaking it into fine pieces and then grinding it into powder in the grinding machine.
Katira Gond (kind of adhesive)- It is obtained from the market in big pieces and costs Rs. 80-85 per kilogram. Before use, the pieces are broken by hand, ground into powder with a grinding machine and sieved with an iron sieve.
Tragacanth Gond- It is can be obtained from a regular grocer’s shop and costs about Rs.150 per kilogram. It is available in the form of grains and needs to be ground up before use.
Fullers Earth (Multani Mitti)- It is available in the market in small pieces and costs about Rs. 8 – 10 per kilogram.
Saaji (soda bicarbonate/ bentonite)– It is available in the market in the form of small pieces and costs about Rs. 40-50 per kilogram. Broken pieces of ‘Multani Mitti’ and ‘Saaji’ are taken in equal proportions and then ground to a powdered form in the grinding machine. It takes approximately five days to prepare a 50 kilogram mixture of Multani Mitti and Saaji.
Flour- Refined white flour made of wheat known as ‘Maida’ can be obtained easily from the market and is used as an adhesive in the process of blue pottery.
Colors- The colors used in blue pottery are of two types: oxide colors and ferro colors. The usual oxides used for coloring are cobalt oxide (for dark blue color), copper oxide (for light blue color), chrome oxide (for green color), cadmium oxide (for a bright yellow color). The Ferro colors are used for the colors brown and yellow.
Borax- It is available in the market at the cost of Rs. 3500 – 4000 per 50 kilogram.
Zinc Oxide, potassium nitrate and boric acid.-These are easily obtained from the market.
Water- It is used in binding and forming the dough.
Chakki (Grinding Machine) – It is a grinding tool made of stone. In this, one stone rotates over the other stone and the material is poured from above. On rotating the wheels, the material reaches between the two stones and is ground through friction. It is a manual use machine in which the upper stone is rotated by hand. Nowadays, mechanical machines are taking its place.
Molds- These are made of clay or a quartz mixture and are used to give shape to the products. Molds in several shapes are prepared for different items and one mold can be used several times.
Flattening Tool- It is made of terracotta clay and is used to flatten the dough prepared for blue pottery.
Sand Paper- It is used for giving a smooth polished finish to the products.
Iron Blade or Knife- It is used for cutting the dough and scooping the portions of pottery items. It is bent at a right angle so that the scooping can be done easily.
Base Stone- The base stone is a smooth stone block where the polishing of the pots or other items is done by rubbing them on the stone.
Broom- It is a very small broom made of husk.
Potter’s Wheel- It is a wheel used by potters for shaping utensils and consists of a big circular stone pivoted at the center of the wheel which is rotated by an iron pipe.
Brushes- The brushes are made by the craftsman using squirrel hair. These are used for coloring and making designs on the various pottery products.
Heating Kiln- A heating kiln is made of clay and brick and is a closed kiln. It is usually circular in shape and about 40 to 50 items of blue pottery can easily be put inside the kiln. It is heated by charcoal or wood and can be heated to the temperature of 800 to 900 degrees Celsius. The wood and charcoal are moved below the kiln by long iron rods.
The process of making blue pottery is not simple but rather tedious and time-consuming. The articles of blue pottery are handled with utmost care as the slightest mistake can create cracks or turn them black. It takes 10-12 days for a batch of blue pottery articles to be made.
Preparation of the Dough
The dough used for molding is prepared by mixing five ingredients. These are quartz stone powder (40 kilograms) which is the major item, powdered glass (5 kilograms), Katira gond powder (1 kilogram) and a mixture of multani mitti and saaji (1kilogram). These are put on the hard floor and are thoroughly mixed till the mixture becomes homogeneous. After that, water (25 liters) is mixed into it till a smooth non-sticky dough is made. The dough is rested for 8 – 10 hours.
Pressing it into Molds
A small amount of prepared dough is taken and then rolled by hand on the base stone. It is cut in equal parts (using a) according to the item being prepared. After this the dough is flattened with the help of a flattening tool till it takes the form of a 4 – 5 millimeter thick ‘Chapatti’ (pancake). The ‘Chapatti’ is carefully put into the mold which is shaken lightly so that the chapatti sets in the mold. After that, a mixture of fine ‘Bajri’ (stones) and ‘Raakh’ (ash made from burnt wood) is put into the mold and is lightly pressed so that the dough takes the exact shape of the mold. The extra dough is cut off with a knife. The mold is then turned upside down on the base stone and removed. The dough made with bajri and raakh, is left to dry for one to two days.
Cleaning
The dried dough is now in the shape of the mold. It is again turned upside down and the raakh and bajri mix is removed from it. During the process of drying, some raakh sticks to the pottery item. It is cleaned with the help of a small broom made from husk.
Shaping Process
Once the pottery item is ready; it is rubbed lightly by hand on the base stone to even out the edges. After doing this, the pot becomes evenly shaped.
Adding Base
Except for tiles and wall hangings, most of the pottery items are prepared in two or more parts. After the molded item is ready, a base is added below it. In rounded pots, it is done by putting it on the potter’s wheel. The wheel is set in motion and the pot is fixed at the center of the wheel. A little amount of dough is taken and with a touch of water, the base of the vessel is added. It is again left for drying for one to two days.
Polishing Process
The pot is now ready in form. It is rubbed with ‘Regmaal’ to polish the surface. A little amount of wet dough is taken and applied on the vessel. It is removed with a knife thereby burnishing the vessel. The process is repeated two to three time still the vessel becomes absolutely even. It is then left for drying. After it dries, it is again rubbed with sandpaper.
Coating with Mixture
After this process a solution of quartz powder (10 kilograms), powdered glass (3 kilograms), edible flour (maida) and water is made. The vessel is dipped in this solution and taken out in such a way that it is evenly coated. It is then left to dry.
Designing
A design is made on the dried, coated vessel with a solution of cobalt oxide and edible gum. The initial rings on the vessel (if circular) are made by keeping it on the potter’s wheel and touching the brush tip on the vessel. The later intricate design is then made by brushes of varying thicknesses.
Coloring
Once the design of the vessel is complete; the coloring is done by using oxides of various metals. These oxides are mixed with edible gum and then ground on the stone. The color is carefully filled with a brush. The vessel is left for drying.
Glazing
After this, a coating of glaze is done on the vessel. The mixture of glaze is prepared by mixing the following things in their respective proportions: Powdered glass (21 kilograms), borax orsuhaaga (17.5 kilograms), zinc oxide (1.5 kilograms), potassium nitrate (2.5 kilograms) and Boric acid (7.5 kilograms). This mixture is heated in the kiln till it melts. On cooling, the mixture transforms into small pebbles. It is then ground to a powdered form in the grinding machine. The mixture is mixed with water and maida (used as an adhesive). The solution is then coated on to the vessel.
Firing
Finally, the prepared vessels are heated in the closed kiln fuelled with charcoal for four to five hours at temperatures of 800 to 850 degrees Celsius. Most of the material melts, but 80 per cent of the quartz is left behind, and this maintains the form of the vessel. The kiln is left to cool for three days, avoiding any rapid temperature change which cracks the china very easily. Care is taken that no two vessels touch each other as they may turn black. After cooling, the vessels are taken out and are ready for sale.
Jaipur was founded on 18 November 1727 by Maharaja Sawai Jai Singh II who was a lover of astronomy, mathematics and astrophysics. The city was named after him when he shifted the capital from Amer to Jaipur due to growing population and scarcity of water. Jaipur was a planned city and the layout was based on several traditional architectural treatises like the Vaastu Shaastra. In 1876, during the regime of Sawai Ram Singh, the whole city was painted pink to welcome Edward, Prince of Wales. Even today, these buildings remain painted in pink, giving Jaipur a distinctive appearance. In 1922, the throne was taken over by Man Singh II, during his reign buildings like secretariat, schools, and hospitals were built. After India got independence, Jaipur merged with Jodhpur, Jaisalmer and Bikaner to form the largest state of India with Jaipur as its capital.
Jaipur is located in the eastern part of Rajasthan at the co-rdinates of 26.92°N 75.82°E. It has an average elevation of 431 metres (1417 ft). The rivers Banas and Banganga pass through the district.
By air - Jaipur Airport at a distance of around 11 km from the city center is the main air gateway to Jaipur. There are direct flights to Delhi, Mumbai, Udaipur, Jodhpur, Aurangabad, and some other cities from Jaipur.
By rail - There are many trains that connect Jaipur and other cities in Rajasthan; Palace on Wheels is a dedicated train for tourists. Other important trains include, Shatabdi Express and Pink City Express both from Delhi.
By road - From Delhi, there is a direct and well-maintained road to Jaipur. City is connected to most of the tourist destinations in Rajasthan as well as Agra. Jaipur is part of the Golden Travel Circuit of India that includes Delhi, Agra, and Jaipur. Most of the tours are conducted either through the buses or trains.
Jaipur has a semi-arid hot climate with monsoon months bringing in 650mm of rain from June to September, the summer months of April to early July having average daily temperatures of around 30 °C and the winter months of November to February are chilly with average temperatures ranging from 15 to 18 °C.
Jaipur district is a centre for both traditional and modern industries. It is famous as a large exporter of gold, diamond and stone jewellery in Asia it is the only city finishing blue diamond, or tanzanite, in the world. It is a fast developing city and has every necessary infrastructure like airports, banks and educational institutes. Jaipur is a hub of educational activities from primary level to college level education. University of Rajasthan in Jaipur has completed its 60 years. Jaipur district is receiving the hydro-electric power, supplied by the Chambal Hydel System. Out of total 2,131 villages in the district, all were electrified (as on March 2000).
Jaipur was developed as India's first ever planned city by Raja Jai Singh with the help of chief architect from Bengal, Vidhyadhar Bhattacharya. Vidhyadhar Bhattacharya, following the principles of Shilpa Shastra (the science of Indian architecture), and referencing the ancient Indian knowledge on astronomy, devised the planning of the entire new capital. The town of Jaipur is built in the form of an eight-part Mandala known as the 'Pithapada'.
The city was divided into nine blocks, of which two consist the state buildings and palaces, with the remaining seven allotted to the public. Huge fortification walls were made along with seven strong gates for the purpose of security of the city. Jaipur city is remarkable among pre-modern Indian cities for the width and regularity of its streets which are laid out into six sectors separated by broad streets of 111 feet. This number is a holy number in Hinduism and hence considered lucky.
Jaipur is largely populated by the Hindu community, closely followed by a substantial percentage of Muslims, Sikhs and Jains. Hindi and Rajasthani are the most commonly spoken languages. The Rajasthani culture is colourful and flamboyant. It is rich in heritage. Famous dances of Jaipur include Ghoomar and Chari; the Chari dancers dance gracefully on a pot with a lit diya on their head. Traditional instruments like Sarangi, Ektara, and Jhalar are also played while singing folk songs. Food or the local delicacies of Jaipur also reveal the culture of the city. Jaipur's utterly delicious mangodi, papad, khichdi, buttermilk, sohan halwa have no match.
The prominent festivals celebrated are:
Teej- This festival is dedicated to Lord Shiva and Parvati; celebrated during the month of monsoon July-August by married women who pray for a long and happy marital life.
Gangaur fair- Idols of Issar and Gangaur, manifestations of Shiva and Parvati, are worshipped by women, particularly those unmarried women who wish for a consort of the likes of Shiva.
Elephant festival- This is celebrated during the month of Holi. The elephants are caparisoned, their bodies painted with floral decorations by the mahouts and paraded around with great pomp.
The lac bangles are crafted by the Manihar community who are traditional Muslim bangle makers. Many of them were rajputs who had converted to Islam. The community speaks Shaikawati dialect of Rajasthani.
The city is one of the most sought after destinations. It is famous for its architecture, vibrant handicrafts and arts.
Hawa Mahal - The palace of winds was built in 1799 A.D by Maharaja Pratap Singh. This five storied pyramid shaped structure is made up of small casements, each with tine windows and arched roofs with hanging cornices, exquisitely modeled and carved. This unusual structure is more like a screen than a palace, its top three stories are just a single room thick and at the base are two courtyards.Built at a time when ladies of the royal household observed very strict pardaa, this unusual palace, with its screened balconies provided them with an opportunity to watch processions and other activities on the streets without being observed themselves.
Jal Mahal - The lake palace was built in the middle of Man Sagar Lake near Amber. There was a natural depression in earth where the rain water of surrounded Aravali Hills was collected. No man made construction was there till 16th century. Natural beauty of lake, surrounded Aravali hills, lush green mountains, and migratory birds attracted Sawai Pratap Singh, the then-ruler of Amber. In 1799 AD, Sawai Pratap Singh decided to convert Man Sagar Lake in a pleasure spot; hence, he built Jal Mahal.
Jantar Mantar - This fascinating observatory was constructed in the year 1728 by Maharja Sawai Jai Singh II, the founder of Jaipur. He was a learned person and a great astrologer. He acquainted himself thoroughly with religion, philosophy, art, architecture, Hindu, Greek, Muslim and European schools of astronomy and astrology. He thoroughly studied Ptolemy's Syntaxis, De La Hire's Tabulae, Newton's Principia, Euclid's Clements, Mirza Ulugh Beg's Astronomical Tables, Master works of Aryabhatta, Varahmihir, Brahamgupt, and Bhaskaracharya. UNESCO inscribed Jantar Mantar Jaipur in the list of World Heritage in July 2010.
List of craftsmen.
Team Gaatha