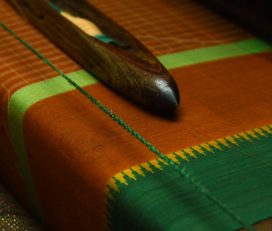
Saree Weaving ~ Nara...
Narayanpet sarees, handwoven in the small, vibrant town of Narayanpet in Telangana, are not confined to ceremonial grandeur or museum-worthy curation.
Narayanpet, Telangana, India...
The leather craft of Jawaja, which was practiced for more than three hundred years, was beautifully structured and meticulously stitched back to glory through a joint initiative taken by IIM and NID in the 1970s. Through this collaboration known as ‘The Rural University Initiative’ the institutions devised innovative methods of coproducing, that would prove fruitful in permanence for the Jawaja craftsmen. This effort has been a turning point in the fortunes of the craft, as the products are making a mark universally.
Leather bag
The leather craft of Jawaja, which was practiced for more than three hundred years, was beautifully structured and meticulously stitched back to glory through a joint initiative taken by IIM and NID in the 1970s. Through this collaboration known as ‘The Rural University Initiative’ the institutions devised innovative methods of coproducing, that would prove fruitful in permanence for the Jawaja craftsmen. This effort has been a turning point in the fortunes of the craft, as the products are making a mark universally.
The ‘Raigar’ communities are the leather workers.
It was initiated by then director of IIM, Ahmedabad Prof. Ravi Mathai and ‘National Institute of Design’, Ahmedabad, was invited to collaborate under the guidance of Prof. Ashok Chatterjee.
– The surface finish is either kept buffed or plain.
– Pockets are a common feature on leather bags.
– Flaps are provided on the top of the leather bags.
– Braiding is a characteristic feature. It is done either on the shoulder strap or as decoration.
Initially the craftsmen would only make leather water canteens and shoes as these were the basic needs of the local people. But after the ‘Rural University Initiative’, the horizon of the leather craft products has widened to include various types of leather bags, purses, accessories such as belts, key chains, file folders and other storage products. Of these, the leather bags have proved to be the most successful products and have become symbolic to the craft.
The Jawaja project has brought about a new lease of life and self-dependency to the village. It has been able to slowly break the caste divide and form an environment of mutual respect for the professions. The most visible interaction has been of traditional skill with modernity, the meeting of two worlds. This has proven to be an inspiration to many movements thereafter, with self-empowerment and reliance as their goals. The Jawaja village was thus crafted in a way that the people itself became its reliable resource.
In the words of Prof. Ashok Chatterjee (NID) from an interview conducted in 20 October 1997 by Carolyn Jongeward,
“15 to 20 years ago the artisans of Jawaja had no ability to deal with the external market. There was no capacity to understand the needs of buyers far removed from them physically, socially, emotionally and psychologically. That gap was huge. They felt inadequate and that they needed to wait until someone told them what to do. In those days they couldn’t enter the Taj Hotel in Bombay to have direct contact with a buyer. Now they are no longer thrown out of the Taj Hotel. They are travelled widely and have developed street smartness to cope. Now their products have gained an international reputation, not just occasional local exposure. OXFAM, just one of their international buyers, has sold their crafts for almost 15 years. This is a huge accomplishment for this community…
In 1975, a small collective of people from the ‘Indian Institute of Management’, Ahmedabad, conducted an experiment in rural education and development. It was initiated by then director of IIM, Ahmedabad Prof. Ravi Mathai. The initiative was called ‘The Rural University’ and the ‘National Institute of Design’, Ahmedabad, was invited to collaborate under the guidance of Prof. Ashok Chatterjee.
With an aim to actively collaborate with the rural communities and to catalyze local solutions to problems of poverty and self-reliance, the volunteers, teachers and students from both these institutions worked together with the people of the Jawaja village.
Jawaja, an erstwhile derelict village of Rajasthan that had been written off by the government as a resource-less and underdeveloped region, was given a new lease of life.
A team of designers headed by product designer Ms. Helena Peerhenthupa and textile designer Ms. Neelam Iyer worked with the lowest caste of occupational groups – the ‘Raigar’ families of leather-workers and the relatively better off ‘Bunkar’ families or the weavers. The team had to deal with an initial opposition and skepticism from the doubting villagers and village elite.
Of the few tools the villagers were equipped with, the loom was a prominent one. The ‘Bunkars’ or the ‘weavers’ used it to weave woolen shawls, ‘Odhnis’ and other locally worn textiles. They would use it for themselves, barter it for food and other supplies or sell them in the local market for cash.
The ‘Raigar’ communities, on the other hand, were leather workers. They made objects like camel harnesses, footwear and other adornments. In the 1940’s and 1960’s, the work of this community was facing a major setback because of the banning of flaying, tanning and shoe repair by their community heads to raise their social standing. By the 1970’s, the leather workers had to purchase leather at high market rates making the craft highly disadvantageous. With the advent of electric pumps and motors, the leather bags or ‘Chaaras’ made by them to draw water from the wells also became obsolete. The local markets were ruled by the higher castes and the money lenders.
The ‘Rural University’ team helped the villagers overcome these obstacles to a large extent and worked with the rural craftsmen to develop contemporary products which could be sold in the national market. Many other organizations were consulted for refining the techniques and making the processes more speedy and efficient. The craftsmen were taught modern marketing skills and contemporary design interpretations, in a manner that now they have become artisan designers in their own right. Presently the processes of management, innovation and marketing are completely run by the artisans themselves.
The design elements were worked out by the craftsmen in collaboration with the designers from the reputed design institutes of the country to obtain the most out of the material. A few commonly followed design elements are:
– The surface finish is either kept buffed or plain.
– Pockets are a common feature on the leather bags.
– Flaps are provided on the top of the leather bags.
– Braiding is a characteristic feature. It is done either on the shoulder strap or as decoration. This has various advantages as leather has to be cut into thin strips. Even stiff leather is more pliable in thin strips and does not show much defects of the skin. Once the basic braiding principle is learnt, any number of variations can be achieved.
Every step in the leather craft, from processing to finishing, is done without the use of any machines. While environmental pollution continues to be an important issue, the younger generation may be losing interest in this traditional craft. Many now have salaried jobs in nearby towns.
The biggest challenge for Jawaja craftsmen has been marketing their work in western markets due to stiff competition and a language barrier. According to a few craftsmen they are not able to explain their work well because of this. They do not know what the customers understand and what they don’t. The customer’s understanding determines the monetary value they give for the craftsmen’s work.
The buyers of the Jawaja products are located in places far away from the village. The means of transport and accessibility are very less for the craftsmen. This has led to almost no direct interaction with the buyers. Only middlemen have direct interactions and the artisans only know what they tell them. Even though they have a website, there have been no or very few direct sales.
‘The leather products of Jawaja are completely hand made from the very first stage of their making. The leather is sourced and processed in a manner that reduces its odour and is made workable. The craftsmen work with this leather from his workshop at home. Its unique leather stitches set it apart from the other leather work available in the markets.’
Leather – It is sourced from Nasirabad and Raipur
Chemicals for processing – Chemicals such as lime, sodium sulphite, sulphuric acid are used to treat the raw animal hide.
Varnish or glaze – It is used to add shine and polish the final leather product.
Brass button and Buckle –
Fabric – for lining
Knives – A curve edged knife is used to clean the flesh off the inside of the leather and make it even. Smaller knives are used to cut the leather pieces to workable sizes.
Palet – A blunt edged palet is used to smoothen and stretch the leather. It is shaped like a mason’s tool.
Hammer – A cylindrical hammer is used to pound the wet leather to soften it.
Awl – A straight awl needle is used to pierce holes through the thick leather.
Aari Needle – A flat blunt needle is used to pull the leather strips to stitch the pieces together.
‘The leather products of Jawaja are completely hand made from the very first stage of their making. The leather is sourced and processed in a manner that reduces its odour and is made workable. The craftsmen work with this leather from his workshop at home. Its unique leather stitches set it apart from the other leather work available in the markets.’
Flaying
Removing the skin of the animal is called Flaying. The skins obtained are of two types, one is from the slaughterhouse and the other is removed from animals that die a natural death. The skins from the slaughterhouse can be recognized by the horizontal cut made at the neck. These are obtained in far better conditions than others. This is mainly so because animals that die naturally have to be flayed only after taking them to the outskirts of the community. This dragging and moving causes many scratches on the skin.
Preserving
The skin has to be protected from putrefaction once it is removed from the animal carcass as there is often a long gap of time before the actual tanning process begins. For preserving the skin it is dried in the sun, dry salted (salt sprinkled while drying in the sun) or wet-salted (skins soaked in brine).
Processing leather
The tanning process prevents putrefaction and imparts durability to the leather. It also makes it firm, supple and resistant. Various types of tanning methods are employed such as vegetable tanning, mineral tanning (using Alum & salt or more recently Chromium or Zirconium salts) as well as ‘Chamoising’ or oil tanning (using fish oil). Even though mineral tanning is a much faster process, the most process of vegetable tanning is widely followed.
Cleaning and drying
The fresh hides are first washed in plain water. The inner side of the hide is plastered with mud or salt and spread out flat. It is also sometimes held by pegs to prevent contraction. This is then dried and scraped with a blunt instrument to remove dirt particles. It is again spread flat to remove the creases and folds.
Liming
The liming process makes the hides swell to make it porous and permeable to the tanning solution. The hide is sprinkled with milk extracts of ‘Aankda na phool’ and with a solution of water and salt. This is done once or twice in a day, for a period of 14 days. A goat hair brush is used to spread this solution on the hide or it is done by hand. This is then folded and immersed into a pit containing the mixture. The skin is usually taken out every day, aired for an hour and immersed again.
Removing hair
After liming, the water is wrung out and the hide is spread on a smooth surfaced stone. The liming makes the hair fall off easily. The hair is scraped off using a blunt knife, also called Scudding. It is then soaked for 2-3 hours. Next the adherent flesh and fat on the inner side is scraped clean with a sharp knife. This step takes one whole day. After this, the hide is then put in clean running water and the lime is washed away.
Applying tannin
Treading is done for 3-5 hours a day, while rubbing with hand is done 4-5 times. After 2-4 days, the hide is taken out and the moisture is squeezed out or alternatively it is pressed on a draining table. The hide is again soaked in a fresh and stronger solution of tannin mixture for 2-3 days. This process is repeated 5-6 times.
Infiltration process / bag process
The hides are sewn together to the leather water bag. The tannin liquor is then poured into this bag, which is suspended on bamboo bars. This facilitates proper impregnation of the hide with tannin. The process is repeated several times after which it is done with the bag turned inside out. The hide is occasionally beaten to test if the tanning is done. If it produces a hard sound, it indicates the process is complete but if the sound is soft then the tanning is unsatisfactory.
Finishing
1) Softening– The leather bag is opened out and stretched to partially dry it. It is then rolled up and trampled for some time before it is unrolled. This makes the leather compact, soft and supple.
2) Shaving- The outer side of the leather is scraped, rubbed and scoured with a knife. This process helps remove creases and the marks of the folds.
3) Polishing and Graining-The leather is now dressed with oil, mostly vegetable oil. It is applied over the leather using a smooth edged instrument or a glass bottle.
Coloring and varnishing
There are three methods of coloring the leather:
1) Dyeing – The leather is immersed in the dye bath until the dye penetrates. The grain pattern will nevertheless be visible through the color. Further glazing can be done using pigment or varnish.
2) Staining – In this case only the grain side of the leather is colored as it is not immersed in solution, but the solution is applied using a brush or a spray. This too can be glazed after.
3) Pigmentation – Pigment color is coated using a spray on the grain side of the skin. This forms an even surface and is used to hide flaws in the skin. In this method the natural grains of the skin are hidden. A plastic finish is obtained. Therefore, the leather is sometimes embossed with an artificial grain pattern.
4) Making bags– Two rectangular pieces of uniform thickness are taken for the front and back pieces or the body of the bag. The top edges of both are folded down. Firstly, a ‘V-shaped’ groove is cut on the underside along the line of the fold.
The position of the pocket is marked on one of the pieces and the top edge fold of the pocket is stitched. The piece for the pocket is dampened and stuck with rubber solution and then stitched over. A wooden mould is inserted into the damp pocket piece to help it get the sturdy shape.
The lower corners of the front and back pieces are folded at a 45 degree angle along diagonally folded upwards and then stuck. The overlap of the joining strip is marked on the sides and then stuck to both the pieces simultaneously. The right-angled triangles at the base are stitched along the sides of the triangle. The shoulder strap too is first marked and then stitched in a rectangular form. It is stitched with two crossed lines to add strength.
Braiding
According to the design requirements, the technique of braiding is used in the leather products in the form of braided straps or embellishment. The basic principle of braiding is the overlapping of a number of linear strips with each other in one plane. Each strip rides over the two consecutive strips, and goes under the third one. This is done alternatively with strips from both sides. There are three types of braiding done:
1) Flat braiding – In this type, the minimum number of strips used is three and many more can also be used. For greater variations in patterns, more number of strips is used.
2) Circular plaiting – The minimum number of strips used is four. As the number of strips increases, the circular tubes become wider and forms cylindrical shapes that can be used in making dog leashes, whips, decorative cover for cylindrical objects etc.
3) Square or solid braiding -The outermost strip is crossed over its own group and the next two groups, then threaded under the last group it has crossed over, ending in the center of the strands. In this manner, an enclosed solid braid is made which is flexible in both directions.
During tanning process, substantial amount of water gets wasted. This can be recycled and put to other uses. Left-over pieces of leather can be cut into thin strips and used as stitching material for binding the pieces together. These strips are also used in braiding and making smaller products or parts of products like pocket flaps, folder binding strips, button hooks, beadings etc.
Beawar was founded by Colonel Dixon in 1835 AD. It was part of British India, and the administrative headquarters of Merwara district. Since early times, the region where 'Beawar' lies is called the 'Magra-Merwaran', and it was named after a local village called 'Beawar Khas' by the British. This region was ruled by fierce tribes such as the 'Kathats' (Muslim Rajputs) and 'Rawat Rajputs'. The British tried to subdue them but were unsuccessful because the tribes were scattered across many small villages and they were excellent in conducting guerilla warfare. The 'Battle of Shyamgarh' was fought between the Kathats and the British. The British won and Kathats abandoned the fort of Shyamgarh, but employed guerilla tactics causing great loss to the British. So the British founded a military cantonment with fortified walls for protection and further military missions. Another factor involved in building a cantonment here was, Beawar was situated at a strategic tri-junction of the royal states of Jaipur, Jodhpur, and Udaipur.
To keep the menace of Kathats and Rawat-Rajputs at bay, British raised a battalion enrolling Kathats and Rawat-Rajputs (designating them as a Martial Race) and named it Magra-Merwara battalion. They used this Battalion for further military missions which proved quite efficient. According to a legend British put a sign board of 'Be-aware' as a warning to the British caravans and officers leaving the cantonment or crossing the cantonment. Slowly with time the local people came to think of it as the name of the cantonment and so the cantonment came to be called 'Beawar'.
The 'Jawaja' village is located in the 'Jawaja Panchayat Samiti' or the 'Jawaja Block' on the National Highway no.8. It is located around 70 kms south of Ajmer and about 500 kms north of Ahmedabad on the highway. The only largest town near it is Beawar. It consists of about 200 villages and hamlets of which one of them is Beawar Khas village and is situated 4 kms northeast of Beawar. It extends over an area of 3015 acres of land.
The village used to boast of a rich forest many years ago that has now depleted with only few trees remaining. Dense shrubs appear during the monsoons and the land is dry and dusty during the remaining months. The main vegetables grown in the northern region of Jawaja are tomatoes and hot peppers or chillies. The chief grain crops are bajra, maize, jowar and wheat. The area is drought or flood prone, in the two extremes, because of the topography of the land. Most of the land that can be cultivated is a thin strip towards the centre of the block, starting from the south of Jawaja village and widening towards Beawar. Just outside the village of Beawar Khas is a lake that has dried.
The village has one school and around four drinking water wells. There is a medical dispensary and it has power supply. The village has a few small shops where basic commodities and groceries can be bought. A tea stall and post office are situated next to each other. This spot is also used as a space for panchayat meetings, casual gatherings and festival celebrations. It depends on the town of Beawar for further needs. The neighboring Beawar town is equipped with cinema halls, schools (both middle and higher secondary), college, municipal library and hospitals.
The narrow roads are lined with rows of brick houses. There are two small temples or shrines in the centre of the village, built in the shade of a banyan tree. The houses are simple and seldom have decorations on them. Most houses still have thatched roofs and walls of mud mortar.
The weave's houses lie in a separate cluster away from the other communities. Each house has its loom placed in an area to catch maximum sunlight. Some weavers don't have looms at home and they work under a master weaver.
The staple food is maize. Rice appears less often in their cuisine as compared to wheat, bajra/maize and jowar. Tea is a popular beverage. Meals are eaten early in the mornings and early in the evenings. It consists of a thick maize roti and chutney made of chilies and onions.
Marriages are arranged by parents and they are very strict about it. In the Bhambi or weaver community, the grooms' father or the bridegroom himself gives the dowry. Divorce is allowed and widows are permitted to remarry. An interesting ritual exists in the community, called the 'Nate-lana', a marriage without a marriage. The bride goes back to her father's home after the wedding and anyone can approach her father for her hand by paying some money. If the husband wants her back, he has to pay twice the amount of money the new suitor has paid.
The majority of people are occupied in multiple occupations. The two main occupations are farming and craft. The higher castes are 'Rawats', 'Rajputs', 'Mehrats' and 'Jats' while the 'Harijans' are considered as the lowest caste. The craftsmen are 'Kumbhars' (potters), 'Lohars' (blacksmiths), 'Kuhars' (former palanquin carriers), 'Raigars' (cobblers) and the 'Bhambis' or 'Bunkars'(weavers). The 'Bhambis' were generally regarded as 'untouchables' or 'Harijans' after the Gandhi movement and thereafter they fall into the schedule caste category. The men wear simple 'Rajasthani' attire consisting, of a traditional shirt, dhoti and turban while the younger generations have taken to more western fashions such as jeans, trousers and t-shirts. Women wear traditional attires consisting of Lehenga, Choli, Odhani and wear ornaments that display their financial standing in society.
The village is famous for its vibrant dhurries and weaving.
List of craftsmen.
Team Gaatha