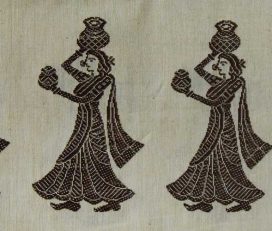
Gollabhama Saree Wea...
The Siddipet Gollabhama Saree is not just a piece of fabric; it is a living tradition, worn, celebrated, and reinterpreted through generations.
Siddipet, Telangana, India...
The lac bangles are vibrant manifestations of resin, crafted by the artisans in Jaipur. These bangles being an integral part of culture in Jaipur, attract localities and visitors alike.
The importance of these bangles marks a religious, cultural and auspicious context. Many Rajasthani rituals require specific ornamentations and the lac bangles are one of them. These are highly sought after for local celebrations such as teej, the marwari festival of gangaur, karva chauth, holi, weddings and special ceremonies for the mothers-to-be. It has been a custom that the bride wears lac bangles on her wedding day and after being married.
Lac production is also found in Bangladesh, Myanmar, Thailand, Laos, Vietnam, parts of China, and Mexico.
Ironically, lac has many significance other than in bangle-making. It is also used to make decorative objects, paintings, home accessories, pens, diaries, toys and to create jewelries like rings, toe rings (bichchua), anklets (payal), nose rings, necklaces, Bala, Bajuband, Rakhi, Gajra, Gokhru, Timaniyan and ‘maathe ka tika.
The lac bangles are made in a variety of ways. They are made plain with a smooth surface with a variety of colours. The lac sometimes acts as the base to hold pieces of precious and semi-precious stones as well as coloured glass.
The lac bangles form an essential part of tradition. The ‘gulali choodha’ (red coloured bangle) or the ‘Hare bandon ka choodha’ (green coloured bangles) is purchased during weddings. The pink ones are worn during Holi. This craft is also used to create rings, toe rings (bichchua), anklets (payal), nose rings, necklaces, bala, bajuband, rakhi, gajra, gokhru, timaniyan and ‘maathe ka tika’. The lac is also sometimes used to hold the ornament when it is being set with precious/semi-precious stones or enameled. It is also used to fill the ornaments to give it body and strength.
The significance and beauty of these bangles lies in their ability to be customized. The manihari women create custom made accessories for their clientele by adjusting the bangle to the desired size and ornamenting them with the preferred beads, stones, crystals and other embellishments fancied by the she patrons visiting the store.
The lac bangles can be reused once broken, they can be rejoined by mild heating and shaping, however reheating and forming makes the lacquer brittle; therefore the reworking has a limit of 8 to 10 times only.
Lac bangles are skin soothing and don’t cause infections or itchiness.
The story of the notorious Lac palace built by the Kauravas in a plot to eliminate the Pandavas, in an episode from the 3000-year-old Mahabharata epic sheds more light on the history of this material.
Lac has been mentioned in the texts of vedas. The Lakshataru or the Lac tree is a well known feature. A small chapter is devoted to the Lac insect in Atharva Veda. It appears in the story of the notorious Lac palace built by the Kauravas in a plot to eliminate the Pandavas in an episode from the 3000-year-old Mahabharata epic. Ayurveda stresses the importance of lac in medical therapies. India is one of the largest producers of lac and its principal exporter. It is widely used in food processing, textile, leather, cosmetics, varnish, and printing industries. Being biodegradable and eco-friendly its usage is becoming highly popular.
The craft of making Lac bangles dates back to the time when Jaipur was established. The king of Amer had invited craftsmen from the Manoharpur district of Uttar Pradesh to settle down in his kingdom. When the capital city of Jaipur was established, the crafts men shifted base. The craft is practiced by the Muslim community. The women sit at the shops and the men work at preparing the raw material in the kilns.
The lac bangles are made in a variety of ways. They are made plain with a smooth surface and painted over with a variety of colors. The lac sometimes acts as the base to hold pieces of precious and semi-precious stones as well as colored glass.
The availability of Lac has decreased due to deforestation and led to the escalation of raw material costs. The lack of awareness has also led to the buyers expecting the products in the same prices. This has led to a decrease in demand and the number of outlets falling to around 200-250 in number from 1500 in the last few years. The craftsmen too have started to seek alternative professions with better returns.
The lac pieces are melted in the shallow vessel till it reaches a semi-molten state. At this stage beroza and giya pathar powder is added along with powdered colors brought from the market. The mixture is stirred well. Once the mixture is properly made heating is stopped and the liquid is allowed to cool down to a semi solid state. After this, lac is stuck at the end of a wooden or cane stick.
Lac is a crimson red, plant sucking, tiny insects such as Laccifer lacca, Carteria lacca and Tachardia lacca colonize the branches of selected species of host trees and secrete a natural scarlet resin known as Lac. Later the different layers of resin residue on the coated branches of the host trees are scraped off as long sticks known as sticklac, crushed, sieved and washed several times to remove impurities till it shows up in natural red color. This is sourced mainly from Balrampur in Uttar Pradesh. Other raw materials include beroza, giya pathar powder, coal, sequins, semi precious stones and colors such as pevdi (yellow), safeda (lithophone), copper, green and chamki (gold).
Angethi is a coal burner with flat steel plates in top; it is utilized for generating heat. Kadai is used to accommodate lac while heating and coloring; it is a shallow vessel with huge capacity. Chimta is another traditional tool which is used to stir, it is a large spatula. Hattha a handle shaped tool helps in pressing and shaping lac. Wooden rod, stone piece, iron bangles, tin foil, round wooden rod, cutter tool are some of the general tools which are taken into account in lac bangle making.
Many Rajasthani rituals require specific ornamentations and the lac bangles are one of them. These bangles are considered essential for local celebrations such as teej, gangaur, karva- chauth, holi, weddings and special ceremonies for the mothers-to-be.
The lac pieces are melted in the shallow vessel till it reaches a semi-molten state. At this stage beroza and giya pathar powder is added along with powdered colors brought from the market. The mixture is stirred well. Once the mixture is properly made heating is stopped and the liquid is allowed to cool down to a semi solid state. After this, lac is stuck at the end of a wooden or cane stick.
Rang Chapna
The normal lac, without the pigment, is stuck around a wooden rod is heated slowly over the coal burner or Angethi and is simultaneously pressed with a stone or a wooden tool called hattha at regular intervals. When it is sufficiently warm and soft, it is covered with the desired colour by rubbing the coloured lac stick on it evenly
Rolling the bangle
After the desired colour is applied, this lac piece is again shaped with the help of Hatta into a thin coil and then it is cut off from the plain lac rod. The thickness and the length of the coil approximately depend on the final shape and size of the bangles. This whole process is done by a single artisan and then passed on to different artisans. The coil is then placed in a farma or a mould for the shape of the bangle, and pressed with the help of hatta so that the coil takes the shape of the farma. This coil is taken out and heated over a burner. Moohjodai or joining the ends of the bangle is done using this heat.
Working on the bangle
Another artisan takes up these coils and slips it onto a wooden beam with a tapering end, for different sizes. A cotton cloth is dipped in oil and used to hold these coils and rub them on the hot wooden beam. This gives a shine to the bangles and the process is called Ghotaai. Once the bangles have reached the desired shape and size, they are dipped in cold water and then left to dry.
Embellishments
If adornment is required, these bangles are then heated over a tin plate kept on a small burner. Sequins or other embellishments are placed on this warm surface according to the design. They settle in and stick once the lac is cooled. The process requires great precision. It takes much longer when working with smaller sized sequins. This process is called Chipai.
Coal ash and other types of ashes resulting from burning fuels is the major waste in Lac bangle making, it can be utilized brick making process.
Jaipur was founded on 18 November 1727 by Maharaja Sawai Jai Singh II who was a lover of astronomy, mathematics and astrophysics. The city was named after him when he shifted the capital from Amer to Jaipur due to growing population and scarcity of water. Jaipur was a planned city and the layout was based on several traditional architectural treatises like the Vaastu Shaastra. In 1876, during the regime of Sawai Ram Singh, the whole city was painted pink to welcome Edward, Prince of Wales. Even today, these buildings remain painted in pink, giving Jaipur a distinctive appearance. In 1922, the throne was taken over by Man Singh II, during his reign buildings like secretariat, schools, and hospitals were built. After India got independence, Jaipur merged with Jodhpur, Jaisalmer and Bikaner to form the largest state of India with Jaipur as its capital.
Jaipur is located in the eastern part of Rajasthan at the co-rdinates of 26.92°N 75.82°E. It has an average elevation of 431 metres (1417 ft). The rivers Banas and Banganga pass through the district.
By air - Jaipur Airport at a distance of around 11 km from the city center is the main air gateway to Jaipur. There are direct flights to Delhi, Mumbai, Udaipur, Jodhpur, Aurangabad, and some other cities from Jaipur.
By rail - There are many trains that connect Jaipur and other cities in Rajasthan; Palace on Wheels is a dedicated train for tourists. Other important trains include, Shatabdi Express and Pink City Express both from Delhi.
By road - From Delhi, there is a direct and well-maintained road to Jaipur. City is connected to most of the tourist destinations in Rajasthan as well as Agra. Jaipur is part of the Golden Travel Circuit of India that includes Delhi, Agra, and Jaipur. Most of the tours are conducted either through the buses or trains.
Jaipur has a semi-arid hot climate with monsoon months bringing in 650mm of rain from June to September, the summer months of April to early July having average daily temperatures of around 30 °C and the winter months of November to February are chilly with average temperatures ranging from 15 to 18 °C.
Jaipur district is a centre for both traditional and modern industries. It is famous as a large exporter of gold, diamond and stone jewellery in Asia it is the only city finishing blue diamond, or tanzanite, in the world. It is a fast developing city and has every necessary infrastructure like airports, banks and educational institutes. Jaipur is a hub of educational activities from primary level to college level education. University of Rajasthan in Jaipur has completed its 60 years. Jaipur district is receiving the hydro-electric power, supplied by the Chambal Hydel System. Out of total 2,131 villages in the district, all were electrified (as on March 2000).
Jaipur was developed as India's first ever planned city by Raja Jai Singh with the help of chief architect from Bengal, Vidhyadhar Bhattacharya. Vidhyadhar Bhattacharya, following the principles of Shilpa Shastra (the science of Indian architecture), and referencing the ancient Indian knowledge on astronomy, devised the planning of the entire new capital. The town of Jaipur is built in the form of an eight-part Mandala known as the 'Pithapada'.
The city was divided into nine blocks, of which two consist the state buildings and palaces, with the remaining seven allotted to the public. Huge fortification walls were made along with seven strong gates for the purpose of security of the city. Jaipur city is remarkable among pre-modern Indian cities for the width and regularity of its streets which are laid out into six sectors separated by broad streets of 111 feet. This number is a holy number in Hinduism and hence considered lucky.
Jaipur is largely populated by the Hindu community, closely followed by a substantial percentage of Muslims, Sikhs and Jains. Hindi and Rajasthani are the most commonly spoken languages. The Rajasthani culture is colourful and flamboyant. It is rich in heritage. Famous dances of Jaipur include Ghoomar and Chari; the Chari dancers dance gracefully on a pot with a lit diya on their head. Traditional instruments like Sarangi, Ektara, and Jhalar are also played while singing folk songs. Food or the local delicacies of Jaipur also reveal the culture of the city. Jaipur's utterly delicious mangodi, papad, khichdi, buttermilk, sohan halwa have no match.
The prominent festivals celebrated are:
Teej- This festival is dedicated to Lord Shiva and Parvati; celebrated during the month of monsoon July-August by married women who pray for a long and happy marital life.
Gangaur fair- Idols of Issar and Gangaur, manifestations of Shiva and Parvati, are worshipped by women, particularly those unmarried women who wish for a consort of the likes of Shiva.
Elephant festival- This is celebrated during the month of Holi. The elephants are caparisoned, their bodies painted with floral decorations by the mahouts and paraded around with great pomp.
The lac bangles are crafted by the Manihar community who are traditional Muslim bangle makers. Many of them were rajputs who had converted to Islam. The community speaks Shaikawati dialect of Rajasthani.
The city is one of the most sought after destinations. It is famous for its architecture, vibrant handicrafts and arts.
Hawa Mahal - The palace of winds was built in 1799 A.D by Maharaja Pratap Singh. This five storied pyramid shaped structure is made up of small casements, each with tine windows and arched roofs with hanging cornices, exquisitely modeled and carved. This unusual structure is more like a screen than a palace, its top three stories are just a single room thick and at the base are two courtyards.Built at a time when ladies of the royal household observed very strict pardaa, this unusual palace, with its screened balconies provided them with an opportunity to watch processions and other activities on the streets without being observed themselves.
Jal Mahal - The lake palace was built in the middle of Man Sagar Lake near Amber. There was a natural depression in earth where the rain water of surrounded Aravali Hills was collected. No man made construction was there till 16th century. Natural beauty of lake, surrounded Aravali hills, lush green mountains, and migratory birds attracted Sawai Pratap Singh, the then-ruler of Amber. In 1799 AD, Sawai Pratap Singh decided to convert Man Sagar Lake in a pleasure spot; hence, he built Jal Mahal.
Jantar Mantar - This fascinating observatory was constructed in the year 1728 by Maharja Sawai Jai Singh II, the founder of Jaipur. He was a learned person and a great astrologer. He acquainted himself thoroughly with religion, philosophy, art, architecture, Hindu, Greek, Muslim and European schools of astronomy and astrology. He thoroughly studied Ptolemy's Syntaxis, De La Hire's Tabulae, Newton's Principia, Euclid's Clements, Mirza Ulugh Beg's Astronomical Tables, Master works of Aryabhatta, Varahmihir, Brahamgupt, and Bhaskaracharya. UNESCO inscribed Jantar Mantar Jaipur in the list of World Heritage in July 2010.
List of craftsmen.