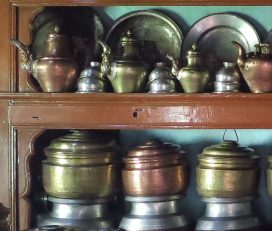
Copper Craft ~ Chili...
Copper and brass have played a significant role in fulfilling these needs. Even today, in most traditional Ladakhi kitchens such utensils are commonly seen
Chiling Sumda...
Jawaja famous for its leather crafts is equally famous for its colorful jute dhurries. The craft of jute dhurries, a reversible flat-weave rug or mat was initiated during the ‘Rural University initiative’ conducted by IIM and NID in the mid nineteen seventies.The characteristic designs and colors of these carpets are an expression of the village surroundings and were created by the craftsmen with the help of designers.
Unlike carpets the panja dhurries are woven and not knotted, making them light and usable on both sides.
They are known for their colorful jute dhurries. The craft of Jawaja jute dhurries, a reversible flat-weave rug or mat.
The designs in the dhurries were crafted in a way to allow inspirations from the local landscape to be incorporated. The patterns and colors used in the carpets are simple and evocative of the earthy tones of the village environment.
It was initiated by then director of IIM, Ahmedabad Prof. Ravi Mathai. The initiative was called ‘The Rural University’ and the ‘National Institute of Design’, Ahmedabad, was invited to collaborate under the guidance of Prof. Ashok Chatterjee. A team of designers headed by product designer, Ms. Helena Peerhenthupa, and textile designer, Ms. Neelam Iyer, worked with the lowest caste of occupational groups – the ‘Raigar’ families of leather-workers, and the relatively better off ‘Bunkar’ families of weavers.
The Jawaja weavers weave colorful dhurries that are mainly used to cover floors or as doormats. These multi-functional dhurries are also used as wall hangings and as art decor.
The Jawaja project has brought about a new lease of life and self-dependency to the village. It has been able to slowly break the caste divide and form an environment of mutual respect for the professions. The most visible interaction has been of traditional skill with modernity, the meeting of two worlds. This has proven to be an inspiration to many movements thereafter, with self-empowerment and reliance as their goals. The Jawaja village was thus crafted in a way that the people itself became its reliable resource.
In the words of Prof. Ashok Chatterjee (NID) from an interview conducted in 20 October 1997 AD by Carolyn Jongeward,
– 15 to 20 years ago the craftspeople of Jawaja had no ability to deal with the external market. There was no capacity to understand the needs of buyers far removed from them physically, socially, emotionally and psychologically. That gap was huge. They felt inadequate and that they needed to wait until someone told them what to do. In those days they couldn’t enter the Taj Hotel in Bombay to have direct contact with a buyer. Now they are no longer thrown out of the Taj Hotel. They are travelled widely and have developed street smarts to cope. Now their products have gained an international reputation, not just occasional local exposure. OXFAM, just one of their international buyers, has sold their crafts for almost 15 years. This is a huge accomplishment for this community…
The designs made in the 1970s are still most sought after. The wool is different in its quality of not having as much oil as that of sheep from more damp climates.
The weavers are categorized into four groups:
1) Independent weavers: Ones who have their own looms and capital investment. They cater to the needs of the villagers.
2) Weavers employed by master weavers: They produce cloth for a wider local market
3) Weavers in the Jawaja Weaver’s Association
4) Weavers employed under Intensive Handloom Development Scheme and carpet weaving centers.
In 1975, a small collective of people from the ‘Indian Institute of Management’, Ahmedabad, conducted an experiment in rural education and development. It was initiated by then director of IIM, Ahmedabad Prof. Ravi Mathai. The initiative was called ‘The Rural University’ and the ‘National Institute of Design’, Ahmedabad, was invited to collaborate under the guidance of Prof. Ashok Chatterjee.
With an aim to actively collaborate with the rural communities and to catalyze local solutions to problems of poverty and self-reliance, the volunteers, teachers and students from both these institutions worked together with the people of the Jawaja village.
Jawaja, an erstwhile derelict village of Rajasthan that had been written off by the government as a resource-less and underdeveloped region was given a new lease of life.
A team of designers headed by product designer, Ms. Helena Peerhenthupa, and textile designer, Ms. Neelam Iyer, worked with the lowest caste of occupational groups – the ‘Raigar’ families of leather-workers, and the relatively better off ‘Bunkar’ families of weavers. The team had to deal with an initial opposition and skepticism from the doubting villagers and village elite.
Of the few tools the villagers were equipped with, the loom was a prominent one. The ‘Bunkars’ or the ‘weavers’ used it to weave woolen shawls, odhnis and other locally worn textiles. They would use it for themselves, barter it for food and other supplies or sell them in the local market for cash.
The ‘Raigar’ communities, on the other hand, were leather workers. They made objects like camel harnesses, footwear and other adornments. In the 1940’s and 1960’s, the work of this community was facing a major setback because of the banning of flaying, tanning and shoe repair by their community heads to raise their social standing. By the 1970’s, the leather workers had to purchase leather at high market rates making the craft highly disadvantageous. With the advent of electric pumps and motors, the leather bags or ‘Chaaras’ made by them to draw water from the wells also became obsolete. The local markets were ruled by the higher castes and the money lenders.
The ‘Rural University’ team helped the villagers overcome these obstacles to a large extent and worked with the rural craftsmen to develop contemporary products which could be sold in the national market. Many other organizations were consulted for refining the techniques and making the processes more speedy and efficient. The craftsmen were taught modern marketing skills and contemporary design interpretations, in a manner that now; they have become artisan designers in their own right. Presently the processes of management, innovation and marketing are completely run by the artisans themselves.
The designs in the dhurries were crafted in a way to allow inspirations form the local landscape to be incorporated. The patterns and colors used in the carpets are simple and evocative of the earthy tones of the village environment. The earlier dhurries were made only in plain colors but with changing trends in customer demands, brighter and more vibrant colors are being incorporated in the designs. Small knotted tassels on the ends of the carpets are a common feature of the design and the colors have become more harmonious and sophisticated. The rugs are tightly woven from uncolored wool and some dyed colors.
The biggest challenge for Jawaja craftsmen has been marketing their work in western markets due to stiff competition and a language barrier. According to a few craftsmen they are not able to explain their work well because of this. They do not know what the customers understand and what they don’t. Their understanding determines the amount of value they give for the craftsmen’s work.
The buyers of the Jawaja products are located in places far away from the village. The means of transport and accessibility are very less for the craftsmen. This has led to almost no direct interaction with the buyers. Only middlemen have direct interactions and the artisans only know what they tell them. Even though they have a website, there have been no direct sales.
Cotton yarn – single, double twisted or mercerized cotton is used where the counts used are medium (30’s, 40’s) and coarse counts (20’s and below).
Woolen yarn- Mill-spun yarn is used in greater quantity than hand-spun yarn since the hand-spun ones are not of superior quality and does not absorb colors well. The mill spun yarn is also evenly spun.
Jute twine- In products of lower quality, jute twine forms the weft and forms the lower portion of the carpet. The material adds strength to the carpet and enhances its ability to withstand pressure.
Dyes- The dhurries are dyed with synthetic dyes and are sourced from Beawar.
Fuel- Dried Cactus pieces or wood is used as fuel to heat the vats of dye.
Fly shuttle loom – It is the main tool for the weavers in making the dhurries.
Charkha or winding wheel – It is used to transfer yarn from creels to bobbins.
Carpet loom – It consists of a pair of horizontal wooden rollers or beams, supported by two flat poles which can revolve. Weaving is done between these horizontal rollers.
Chura or round-pile cutter – It is a short knife with a semi circular pile and a wooden handle and is made of tempered steel. It is used for cutting the pile after the knot has been tied.
Panja or comb – It is a short iron comb with a wooden handle. It is used to settle and fix the woven weft between the cotton warp lines. Since the comb is heavy, its weight helps to settle down the knots tightly.
Padla or Creel – It is a wooden tool used to wind yarn from the cotton hank.
Finishing scissors – It is used to level up the piles and give the carpet a smooth finish.
Brushes – These are large stiff hair brushes that are used to brush-off unwanted fibers from the finished carpet.
The Jawaja dhurries are woven using cotton yarns that are first dyed in the required hues. These are then woven together by the craftsmen on a horizontal loom. A couple of craftsmen are required to work on the weaving, both in stages and in tandem, to craft the dhurries efficiently. The marketing and sale of the dhurries are now handled by the craftsmen themselves, and are dispatched and sold according to order.
Dyeing –The process begins with the immersion of ‘Atti’ or hanks with yarn into boiling water for half an hour. This is then immersed in vats of hot dyes which are of three main types – direct colors, sulphur colors and acid colors. After dyeing, the yarn is washed in cold water and left to dry in the sun.
Winding – ‘Winding’ is a process of transferring yarn from the hanks to the bobbins. Locally known as ‘Kandi Bharna’, the process involves stretching the yarn around the ‘Creel’ and the ‘Winders’ draw threads from the stretched hank attached to the bobbin. This is then placed on the spindle.
Warping – The length of the warp generally ranges from 40 yards to 60 yards depending on its work-ability. ‘Warp bobbins’ are attached in rows to a vertical stand. Threads are drawn from these to the reed and then to the warp drum. Keeping the circumference of the drum as a measurement, the length of the warp is determined according to the number of times it is rotated. This process has to be done with utmost care to enable good weaving.
Drafting – Locally known as ‘Sarai Karna’, drafting is done to keep the warp threads parallel to one another and divide them into sheds while weaving.
Denting – This is the process of drawing the warp-ends through the reed. Two people are required in this process. One picks up the thread in twos and the other draws them through the reed. It is called ‘Taar Bharna’
Weaving- The weaving of the dhurries is carried out in three primary weaving actions of shedding, picking and beating. The act of shedding results in creating an opening in the warp threads while picking propels the shuttle. The beating motion, as the name suggests, beats up the weft thread by drawing the ‘slay’ forward. Expertise and efficiency aids the weaver in carrying about these three in a rhythmic manner.
Beawar was founded by Colonel Dixon in 1835 AD. It was part of British India, and the administrative headquarters of Merwara district. Since early times, the region where 'Beawar' lies is called the 'Magra-Merwaran', and it was named after a local village called 'Beawar Khas' by the British. This region was ruled by fierce tribes such as the 'Kathats' (Muslim Rajputs) and 'Rawat Rajputs'. The British tried to subdue them but were unsuccessful because the tribes were scattered across many small villages and they were excellent in conducting guerilla warfare. The 'Battle of Shyamgarh' was fought between the Kathats and the British. The British won and Kathats abandoned the fort of Shyamgarh, but employed guerilla tactics causing great loss to the British. So the British founded a military cantonment with fortified walls for protection and further military missions. Another factor involved in building a cantonment here was, Beawar was situated at a strategic tri-junction of the royal states of Jaipur, Jodhpur, and Udaipur.
To keep the menace of Kathats and Rawat-Rajputs at bay, British raised a battalion enrolling Kathats and Rawat-Rajputs (designating them as a Martial Race) and named it Magra-Merwara battalion. They used this Battalion for further military missions which proved quite efficient. According to a legend British put a sign board of 'Be-aware' as a warning to the British caravans and officers leaving the cantonment or crossing the cantonment. Slowly with time the local people came to think of it as the name of the cantonment and so the cantonment came to be called 'Beawar'.
The 'Jawaja' village is located in the 'Jawaja Panchayat Samiti' or the 'Jawaja Block' on the National Highway no.8. It is located around 70 kms south of Ajmer and about 500 kms north of Ahmedabad on the highway. The only largest town near it is Beawar. It consists of about 200 villages and hamlets of which one of them is Beawar Khas village and is situated 4 kms northeast of Beawar. It extends over an area of 3015 acres of land.
The village used to boast of a rich forest many years ago that has now depleted with only few trees remaining. Dense shrubs appear during the monsoons and the land is dry and dusty during the remaining months. The main vegetables grown in the northern region of Jawaja are tomatoes and hot peppers or chillies. The chief grain crops are bajra, maize, jowar and wheat. The area is drought or flood prone, in the two extremes, because of the topography of the land. Most of the land that can be cultivated is a thin strip towards the centre of the block, starting from the south of Jawaja village and widening towards Beawar. Just outside the village of Beawar Khas is a lake that has dried.
The village has one school and around four drinking water wells. There is a medical dispensary and it has power supply. The village has a few small shops where basic commodities and groceries can be bought. A tea stall and post office are situated next to each other. This spot is also used as a space for panchayat meetings, casual gatherings and festival celebrations. It depends on the town of Beawar for further needs. The neighboring Beawar town is equipped with cinema halls, schools (both middle and higher secondary), college, municipal library and hospitals.
The narrow roads are lined with rows of brick houses. There are two small temples or shrines in the centre of the village, built in the shade of a banyan tree. The houses are simple and seldom have decorations on them. Most houses still have thatched roofs and walls of mud mortar.
The weave's houses lie in a separate cluster away from the other communities. Each house has its loom placed in an area to catch maximum sunlight. Some weavers don't have looms at home and they work under a master weaver.
The staple food is maize. Rice appears less often in their cuisine as compared to wheat, bajra/maize and jowar. Tea is a popular beverage. Meals are eaten early in the mornings and early in the evenings. It consists of a thick maize roti and chutney made of chilies and onions.
Marriages are arranged by parents and they are very strict about it. In the Bhambi or weaver community, the grooms' father or the bridegroom himself gives the dowry. Divorce is allowed and widows are permitted to remarry. An interesting ritual exists in the community, called the 'Nate-lana', a marriage without a marriage. The bride goes back to her father's home after the wedding and anyone can approach her father for her hand by paying some money. If the husband wants her back, he has to pay twice the amount of money the new suitor has paid.
The majority of people are occupied in multiple occupations. The two main occupations are farming and craft. The higher castes are 'Rawats', 'Rajputs', 'Mehrats' and 'Jats' while the 'Harijans' are considered as the lowest caste. The craftsmen are 'Kumbhars' (potters), 'Lohars' (blacksmiths), 'Kuhars' (former palanquin carriers), 'Raigars' (cobblers) and the 'Bhambis' or 'Bunkars'(weavers). The 'Bhambis' were generally regarded as 'untouchables' or 'Harijans' after the Gandhi movement and thereafter they fall into the schedule caste category. The men wear simple 'Rajasthani' attire consisting, of a traditional shirt, dhoti and turban while the younger generations have taken to more western fashions such as jeans, trousers and t-shirts. Women wear traditional attires consisting of Lehenga, Choli, Odhani and wear ornaments that display their financial standing in society.
The village is famous for its vibrant dhurries and weaving.
List of craftsmen.
Team Gaatha